Maintenance problem-solving is essential for ensuring smooth operations and minimizing downtime. By adopting a structured approach, maintenance teams can identify, analyze, and resolve issues efficiently, improving equipment reliability and overall productivity. This guide outlines a practical, step-by-step process for addressing maintenance challenges effectively.
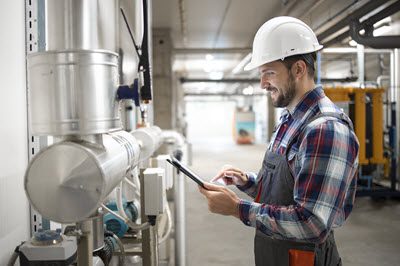
Step 1: Identify the Problem
The foundation of effective problem-solving lies in accurately identifying the issue. This involves:
- Gathering detailed information on the equipment’s history, symptoms, and operating environment.
- Consulting maintenance logs, inspection reports, and diagnostic data.
- Observing equipment during operation to detect anomalies or unusual patterns.
Understanding the issue thoroughly helps avoid misdiagnosis and ensures teams address the root cause instead of just the symptoms.
Step 2: Establish possible reasons for the malfunction or breakdown
With a clear problem definition, the next step is to identify potential causes:
- Brainstorm possible reasons for the malfunction or breakdown.
- Consider both apparent and less obvious contributing factors.
- Draw on past experiences and insights from similar problems.
Developing multiple theories prevents tunnel vision and encourages a comprehensive approach.
Step 3: Confirm the Root Cause Through Testing and Analysis
Testing theories help identify the root cause with confidence:
- Conduct diagnostic tests and inspections.
- Analyze data from sensors and monitoring systems.
- Use root cause analysis tools like the 5 Whys or fishbone diagrams.
The goal is to eliminate false assumptions and focus on critical factors contributing to the issue.
Step 4: Establish a Plan of Action
Once the root cause is determined, outline a clear action plan to fix the problem:
- Outline specific steps for addressing the root cause.
- Include both immediate fixes and long-term preventive measures.
- Allocate resources and assign roles to relevant personnel.
A well-structured plan ensures systematic and efficient problem resolution.
5: Implement the Solution
Executing the plan requires coordination and attention to detail:
- Carry out the planned repairs or modifications.
- Communicate with team members and departments involved.
- Document actions taken during the implementation phase.
Proper execution ensures effective problem resolution while providing valuable insights for future reference.
Step 6: Verify Full System Functionality
Post-implementation, confirm that the issue has been resolved and systems are fully functional:
- Conduct thorough testing of the repaired equipment.
- Monitor performance metrics to verify compliance with standards./li>
- Gather feedback from operators and maintenance personnel.
Verification ensures the solution’s effectiveness and restores operational confidence.
Step 7: Implement Preventive Measures
To avoid recurrence, establish preventive measures:
- Update maintenance procedures and schedules.
- Train staff and operators on best practices.
- Use condition monitoring or predictive maintenance tools.
Proactive steps reduce future issues and improve overall maintenance efficiency
Conclusion
Effective maintenance problem-solving relies on a structured, step-by-step approach emphasizing careful analysis, detailed planning, and diligent execution. Leveraging tools like CMMS software enhances this process by providing critical insights and streamlined workflows.
Regularly reviewing and refining your problem-solving strategies is vital for continuous improvement. To take your maintenance strategy to the next level, explore how eWorkOrders CMMScan simplify tasks, minimize downtime, and boost equipment reliability.