Conveyor belts are critical assets in manufacturing and material handling operations. Proper maintenance is crucial to prevent costly breakdowns, minimize downtime, and ensure smooth production. This comprehensive guide provides an essential conveyor belt maintenance checklist to keep your systems running efficiently.
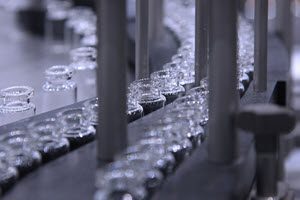
The Importance of Conveyor Maintenance
Implementing routine preventive maintenance for conveyor systems provides numerous advantages, including:
Avoiding Unforeseen Breakdowns
Regular upkeep minimizes the chances of unexpected failures, ensuring continuous production flow.
Lowering Repair Expenses
Consistent maintenance helps avoid costly repairs and contributes to a longer lifespan for your equipment.
Enhancing Employee Safety
Regular maintenance of conveyor systems significantly lowers the likelihood of accidents, fostering a safer workplace for all staff members.
Optimizing Performance
Keeping conveyors in top condition ensures efficient material handling and flow, boosting overall productivity.
Detecting Issues Early
Regular inspections allow for the identification of potential problems before they escalate into significant complications.
Common Conveyor Belt Maintenance Checklist
Note:These are general preventive maintenance guidelines. Below are only a few very broad items to be aware of when performing or scheduling conveyor maintenance. Every standard conveyor ships with a detailed maintenance manual specific to that conveyor’s parts, safety, and maintenance tips to ensure continued quality. Your specific facility will determine what unique checklists are needed based on your asset\equipment inventory.
Suggested Conveyor Maintenance Checklist
Routine Conveyor Maintenance
- Do a routine cleaning at the start and end of the day to ensure that there are no components that will interfere with the function of the conveyor belt.
- Physically inspect conveyor drive components and any debris that may be stuck in the conveyor mechanism.
- Inspect the entire surface of the conveyor belt for any wear that may cause issues.
- Check for damaged or broken parts
- Check rollers for any structural damage, debris buildup, motor, etc.
- Check for misalignment of conveyor belts.
- Check the conveyor belt and joints to make sure that there is no unusual peeling or damage.
- Check machine guard placement (for belts, pulleys, sprockets, and other pinch points).
- Check emergency stops to make sure that it is functioning properly.
Belt Maintenance
- Check the conveyor belt for cuts, cracks, or damages.
- Take note of any belt slippage or material spillage.
- Check for any conveyor belt abrasions.
- Check the upper and lower cover rubber for damage and excessive wear.
- Check the belt chain for any extra slack, fraying, buildup, or damage.
- Check for carryback. Carryback is the material that sticks to or embeds into a conveyor belt or chain rather than discharging at the head. The conveyor “carries back” the material until it falls off under the conveyor (tailings) or is otherwise removed. There are two ways to reduce this issue. First, belt cleaners can reduce and sometimes even completely eliminate carryback. Second, belt scrapers (which are installed in primary and secondary locations) remove residue and debris from the belt, and will drastically reduce your carryback.
- Monitor the tension to ensure the V-belts and O-rings for wear and tear and are not worn, not too tight or too loose.
Motor
- Listen and monitor for any unusual noise during normal conveyor operation.
- Check gearbox noise for excessive heat from either the motor or the gearbox.
- Monthly document and keep track of the motor temperature. This will help you to identify any potential issues.
- Check to see if the bearings are operating properly. A worn bearing can result in major repair costs.
- Regular inspection and cleaning of idlers will help you to avoid problems before they start. Idlers are sensitive to the environment around them, and often become misaligned, freeze, or get clogged by dirt and debris.
- Inspect and evaluate the mounting bolts to make sure that they are secure.
Spare Parts & Materials
- Do an analysis of the repairs that you have done for the past year and the spare parts replacements that you have gone through. Keeping at least one or two spare parts in stock for each of the main conveyor components would be a safe route to take
- Check to make sure to use a high-quality sealer, ensure that the pulley lagging system creates enough friction, and install impact idlers and cradles to avoid heavy objects falling on and damaging the belt.
Resources
- Identify those Subject Matter Experts who have the expertise and training to fix equipment when it goes down.
Miscellaneous
- Schedule a time to inspect and evaluate every bolt, pulley sprocket, or any other pinch point to ensure that everything is securely in place.
- Know the capacity of the conveyor belt and what it can handle. Overloading the conveyor belt can cause major problems in operations.
- Make sure that employees working with or around conveyors are familiar with all safety warning stickers.
Effective Conveyor Maintenance Strategies
Tailor Your Maintenance Schedule:Establish a maintenance routine that aligns with the specific needs of your equipment and the conditions under which it operates.
Operator Training is Essential: Equip operators with the knowledge of proper conveyor operation and basic inspection techniques to enhance safety and efficiency.
Document Everything: Diligently document every maintenance activity to create a thorough history of your equipment. This practice not only aids in tracking recurring issues but also facilitates timely resolutions, ensuring optimal performance and longevity of your systems.
Implement a CMMS: Leverage a computerized maintenance management system (CMMS) to efficiently plan and track all maintenance tasks.
Stock Critical Spare Parts: Maintain an inventory of essential spare parts to minimize delays during maintenance and repairs.
Prioritize Safety Training:Regularly conduct safety training for all personnel working near conveyors to ensure a safe working environment.
Building an Effective Conveyor Maintenance Checklist
Preventive maintenance checklists are an essential part of an effective PM program and are included in preventive maintenance software. Checklists help ensure that tasks will not be missed and are completed quickly meeting defined specifications. Incorporating checklists into your work orders using computerized maintenance management system (CMMS) software improves efficiency and keeps your maintenance team focused on the tasks that need to be done. With eWorkOrders, creating checklists for each preventive maintenance task only takes a few minutes and can provide tremendous benefits for any organization.
Frequently Asked Questions (FAQs)
Why is it important to have a conveyor belt maintenance checklist?
A conveyor belt maintenance checklist is important because it helps to ensure that all of the necessary maintenance tasks are performed on a regular basis. This helps to prevent breakdowns and other problems that can lead to downtime and lost productivity.
What are the different types of conveyor belts?
Conveyor belts can be made from a variety of materials, including PVC, polyester, cotton, and rubber. There are four main types of conveyor belts: flat belts, modular belts, timing belts, and V-belts.
What are the two major causes of belt slippage?
The Wrong Conveyor Belt or Poor Installation are the main causes.
It’s possible for a belt to be too heavy for the system’s pulley, causing poor conveying. Over time, high pressure on the belt conveyor will cause it to fail prematurely. Improper installation is another problem that results in belt slippage.
What are the OSHA regulations for conveyor systems?
Safe practices. Only designated persons shall operate, repair, or service powered conveyors. The employer shall direct employees to stay off operating conveyors. Conveyors shall be operated only with all overload devices, guards, and safety devices in place and operable. Check the OSHA guidelines for more details.
See What Our Customers Are Saying
Additional Resources
Maintenance Terms &; Definitions Glossary
How to Avoid Overworked Machines & Unexpected Breakdowns
Overhead Crane Issues And How To Avoid Them
Preventive Maintenance Checklists – Important Tasks You Need To Include