IManaging maintenance tasks without a proper system can result in delayed urgent repairs or forgotten routine checks. Before you know it, you’re facing breakdowns and dealing with frustrated teams. This is where work orders come in.
Work orders bring order and organization to businesses by helping teams stay on track, save time, prevent unexpected equipment breakdowns, and boost productivity in general.
Let’s break it all down in this post. We’ll go over what a work order is, explore its different types, and cover the essential details every work order should include.
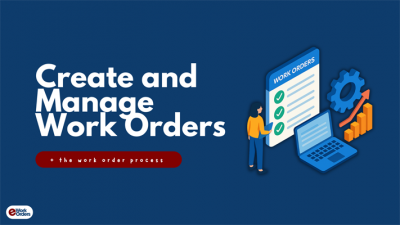
What is a Work Order?
A work order is a formal request that tells you what tasks need to be done. It’s mainly for maintenance or repair tasks. It states what the issue is, who’s responsible for fixing it, and how they’ll get it done. A proper work order also includes the tools needed to fix the problem, a deadline, and how urgent the job is.
For example, let’s assume there’s a leaking pipe in your company. A work order would note where the leak is, what tools are needed to fix it, and which plumber is assigned to handle it.
Just like an executive order, a work order authorizes action.
Work Order Vs Work Request
A work request is the initial request for action. It’s a way of letting the team know that there’s a problem or maintenance is needed. You’re basically alerting them of an issue that needs attention. A work order, on the other hand, is what comes next after the request is approved. It’s a detailed action plan.
Simply put, a work request starts the process, while a work order gets things done.
Types of Work Orders
There are different types of work orders depending on the task, its urgency, and what the work is meant to achieve.
1. General Work Order
This type covers basic tasks, such as cleaning, painting, replacing light bulbs, and installing new equipment. A general work order is for broad, basic tasks or those that don’t need a specialized category.
2. Preventive Maintenance Work Order
A preventative maintenance work order is created to schedule routine maintenance tasks on assets and equipment. It helps prolong their lifespan and keep them in good condition. As a result, it reduces unexpected breakdowns and the number of major repairs and saves on long-term costs.
3. Corrective Maintenance Work Order
This work order is issued to facilitate repairs after a failure is detected, whether it’s an equipment failure, a system malfunction, or facility issues identified during inspections or daily operations.
4. Emergency Work Order
As the name suggests, emergency work orders prioritize urgent issues that could threaten safety or affect operations. For example, power outages, gas leaks, or critical equipment failures. They help in minimizing risks and downtime.
5. Inspection Work Order
Think of this work order as your equipment’s regular check-up. It’s issued when you need to assess the condition of equipment, systems, or facilities. It’s all about catching small issues before they become big problems, like spotting worn-out parts before they fail.
Depending on what the inspection discovers, it may trigger follow-up actions, such as scheduling preventive maintenance or flagging urgent repairs.
6. Safety Work Order
A safety work order focuses on protecting teams from workplace hazards. For example, replacing a slippery floor, fixing exposed electric wires, fixing faulty outlets, or replacing machinery guards. It helps prevent accidents and protects teams from injuries.
7. Electrical Work Order
An electrical work order is issued specifically for tasks related to electrical systems, such as rewiring, fixing a faulty circuit, or replacing faulty panels.
8. Custom/Specialized Work Order
A custom or specialized work order is developed to meet unique tasks or industry-specific needs, such as IT server maintenance or setting up a temporary workspace.
What Should a Work Order Include?
Here’s everything a work order should include:
Job Details And Description | This section provides clear job details, including the location and any other relevant information. For example, “Repair elevator door sensor in North Wing.” |
Assigned Personnel | Who’s doing the job? It could be your in-house maintenance guy or a contractor. It must include their name and contact details. That way, if there are any updates, you know who to follow up with. |
Timeline And Priority | Some jobs are urgent, while others aren’t. Work orders should have a clear deadline so that everyone knows when tasks are due. Also, a priority label should be included to indicate whether a task is low, medium, or high priority. |
Materials And Tools Needed | A work order specifies the tools, equipment, and spare parts required to carry out a task. It’s useful in the planning stage and helps avoid delays due to missing supplies. |
Safety Procedures (If Any) | Safety protocols should be clearly defined to keep everyone involved safe and compliant in the workplace. For example, these may include hazard warnings, PPE requirements, or rules for site access. |
Approval And Sign-Off Fields | For accountability purposes, a work order should include a supervisor’s approval and the technician’s notes to verify that the job was done satisfactorily. |
The Work Order Process
Work orders usually go through the following six-step process:
Step 1: Identify the Task
Every maintenance task starts when a team member spots a problem that needs attention. It could be a staff member noticing something that’s off or a sensor triggering an alert. Sometimes, it’s just a maintenance reminder popping up in the system.
Step 2: Submit Or Create The Request
Once a problem is identified, it must be recorded. While some businesses may still rely on spreadsheets or paper forms, those methods can be slow and messy. An efficient approach is to use a work order management system, where teams can quickly enter a request with all the necessary information in just a few clicks.
Step 3: Prioritize and Schedule
After logging the request, the team determines the level of urgency. Safety issues or critical equipment failures are time-sensitive and should be prioritized. The other tasks are scheduled based on priority, available resources, and workload.
Step 4: Assign And Execute The Task
The tasks are then assigned to the preferred technician. They are provided with all the relevant details, including what needs to be fixed, the location, the tools required, the deadline, and any other specific instructions.
Step 5: Review And Close The Order
When a task is completed, it’s reviewed to ensure the technician did it satisfactorily. If everything went well, the technician or supervisor adds any final notes and closes the work order. If something is still not right, the work order can be updated or reopened.
Step 6: Analyze and Document the Results
Finally, once a work order is closed, it becomes a valuable source of information. It shows what was fixed, how long it took, what spare parts were used, and whether the same problem keeps recurring. By analyzing these details, teams can identify patterns, track their performance, and make important future decisions.
Benefits of Using Work Order Software
Switching from outdated methods, such as paper, to work order software makes a huge difference. Here are some of the key benefits:
- Important information, like work orders, schedules, and maintenance history, is stored in a centralized platform.
- No more dealing with manual paperwork. So, the approval process is fast and reliable.
- Team collaboration improves communication between teams.
- Supervisors get a clear view of work progress, delays, and what’s been completed in real-time, all from a single dashboard.
- You can track labor and material costs, making budgeting and planning way easier.
- It makes the audit process smoother since every job is logged, organized, and ready for compliance.
- You can instantly generate reports to track performance, spot recurring trends, and make better decisions.
How eWorkOrders Makes Work Order Management Effortless
eWorkOrders isn’t just about basic task tracking. It’s a complete 360deg; maintenance management solution that transforms how teams manage work, projects, assets, and communication. Here’s what makes our services a game-changer:
- Mobile Accessibility: Create, update, and manage work orders from anywhere, right from your mobile device or tablet.
- Detailed Work Order Details: Attach diagrams, photos, files, schematics, notes, and manuals so technicians have everything they need to complete the job.
- Customizable Templates: Build work orders in just a few seconds. With eWorkOrders work order templates, you don’t have to start from scratch.
- Keep All Relevant Paperwork: Upload invoices, quotes, record part numbers, and any other critical paperwork directly in each work order.
- Communicate with Team Members: Collaborate with team members and keep everyone informed to avoid miscommunication.
- Inventory Management: Know exactly what parts are in stock to avoid delays.
- Makes Budgeting and Planning Easier: Tracks downtime, labor hours, and materials to plan budgets and avoid overspending.
- Reports and KPIs: The system auto-generates reports with key metrics, helping you track efficiency, identify patterns, and make data-driven decisions.
If you want to make creating and managing work orders convenient and time-efficient, you need to give eWorkOrders a try. Be sure to schedule a free demo.
Closing Thoughts
A work order system keeps maintenance tasks on track. No more guesswork or delays. With the right tools, such as eWorkOrders, you’re not just fixing problems, but also saving time, cutting costs, and keeping your team in sync.
FAQs
What is an Example of a Work Order?
A work order could be as simple as requesting that the technician inspect and replace the HVAC filters in the building, including the assigned technician, required tools (filters, ladders), and safety steps (turning off the power in the first unit).
What is the Difference Between a PO and a Work Order?
A purchasing order (PO) is a buyer’s request for goods or services. A work order, on the other hand, details the maintenance task, the resources needed, the technician’s details, and more.
What are the 5 Main Functions of a Work Order?
The five main functions of a work order are to identify and describe the task, assign the task to the right personnel, allocate resources, schedule and track work progress, and record when work is completed and give feedback.
What is Another Name for a Work Order?
A work order is also known as a maintenance order, job order, or service order.