Did you know that unplanned maintenance is estimated to cost industrial manufacturers a staggering $50 billion annually? That’s a huge price to pay for poor planning.
The truth is, smooth operations don’t just happen by chance. You plan for them. Another fact is that maintenance planning isn’t just about fixing assets. It protects you against losses, and if done properly, it can extend asset life and keep operations running smoothly.
Let’s break down what maintenance planning means, explore the best strategies, and show you how you can handle your operations better for smoother and more cost-effective results.
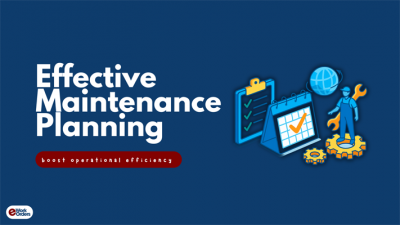
What is Maintenance Planning?
Maintenance planning is the process where maintenance teams get everything ready for repair and upkeep tasks before equipment actually starts breaking down. The process involves checking what needs attention, gathering the right tools, planning when to do it, and deciding who will handle it. While it might sound like a checklist, it’o;s a system that prevents fires instead of fighting them.
For example, if you oversee a factory, maintenance planning involves the following:
- Identifying machines that need regular servicing
- Scheduling when to do it (like during slower shifts)
- Having the tools and spare parts ready when needed
- Making sure technicians know exactly what to do
Maintenance Planning Vs Maintenance Scheduling
Maintenance planning and scheduling often get mixed up, but they in fact play different (and equally important) roles in keeping operations running smoothly.
Maintenance planning helps you identify and define tasks. It addresses the what, how, and why of the job. Maintenance scheduling, on the other hand, determines when and by whom.
Maintenance Planning | Maintenance Scheduling |
---|---|
|
|
Types of Maintenance Planning Strategies
Businesses use different types of maintenance strategies. Let’s discuss the main types and when each works best.
1. Preventive Maintenance
You see how you take your car to the car service centre when it completes some miles, not because it has any issues, but to keep it in good condition and prevent breakdowns. That’s how preventive maintenance works. It’s the regular check-up of equipment to detect potential issues early and avoid malfunctions. It’s best used for equipment with predictable wear.
Here, you pause operations to allow inspections or repairs at set intervals, regardless of the equipment’s condition. For example, changing oil in the equipment every 3 months.
2. Predictive Maintenance
Imagine being able to detect a problem before it turns into a full-blown breakdown. Predictive maintenance helps you do that. It’s like a check engine for equipment.
Instead of waiting for assets to stop working, this approach uses data analysis and advanced technologies, such as smart sensors, to detect small issues that, if not handled, eventually cause big problems.
For example, modern elevators have sensors that track door movements, speed, motor temperature, and usage frequency. Signs such as slower doors, uneven stops, or warning lights on the control panel automatically alert technicians to perform maintenance work before a breakdown.
3. Reactive Maintenance
Reactive maintenance happens to fix things when they break down or fail. While it doesn’t require prior planning, it’s best used when dealing with machines that aren’t critical. But there’s the catch: this approach can lead to higher repair costs and increased downtime.
4. Condition-Based Maintenance
Condition-based maintenance is a smart hybrid of preventive and predictive strategies. It monitors the actual health of equipment and alerts teams when readings hit warning levels. This approach can help you cut costs and reduce unnecessary maintenance. It’s ideal for equipment with variable usage, such as generators and heavy machinery.
The Maintenance Planning Process (Step-by-Step)
Want to improve your maintenance planning? Here are the steps that’ll help you align your business structure with your planning.
Step 1: List and Inspect Critical Assets
Start by listing all your machines, equipment, and other assets that need regular check-ups. While at it, list them based on value and risk. High-value and high-risk assets could affect production, safety, or cost when they fail.
You can create this list using the old-school method (spreadsheets) or the digital method (software). But maintenance planning software is more effective and efficient. The goal is to have a clear view of all your assets and their status.
Step 2: Prioritize Tasks Based on Risk and Urgency
Some tasks are urgent, while others are just routine checks. Urgent tasks require immediate action, while the rest can wait. To determine if a task is urgent, consider the cost of failure, downtime risk, or if it could cause safety concerns.
Step 3: Define Clear Procedures and Work Scopes
Write a step-by-step checklist of what needs to be done, including specific instructions, objectives, manuals, job location, materials and equipment, SOPs, safety steps, and any other relevant details. This will help the technicians do their jobs efficiently.
Step 4: Estimate Labor, Tools, and Material Needs
Plan all the resources required for execution by estimating labor, tools, and materials needed.
- Labor Estimates: Estimate the number of hours and skilled workers required. You may use past performance data to estimate this.
- Tools: Confirm you have all the tools and equipment required.
- Material Estimates: Do you have all the materials and spare parts required? You can estimate these quantities by referring to previous data and the manufacturer’s recommendation.
Step 5: Assign the Right People to the Job
Put the right people on the job. For example, let electricians handle electrical systems and plumbers fix leaky pipes and drainage systems. Look for qualified technicians who understand their work and can organize work efficiently.
Step 6: Document and Track Everything
Record everything on the maintenance planning software because your budget and future planning decisions depend on it. Track what work was done, who did what, every tool and material used, and any unexpected issues that came up. This helps with audits, reports, planning for the future, and knowing where to improve.
Benefits of Smart Maintenance Planning
A properly planned maintenance strategy transforms your entire operation. Here’s how:
- Fewer Breakdowns: Frequent routine checks keep assets running smoothly for a long period. You can detect potential issues before they turn into failures. This helps reduce the likelihood of breakdowns.
- Faster Repairs: When technicians get to work, they use pre-approved checklists. These checklists give them access to everything they need before they begin, saving time and facilitating quick repairs.
- Better Team Coordination: Effective maintenance plans have clear work orders. Everyone, including supervisors and technicians, is aware of what’s happening, who’s doing what, and when.
- Cost Savings: Unexpected breakdowns are budget killers due to downtime, emergency repairs, and production delays. But with proper maintenance planning, you can avoid these costs and keep operations running smoothly.
- Longer asset Life: Assets that are consistently cared for tend to last longer and are more reliable. You won’t need to replace them frequently.
How to Tell if Your Maintenance Planning is Working
So, you have implemented a maintenance plan. How do you know if it’s actually working? Here are a few indicators:
1. Low Backlog and Quick Work Order Completion
With proper planning, tasks are prioritized according to priority, scheduled efficiently, and completed with no delays. This means the backlog is manageable and the team completes work orders quickly.
2. Less Reactive Work
Maintenance planning is working if you’re no longer fixing failed equipment frequently. This means you have moved from a reactive to a proactive approach. It helps your team spend most of the time on planned tasks, not last-minute emergencies.
3. High Equipment Uptime
Another indicator of a successful maintenance plan is that your equipment spends more time up and running. High uptime leads to greater efficiency, less stress, and a happier team.
4. Fewer Repeat Issues
If your equipment doesn’t fail repeatedly with the same issues, you’re probably dealing with the issue at hand well, not just fixing the symptoms. That’s long-term thinking right there.
Make Maintenance Easier with eWorkOrders
Alt text: Screenshot of eWorkOrders; homepage.
Ready to upgrade your maintenance planning game? eWorkOrders is our all-in-one maintenance planning software that’s designed to help companies keep their assets in good shape and the entire operation running smoothly. Here’s how we do that with our services:
- Plan Tasks Proactively, not Reactively: Set automated reminders to avoid missed tasks, track backlogs, equipment downtime, and team productivity.
- Eliminate Guesswork with Real-Time Tracking: Monitor projects and their labor hours, work progress, and spare parts inventory.
- Mobile-Friendly for On-The-Go Teams: View task updates and monitor progress anytime, anywhere.
- Smarter, Faster Work Order Creation: Use templates to generate detailed work orders in seconds, and attach key assets like photos, manuals, and diagrams for better clarity.
If you want to take maintenance planning to a whole new level and save heaps of your time, be sure to schedule a free demo.
Closing Thoughts
So, there you have it. Effective maintenance planning paves the way for smooth operations, reduces unexpected breakdowns, cuts down costs, and minimizes downtime. It might seem complex, but with the right tools, like eWorkOrders, it can save you a lot of stress.
FAQs
What is Meant by Maintenance Planning?
Maintenance planning means getting ready for repairs before assets break. It involves listing assets and equipment that need care, which tools and materials are required, and determining who’s the best person for the job. The goal is to make sure that all assets are well taken care of.
What are the Top 3 Skills for a Maintenance Planner?
The top three skills for a maintenance planner are: organization skills to manage and prioritize maintenance tasks effectively, technical skills for technicians to understand equipment and repair methods, and problem-solving skills to resolve issues quickly when they come up.
What are the 4 Phases of Planned Maintenance?
The four phases of planned maintenance are: planning to identify the assets that need maintenance, scheduling to assign tasks to qualified technicians and allocate resources required to complete the tasks, execution to complete the work, and review to determine what worked and what didn’t, and use that information for future planning.
What are the Steps of the Maintenance Planning Process?
The steps of the maintenance planning process are: listing and inspecting critical assets, prioritizing tasks based on urgency and risk, defining clear procedures and work scopes, estimating labor, tools, and material needs, assigning the right people to the job, and documenting all actions and progress.