If you run or manage a business, you know that even the smallest maintenance inconvenience can affect your entire operation. That broken machine, a missed service request, or a delay in any part delivery does more than just disrupt workflow. It causes other issues like costly downtime, missed deadlines, and frustrated employees.
If you’re still relying on traditional techniques to manage repairs, it might be time for a change. Having efficient maintenance work order management software changes that by reducing downtime and keeping operations running smoothly.
In this post, we’ll explore maintenance work order software, how it speeds up repairs, and what features make the biggest impact. We’ll also look at the best options you can choose from.
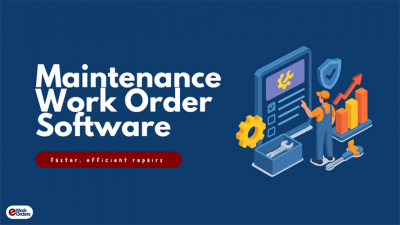
What is Maintenance Work Order Software?
Maintenance work order software is a valuable tool that helps businesses manage, track, and complete maintenance tasks in a structured and effective way. Think of it as a central hub for all repair and service requests.
For example, if you have a leaky pipe or a machine that needs servicing, work order software for maintenance makes sure that these tasks are recorded, assigned to a qualified person to fix them, and tracked from start to finish.
Here’s precisely what work order software can do:
- Submits and Assigns Repair Requests in Real Time: Anyone on the team can report issues, and managers can take them up and assign them to the right technicians.
- Tracks Job Progress: You can see who’s working on what task, monitor progress, and determine when it will be completed.
- Improves Accountability: With digital logs, everyone is on the same page and responsible for their tasks.
You might also see the term CMMS software used alongside or in place of maintenance work order software. While they’re almost identical, CMMS stands for computerized
maintenance management software. It’s the broader software that manages all aspects of maintenance operations.
5 Ways Work Order Software Speeds Up Repairs
Here are the five major benefits of having work order software for maintenance in place, and how each one helps speed up repairs and reduce expensive delays.
1. Automates Manual Processes
There’s no more digging through paperwork or backlogged spreadsheets and emails. This software automates task creation, auto-assigns tasks, monitors work progress, logs updates, and generates reports. Everything in the system is handled digitally, eliminating inefficiencies that often come with traditional processes.
2. Enables Real-Time Technician Communication
All communication channels, including calls, emails, and conversations, are within the system, so technicians and
managers can communicate directly within the platform. This connection allows for instant alerts for new tasks, updates on progress ("waiting for parts" or "complete" updates), or any changes in real-time. It eliminates confusion, speeds up coordination, and helps finish the job quickly.
3. Prioritizes Urgent Request Automatically
Since technicians receive instant notifications and alerts, important tasks like safety hazards or critical equipment failures are flagged so they can address them urgently. This prevents small issues from turning into bigger problems and reduces downtime as well.
4. Tracks Repair History for Faster Diagnoses
Every repair is logged into the system and tied to a specific asset. The team can access past work logs, previous parts replacements, and maintenance notes in just one click. For example, let’s say a conveyor belt fails again. In this case, technicians can tell if it’s a recurring issue or a new problem. This quick access to data often speeds up troubleshooting and leads to faster and more accurate repairs.
5. Reduces Inventory Delays with Stock Alerts
One of the main causes of repair delays is not having the right parts in stock when needed. Facility maintenance work order software has built-in inventory tracking that helps you avoid stock issues. It monitors parts inflows and outflows, generates low-stock alerts, and reorders.
Best Work Order Tools for Lightning-Fast Repairs
There are various work order software solutions, but we’re going to discuss a few that stand out when it comes to
speeding up repairs. Here are some of the best options to help you make the best investment decision for your business:
1. eWorkOrders
eWorkOrders is our cloud-based CMMS solution that offers fast and reliable maintenance across various industries,
such as manufacturing, healthcare, and property management. It helps your business stay on top of maintenance tasks and asset management with advanced features like predictive and preventative maintenance, reporting, and more.
Here’s what makes eWorkOrders stand out:
- Work Order Management: Manage your entire work order process from start to finish.
- Preventive Maintenance: Schedule and track routine maintenance in advance to reduce the likelihood of equipment breakdown.
- Mobile Access: Your team can view and update work orders on the go.
- Custom Dashboards: See information that matters the most at a glance.
- Asset Management: Track your assets’ locations, maintenance history, and performance metrics.
- Inventory Control: Know what parts you have in stock and what’s running out, and reorder automatically.
Some of the biggest companies, such as McDonald’s, KFC, Honda, and Siemens, have used eWorkOrders’ services.
While we’ve worked on numerous projects, here’s one instance where we helped an
faster way to manage maintenance:
- We listened closely to their challenges, namely complex maintenance operations, poor communication, and clunky tools.
- We showed them how our user-friendly CMMS could centralize everything: work orders, assets, inventory, and preventive maintenance.
- We made implementation effortless, which means fast setup, easy onboarding, and no learning curve.
- Our support team stayed hands-on, ready to jump on calls and adapt to custom needs.
With real-time data, they reduced downtime, improved technician response, and boosted productivity. The overall result was a smoother, faster, more efficient maintenance process.
If you need software that’s flexible, scalable, affordable, and built to grow with your business, your search might have just ended here. Book a demo today.
2. MaintainX
MaintainX is a mobile-friendly platform that helps businesses manage work orders, track maintenance, and stay
connected. It’s popular in companies that prioritize real-time communication and digital checklists over paperwork.
Key Features |
|
Pros |
|
Cons |
|
3. UpKeep
UpKeep is designed to help businesses organize work orders, track maintenance costs, and simplify maintenance
scheduling.
Key Features |
|
Pros |
|
Cons |
|
4. Fiix
Built to help teams stay organized and improve maintenance workflows, Fiix is a cloud-based CMMS that’s especially
useful for manufacturing, energy, and facility management.
Key Features |
|
Pros |
|
Cons |
|
5. Limble CMMS
Limble is a CMMS and asset management platform designed to help teams get set up quickly and manage their work
orders. It’s a great option for businesses that want a tool that’s simple yet powerful.
Key Features |
|
Pros |
|
Cons |
|
How to Pick Software That Cuts Your Repair Time in Half
There are many maintenance work order software options out there, so here are a few things you must keep in mind
before making a selection:
- Real-time Alert Customization: Choose software that allows you to customize alerts, notifications, and reminders. This makes sure the right people receive them at the right time.
- Scalability: Your repair needs will likely grow over time. Pick a tool that can grow with you.
- Mobile Access: Repairs happen on the go, not behind a desk. Choose software with a strong mobile app so your team can access tasks, log updates, and check parts inventory from the field.
- Custom dashboards: You want to spot issues fast. A dashboard that displays real-time data on issues, such as overdue tasks or parts availability, can help you make better decisions and act on them quickly.
- Offline Access: Pick software that technicians can access even in areas with poor connectivity.
- Integration: Make sure the software works smoothly with your existing tools, such as QuickBooks or Salesforce.
Closing Thoughts
Maintenance work order software solutions should save you time and money. The right one, like eWorkOrders, can help you avoid breakdowns, reduce downtime, and boost overall productivity. It’s about making maintenance tasks less stressful.
FAQs
What is the Best Work Order Management Software?
The best work order management software
really depends on whether it meets your specific needs, such as the range of features, industry, and other factors. That said, eWorkOrders is a top choice for its ease of use, advanced features, flexibility, and scalability.
Which Software is Used For Maintenance Tasks?
Maintenance teams use work order software to help plan, track, and complete maintenance tasks efficiently.
What is a Maintenance Work Order System?
A maintenance work order system is a tool
that helps businesses organize and control all aspects of maintenance tasks, from submitting requests to assigning and Tracking tasks in real-time.
What is the Best Maintenance Software?
The best depends on your needs, but eWorkOrders excels in its simplicity, range of features, and ability to help teams speed up repairs while still staying organized.