Defined, How It Works and Benefits
Computerized Maintenance Management System (CMMS) is software, also known as Enterprise Asset Management (EAM) software, gives maintenance managers the tools to manage an organization’s data for maintenance operations, work orders, assets, equipment, preventive maintenance, inventory, workflows, safety compliance, teams, expenses, and other processes. To better understand what a CMMS is, let’s break down the term Computerized Maintenance Management System (CMMS):
Computerized(CMMS)
Computerized allows users to input, manage and store data in a computer database. Using a CMMS software solution gives users the ability to manage their data in one centralized database. Looking back at history, maintenance was largely reactive rather than proactive, because maintenance operations were done by pencil and paper before the 1980s. Keeping inventory records, updating data and ensuring that preventive maintenance was properly scheduled was challenging and costly. During this time these paper documents were stored in a desk or cabinet.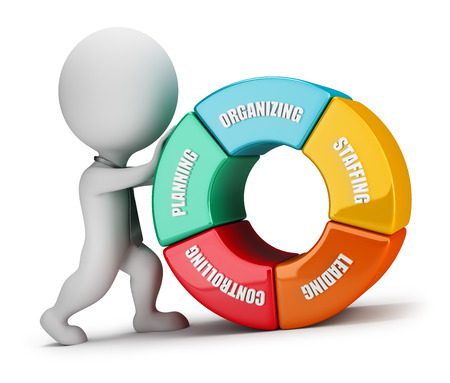
Maintenance (CMMS)
Maintenance management is the managing, planning, and maintaining of an organization’s resources and assets so that production proceeds effectively and no money is wasted due to inefficiency. Maintenance is the everyday tasks users perform when using a CMMS, such as work orders, scheduling and prioritizing things for repair, allocating resources, preventive maintenance scheduling, managing inventory, costs, regulatory compliance, and the list goes on. A CMMS software solution provides users with the tools to better manage maintenance tasks and improve communications.Management (CMMS)
Management is the administration and management of business practices to create the highest level of efficiency as possible. Maintenance Management is the most important role of Computerized Maintenance Management System (CMMS) software. CMMS gives users deep insight into their maintenance needs with detailed work order schedules, reliable reports, dashboards, inventory deadlines, and levels. CMMS cuts down the overhead of maintenance management by allowing organizations to access and retrieve accurate data and make competent decisions.System (CMMS)
The system is a combination of a set of integrated devices and capabilities that are designed to receive, process, manage, and present information in a user-friendly and meaningful format. A Computerized Maintenance Management System (CMMS) is the best software solution that reduces costs, saves time, and allows users to complete maintenance jobs efficiently. CMMS packages can produce status reports and documents giving details or summaries to analyze maintenance activities. eWorkOrders CMMS makes it easy to manage work orders, preventive maintenance tasks, assets, purchase orders, fleet, inventory levels, and more. Visit our Features and Industries sections to learn more.How Does CMMS Software Work?
A Computerized Maintenance Management System (CMMS) works by providing a centralized digital platform to manage and streamline maintenance operations. Here’s a breakdown of how a CMMS typically functions:Asset Management The CMMS maintains a comprehensive database of all assets/equipment, including details like specifications, maintenance history, manuals, warranty information, and associated spare parts/inventory. This allows easy access to asset data for informed maintenance decisions.
Work Order Management The core function of a CMMS is managing work orders for preventive and corrective maintenance tasks. Technicians can receive, prioritize, and complete work orders through the system, with access to relevant asset information and checklists. Managers can assign, track, and close out work orders centrally.
Preventive Maintenance Scheduling CMMS software enables the scheduling of recurring preventive maintenance tasks based on time, usage, or condition-based triggers. Automated work order generation ensures timely preventive maintenance.
Inventory/Spare Parts Management The CMMS tracks spare parts inventory levels and can automatically generate purchase orders when stock runs low, reducing downtime due to missing parts. Parts issuance and returns are also managed within the system.
Mobile Access Most modern CMMS solutions offer mobile capabilities that allow technicians to access asset data, receive/update work orders, and scan barcodes/QR codes directly from their mobile devices while out in the field, improving efficiency and productivity. The mobile functionality enables technicians to view and manage maintenance activities, access asset information, capture data, and stay connected to the CMMS system from anywhere, streamlining maintenance operations and reducing downtime.
Reporting and Analytics CMMS software offers reporting capabilities to analyze maintenance data like costs, downtime, productivity, and key performance indicators (KPIs), enabling data-driven decisions for continuous improvement.
Integration and Automation Advanced CMMS solutions can integrate with sensors, building management systems, and other software (ERP, EAM) to enable automated data capture, condition monitoring, and streamlined workflows.
In summary, a CMMS acts as a centralized digital hub, automating and optimizing maintenance processes through features like asset tracking, work order management, preventive maintenance scheduling, inventory control, mobile capabilities, and data-driven reporting/analytics
A Comprehensive Maintenance Management Solution
A Computerized Maintenance Management System (CMMS) is a powerful tool that helps organizations streamline and optimize their maintenance operations across various aspects. By leveraging a CMMS, companies can effectively manage and enhance the following areas:
Resource Optimization
- Efficient allocation of technicians and resources.
- Tracking labor productivity and costs.
Asset Lifecycle Management
- Centralized asset database and maintenance history.
- Asset performance tracking and replacement planning.
Work Order Management
- Automated work order generation and prioritization.
- Preventive maintenance scheduling based on triggers.
Preventive Maintenance
- Proactive maintenance strategies to reduce downtime.
- Recurring task tracking and condition monitoring.
Inventory Management
- Spare parts tracking and automated reordering.
- Minimizing stock-outs and associated downtime.
Compliance and Audits
- Comprehensive maintenance records for regulatory compliance.
- Audit trails and inspection report generation.
Reporting and Analytics
- Real-time visibility into operations and asset performance.
- Customizable reports and dashboards for data-driven decisions.
Mobile Capabilities
- Seamless remote access for technicians to view and update work order details, asset information, maintenance checklists, and capture multimedia data from their mobile devices, enabling real-time documentation and data entry while on the move.
- Enhanced communication and collaboration through instant notifications, alerts, and real-time data synchronization between technicians, supervisors, and the central CMMS, resulting in faster response times, improved coordination, and efficient resolution of maintenance issues.
Condition Monitoring
- Integration with sensors for real-time asset monitoring.
- Predictive analytics and alerts for potential failure.
The Benefits of a CMMS
There are many advantages and benefits to implementing and using computerized maintenance management system software. One of the main benefits is having the ability to more effectively manage maintenance teams, contractors, resources and align their maintenance practices and tasks with other departments and business goals. Some of the main benefits include:
- Automate Work Requests
- Manage Work Order And Facility Management Tasks
- Service Request Customer Portal
- Innovative Tools To Streamline Processes
- Manage Preventive Maintenace Schedules
- Schedule And Assign Employees, Crews, And Shifts
- Increase Asset\Equipiment Reliability
- Extend Asset and Equipment Life
- Reduced Equipment Downtime
- Reduced Downtime
- Control & Reduce Maintenance Costs
- Improve Productivity
- Improve Inventory Management
- Meet Compliance & Safety Regulations
- Easy Adoption To Changing Technologies
- Extensive Reporting Features
- Generate KPIs For Easy Analysis Of Your Maintenance Operations
Frequently Asked Questions:
How long does it take to implement eWorkOrders CMMS?
With over 24 years of experience, we have helped organizations around the world implement a world-class cloud-based CMMS maintenance solution. We have developed a very simple process to ensure a smooth implementation that meets your requirements. Implementation can be as short as a day but can be longer because it is based on many factors. How organized and prepared your current data is; how large your business is, etc. Going through a demo and speaking with one of our dedicated Account Managers, they will be able to work with you to come up with a plan to help meet your deadlines. For more information on our implementation process click here.
Do I need to buy any additional software?
No software to install, no hardware to purchase, upgrades & technical support are included in the eWorkOrders CMMS solution.
What is a “Modern CMMS”?
Modern Computerized Maintenance Management Systems (CMMS) are typically “in the cloud”, versus older systems that are on-premise in-house systems.
What industries benefit from CMMS?
A CMMS can be used in any industry, including Manufacturing, Facilities, Laboratories, Property Management, Hospitality, Restaurants, Restaurant Franchises, Schools, Utilities, Waste Water Treatment Plants, Airports, Oil & Gas, Government, Gyms, Camps, Stadiums & Arenas, Tourist Attractions, Resorts, Casinos, and more. If you work in an industry with valuable assets that need maintenance, a CMMS could be beneficial to you. If your business has assets that need maintenance, a CMMS could be beneficial to you in extending their lifespan and keeping them working at peak performance. Read more about each industry.
Does a CMMS work for all-size business operations?
If you have assets and facilities that need to be maintained, CMMS software is designed to support any size business, both small businesses and large corporations.
Are there any hidden costs?
The monthly or annual price you are quoted from our organization is all you will have to pay to continue using eWorkOrders.