In every industry, the shared objective in maintenance is to uphold the condition and efficiency of facility equipment, tools, and infrastructure, minimizing unplanned downtime and equipment failure. The dual processes of repair and maintenance play pivotal roles in achieving this goal.
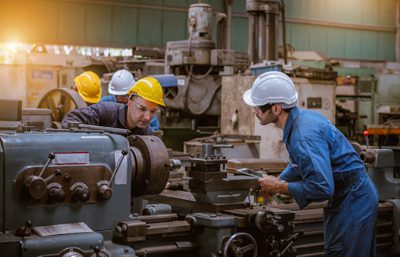
What is the Difference Between Repair and Maintenance?
While often used interchangeably, repair and maintenance have distinct meanings in asset management.
Repair
- Restoration work is undertaken when an asset breaks, is damaged or ceases to function.
- Reactive in nature, triggered by unexpected failures or malfunctions.
- Addresses issues that have already occurred, aiming to restore full functionality.
- Examples of Repair: Broken Conveyor Belt Repair; Faulty Pump Replacement; and Machine Downtime Resolution.
Maintenance
- Proactive and preventive measures aimed at preserving the condition and longevity of assets.
- Involves routine activities, inspections, and corrective actions to prevent damage.
- Can be categorized into various strategies such as preventive, predictive, and reliability-centered maintenance.
- Scheduled and planned to avoid unexpected breakdowns and prolong asset life expectancy.
- Examples of Maintenance: Preventive Maintenance – HVAC System; Predictive Maintenance – Vibration Analysis; Reliability-Centered Maintenance (RCM) – Aircraft Engine; Routine Inspection – Manufacturing Equipment.
Levels of Repair
The level of repair required depends on the degree of failure causing the asset’s malfunction. Two basic types of equipment failure exist:
Partial Failure
The asset still functions but at a reduced capacity, with potential safety hazards. Corrective actions can restore the asset to full functionality before complete failure occurs.
Complete Failure
The asset has malfunctioned entirely and cannot be used until repaired. The resources needed for repairs depend on the root cause of the failure.
Types of Maintenance
Maintenance encompasses various activities, including visual inspections, functional checks, spare parts replacements, and new asset installations. Several maintenance strategies can be tailored to specific needs:
Reactive Maintenance
Also known as breakdown or run-to-failure, this method involves fixing assets as they break. While suitable for non-essential or low-cost equipment, its drawbacks include potential production delays and increased costs.
Preventive Maintenance
This proactive approach involves scheduled inspections or repairs at predetermined intervals, aiming to extend an asset’s life and prevent breakdowns. CMMS software is often used for automated scheduling.
Predictive Maintenance
This strategy aims to predict failures before they occur, utilizing data from sensors to alert the maintenance team when an asset is at risk. CMMS helps track meter readings for effective implementation.
Reliability-Centered Maintenance (RCM)
Addressing the non-linear nature of failure, RCM involves analyzing potential failure modes for each piece of equipment, and creating customized maintenance plans to enhance equipment reliability.
FAQs About Repair and Maintenance:
What is an example of maintenance and repair?
Repairs are restoration work for when something gets broken, damaged, or stops working.
Examples of Repair: Broken Conveyor Belt Repair; Faulty Pump Replacement; and Machine Downtime Resolution.
Maintenance is routine activities meant to prevent damage and prolong the life of appliances, fixtures, and the property itself.
Examples of Maintenance: Preventive Maintenance – HVAC System; Predictive Maintenance – Vibration Analysis; Reliability-Centered Maintenance (RCM) – Aircraft Engine; Routine Inspection – Manufacturing Equipment.
What is the primary goal of maintenance in industries?
The primary goal is to uphold the condition and efficiency of facility equipment, minimizing unplanned downtime and equipment failure.
What distinguishes repair from maintenance?
Repair involves restoring functionality after a breakdown, while maintenance is proactive, preventing issues through routine activities and inspections.
What is the difference between breakdown maintenance and repair?
Breakdown maintenance is performed by running equipment until it malfunctions, at which point repairs and maintenance is carried out.
What are some preventive maintenance strategies?
Preventive strategies include scheduled inspections (Preventive Maintenance), predicting failures before they occur (Predictive Maintenance), and custom plans for each machine (Reliability-Centered Maintenance).
What is the significance of levels of repair in asset management?
Levels of repair depend on the degree of failure. Partial failure involves reduced capacity, while complete failure requires addressing the root cause before the asset can be used again.
How can CMMS software enhance maintenance practices?
CMMS software automates scheduling, tracks meter readings for predictive maintenance, and provides insights for decision-making, streamlining maintenance operations.