Updated: June 2025
Effective asset maintenance management is crucial for any company seeking to prolong the lifespan of its physical assets, minimize downtime, and enhance operational efficiency. With growing demands on maintenance teams and tighter margins, the ability to proactively manage and maintain assets is no longer optional—it’s a necessity.
However, achieving successful asset maintenance requires more than scheduled repairs. It demands a system that aligns preventive maintenance, real-time data tracking, and team coordination. That’s where robust asset maintenance management strategies come in.
If your goal is to improve performance and reduce asset-related risks, you will find this guide helpful. We will answer the question: Why is asset maintenance important? And explain the types of asset maintenance management strategies. Additionally, we will explain how to develop your asset maintenance plan.
Why is Asset Maintenance Management Important?
Below is a breakdown of why asset maintenance management is crucial for maintaining sustained operational performance and maximizing long-term asset value.
It Enhances Equipment Reliability and Workplace Safety
One of the primary goals of asset maintenance is to reduce the likelihood of unexpected equipment failures. In a place such as manufacturing plants, data centers, or healthcare facilities, asset breakdowns can lead to operational shutdowns, compliance violations, or even safety hazards. By implementing preventive and predictive maintenance strategies, organizations can detect early signs of wear, conduct timely repairs, and avoid catastrophic failures.
Cost Savings Through Proactive Management
Reactive maintenance is not only inefficient but also expensive. Emergency repairs often require immediate labor, costly parts, and extended downtime. With the help of asset maintenance management software, businesses can transition to a cost-optimized maintenance strategy. For example, in the logistics sector, regularly scheduled servicing of delivery vehicles helps avoid costly roadside breakdowns.
It Maximizes Asset Lifespan and Capital Investment
Assets like production machinery, medical equipment, or HVAC systems represent significant capital investments. Without a structured maintenance approach, these assets deteriorate more rapidly, necessitating early replacement and resulting in increased capital expenditure. With asset maintenance plans in place, organizations can monitor usage, assess asset health, and make informed decisions about refurbishing or replacing assets. This extends asset lifespan and ensures maximum return on investment.
Types of Asset Maintenance Strategies
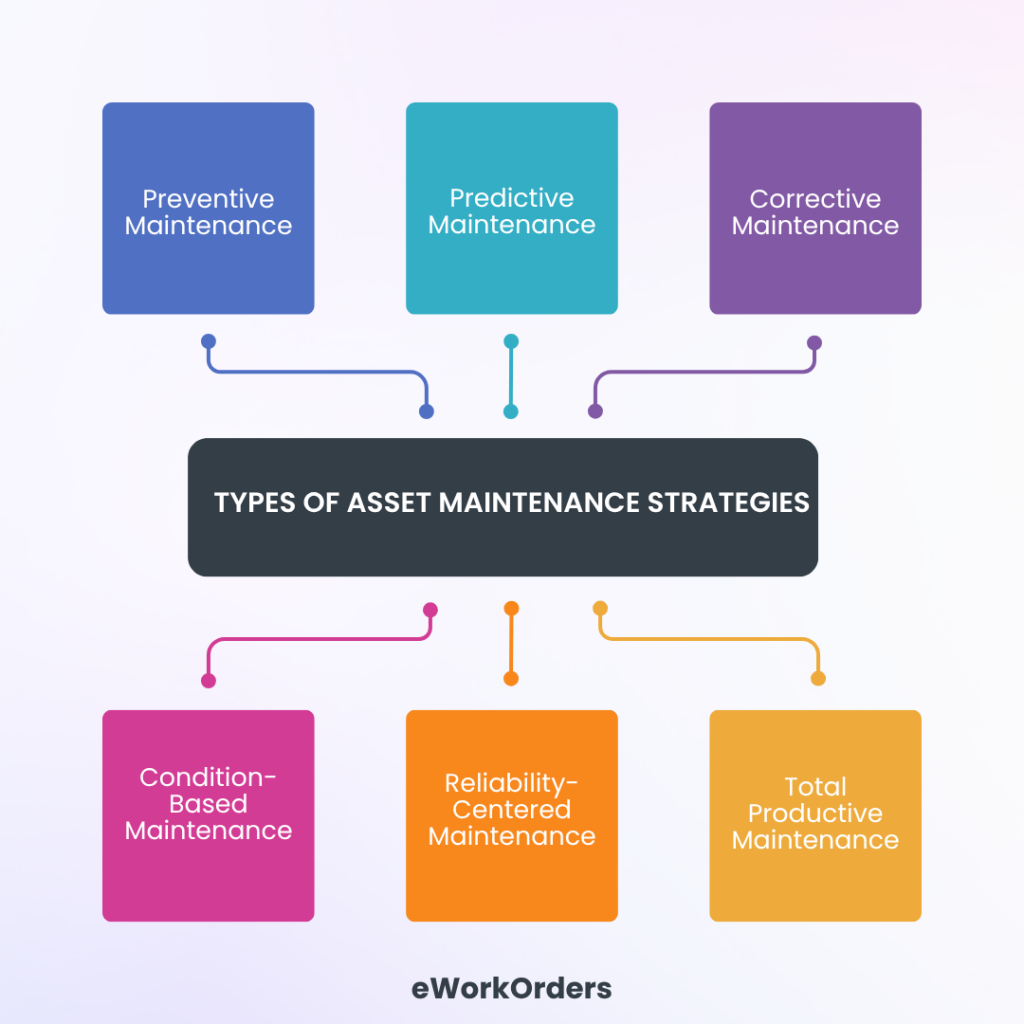
There are several types of asset maintenance management strategies that organizations can adopt. Below, we will discuss each of them in detail.
Preventive Maintenance
Preventive maintenance focuses on regular inspections, adjustments, and repairs to keep assets operational and reliable. This strategy is built around time-based or usage-based preventive maintenance schedules, ensuring consistency in how equipment is monitored and maintained. It identifies and addresses wear or irregularities early, allowing teams to perform maintenance tasks efficiently and reduce the risk of breakdowns.
A well-defined asset maintenance plan incorporates preventive maintenance as a core element. This enables maintenance teams to optimize labor and spare part utilization, thereby reducing emergency costs. For example, in manufacturing, an enterprise asset management system can trigger service alerts for conveyor belts after a set number of cycles. This supports the broader preventive maintenance strategy by aligning scheduled tasks with real usage data.
Predictive Maintenance
Predictive maintenance uses real-time monitoring and advanced analytics to identify when equipment is likely to fail. This method supports asset lifecycle management by allowing teams to allocate maintenance resources precisely where they’re needed, improving performance and reducing unnecessary interventions. With access to accurate asset information, maintenance managers can take proactive measures before disruptions occur, thereby reducing unplanned downtime and extending the lifespan of their assets.
An example is how General Motors applied predictive strategies in its factories. Instead of following fixed schedules, their maintenance projects respond to sensor data, aligning with reliability-centered maintenance. This shift increases uptime and streamlines the use of both time and budget.
Corrective Maintenance
Corrective asset maintenance involves tactics used to restore critical assets after they have failed unexpectedly. Unlike preventive strategies, it responds directly to asset failure, addressing faults as they arise to bring systems back online.
For instance, in a manufacturing plant, if a piece of critical equipment, such as a hydraulic press, malfunctions, technicians must react promptly to diagnose and repair the problem, thereby avoiding prolonged production halts. In such cases, corrective maintenance becomes the fastest path to restoring operational stability. Implementing this strategy within an overall asset maintenance program provides a safety net when preventive actions are insufficient.
Condition-Based Maintenance
This method uses real-time asset tracking and continuous monitoring to assess the current state of equipment. Interventions are implemented only when indicators show a decline in performance, enabling better resource allocation and fewer unnecessary tasks.
Through usage and performance metrics, teams gain visibility into asset details, enabling them to make informed decisions. This reduces repair costs by addressing problems early and ensures well-maintained assets are operating at peak efficiency. Continuous improvement becomes achievable when adjustments are based on actual conditions, rather than predefined timelines.
A practical example is in industrial manufacturing, where vibration sensors detect anomalies in motor operations. Maintenance is then scheduled based on these readings, rather than fixed intervals, which cuts downtime and prevents major breakdowns.
Reliability-Centered Maintenance
Reliability-centered maintenance (RCM) helps teams focus on the most effective tasks to delay an asset’s eventual breakdown. By analyzing asset functions, expected performance, and potential failure modes, RCM supports informed decisions that reduce unnecessary maintenance and optimize resource use. Instead of relying on routine schedules, it utilizes asset data to determine when interventions are truly necessary.
A critical step involves evaluating the impact of failure. For instance, in power generation, if a turbine fails, the entire grid can suffer. With RCM, operators utilize real-time asset data and historical trends to determine the likelihood of failure and establish condition-based triggers. This process directly improves asset reliability while cutting downtime.
RCM was applied in the aviation industry, where components like aircraft landing gear were previously maintained on rigid schedules. Engineers utilized asset data to model failure risks, resulting in performance-based scheduling and extended part life without compromising safety. The outcome was fewer disruptions and better control of maintenance costs.
Total Productive Maintenance
Total Productive Maintenance (TPM) emphasizes participation across all levels, encouraging every team member to engage in maintenance responsibilities. This approach reduces the likelihood of an asset’s eventual breakdown by identifying and addressing potential failures before they impact operations.
It focuses on early detection of faults and systematic inspections, thereby strengthening asset reliability. TPM blends proactive and preventive strategies, targeting not just equipment upkeep but also process improvements.
A key aspect of TPM is the effective use of asset data to track performance trends, schedule interventions, and minimize disruptions. For instance, a manufacturing plant using vibration analysis data to monitor motor health can detect misalignment early, allowing corrective action without halting the line.
Operators are trained to manage routine tasks, enabling maintenance teams to focus on more complex interventions. This shared responsibility model reduces downtime and optimizes production flow.
Developing an Asset Maintenance Management Plan
A well-structured asset maintenance management plan minimizes operational disruptions and ensures assets are kept in optimal working condition. The steps below outline a practical approach for optimizing asset maintenance.
1. Define Organizational Maintenance Objectives
Start by identifying the key outcomes your maintenance strategy should achieve. Objectives often include minimizing equipment downtime, extending the useful life of machinery, improving safety compliance, and lowering repair or replacement costs.
Once you have done that, you should align these goals with broader operational targets. For example, if a manufacturing facility faces frequent unplanned outages, reducing equipment failure rates and increasing uptime would be primary objectives.
2. Build a Complete Asset Inventory
This task includes collecting information such as manufacturer, model number, location, date of installation, warranty status, and service history. You can use barcode or RFID tagging to simplify identification and tracking. Without this information, it’s impossible to plan preventive maintenance or track asset performance effectively. For instance, a logistics hub with dozens of forklifts, conveyors, and scanners needs accurate data on each unit to schedule inspections and replacements systematically.
3. Use Asset Management Software
Adopt a digital platform to centralize and manage all asset-related data. These systems allow maintenance managers to schedule recurring tasks, assign technicians, track labor hours, and maintain logs for compliance audits. Over time, the software can generate insights to help forecast part failures, manage spare inventory levels, and automate task reminders. For example, a water treatment plant using a CMMS (Computerized Maintenance Management System) can automatically trigger pump maintenance based on runtime thresholds, preventing breakdowns during peak usage.
4. Create SOPs and Maintenance Checklists
Standardize the procedures for carrying out routine and critical maintenance activities. You should develop Standard Operating Procedures (SOPs) that define each task, the required tools, safety protocols, and the responsible personnel. Maintenance checklists help ensure consistency and accountability.
For example, in a food processing plant, the standard operating procedure (SOP) for cleaning and maintaining conveyor belts may include a daily visual check, weekly lubrication, and monthly replacement of parts to prevent contamination and mechanical failure. Provide regular training to ensure technicians stay up-to-date and maintain quality standards.
5. Track Maintenance Performance with KPIs
Select and monitor metrics that reflect the efficiency and effectiveness of your maintenance operations. Common KPIs include Mean Time Between Failures (MTBF), which indicates the frequency of asset failures; Mean Time to Repair (MTTR), which measures the efficiency of repairs; and Overall Equipment Effectiveness (OEE), which assesses the productivity of assets.
For example, if the Mean Time To Resolution (MTTR) for a packaging line drops from 3 hours to 1.5 hours after SOP optimization, that indicates a significant process improvement.
Automated Asset Maintenance Management with Software
At eWorkOrders, we help businesses manage their assets efficiently through our CMMS software. Our platform is built to simplify maintenance operations, enabling teams to schedule, track, and complete tasks with ease. Whether you’re looking to implement preventive maintenance to reduce equipment downtime or use predictive maintenance to identify potential issues before they escalate, our system is designed to support both approaches.
We serve a wide range of industries, including manufacturing, warehousing, healthcare, education, government, and facilities management. Our tools are tailored to the unique maintenance needs of each sector, supporting tasks like inspections, work order tracking, inventory control, and real-time reporting.
For those focused on warehouse preventive maintenance, we offer features to help you stay ahead of equipment failure, extend asset life, and meet safety standards. Understanding asset management is crucial, and our software gives you visibility and control over your operations from a centralized dashboard.
We offer flexible pricing plans tailored to your needs. Options start with our Standard Plan, suitable for small teams, and scale up to the Enterprise Plan for larger operations with more complex requirements. Every plan includes mobile access, unlimited work orders, and full technical support.
Discover how eWorkOrders can enhance your workflows. Book a Demo today.
Conclusion
Effective asset maintenance management minimizes downtime, extends the lifespan of assets, and reduces costs. Moreover, by implementing preventive, predictive, and condition-based strategies, organizations can proactively address issues before they escalate. To begin, a solid maintenance plan requires clear objectives, accurate asset data, and standardized procedures. Additionally, utilizing asset management software helps centralize operations, automate tasks, and track performance through key performance indicators (KPIs).
As a result, maintenance teams can align daily activities with broader operational goals, ensuring improved reliability, safety, and return on investment. Ultimately, a well-executed maintenance strategy enhances overall efficiency and performance.
Ready to optimize your maintenance operations? Contact us today.
Frequently Asked Questions
What is asset maintenance management?
Asset maintenance management is a structured process for maintaining and optimizing physical assets to ensure they operate reliably and efficiently. It involves planning, scheduling, and tracking maintenance activities to reduce downtime, control costs, and extend asset life.
What is asset maintenance software?
Asset maintenance software is a digital tool that helps teams organize, schedule, and track maintenance tasks. Whether using a simple spreadsheet or a full-featured CMMS, the goal is to minimize equipment failures, maximize uptime, and enhance asset performance.