If you’re a maintenance manager, you know that one unscheduled hour can drain thousands in labor and lost output. Worse, repeated surprises erode trust between production and maintenance, fueling a blame game that distracts everyone from hitting OEE targets.
Thankfully, autonomous maintenance turns frontline operators into guardians of uptime, and the difference shows fast. This guide promises a proven path out of the chaos: practical steps to embed operator-driven inspections, clear training checkpoints, and digital checklists—so small issues surface early, costs fall, and your team finally wins back control of the plant’s reliability scorecard.
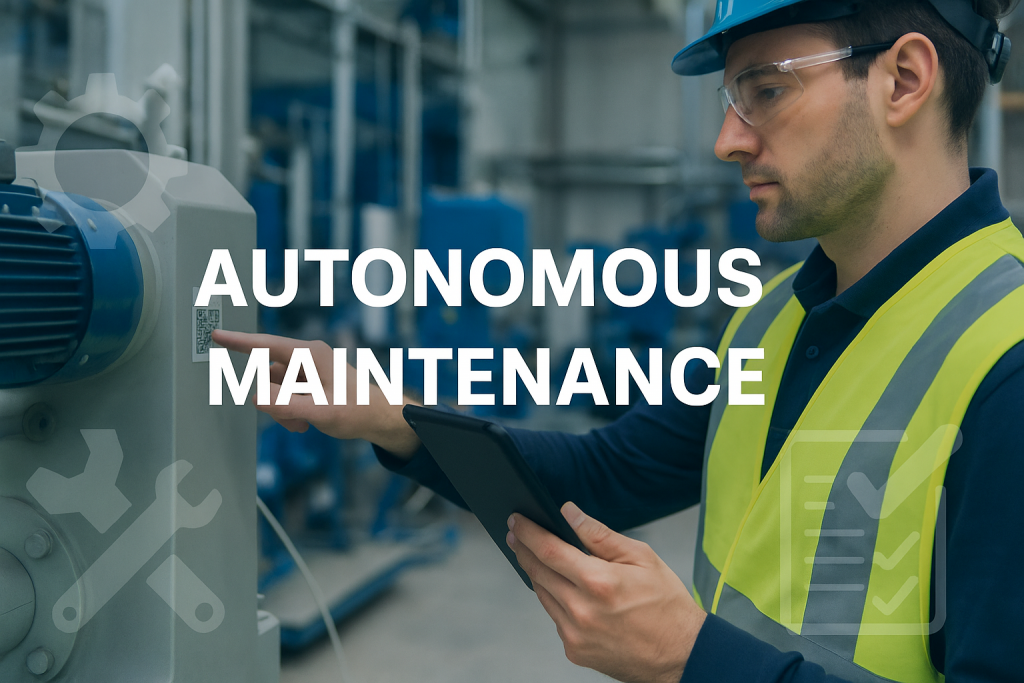
What is Autonomous Maintenance?
Autonomous maintenance is the first step in the process of Total Productive Maintenance (TPM) system, which is a comprehensive approach to equipment maintenance and improvement. The idea behind autonomous maintenance is that operators, who are closest to the equipment and its operation, have a deep understanding of how it operates and can take preventive action to keep it running smoothly. These employees are responsible for handling the basic equipment maintenance tasks, such as cleaning, lubrication, and inspections.
Two core principles that guide autonomous maintenance:
- Proper Operation of Assets: Operating equipment correctly and as directed reduces deterioration and unexpected downtime.
- Efficient Asset Management: This principle ensures that equipment is restored to a “like new” standard and properly managed throughout its lifespan to optimize its performance, reduce maintenance costs, and maximize its value.
Total Productive Maintenance (TPM) Strategy
TPM is a comprehensive approach to equipment maintenance that attempts to maximize equipment effectiveness while minimizing downtime. Autonomous Maintenance (AM), one of the TPM pillars, is a process in which operators take responsibility for the routine maintenance of their equipment.
Total Productive Maintenance
Autonomous maintenance (AM) is a key component of TPM because it allows operators to discover and resolve equipment issues before they become major problems that require significant downtime to repair. Companies that use AM can reduce the frequency and severity of equipment breakdowns, resulting in higher production efficiency, lower maintenance costs, and improved overall equipment performance.
In the context of TPM, AM fits into the overall framework by being one of the eight pillars of the TPM approach. The pillars include autonomous maintenance, focused improvement, planned maintenance, quality maintenance, early equipment management, training and education, safety, health, and environment.
The TPM pillars are focused on improving the overall effectiveness of the maintenance function by addressing issues such as equipment design, maintenance planning and scheduling, and training and development for maintenance personnel. Our in-depth Autonomous Maintenance Complete Guide explores each step in detail and explains how a CMMS accelerates rollout.
Companies can ensure that operators have the skills and knowledge needed to take ownership of routine maintenance of their equipment by including AM in the TPM approach, while also providing guidance and assistance to help them succeed in this role. Eventually, the purpose of AM is to foster a culture of continuous improvement in which operators actively participate in the maintenance and development of equipment rather than merely responding to problems as they arise.
Why It Matters: From OEE to Lower MTTR
When production lines run flat-out, minutes of unplanned downtime feel like hours of lost revenue—and the “fire-fighting” mentality only gets worse as assets age. Autonomous maintenance changes that equation by baking daily care and early-warning inspections into the rhythm of every shift, letting you attack failures before they hit the schedule or the P&L.
Impact at a glance
- +10 – 15 % OEE uplift reported by plants that embed operator-driven cleaning, inspection, and lubrication within the first 12 months.
- 20 – 40 % reduction in unplanned downtime thanks to faster detection of wear, leaks, and misalignments.
- ≈25 % lower MTTR as minor repairs can be handled on the spot—and bigger jobs arrive in the shop with photos, parts lists, and timestamps attached.
- 2–4 × ROI typical when labor, scrap, and spare-parts savings are rolled up across a multi-line facility.
Curious what those numbers look like for your site? Run the scenarios in minutes with the interactive ROI calculator from eWorkOrders and see how quick operator ownership can pay for itself.
Autonomous Maintenance Skills
Autonomous Maintenance requires operators to master skills like detecting abnormalities by understanding the machine’s components, making improvements, identifying possible quality issues, and determining their causes. Some of these skills required are:
- Increasing operator knowledge of their equipment.
- Keeping equipment in a “like new” state, ensuring they are clean and lubricated.
- The ability to notice emerging issues before they become failures.
In the past, the implementation of AM required a significant investment in training and resources, but nowadays, the process has been streamlined with the help of computerized maintenance management systems (CMMS). CMMS integrates the necessary instructions, tools, and customized checklists into work orders maintenance plans, ensuring that maintenance is performed each time according to the same process.
5S & CIL: The Foundation
Before operators can own reliability, the workplace itself must stay stable and predictable. That’s where 5S and the Clean-Inspect-Lubricate (CIL) loop intersect:
5S Step (Japanese) | Purpose | CIL Connection |
---|---|---|
Seiri (Sort) | Remove unused tools, parts, and debris. | Surfaces are clear, so cleaning reveals hidden wear points. |
Seiton (Set in order) | Assign “a place for everything” with labels and shadow boards. | Lubricants and inspection gauges stay within arm’s reach, reducing skip-rates. |
Seiso (Shine) | Deep-clean machines and surrounding areas. | “Shine” is the Clean in CIL—critical for spotting leaks and cracks early. |
Seiketsu (Standardize) | Create visual standards (colors, marks, checklists). | Standard work cards tell operators exactly Inspect and Lubricate intervals. |
Shitsuke (Sustain) | Cultivate discipline through audits and coaching. | Daily CIL checks become a habit, locking in uptime gains. |
Actionable 5S-CIL Checklist for Operators
- Clean—Daily (5 min):
- Wipe oil and dust from guards, belts, and panels.
- Sweep floor area; dispose of debris in marked bins.
- Inspect—Every Shift (3 min):
- Look for frayed hoses, loose bolts, unusual odors.
- Log any abnormal noise or vibration in eWorkOrders.
- Lubricate—Per SOP (2 min):
- Top up grease points to fill lines—not overflow.
- Confirm lube type matches the tag color code.
- 5S Audit—Weekly (15 min):
- Score each “S” on a 1–5 scale; photo‐document gaps.
- Assign follow-up tasks directly in the CMMS to close loops.
By weaving 5S discipline into the CIL cycle, autonomous maintenance turns “housekeeping” into a frontline reliability engine, revealing defects sooner, extending component life, and freeing skilled technicians for higher-value projects.
Autonomous Maintenance vs. Preventive & Predictive Maintenance
While autonomous maintenance (AM), preventive maintenance (PM), and predictive maintenance (PdM) all pursue the same goal—maximum equipment uptime—they differ in who does the work, when it happens, and how decisions are made. Think of them as three layers of a reliability “defense-in-depth” strategy:
Approach | Primary Owner | Typical Tasks | Trigger Basis | Ideal Use Case |
---|---|---|---|---|
Autonomous Maintenance (AM) | Line operators | Clean-Inspect-Lubricate (CIL), tighten fasteners, adjust belts, basic visual checks | Daily shift routines or at start-up | Catching early-stage faults and promoting equipment ownership culture |
Preventive Maintenance (PM) | Maintenance technicians | Component replacements, detailed inspections, calibrations, safety checks | Fixed time or usage intervals (hours, cycles) | Mitigating age-related wear and compliance-driven tasks |
Predictive Maintenance (PdM) | Reliability / engineering team | Vibration analysis, thermal imaging, oil analysis, sensor-driven diagnostics | Condition thresholds from IoT data | Detecting failure modes invisible to human senses and optimising part life |
How They Complement One Another
- AM feeds PM & PdM with real-time observations. Operators log anomalies in the CMMS, giving planners better data to schedule targeted PM or deeper PdM diagnostics.
- PM creates the structured baseline. Regular service intervals ensure fundamental wear parts are replaced before failure—reducing the load on PdM and avoiding surprise downtime.
- PdM fine-tunes both layers. When sensor trends show a bearing can safely run 20 % longer, PM intervals are adjusted—and AM checklists expand to watch that bearing more closely.
By layering these approaches, plants build a resilient maintenance ecosystem where frontline ownership, scheduled upkeep, and data-driven insights work in concert—delivering the lowest total cost of reliability.
How To Implement Autonomous Maintenance
Although there is a standardized set of seven stages for implementing autonomous maintenance, the process may differ throughout various organizations.
Implementing autonomous maintenance can be achieved through the following seven steps:
Step 1: Increase Operator Knowledge
Machine operators often receive training on how to operate machinery at optimal capacity, but for a successful autonomous maintenance program, they require a more comprehensive understanding of the machines. This involves technical knowledge of the assets, their components, common issues, and troubleshooting procedures. Equipment-related skills that machine operators should possess include problem detection and troubleshooting, asset repairs and restoration, and optimal asset operating conditions settings. Implementing an effective training schedule and periodic retraining can help to develop and upgrade the machine operators’ skills.
Step 2: Establishing Baseline Standards for Asset Maintenance
To prepare the assets for autonomous maintenance, the initial step involves cleaning and inspecting the machines to achieve an “almost new” condition, and this task should involve the production, machine engineering, and maintenance teams. Thorough cleaning and overhauling of the assets and the surrounding area should be carried out while keeping an eye out for common signs of deterioration such as loose bolts, leaks, cracks, contaminated fluids, dirt and dust accumulation, and limited asset functionality. Additionally, it is important to create easy-to-follow Standard Operating Procedures (SOPs) for inspections and other basic maintenance tasks.
Step 3: Root Cause Analysis for Contamination Control
Once the initial inspections and cleaning are complete, it is crucial to address any identified problems and eliminate their root causes to prevent further deterioration of the assets. Improving access to the assets for baseline maintenance activities is also recommended. To prevent recontamination of the equipment, established cleaning and maintenance standards should be followed by everyone, quality machine covers and seals should be installed, continuous inspections should be carried out to ensure cleanliness, and orderliness should be established within the facility. Safety measures must also be taken into consideration, as there is a responsibility under OSHA regulations to provide a safe working environment for employees.
Step 4: Establish Lubrication and Inspection Protocol
After setting up baseline standards for machine maintenance in step 2, these standards will serve as a foundation for creating inspection and lubrication standards for the assets. The standards should clearly outline which assets and components need cleaning and lubrication, how the process should be carried out, and whose responsibility it is. It is recommended to develop these standards, particularly for critical assets, with the guidance of experienced maintenance engineers. The standards should be regularly reviewed and updated for maximum efficiency. Operators can create their own standards for non-critical assets, but all standards should be documented, maintained, and accessible to primary users.
Step 5: Maintain Consistent Asset Inspection and Monitoring
This stage entails inspecting and monitoring equipment on a regular basis to ensure it is operating at peak performance. This is accomplished by developing a checklist of inspection tasks and frequently checking equipment performance data. Operators can be taught to undertake these inspections and report any abnormalities to the maintenance staff. Equipment downtime and maintenance expenses can be avoided by proactively detecting and addressing possible issues. Furthermore, frequent monitoring and inspection can help discover areas for improvement and allow for continual process optimization. Overall, this process helps to guarantee that equipment is running efficiently, reducing the chance of breakdowns and increasing equipment lifespan
Step 6: Standardize Visual Maintenance
At this stage, the objective is to enhance asset visibility. This means ensuring that machine operators can easily comprehend how the equipment works. To achieve this, opaque machine covers should be replaced with transparent ones. Valves and levers should be clearly labeled to indicate the direction of opening and closing. Moreover, normal and safe operating values should be marked next to gauges, and sight glasses should be installed so that operators can detect when machines reach hazardous operating levels.
Step 7: Achieving Continuous Improvement
Autonomous maintenance is an ongoing process that requires continuous attention throughout an asset’s lifecycle to ensure that it remains effective in identifying and preventing equipment breakdowns This can be achieved by gathering and analyzing data, seeking feedback from machine operators and maintenance technicians, and implementing changes to the program as necessary. The focus should be on continually refining the maintenance processes and protocols to improve equipment reliability, increase productivity, and reduce costs. By prioritizing continuous improvement, you can create a maintenance program that is sustainable and provides long-term benefits for your business.
Autonomous maintenance is a continuous process that extends throughout the entire lifecycle of your assets. It’s crucial to collect and evaluate maintenance data to identify areas for improvement in your maintenance program. By implementing a computerized maintenance management system (CMMS) like eWorkOrders and seeking feedback from machine operators, team leaders, and maintenance technicians, you can establish a sustainable autonomous maintenance program that will serve you well over the long term.
Autonomous Maintenance Training Program (90-Day Roadmap)
Launching autonomous maintenance training without a structured timeline often leads to half-adopted checklists and forgotten SOPs. The roadmap below breaks the first three months into clear sprints so operators, supervisors, and technicians know exactly what “good” looks like— and when.
Day Range | Core Objective | Key Activities | Deliverables | Primary Owner |
---|---|---|---|---|
0 – 30 Foundation | Build awareness and baseline skills | • Kick-off workshop on TPM pillars • 5S “red-tag” event to clear work areas • Classroom demo of Clean-Inspect-Lubricate (CIL) loop | • Signed operator commitment cards • 5S score ≥ 3/5 in audit | Maintenance Manager + CI Lead |
31 – 60 Skill Development | Embed daily CIL habits | • Pair operators with tech mentors for hands-on CIL • Create mobile checklists in eWorkOrders CMMS • Daily huddles to review “finds” and log work orders | • 100 % operators trained on eWorkOrders mobile app • First batch of CIL SOPs approved | Line Supervisors |
61 – 90 Certification & CI | Lock in standards and measure impact | • Practical skill check: lube points, torque checks, tagging • Mini-Kaizen to remove two recurrent contamination sources • KPI dashboard review (MTTR, downtimes) | • Operator AM certificates issued • 10 % reduction in minor stoppages vs. baseline | Reliability Engineer |
Tips for Sustaining Momentum
- Micro-learning: Push 3-minute video refreshers every Monday via your CMMS portal.
- Visual wins: Post a downtime “thermometer” in the break room so teams see progress.
- Gamify audits: Award a rotating “Golden Grease Gun” trophy to the line with the highest 5S + CIL compliance score each month.
The Importance Of Autonomous Maintenance
Autonomous maintenance is important for businesses looking to maximize their equipment’s performance while minimizing downtime and repair costs. By empowering operators to take ownership of routine maintenance tasks, autonomous maintenance can increase machine reliability and reduce the need for costly repairs. It also helps to extend the lifespan of equipment and reduce the likelihood of unplanned breakdowns that can disrupt production. Moreover, by shifting the responsibility of maintenance to the operators, maintenance teams can focus on more complex tasks, such as troubleshooting and repairing more critical components. Overall, autonomous maintenance is a key element in creating a sustainable and efficient maintenance program for businesses across various industries.
Benefits Of Autonomous Maintenance
Below are some benefits of autonomous maintenance:
Reduced Labor Costs: Transferring simple maintenance tasks to operators eliminates the need to allocate time for those duties to maintenance technicians, freeing up time for more critical repairs. This can lead to cost savings by avoiding the need to hire additional personnel. It is important to note that this approach does not place an additional burden on employees, as autonomous maintenance is integrated into their existing job responsibilities.
Increased Productivity: Autonomous maintenance can help reduce equipment downtime, allowing for improved uptime and higher productivity.
Increased Uptime: By ensuring that equipment is consistently inspected and maintained, autonomous maintenance helps reduce the occurrence of breakdowns, which can result in increased uptime and reduced downtime.
Improved Equipment Maintenance: While cleaning and lubrication may seem like minor tasks, they can greatly extend the lifespan of equipment and reduce the likelihood of major repairs. With autonomous maintenance, operators can take care of these tasks and report any issues to technicians before they escalate into larger problems.
Early Problem Detection: Operators are in close contact with their machines and can quickly detect and address issues before they worsen. With the right training, they can take corrective action on the spot, reducing equipment downtime and the need for more extensive repairs.
Enhanced Teamwork and Participation: Autonomous maintenance gives operators a sense of ownership over their equipment and encourages collaboration between maintenance and production teams. By involving operators in the maintenance process, they are more invested in the success of the equipment and the production process, leading to a more engaged and motivated workforce.
Improved Safety: Autonomous maintenance can help reduce workplace hazards by preventing equipment deterioration and related safety risks. Operators become more aware of potential safety hazards and can take steps to prevent accidents from occurring, resulting in a safer work environment.
More Time for Critical Tasks: By reducing the workload of maintenance technicians, autonomous maintenance allows them to focus on more complex tasks that require specialized knowledge and training. This can lead to more efficient and effective maintenance programs overall.
Empowered employees: Operators are given more responsibility and autonomy, which increases their investment in the equipment and the production process, leading to a more motivated and engaged workforce.
Tips for sustaining autonomous maintenance
Below are some tips for sustaining autonomous maintenance as you scale:
Define roles and responsibilities: Clearly define the individuals or teams responsible for carrying out AM tasks, and make sure that all employees are aware of their roles and responsibilities in the process.
Develop and implement a comprehensive training program: As you scale your autonomous maintenance program, it’s important to have a well-designed training program in place to ensure that all employees are adequately trained in maintenance procedures and safety practices.
Develop a clear and concise communication plan: Effective communication is key to the success of any program, and autonomous maintenance is no exception. Develop a communication plan that outlines roles and responsibilities, establishes clear lines of communication, and ensures that all stakeholders are aware of program progress and changes.
Establish a system for reporting and addressing equipment issues: Invest in a system for logging and tracking machine failures and abnormalities, and establish a process for identifying and addressing the root causes of failures. A CMMS can help in creating and implementing such a system. By analyzing the data, the maintenance team can prioritize maintenance tasks, improve maintenance planning, and identify process improvement areas.
Monitor and measure outcomes: Regularly measuring the results of your AM program helps to identify areas for improvement and ensures that the program is meeting its objectives.
Encourage continuous improvement: To sustain your AM program, you need to encourage a culture of continuous improvement. Encourage operators to share their ideas for improving maintenance processes and reward those who come up with innovative solutions.
Continuously measure and evaluate program effectiveness: It’s important to track the progress and effectiveness of your autonomous maintenance program through data analysis and performance metrics. This allows you to identify areas for improvement and adjust your program accordingly.
Leverage technology and automation: Utilizing technology such as sensors, predictive maintenance software, and automated inspection tools can help streamline maintenance procedures and identify potential issues before they become larger problems.
Foster a culture of continuous improvement: Encourage your employees to actively seek out and suggest improvements to the autonomous maintenance program. This can be achieved through regular feedback and recognition of employee efforts.
The Role of CMMS in Autonomous Maintenance
A computerized maintenance management system (CMMS) plays an important role in autonomous maintenance. It provides a centralized platform for managing maintenance operations, allowing operators to log and track equipment performance data, report issues, and schedule and prioritize maintenance tasks. With a CMMS, operators can receive automated alerts and reminders for preventive maintenance activities, ensuring that maintenance is performed on schedule and before equipment failure occurs. Additionally, a CMMS can help identify trends in equipment performance and track the effectiveness of maintenance efforts, allowing for continuous improvement and optimization of the maintenance program. Overall, a CMMS is a valuable tool in supporting the implementation and sustainability of autonomous maintenance practices.
Here are some features of CMMS software that help:
Work Order Management: A CMMS can help operators create and manage work orders, assign tasks, and track the progress of maintenance activities.
Asset Management: CMMS allows maintenance personnel to track equipment assets and generate reports on equipment performance, downtime, and maintenance costs.
Preventive Maintenance: CMMS can assist in scheduling and tracking preventive maintenance tasks, such as routine inspections, cleaning, and lubrication.
Root Cause Analysis: Root Cause Analysis is the process of analyzing equipment failure to determine the underlying reason and prevent future occurrences. A CMMS can help in root cause analysis by providing a centralized system for documenting and tracking equipment failures, maintenance tasks, and associated data. This data can be utilized to discover patterns and trends, helping maintenance teams in determining the root cause of the problem and taking corrective actions to prevent similar issues from occurring in the future.
Training: Track training and certification for operators. This ensures that operators are adequately trained and qualified to perform maintenance tasks.
Inventory management: Track and manage inventory levels of spare parts and consumables needed for maintenance activities. This helps ensure that the necessary parts are available when needed and also helps reduce excess inventory and costs.
Communication and Collaboration: A CMMS provides a platform for communication and collaboration between maintenance and production teams, allowing them to share information and work together more effectively.
Digital Tools & CMMS Support
Modern autonomous maintenance lives or dies by how easy it is for operators to log findings and for supervisors to see trends. That’s where the eWorkOrders CMMS platform becomes the backbone of your program:
- Mobile work orders: Operators scan a QR code, open a pre-filled CIL checklist, and tap “complete” without leaving the line.
- Instant photo capture & markup: Snap a picture of a leaking seal, circle the problem area, and auto-attach it to the work order—no extra apps or USB cables.
- Real-time KPI dashboards: MTTR, first-time fix rate, and CIL compliance scores update as soon as a ticket closes, giving managers a live pulse on reliability and OEE.
- Smart notifications: Escalate overdue tasks, parts shortages, or repeated fault codes before they snowball into downtime.
Watch our short “What Is a CMMS?” overview video to see an operator scan, complete a checklist, and push data straight to the dashboard.
Metrics & ROI Calculator
Before you invest time and budget in an autonomous-maintenance rollout, quantify the upside with three core reliability metrics:
Calculate Your Payback in Minutes
Want to see how these improvements translate into dollars? Plug your downtime costs, crew rates, and target MTBF/MTTR gains into the interactive CMMS ROI Calculator. The tool estimates:
- Annual downtime savings
- Labor-hour reductions
- Parts-inventory carry cost cuts
- Total ROI and payback period
Run multiple “what-if” scenarios, download the PDF report, and walk into your next budget meeting with numbers everyone can trust.
Final Thoughts
In conclusion, autonomous maintenance is a critical component of a successful maintenance program, providing numerous benefits such as improved safety, increased productivity, and better quality control. By empowering operators to take a more active role in equipment maintenance, companies can reduce labor costs, ensure equipment is well taken care of, and detect issues early on. With the help of a CMMS, operators and maintenance teams can work together to implement a sustainable autonomous maintenance program that leads to long-term success and cost savings.
FAQ
What are the 7 steps of autonomous maintenance?
The classic 7-step roadmap is (1) initial deep-clean and baseline inspection, (2) eliminate contamination sources, (3) set cleaning-lubrication standards, (4) train operators on general inspection, (5) conduct autonomous inspections with checklists, (6) introduce visual controls/5S audits, and (7) drive continuous improvement through KPI review and kaizen events. Following these steps in order builds operator skill, locks in daily care routines, and creates a culture of proactive reliability.
What is the difference between autonomous and preventive maintenance?
Autonomous maintenance is carried out by line operators every shift—simple clean-inspect-lubricate tasks that spot problems early—whereas preventive maintenance is scheduled work handled by technicians (e.g., component change-outs or calibrations) based on time or usage intervals. The two approaches are complementary: good operator care reduces emergency calls and lets preventive work happen on schedule.
What is automated maintenance?
“Automated maintenance” usually means using digital tools, sensors, or robotics to trigger, plan, or even perform maintenance tasks without manual intervention—for example, IoT vibration sensors that auto-generate a work order in your CMMS. It focuses on automating the workflow itself, not on transferring ownership of routine tasks to operators.
What is the difference between autonomous maintenance and TPM?
Total Productive Maintenance (TPM) is a comprehensive reliability framework with eight pillars covering everything from safety to early equipment design. Autonomous maintenance is just one of those pillars—specifically the one that empowers operators to handle routine upkeep—so implementing AM means you’re practicing TPM, but TPM includes much more than AM alone.