eWorkOrders Predictive Maintenance Program empowers organizations with additional tools to create more accurate predictions on when a piece of equipment will require maintenance or replacement. Predictive Maintenance is a condition-based maintenance program where assets are monitored with sensor devices that supply data about the asset’s operation and possible defects. The data is used to predict when the asset will require maintenance or replacement.
eWorkOrders CMMS software solution will automatically create a work order when it detects that an asset has fallen outside of the defined parameters. Alerts will be sent to the maintenance team to assess and repair the issue. With the alerts being identified and sent directly to the technicians in real-time, the elimination of extensive downtime is minimized.
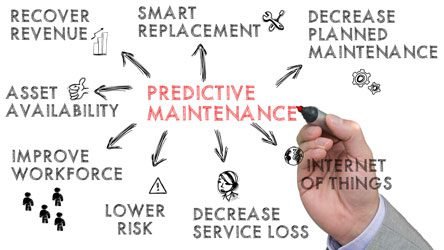
What is Predictive Maintenance
Predictive maintenance (PdM) is a proactive maintenance strategy that tracks and monitors the performance and condition of equipment during normal operation. These monitoring tools detect various deterioration signs, anomalies, and equipment performance issues. Based on these measurements, maintenance work can be done just before a failure happens.
Real Results – From Real Users
Explore Additional Testimonials & Case Studies
Predictive vs. Preventive Maintenance
Predictive Maintenance monitors the performance and condition of equipment during normal production operations. Predictive Maintenance estimates the exact moment of a failure, and repairs can be scheduled when necessary. This is a cost-effective approach with minimal impact on production.
Preventive Maintenance tasks are completed based on a recurring time schedule or a given amount of usage or cycles. A planned and scheduled maintenance routine is put in place to extend the life of assets and reduce downtime. The maintenance is performed on predetermined assumptions, based on manufacturers’ recommendations or history.
Predictive Maintenance Objective
The main objective of Predictive Maintenance is to first predict when equipment failure might occur (based on certain factors), and be able to prevent the failure with regularly scheduled and corrective maintenance.
How Predictive Maintenance Works
Predictive Maintenance depends on condition monitoring, which collects and analyzes data from the machine during operations, to ensure the optimal use of equipment.
There are three main elements that allow PdM to track asset conditions and alert technicians about projected equipment failures:
- With real-time tracking, each piece of equipment is monitored through installed and fitted sensors that capture data about equipment deterioration and performance.
- Internet of Things (IoT) technology collects and shares the data enabling the assets to communicate, work together, analyze data, and recommend appropriate action to be taken directly based on how the system is set up.
- Predictive Data collected is analyzed using predictive algorithms that identify trends when an asset will require repair, servicing, or replacement.
Predictive Maintenance/Condition Monitoring Techniques
There are numerous condition-monitoring devices and techniques that can be used for effectively predicting failure, as well as providing advanced warnings for maintenance teams. Some of them include:
Infrared Thermography / Temperature Measurement
Infrared thermography is used to detect heat variations in machines and equipment. By capturing thermal images, infrared cameras help identify overheating components, allowing technicians to address potential failures before they escalate.
Ultrasonic Monitoring / Acoustic Analysis
This method uses high-frequency sound waves to assess the condition of bearings, rotating parts, and other machinery. It helps detect leaks, gear faults, and lubrication issues that could lead to equipment failure.
Vibration Analysis / Dynamic Monitoring
Vibration analysis is essential for high-speed rotating equipment, as it measures vibration patterns to assess a machine’s health. By analyzing these signals, technicians can detect imbalances, misalignments, or worn components before they cause major breakdowns.
Oil Analysis / Tribology
By examining oil samples, technicians can determine the presence of contaminants, metal particles, or signs of wear. This helps ensure proper lubrication and prolongs the life of mechanical components.
Laser Interferometry
A precision measurement technique that uses laser-generated wavelengths to detect even the smallest changes in wave displacement. This method is valuable for ensuring structural integrity and component alignment.
Motor Circuit Analysis
This process involves computerized testing of electric motors to evaluate their overall condition. It helps identify faults, insulation breakdowns, and early signs of electrical failure, ensuring reliability.
Radiography / Neutron Imaging
This technique uses radiation to inspect internal structures and detect hidden defects in machinery. It provides a non-destructive way to assess material integrity and prevent failures due to unseen damage.
What Circumstances Call For Predictive Maintenance?
Predictive maintenance (PdM) applications include those that: possess a crucial operational role and possess failure modes that are reasonably predictable with routine monitoring.
Some applications that predictive maintenance is not appropriate for include those that don’t perform a critical task and do not have a cost-effective predictable failure mode.