Simplifying Sensor Deployment For Maintenance Management Services
Sensors play a crucial role in maintenance management as they provide real-time data and information about the condition of equipment, systems, and facilities. By using sensors, maintenance managers can monitor the performance of machinery and detect any anomalies or potential issues before they become major problems. Sensors can also help to optimize maintenance schedules, reduce downtime, and increase overall efficiency by allowing maintenance teams to prioritize maintenance activities based on actual usage and wear and tear. With the increasing use of the Internet of Things (IoT) technology, sensors have become even more important in maintenance management, providing a wealth of data that can be used to improve the overall performance and reliability of equipment and facilities.
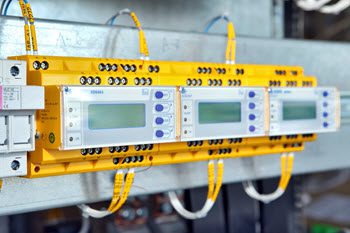
Table of Contents
TOP
- What is Sensor Monitoring?
- The Future of IoT: Opportunities for Growth and Innovation
- Exploring the Various Types and Functionality of Sensors
- Optimizing Maintenance Operations: Applications of Sensor Technology
- The Integration of Sensors and CMMS
- Business Solutions – Examples
- Maximizing ROI with Sensor-Enabled CMMS for Maintenance Operations
- Benefits of Sensor Monitoring
- Next Steps
- Final Thoughts
Mastering Sensor Deployment: Simplifying a Complex Process
(Top)
As sensors have become a critical component of modern maintenance management, organizations are tasked with managing and maintaining a large number of devices. Procurement, R&D, engineering and development work, network management, and API integration all add to the complexity of sensor deployment.
For businesses that lack the resources or budget to tackle this complex task, abandoning the project may seem like the only option. However, Computerized Maintenance Management System (CMMS) software offers a practical solution to streamline sensor management and simplify the deployment process.
This article explores the rapid growth of IoT and how the implementation of CMMS can enhance the management of sensors in maintenance operations. As the IoT advances, it becomes increasingly valuable to have a CMMS system in place for working with sensors, and this article provides a comprehensive explanation of the underlying reasons.
What is Sensor Monitoring?
(Top)
Sensor monitoring is a technology-driven process that utilizes sensors and the Internet of Things (IoT) to enable maintenance teams to remotely monitor equipment performance and identify potential issues in real time. IoT refers to the network of physical devices, vehicles, and other objects that are embedded with sensors, software, and connectivity, enabling them to collect and exchange data. The sensors installed on equipment can detect changes in temperature, pressure, vibration, or other performance indicators, and transmit the data to a centralized system through IoT-enabled connectivity. By leveraging IoT, maintenance teams can access equipment performance data in real time, analyze it, and take necessary action to optimize equipment performance and prevent downtime. Overall, the combination of sensor monitoring and IoT is a powerful tool that maintenance teams can use to optimize maintenance operations and ensure that equipment is operating at peak performance.
The Future of IoT: Opportunities for Growth and Innovation
(Top)
The Internet of Things (IoT) is a rapidly growing field that has the potential to revolutionize the way we live and work. IoT involves the use of interconnected devices to collect and share data, enabling better decision-making and process optimization. The potential for monetizing IoT is huge and vast, as businesses can leverage this technology to create new revenue streams, increase efficiency, sell data, provide services, and develop new products.
Businesses are increasingly understanding the enormous monetization potential of the Internet of Things (IoT). Businesses may collect data from linked devices to acquire important insights, streamline processes, and even establish new revenue streams by embracing IoT technology. Predictive maintenance services are a classic example of this, in which IoT sensors can monitor equipment performance and anticipate possible faults before they arise, resulting in increased equipment uptime and a new revenue stream. Furthermore, the data collected by IoT devices can be sold to third-party organizations, opening up another revenue stream. With IoT, businesses can unlock a world of opportunities to improve operations, boost revenue, and drive growth.
Overall, the potential for monetizing IoT is huge and growing. As more businesses adopt IoT technology, the opportunities for new revenue streams and increased efficiency will only continue to expand. By leveraging the power of IoT, businesses can stay ahead of the competition and drive growth in the years to come.“
Insider Intelligence forecasts that there will be more than 64 billion IoT devices installed around the world by 2026. Additionally, companies and consumers will spend nearly $15 trillion on IoT devices, solutions, and supporting systems from 2018 through 2026.
Insider Intelligence forecasts that there will be more than 64 billion IoT devices installed around the world by 2026. Additionally, companies and consumers will spend nearly $15 trillion on IoT devices, solutions, and supporting systems from 2018 through 2026.
Exploring the Various Types and Functionality of Sensors
(Top)
Sensors play a crucial role in various industries, including maintenance management. They provide valuable data that can help identify potential issues with equipment, enabling maintenance teams to address them proactively. With the rise of the Internet of Things (IoT), sensors have become even more essential, as they enable remote monitoring and control of equipment. Below, we will explore some of the most common types of sensors used in IoT and their functionality in maintenance management. Understanding the types of sensors available and their capabilities can help maintenance teams make informed decisions about which sensors to use in their maintenance operations, ultimately leading to more efficient and effective maintenance practices.
Temperature Sensors
Temperature sensors are commonly used to monitor the temperature of equipment such as engines, motors, and bearings. By continuously monitoring the temperature, maintenance personnel can identify trends and patterns that could indicate potential issues, such as overheating.
Vibration Sensors
Vibration sensors are used to monitor the vibration of equipment such as motors and pumps. By monitoring the vibration levels, maintenance personnel can identify potential issues such as unbalanced rotors or misaligned couplings.
Pressure Sensors
Pressure sensors are commonly used to monitor equipment such as hydraulic systems and boilers. By monitoring the pressure levels, maintenance personnel can identify issues such as leaks or clogs that could cause equipment failure.
Flow Sensors
Flow sensors are used to monitor the flow of fluids through pipes and equipment. By monitoring the flow rate, maintenance personnel can identify potential issues such as blockages or worn-out pumps.
Humidity Sensors
Humidity sensors are used to monitor the humidity levels in buildings and storage areas. By monitoring the humidity levels, maintenance personnel can identify potential issues such as mold growth or corrosion.
Optimizing Maintenance Operations: Applications Of Sensor Technology
(Top)
Sensor technology has revolutionized maintenance operations in various industries, enabling maintenance teams to optimize their processes and improve the reliability of equipment. By using sensors to remotely monitor the performance of equipment and detect potential issues in real-time, maintenance teams can ensure that equipment is operating at peak performance, reduce downtime, prevent unplanned maintenance, and enhance workplace safety. Below, we will explore some of the applications of sensor technology in maintenance operations:
Asset Management
One of the primary functions of a CMMS is to manage assets. With a CMMS, you can create an inventory of all the sensors you have, including their location, specifications, and maintenance history. This inventory helps you keep track of all your sensors, making it easier to manage and maintain them.
Preventive Maintenance
Preventive maintenance is essential for keeping equipment running smoothly and preventing unexpected downtime. A CMMS can help you schedule preventive maintenance for your sensors, ensuring that they are inspected, calibrated, and serviced at regular intervals. This not only helps extend the life of the sensors but also reduces the risk of unexpected failures.
Predictive Maintenance
Predictive maintenance is a proactive approach to maintenance that uses data from sensors and other sources to predict when equipment is likely to fail. By analyzing data on factors such as vibration, temperature, and other indicators of performance, maintenance teams can identify potential issues before they cause downtime or damage to equipment. Predictive maintenance can also help reduce maintenance costs by allowing maintenance teams to schedule repairs or replacements at the optimal time, rather than waiting for equipment to fail. Overall, predictive maintenance is a valuable tool for optimizing maintenance operations, improving equipment reliability, and reducing downtime.
Condition-Based Maintenance
Condition-based maintenance is a maintenance strategy that involves using sensors to continuously monitor equipment performance and detect any changes or anomalies in real time. By monitoring various parameters such as temperature, pressure, vibration, and fluid levels, maintenance teams can identify potential issues before they cause a breakdown or failure. Condition-based maintenance allows for more efficient use of resources as maintenance is only performed when necessary based on the condition of the equipment. This strategy can help reduce downtime, extend equipment life, and minimize the risk of catastrophic failures.
Work Order Management
If a sensor requires maintenance or repair, a work order can be generated in the CMMS. The work order can include information about the problem, the steps to be taken to fix it, and the parts required. The CMMS can also assign the work order to a technician, track its progress, and notify the maintenance manager when the job is complete.
Inventory Management
Managing spare parts Inventory can be a daunting task, especially if you are dealing with a large number of sensors. With a CMMS, you can keep track of your inventory, order parts when needed, and maintain accurate stock levels. This ensures that you always have the parts you need to keep your sensors running smoothly.
Analytics and Reporting
CMMS software can also help you analyze sensor data and generate reports that provide valuable insights into equipment performance, maintenance trends, and costs. By analyzing this data, you can identify opportunities for improvement, optimize maintenance schedules, and reduce costs.
The Integration of Sensors and CMMS
(Top)
Integrating sensor monitoring using CMMS is a powerful strategy for businesses looking to streamline their maintenance operations. By integrating sensors with CMMS, businesses can automate data collection, tracking, and analysis, providing real-time insights into asset performance. This enables predictive maintenance, reducing downtime and optimizing maintenance costs. For example, sensors can be used to monitor the temperature, vibration, and pressure levels of equipment such as motors, pumps, and boilers. By continuously monitoring these parameters, CMMS can identify patterns of wear and tear, leading to predictive maintenance and reducing the likelihood of equipment failure. By integrating sensor monitoring with CMMS, businesses can optimize their maintenance operations, leading to increased efficiency and cost savings.
Business Solutions – Examples
(Top)
These are just a few examples of how integrating sensor monitoring using CMMS can optimize maintenance operations, leading to increased efficiency and cost savings.
Manufacturing
A manufacturing plant that uses CMMS software can integrate vibration sensors to monitor the vibration levels of critical equipment. By integrating this data with CMMS, the software can analyze the data in real time and detect any patterns or trends that could indicate potential issues, leading to predictive maintenance.
Healthcare
A hospital that uses CMMS software can integrate temperature and humidity sensors in its medical storage rooms. The sensors can collect data on the temperature and humidity levels, and the data can be integrated with CMMS to monitor the performance of the equipment stored in the room. This enables the hospital to detect any deviations from standard parameters early, leading to timely corrective action.
Building Management
A building management company that uses CMMS software can integrate humidity sensors to monitor the humidity levels in its buildings. By integrating the humidity data with CMMS, the software can analyze the data in real time and detect any deviations from standard parameters, leading to timely corrective action.
Energy Company
An energy company that uses CMMS software can integrate temperature sensors to monitor the temperature of its turbines. By integrating this data with CMMS, the software can analyze the data in real time and detect any patterns or trends that could indicate potential issues, leading to predictive maintenance.
Food and Beverage
A food and beverage manufacturing plant that uses CMMS software can integrate pH sensors to monitor the pH levels of its product during the production process. By integrating the pH data with CMMS, the software can analyze the data in real time and detect any deviations from standard parameters, leading to timely corrective action.
Facility Management Company
A facility management company that uses CMMS software can integrate carbon monoxide sensors to monitor the air quality in its buildings. By integrating the carbon monoxide data with CMMS, the software can detect any deviations from standard parameters and alert the appropriate personnel to take corrective action.
Agriculture
Integrating sensor monitoring with CMMS can help optimize maintenance operations by providing real-time data on equipment performance, such as irrigation systems and machinery used in harvesting. This can help identify potential problems before they become critical, reducing downtime and increasing efficiency.
Hospitality
In the hospitality industry, integrating sensors with CMMS can help optimize maintenance operations by automating preventive maintenance tasks for critical systems such as HVAC, lighting, and kitchen equipment. This can help ensure that facilities are always in good working order, reducing downtime and improving guest satisfaction.
Retail
In the retail industry, integrating sensor monitoring with CMMS can help optimize maintenance operations by providing real-time data on equipment performance, such as refrigeration systems and lighting. This can help identify potential problems before they become critical, reducing downtime and increasing energy efficiency.
All industries can benefit from Senor Maintenance Management.
Maximizing ROI with Sensor-Enabled CMMS for Maintenance Operations
(Top)
Maximizing Return on Investment (ROI) is a key goal for any organization, and integrating sensor-enabled CMMS into maintenance operations can be an effective way to achieve this. By leveraging sensor technology, maintenance personnel can monitor equipment health in real-time, identify potential issues before they become major problems, and schedule maintenance proactively, reducing downtime and associated costs. Sensor-enabled CMMS can also facilitate predictive maintenance, reducing the need for reactive maintenance, which can be more costly and time-consuming. The integration of sensors and CMMS can improve decision-making by providing valuable insights into equipment performance, usage, and maintenance needs, enabling informed decisions and proactive maintenance. By minimizing downtime and improving equipment reliability, organizations can increase productivity, efficiency, and profitability, maximizing ROI.
Benefits of Sensor Monitoring
(Top)
Real-Time Monitoring
Sensors can provide real-time data on the performance of equipment, allowing maintenance teams to identify potential issues before they become major problems.
Improved Maintenance Efficiency
By using sensors, maintenance teams can optimize maintenance schedules and reduce the time and cost associated with manual inspections and maintenance tasks.
Cost savings
By detecting and addressing issues early, sensors can help reduce the cost of repairs and extend the lifespan of the equipment.
Increased Safety
Sensors can help identify potential safety hazards and prevent accidents in the workplace.
Better Data for Decision-Making
The data collected by sensors can be analyzed to identify patterns and trends, allowing maintenance teams to make data-driven decisions about maintenance schedules, repairs, and replacements.
Predictive Maintenance
Sensors can be used to collect data on equipment performance over time, enabling maintenance teams to predict when maintenance will be required and schedule it proactively. This can help reduce downtime and prevent unplanned maintenance.
Condition-Based Maintenance
By using sensors to monitor the actual condition of equipment, maintenance teams can optimize maintenance schedules and reduce the amount of unnecessary maintenance.
Remote Monitoring
Sensors can be used to remotely monitor equipment performance, allowing maintenance teams to identify and address issues without having to physically inspect the equipment.
Improved Asset Tracking
By using sensors to track asset performance and maintenance history, maintenance teams can make more informed decisions about when to repair or replace equipment. This can help optimize maintenance schedules and reduce costs.
Increased Equipment Reliability
By using sensors to monitor equipment performance and detect potential issues, maintenance teams can ensure that equipment is operating at peak performance and reduce the risk of breakdowns or failures.
Next Steps
(Top)
Incorporating a CMMS into your maintenance operations can significantly improve the efficiency and flexibility of your maintenance processes. With its automated data collection and real-time equipment status updates, CMMS enables organizations to optimize maintenance planning, scheduling, and execution, minimize unexpected downtime, and extend equipment lifespan. To learn more about how eWorkOrders’ CMMS can benefit your business, or to request a demo, please contact our team today. We are always available to answer any questions and help you take the next step toward efficient and effective maintenance management.
Final Thoughts
(Top)
In summary, using sensors for maintenance provides several benefits to organizations across industries. These benefits include real-time monitoring, improved maintenance efficiency, cost savings, increased safety, and better data for decision-making. Sensors also enable predictive and condition-based maintenance, remote monitoring, improved asset tracking, and increased equipment reliability. By leveraging sensor data, maintenance teams can optimize maintenance schedules, reduce costs, improve safety, and increase the reliability of equipment. Overall, using sensors in maintenance operations can help organizations move from a reactive to a proactive maintenance approach, leading to increased efficiency and reduced downtime.