The primary function of a forklift is the speedy and effective transportation of materials and goods across a range of sectors. Modern forklifts are strong and durable, but due to their numerous moving parts and continuous use, repairs will eventually be necessary.
The proper upkeep of forklifts may appear to be an expensive hassle. It may seem like a waste of time and money to pay for the replacement of hoses, fluids, forks, or tires before they break and to set up preventive maintenance schedules.
However, the truth is that regular forklift maintenance is essential to avoiding expensive failures, unnecessary downtime, and extending the life of your forklifts. With the right maintenance routine, you will be able to identify minor issues before they grow into larger and more expensive ones.
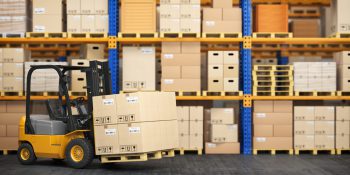
Tips to Diagnose A Forklift Problem
In this article, we’ll offer some tips on how to recognize some of the most typical forklift problems. In experiencing any of the failures below, you may need to do a little more troubleshooting to determine the source of the problem because we all know there are unique circumstances that may make an issue more complex.
Starting Issues
Battery Issues
Forklift starting issues are frequently simple to fix. The actions you choose will be influenced by the forklift’s power source. To diagnose an electric forklift, take the following actions:
The battery is probably the problem if you crank the ignition and hear a simple clicking sound instead of an engine sound.
First, confirm that:
- Your battery is charged and properly connected.
- Verify your battery’s level of charging: How recently was the battery charged?
- Temperature: If it’s too chilly outside, your battery might not be functioning. A forklift battery can struggle to start in subzero temperatures, just like a vehicle.
- Verify all auxiliary features: Check the functionality of your lights, brakes, and other systems. If they are not working you might need to completely recharge your battery. If you have a battery that has recently been recharged, and still not working, it is time to replace it.
Other Starting Issues
Starting problems could be more complicated if your forklift runs on internal combustion. Follow these troubleshooting instructions:
- Establish the fuel’s age: How long has the fuel been in your tank? If the fuel is old, this may be a good indication of why your forklift is difficult to start.
- Check the level of your oil: Some forklift models won’t open the fuel valve until there is a specified volume of oil in the tank.
- Detect fuel leaks: There may be a leak if the gas smell is extremely powerful.
- Examine the battery: If none of the above solutions work to fix your issue, check to verify if your battery is fully charged.
- Verify the coolant: Check the level of your coolant to see if your battery has an adequate charge. Forklifts can occasionally fail to start because of overheating, which is caused by a blocked radiator or a shortage of coolant. Clean the radiator or add more if necessary.
- Weighted seats: A common safety feature on forklifts prevents them from starting unless there is weight in the seat. Before attempting to start the forklift, make sure you are seated securely and completely in the seat.
Engine Not Starting, But Makes a Sound
If the engine turns over but won’t start, before ruling out that it is the battery, check to see if the battery is low and not able to supply the ignition system properly.
Are there any warning lights on? Does the dashboard illuminate normally? If so, your battery or electrics are most likely unrelated to the issue.
If the battery is functioning, there may be a variety of other problems that an engineer needs to investigate.
Some of these issues may be:
Spark Plugs
Spark plugs are a typical cause of forklifts that turn over but won’t start. You can assess the spark’s intensity if you have a spark tester. The plug might need to be changed if the spark is feeble and yellow. A strong, blue spark is an excellent spark.
The condenser, rotor, and coil wires are further ignition system components that need to be examined. Any of these components that have corroded or been damaged require replacement. Even if they are not the main source of the problem, performing this maintenance is wise.
Fuel System
If your ignition system is operating properly, a fuel system issue may be present. Some of the parts that you might want to look at are the fuel filter, lock-off valve, fuel regulator, and tank connector (LPG).
Elimination is the first step in troubleshooting a forklift that turns over but won’t start. If you have a mechanic on-site, they might be able to identify the problematic part (or parts) with simple visual inspections and testing.
Emergency Power Off (Kill Switch)
There is an emergency stop button on forklifts. Before the forklift will start again, this must be deactivated if it was activated the previous time the forklift was in operation.
Steering Issues
Forklifts can be difficult to drive, especially in confined spaces. It’s important to ensure that your steering is working properly because steering issues might result in accidents that injure operators or others nearby.
It can be challenging to spot a steering problem at times. A few things to look for are:
- Hearing strange noises when turning the wheel, particularly if this occurs when the forklift is loaded. This can indicate that the steering system is rusting out or that there is a problem with the hydraulics that regulate steering pressure.
- Low steering fluid levels. If adding more liquid doesn’t resolve the issue then you need to continue investigating other possibilities.
- Check the steering fluid consistency, if it is thick and gooey, you should completely replace the fluid.
- Unbalanced tires can cause a bent axle as well as general instability and excessively worn tires put extra strain on your forklift’s transmission, which can cause a breakdown and/or shorten the life of the forklift.
- Pressure valves that are rusted, loose, or worn out should be left for a qualified forklift repair specialist.
- Rusted out gears or worn-out gears should be left for a qualified forklift repair specialist.
Worn-out Tires and Suspension
A forklift may not travel very far, but it is used frequently and is capable of carrying heavy loads, which puts strain on the tires and eventually wears them out. To maintain traction and forklift operating stability, it is best to replace any worn-out tires. It’s the same with suspension systems that react to the load and provides stability.
Mast Temperatures
The mast, which controls the forklift’s lifting, lowering, and tilting, frequently causes trouble. The carriage, which is propelled by a hydraulic piston positioned in the middle of the mast, and the forks, which support loads, are fastened to the mast. The hydraulic force of this piston is used by the mast to lift loads, while gravity is used to descend burdens. Forklifts frequently raise loads in phases, which might result in a number of problems. Typical mast-related problems include improper lifting or lowering, too-slow lifting, and jerky lifting and lowering.
Cold Temperatures
Forklifts powered by liquid propane gas (LPG) and electric forklifts, in particular, can have problems after being left outside in the cold. Low temperatures have the potential to cause battery failure by thickening the electrolyte. A weak battery can also impact LPG fuel, and in really cold weather, fuel regulators can also freeze.
Due to rough starts, gas and diesel forklifts consume more fuel in colder weather. Additionally, if the tank is running low or empty, condensation may accumulate and cause the engine to stutter and malfunction when started.
Avoid this by:
- Run the forklift engine for at least 10 minutes to warm up the engine before starting work.
- Keeping forklifts inside or outside under a shelter.
- Ensuring forklifts are well-fueled.
Break Issues
Brake failures could result in fatal workplace accidents and keep your forklift out of commission permanently.
If you discover that your forklift brakes need repair or maintenance frequently, it may be the result of some typical mistakes, such as:
- Operators leaving the parking brake engaged.
- Attempting to brake too quickly without allowing your forklift enough time to slow down.
- Driving with your foot permanently on the brake pedal, and only ever partially applying the brakes.
- Driving too fast and needing to hit the brakes harder each time you want to stop.
- Adding brake fluid to a hydraulic oil-only system.
- Operating the forklift even with the brake shoes needs to be replaced or repaired.
The easiest approach to prevent these issues, minimize the expensive repairs and prevent costly accidents is to ensure that your operators are properly trained on the best driving practices and keep your forklifts well maintained. For instance, checking the brakes every day will help you spot soft or leaky brakes early on, and replacing worn rotors and brake pads can help you avoid more costly damage.
Broken Forks
Forklift forks will eventually wear out, crack, bend or break and require pricey repairs. Dealing with workplace hazards brought on by fork failure and replacing products that are destroyed or damaged when the forks fail could be much more expensive. Forklift maintenance practices include daily fork inspection, quick replacement of weak or cracked forks and parts, and adherence to industry standards for replacing thinning forks to help stop breakage (and its effects) before they occur.
It’s crucial to spot wear issues and change the forks before they break. Below are some signals that any forklift driver should be aware of:
- A fork’s metal eventually deteriorates. The metal deterioration puts additional stress on the forks and can reduce the load capacity significantly. Because it is difficult to notice the wear, it is a good idea to use forklift calipers to measure the shaft to establish a baseline. Next, compare the thickness of the fork blade, heel, and hook to your base measurement.
- Replace the fork if either the shank or the blade is bent more than 93 degrees (s). Bending the fork back into place is a dangerous fix.
- Fork hooks that are bent or worn should be measured using a caliper to check for wear and straightness. The fork(s) has to be replaced if the hook’s lip touches the back of the caliper.
- Uneven blade height – both forklift blade tips should be at the same height (approximately). It’s time to replace the forks if there is a blade length discrepancy.
- Surface cracks are common in the heel region and near welds.
Leaks
Clamps, hoses, and o-rings are frequently used by forklifts in their cooling, drivetrain, and hydraulic systems, and are the most common source of forklift oil leaks.
Leaks are avoided with proactive forklift maintenance. Regularly check the wear on the hoses to determine where the leak is most likely to happen. Next, keep an eye out for any loose clamps and fittings before they cause an issue.
Hose Failures
Damaged or cracked hoses can keep a forklift off the job for an extended period of time and cost a lot of money, especially if the failure causes additional harm to the forklift.
Damaged hoses can be avoided with proactive forklift maintenance. Hoses that are weakening can be found and replaced before they fail, greatly reducing the likelihood of problems developing.
Safety
In the manufacturing industry, warehouses are growing every year, and forklifts are not going away. It is important that all businesses that use forklifts should place a high priority on safety.
Unfortunately, working with any piece of equipment, accidents do happen. Even though it is impossible to predict such accidents, they can be avoided with the right training and proper equipment upkeep. Some of the most frequent forklift accidents include:
- Operator/Driver Poorly Trained
- Operator/Driver Does Not Follow Regulations
- Operator/Driver Ignores Signs of Possible Problems
- Overconfident Drivers Tend to Speed
- Faulty Equipment
- Maintenance Schedules are Ignored
- Giving Rides Using the Mast
- Load is Not Secure
- Forklift Markings Ignored
- Heavy Loads have a tendency to Toppling Over
Failure of Safety Accessories
Any forklift will have safety accessories like horns, sirens, and lights. With the frequent use of these accessories, these parts get deteriorate or break over time.
Broken wires, grimy contacts or pins, damaged light bulbs, defective assemblies, or blown fuses can all cause accessories to stop operating.
Damaged accessories can be avoided with proactive forklift maintenance. Cleaning and lubricating electrical contacts on the accessories, using dielectric grease, or tune-up grease, can be used to clean and lubricate the electrical contacts on the accessories to help reduce wear. Change light bulbs as soon as you can.
OSHA Compliance
It is always a good idea to keep your forklifts in good repair. Regular forklift maintenance is crucial since OSHA mandates it, and it is a good idea to prevent mechanical and workplace issues and is also necessary to comply with regulations.
You need to check the OSCHA requirements to make sure that you conform to their guidelines.
If you ignore OSHA regulations, you run the risk of being in violation, which can lead to some very heavy penalties.
When to Call an Expert
Knowing the most common forklift issues and how to fix them will help you be more prepared in handling some of the most common situations. Remember, that the majority of repairs, including technical ones and part replacements, should still be left to trained professionals. To save money, you might be tempted to perform these repairs yourself, but doing so puts your employees and your equipment at risk. In fact, some of the most costly forklift repairs occur when nonprofessionals try to solve a problem but end up making it worse.
Summarizing – How To Avoid Common Forklift Problems
Owning forklift(s), your goal is to keep them running as long as possible, making sure you follow all of the regulations, and most important is keeping your operators and employees safe.
How do you meet all of these challenges and keep your business running? To meet these challenges, you need a comprehensive forklift maintenance plan to manage all of these tasks, easy to use, and doesn’t cost a bundle so that you can get back to running your business. That is where Computerized Maintenance Management System (CMMS) software can help you manage all of these tasks and more. Some of the things our CMMS can provide to help automate and streamline processes include:
- Tracking all of your assets by keeping detailed information on your equipment from purchase through retirement.
- Setting up preventive maintenance schedules that are convenient for your business operations.
- Get automated notifications of maintenance tasks and schedules.
- Creating detailed checklists and attaching them to work orders.
- Keeping track of spare parts inventory and set levels so that you can get notifications when they meet defined thresholds.
- Prioritize work orders because of unexpected emergencies.
- Create checklists and attach them to work orders. Be prepared for OSHA, ASME, and CMAA inspections.
- Upload pictures, manuals, and schematics and have them available from anywhere.
- Manage resources more efficiently.
- Our signature capture feature gives you the assurance that repairs have been made and who made the repairs.
- Create and access hundreds of reports to meet your needs.
- Customized dashboards to see the health of your maintenance operations.
- CMMS is a centralized system that is accessible from anywhere.
The bottom line is that by using a maintenance management system software like CMMS you can keep ahead of these issues. You can manage and automate all of your maintenance tasks from a computer, Smartphone, or mobile device, with our user-friendly and cost-effective CMMS software.
Please feel free to get in touch with one of our account executives if you have any questions or would like to have a live demo.