Effective maintenance management is essential for maximizing equipment performance and longevity. Businesses achieve this through the use of maintenance metrics and key performance indicators (KPIs) to measure and monitor the effectiveness of their maintenance processes. By analyzing these metrics and KPIs, companies can identify areas for improvement and develop strategies to reduce downtime, increase efficiency, and ultimately enhance profitability. In this guide, we’ll delve into the most critical maintenance metrics and KPIs, what they measure, and how to use them effectively to optimize maintenance management and equipment health.
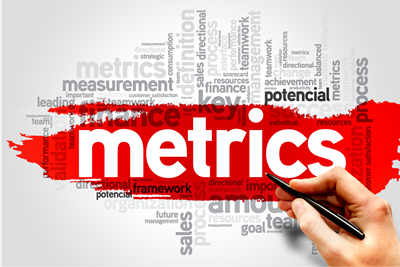
Table Of Contents
What Are Maintenance Metrics?
(Top)
Maintenance metrics are performance indicators used to measure and track the effectiveness of maintenance processes in order to optimize equipment health, reduce downtime, and increase overall business profitability. These metrics provide valuable insights into various aspects of maintenance management, including equipment reliability, maintenance costs, work efficiency, and more. By regularly tracking and analyzing maintenance metrics, organizations can identify areas for improvement and develop effective maintenance strategies to achieve their operational goals.
What Is A Metric?
(Top)
A metric is a numerical value that an organization monitors to gain insights into its processes. While some metrics may be more relevant for tracking progress than others, each metric serves a purpose in providing visibility into an aspect of the organization. For instance, monitoring compliance with preventive maintenance schedules may not directly impact overall profitability, but it can reveal the effectiveness of maintenance processes.
What Are KPIs?
(Top)
Maintenance KPIs, or Key Performance Indicators, are specific metrics used to measure and track the performance of maintenance activities in an organization. These metrics are typically tied to specific goals or objectives and help management evaluate whether maintenance activities are meeting those targets. Maintenance KPIs can include a wide range of measurements, such as equipment uptime, maintenance costs, mean time between failures (MTBF), mean time to repair (MTTR), and overall equipment effectiveness (OEE). By tracking maintenance KPIs, organizations can identify areas for improvement and develop strategies to optimize maintenance performance.
Breaking Down Maintenance Measurements: Metrics Vs. KPIs
(Top)
Maintenance measurements are critical for ensuring the optimal performance and longevity of equipment and machinery. Two types of maintenance measurements that businesses rely on are metrics and key performance indicators (KPIs). While they may seem similar, they have distinct differences.
Metrics are quantitative measures of performance that organizations track to monitor their processes’ effectiveness. They are objective and provide data to help organizations understand how their maintenance processes are performing. Metrics are often used to identify areas for improvement and develop effective maintenance strategies that reduce downtime, increase equipment efficiency, and ultimately improve business profitability.
Examples of maintenance metrics include equipment downtime, mean time between failures, scheduled maintenance compliance, mean time to repair, and maintenance costs.
On the other hand, KPIs are more strategic and focus on measuring progress toward specific business objectives. KPIs are used to evaluate the success of maintenance initiatives and help organizations make informed decisions about resource allocation. They are typically high-level, qualitative measures of performance that are closely tied to business goals and objectives.
Examples of maintenance KPIs include overall equipment effectiveness (OEE), return on investment (ROI) of maintenance initiatives, equipment availability, and maintenance backlog.
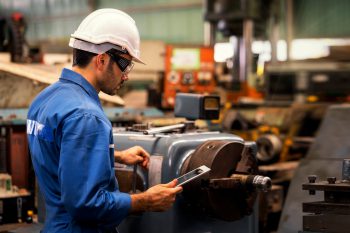
Differentiating Between Leading And Lagging Indicators
(Top)
To effectively manage maintenance operations, it is important to differentiate between leading and lagging indicators. Leading indicators are forward-looking metrics that provide insight into future performance while lagging indicators are retrospective metrics that describe past performance.
An example of a lagging indicator in maintenance management is equipment downtime, which measures the amount of time equipment was down in the past. In contrast, a leading indicator like preventive maintenance compliance can predict the likelihood of equipment downtime in the future.
While lagging indicators are useful for evaluating past performance and identifying areas for improvement, leading indicators are crucial for predicting and preventing potential problems before they occur. By focusing on leading indicators, maintenance managers can take proactive steps to improve equipment reliability, reduce downtime, and optimize maintenance operations.
Some examples of leading indicators in maintenance management include the number of maintenance requests or work orders submitted, the frequency of preventive maintenance activities, or the number of hours of training provided to maintenance personnel. On the other hand, examples of lagging indicators in maintenance management might include equipment downtime, maintenance costs, or equipment failure rates.
By using a balanced approach that combines both leading and lagging indicators, maintenance managers can gain valuable insights into their maintenance processes, identify areas for improvement, and ultimately, achieve their maintenance performance goals.
The Importance Of Maintenance Management Metrics
(Top)
Maintenance management metrics play a critical role in assessing the effectiveness of maintenance processes and identifying areas for improvement. By measuring key performance indicators (KPIs) and metrics, businesses can monitor maintenance performance and equipment health, ultimately leading to increased uptime, improved safety, and reduced costs.
One of the primary benefits of maintenance management metrics is that they provide visibility into maintenance activities, helping businesses identify trends and patterns in equipment performance. For example, tracking the mean time between failures (MTBF) can reveal whether the equipment is performing as expected or experiencing more frequent breakdowns than anticipated. This information can then be used to adjust maintenance schedules, reduce downtime, and optimize asset utilization.
Maintenance management metrics also allow businesses to track the effectiveness of maintenance programs and identify areas for improvement. For instance, tracking the percentage of preventive maintenance (PM) tasks completed on time can reveal whether PM schedules are realistic and achievable or need adjustment. Similarly, tracking the ratio of corrective maintenance (CM) to preventive maintenance (PM) tasks can highlight areas where equipment is frequently breaking down, indicating a need for more effective maintenance strategies.
Another critical benefit of maintenance management metrics is their ability to support data-driven decision-making. By providing objective, quantitative data, maintenance metrics can help businesses make informed decisions about maintenance strategies, equipment replacement, and resource allocation. For example, if a piece of equipment has a high total cost of ownership (TCO) due to frequent breakdowns and repair costs, maintenance metrics can help justify investing in a replacement asset or upgrading the existing equipment.
Overall, maintenance management metrics are an essential tool for businesses seeking to optimize maintenance performance, reduce costs, and improve equipment health. By tracking key performance indicators and metrics, businesses can gain valuable insights into maintenance processes, identify areas for improvement, and make informed decisions about equipment maintenance and replacement.
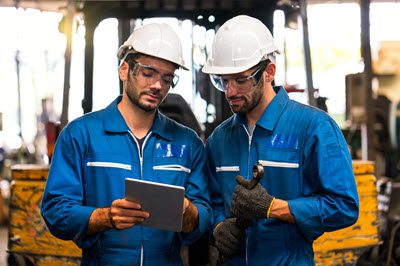
Advantages Of Maintenance KPIs
(Top)
The following are some of the main advantages of maintenance management metrics:
Increased Equipment Reliability: By monitoring indicators like the mean time between failures and downtime, businesses can identify equipment problems early and fix them before they become expensive failures.
Reduced Maintenance Expenses: Organizations can find opportunities to save costs and boost efficiency by monitoring measures like maintenance costs and labor hours.
Increased Safety: Organizations can identify possible hazards and take action to mitigate them by measuring metrics like safety incidents and near misses.
Enhance Decision-Making: Organizations can make data-driven decisions about resource allocation, equipment procurement, and other crucial maintenance-related decisions by examining data on various maintenance indicators.
Improved Communications: Metrics for maintenance management can assist managers in informing higher management, stakeholders, and other departments about the performance of their departments.
Compliance: KPIs for maintenance must be tracked and monitored in sectors like aviation, healthcare, and transportation. Setting and monitoring maintenance KPIs can aid firms in adhering to rules and specifications.
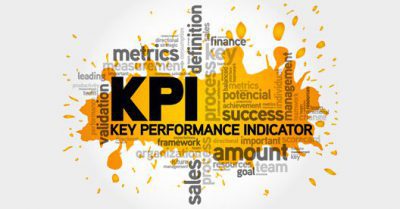
Types of Maintenance Management Metrics
(Top)
Metrics are crucial to understanding, diagnosing, and resolving the issues that prevent your maintenance organization from operating at peak efficiency. Each metric provides a different insight into the performance of your maintenance operations. When used together, they can give you a more comprehensive insight into how successful your team is in resolving issues and where the team can improve. Although there are many different types of metrics that can also be valuable, these are the standard metrics tools that are most commonly used and will give you a good understanding of your overall maintenance operations.
Equipment Downtime
The equipment downtime metric is used to determine the duration of time that a particular piece of equipment is not operational or available for use. This can encompass both scheduled downtime for maintenance purposes, like repairs, preventive maintenance, and inspections, as well as unscheduled downtime arising from equipment failures or breakdowns.
Tracking equipment downtime is critical for maintenance managers to evaluate equipment performance and identify areas for improvement. By keeping tabs on downtime metrics, maintenance teams can examine the root causes of equipment failures and take measures to decrease the time equipment spends out of service.
The measurement of equipment downtime can take many forms, such as total downtime per equipment unit, average downtime per incident, and downtime as a percentage of total available operating time. The information obtained from these measurements can be used to compute key performance indicators (KPIs) and assist in maintenance decision-making.
Maintenance Backlog
The maintenance backlog metric refers to the accumulation of maintenance work that has not been completed within a specified timeframe. This pending work may be unassigned to a technician or unfinished due to a lack of resources or low priority.
Tracking the maintenance backlog metric is crucial for maintenance managers to understand how much work is pending and where additional resources or prioritization are necessary. By monitoring maintenance backlog metrics, maintenance teams can prioritize work, allocate resources, and improve maintenance scheduling to ensure timely completion of work orders.
There are several ways to measure maintenance backlog, including counting the number of work orders awaiting completion, calculating the average time to complete a work order, or measuring the percentage of work orders completed within a specified timeframe. The data collected from these measurements can be used to calculate key performance indicators (KPIs) and inform maintenance decision-making.
Mean Time to Detection (MTTD)
MTTD is a metric used in maintenance management to measure the average time it takes to detect a problem or issue with a piece of equipment or system. It is the time interval between the occurrence of an issue and the moment when it is detected and recorded.
MTTD is an important metric because it helps maintenance teams to identify how quickly they can detect equipment failures, diagnose the root cause, and implement corrective actions to prevent further damage or downtime. By reducing the MTTD, maintenance teams can minimize the impact of equipment failures and improve equipment reliability and uptime.
MTTD can be calculated by dividing the total time between the occurrence of an issue and the moment it was detected by the number of occurrences. The data collected from MTTD can be used to identify areas for improvement and track the effectiveness of maintenance strategies over time.
Mean Time to Acknowledge (MTTA)
MTTA is a maintenance metric that measures the average time it takes for a maintenance team to acknowledge a work order or maintenance request. It is calculated by taking the total time between the creation of the work order and the first acknowledgment by the maintenance team and dividing it by the total number of work orders.
MTTA = Total time to acknowledge work order / Total number of work orders
MTTA is an important metric to track, as it provides insights into how quickly maintenance teams are responding to maintenance requests and can help identify areas for improvement in maintenance processes.
Mean Time to Respond (MTTR)
Mean Time to Respond is a maintenance metric that measures the average time it takes for a maintenance team to respond to an equipment issue or failure and restore the equipment to its normal operating condition. It includes the time it takes to diagnose the problem, plan and schedule the maintenance work, and complete the repairs.
MTTR is an important metric for maintenance teams as it helps them assess the effectiveness of their maintenance operations and identify areas for improvement. A lower MTTR indicates that maintenance teams are able to respond quickly to equipment failures, reducing downtime and minimizing the impact on production.
MTTR can be calculated by dividing the total time it takes to respond to an equipment failure by the number of maintenance incidents during a given time period.
Mean Time to Repair (MTTR)
Mean Time to Repair is a maintenance metric that measures the average time it takes to repair a piece of equipment after a failure or breakdown has occurred. This metric includes the time it takes to identify the problem, schedule repairs, obtain necessary parts or materials, and complete the repair work.
MTTR is a critical metric for maintenance managers to understand how efficiently their maintenance team can restore equipment to its operational state. A lower MTTR indicates that equipment failures are being addressed quickly, reducing downtime and improving productivity.
To calculate MTTR, the total downtime for a piece of equipment is divided by the number of repairs made during a given period. The resulting value represents the average time it takes to repair equipment.
Mean Time to Resolve (MTTR)
Mean Time to Resolve is a maintenance metric that measures the average time it takes to resolve or fix a maintenance issue after it has been reported. It includes the time it takes to respond to the reported issue, diagnose the problem, obtain the necessary parts or resources, and complete the repair work.
To calculate MTTR, the total time it takes to resolve a maintenance issue is divided by the number of reported issues during a specific period. The resulting figure gives the average time taken to resolve each issue. A lower MTTR indicates that maintenance teams are responding to and resolving issues more efficiently, which helps to minimize equipment downtime and improve overall maintenance performance.
Mean Time to Recovery (MTTR)
Mean Time to Recovery is a maintenance metric that measures the average time it takes to restore a failed asset or system to normal operating condition after a failure or downtime event. It is the duration of time from the moment the failure or downtime event is detected until the asset or system is fully operational again. The MTTR metric is often used to assess the effectiveness of maintenance teams in responding to and resolving unplanned downtime events.
To calculate MTTR, the total downtime for an asset or system is divided by the number of repair events during a specific period. The result is the average time it takes to repair the asset or system after a failure. The MTTR metric can be used to identify opportunities for improvement in maintenance processes, such as reducing the time it takes to diagnose issues, acquire replacement parts, or perform repairs.
Mean Time Between Failures (MTBF)
Mean Time Between Failuares is a reliability metric that measures the average time between two failures of a system or a component. It is a measure of how long a system or a component can be expected to operate before experiencing a failure. MTBF is calculated by dividing the total operating time by the number of failures that occurred during that time. MTBF is commonly used in the maintenance and reliability industries to predict and improve the reliability of systems and components. A higher MTBF indicates a more reliable system or component, while a lower MTBF indicates a less reliable one.
Mean Time To Failure (MTTF)
Meantime Between Failures is a metric that measures the average time that a system or component operates before it fails. Unlike MTBF, MTTF does not take into account repair time or maintenance activities. MTTF is often used to predict the reliability of a system or component, and it is calculated by dividing the total operating time by the number of failures.
Planned Maintenance Percentage (PMP)
Planned Maintenance Percentage is a maintenance metric that measures the percentage of maintenance activities that are planned or scheduled in advance, out of the total maintenance activities performed. PMP is an important indicator of a company’s maintenance performance as it shows how much maintenance is performed proactively to prevent equipment failure, compared to reactive maintenance done after a failure occurs.
To calculate PMP, the total number of planned maintenance hours is divided by the total number of maintenance hours performed (both planned and unplanned) over a specific time period, usually a month or a year. The resulting percentage reflects the proportion of maintenance activities that were planned versus unplanned. A higher PMP indicates that more maintenance activities are scheduled in advance, reducing downtime and improving equipment reliability.
Overall Equipment Effectiveness (OEE)
Overall Equipment Effectiveness is a performance metric that measures the overall efficiency and effectiveness of a manufacturing or production process. It is calculated by multiplying three factors: availability, performance, and quality.
The availability factor measures the percentage of time the equipment is available for production, while the performance factor measures the speed at which the equipment runs compared to its maximum capacity. The quality factor measures the percentage of products that meet quality standards.
By measuring OEE, manufacturers can identify areas where the production process can be improved to increase efficiency, reduce downtime, and improve product quality. OEE can also be used to track the effectiveness of maintenance efforts and identify areas for improvement.
Maintenance Cost As A Percentage of RAV
Maintenance Cost As A Percentage of RAV refers to the ratio of maintenance costs incurred on an asset to its replacement asset value (RAV). RAV is the estimated cost of replacing the asset at the end of its useful life.
This maintenance metric is used to assess the efficiency of the maintenance program and the cost-effectiveness of maintenance activities. A higher percentage indicates that more maintenance costs are being incurred relative to the asset’s value, while a lower percentage indicates a more efficient maintenance program.
To calculate maintenance cost as a percentage of RAV, the total maintenance costs for an asset are divided by its RAV and then multiplied by 100 to express the result as a percentage.
Average days To Complete Work Orders is a maintenance metric that measures the average number of days it takes to complete a maintenance work order, from the time it was submitted to the time it was closed out. It provides insight into the efficiency of maintenance processes and can help identify areas for improvement in terms of work order prioritization, resource allocation, and scheduling. The calculation for this metric is the total number of days to complete all work orders divided by the total number of work orders completed within a specified time period.
Percentage Of Work Covered By A Work Order
Percentage Of Work Covered By A Work Order is a maintenance metric that measures the extent to which a work order captures all the necessary tasks and activities required to complete a maintenance job. It indicates the degree to which maintenance activities are effectively planned and executed.
For example, if a work order covers all the necessary tasks required to complete a maintenance job, then the percentage of work covered by the work order is 100%. If a work order only covers some of the tasks required to complete the job, then the percentage of work covered by the work order would be less than 100%.
To calculate the percentage of work covered by a work order, the total number of tasks or activities covered by the work order is divided by the total number of tasks or activities required to complete the maintenance job and then multiplied by 100 to express the result as a percentage.
Key Considerations for Selecting Maintenance Metrics
(Top)
Relevance: The metric should be relevant to the maintenance goals and objectives of the organization.
Measurability: The metric should be measurable and provide accurate data that can be used to make informed decisions.
Assets: Consider what type of assets are being tracked and how critical they are to the organization.
Existing Tracking: Consider what metrics are already being tracked and if they are providing useful information.
Actionability: The metric should provide information that can be acted upon to improve maintenance performance.
Timeliness: The metric should be timely, meaning that it should be available when needed and not require excessive time or effort to obtain.
Consistency: The metric should be consistent over time and across different organizational departments or locations.
Cost-Effectiveness: The cost of measuring the metric should be reasonable in relation to the benefits gained from the information it provides.
Compatibility: The metric should be compatible with existing systems and processes within the organization.
Accessibility: The metric should be easily accessible to those who need it within the organization.
Understandability: The metric should be easily understood by those who will be using it.
Alignment: The metric should align with the organization’s overall strategy and goals.
Understanding Cause and Effect Relationships in Maintenance Metrics: When selecting leading indicators for maintenance metrics, it’s crucial to consider cause and effect relationships. The metrics must have a significant impact on achieving desired results, and they should be predictive in nature. Trial and error are often required to determine whether a metric is genuinely predictive.
One way to determine cause-and-effect relationships is by tracking data and seeing if lagging indicators correlate with the selected leading indicators. Additionally, existing studies can provide insight into the cause-and-effect relationships of maintenance metrics. For instance, studies have shown that preventive maintenance leads to cost savings of 12% to 18% compared to reactive maintenance. Therefore, tracking and improving preventive maintenance as a metric may help reduce unplanned downtime.
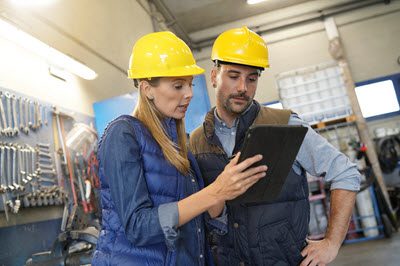
Data Security
(Top)
In today’s digital age, data security has become a critical concern for individuals and organizations alike. With the increasing amount of sensitive information being stored and transmitted online, the risks of cyberattacks, data breaches, and other forms of malicious activities have also grown exponentially. The consequences of a security breach can be severe, ranging from financial losses, legal liabilities, damage to reputation, to the compromise of personal information. Therefore, it is crucial to implement robust data security measures that protect data at rest, in transit, and in use.
To mitigate these risks, it is essential to implement robust data security measures, such as encryption, access controls, and regular backups, to safeguard data from unauthorized access, theft, and corruption. At eWorkOrders, we strive to exceed the norm and are deeply committed to delivering a platform that is not only highly reliable but also exceptionally secure. Our focus on security goes beyond standard industry processes and protocols, and we continuously work to ensure that our user’s data is always protected. We have implemented a strict security program an have partnered with SecurityScorecard to continuously assess our security controls and identify potential vulnerabilities. Unlike many competitors, At eWorkOrders, we understand the paramount importance of cybersecurity and are proud to hold high scores across all categories that pose a threat, including Application Security Network Security, and more.
Conclusion
(Top)
Metrics and KPIs are essential tools to maintain the efficient operation of your facility. By selecting a few key metrics and KPIs, your management team can monitor changes and measure their effectiveness. Choosing the appropriate metrics is a process that depends on the asset’s criticality and your business objectives. Sometimes, you have substantial research to support specific metrics, while in other cases, you may need to engage in some trial and error to identify what is worth measuring. In either case, selecting the appropriate metrics will help improve your maintenance planning and enhance your maintenance team’s efficiency.
Other Resouces
(Top)
Transform your maintenance team and drive business success with eWorkOrders – the ideal CMMS solution. With the ability to track numerous metrics, KPIs, and objectives, eWorkOrders empowers you to achieve your business goals effortlessly. Take the first step towards revolutionizing your maintenance team and optimizing KPIs by trying out eWorkOrders today.
Maintenance Management Terms & Definitions