The foundation of any company’s facilities management (FM) program is repairs and maintenance, or R&M as it is known in the industry. No matter what industry you are in, maintaining facility assets is every maintenance department’s first priority. The secret to a successful and effective maintenance program is to understand the distinction between repair and maintenance, and know when and how to deploy each effectively.
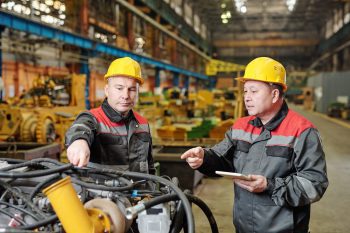
Is There a Difference Between Repair & Maintenance?
For anyone who has ever worked as a maintenance technician, the terms “maintenance” and “repair” are frequently used interchangeably. In essence, repair and maintenance have the same end goal of extending the llifespan of the infrastructure, tools, and assets that they use. However, the way they approach achieving this objective is quite different.
For an asset management program, maintenance staff, and business to be successful, it is essential to understand the differences between the two terms.
What Are Repairs?
Repair is an action taken to bring back an asset’s proper functionality. It involves restoring a damaged object to its ideal state of operation. The type of asset failure determines the extent of the necessary repairs. There are primarily two basic types of asset failures:
Complete Failure: These are failures that prevent the usage of assets. Until someone takes care of the asset, it cannot be used for its intended purpose. For instance, if the engine in your car stalls, it won’t start again until you take it to the mechanic. Unplanned downtime caused by asset failure is typically expensive and necessitates immediate maintenance. When downtime costs too much, this comprehensive guide helps you get proactive about uptime.
Partial Failure: In this situation, the asset still works to some degree despite the failure. The equipment is still operable, but it is either dangerous or ineffective. For example, a driver may decide to operate a vehicle with a dirty air filter. However, he might notice that the air conditioning isn’t as cold as it formerly was. Generally, minor failures should be fixed as soon as possible to prevent full breakdowns from occurring at inopportune periods.
Naturally, some repairs cost more than others. The cost of repairs will vary depending on what caused the breakdown in the first place.
Repairs after an asset fails can be very expensive. Aging equipment, mechanical failure, and operator mistakes are just a few of the common reasons why assets fail.
Even though failure is unavoidable, most asset failures can be prevented. This is where maintenance comes in. Proactive or preventive maintenance can help you avoid major, costly repairs.
What Is Maintenance?
Maintenance is the process of keeping an asset functional and in good working condition. Preventive maintenance is done to maintain a machine’s operation, performance, and safety throughout its lifecycle; its main objective is to prevent expensive or unexpected repairs.
Maintenance can be divided into four categories: preventative, corrective, predictive, and reliability-centered.
Some of the most common maintenance activities include:
- Visual checks, functional tests, and other forms of regular maintenance
- Installing sensors and equipment for condition monitoring
- Installing or upgrading HVAC or lighting systems
- Upgrading or installing current resources and infrastructure
- Upgrading current equipment and systems
- Conducting safety inspections
- Upgrading or replacing asset components
Maintenance is performed to avert unplanned asset downtime, repairs are carried out to reduce losses after downtime.
Making the most of your assets is the goal of both maintenance and repair. They have diverse approaches to achieving this goal. The cost of maintenance can vary greatly depending on the equipment and parts complexity.
Increase Workforce Visibility and Effectiveness
CMMS will help you in determining whether or not you are actually making the most of your workforce and facility spending. You can forecast the days, months, and seasons when the maintenance activity is at its height with the help of the data you gathered. It can also help you decide when to tackle large-scale projects so that you can avoid service interruptions.
Optimize Preventive Maintenance
Ad hoc repair requests will still come up from time to time, and they will be handled as necessary, but a CMMS system really shows its value when it comes to maximizing your preventive maintenance efforts. You can better understand how to prevent your reoccurring maintenance problems if you have insight into them. Other advantages are:
- Extended Asset Life.
- Better budgeting procedures based on past asset data and performance.
- Prevent problems or equipment failures before they occur.
Repair & Maintenance Expenses
Businesses that depend heavily on physical assets would have to devote a sizeable amount of their operating budget to maintenance and repairs. Businesses commonly classify these costs as Maintenance, Repair & Operations (MRO) costs.
The size of the maintenance department, the quantity, and size of the facilities that require maintenance, the cost of maintaining and repairing the infrastructure and equipment, and the ratio of proactive vs. reactive maintenance work an organization performs will all have an impact on the total MRO expenses you see at the end of the year.
Regardless of how much time and money you invest in maintenance, assets eventually stop being cost-effective. There comes a time when purchasing new equipment makes more sense than attempting to keep the old one operating as it approaches the end of its lifespan. Maintenance workers should think about performing a repair vs. replace analysis when working with aging equipment.
Simplify Preventative Maintenance
Always keep in mind that while repairs cannot be avoided, they can be greatly reduced. Your facilities program can be managed using a cloud-based system, (such as a computerized maintenance management system (CMMS), that allows you to easily create work orders and monitor their progress. You can store, track, and change work orders and R&M requests whenever and wherever you choose thanks to automation, which removes the need for manual switching between outdated systems.
With a CMMS, you will have access to predictive analytics with this type of end-to-end system, a crucial function that uses historic data to forecast future results. With our CMMS software, users can track important asset characteristics in real-time, allowing you to see the big picture and decide if it makes more financial sense to repair or replace an HVAC unit that continually is breaking down.
CMMS software includes all the tools you need to automate spare parts inventory, monitor maintenance operations in real-time, track asset activity, and assign work orders.
In Summary
Repairs and maintenance are crucial parts of the lifecycle of the majority of most of your physical assets. Regular maintenance should be the main priority for anyone trying to extend the useful life of their assets and infrastructure. Although they can’t entirely be avoided, repairs shouldn’t happen frequently.
Please feel free to get in touch with one of our account executives if you have any questions about using cloud-based maintenance solutions, like CMMS, to plan, automate, and streamline your maintenance tasks.