In the rapidly evolving landscape of diverse industries, the smooth operation of machinery and equipment stands as the linchpin of success. From boosting productivity to minimizing disruptions, the role of preventive maintenance is pivotal. This comprehensive guide delves into the critical role of preventive maintenance across various sectors, highlights its extensive benefits, and unveils a roadmap for implementing a top-tier program that garners recognition and operational distinction.
Understanding the Core Concepts: Preventive vs. Reactive Maintenance
Preventive maintenance, also known as preventative maintenance, stands in stark contrast to reactive maintenance, where repairs are conducted only after equipment failure. Preventive maintenance emphasizes scheduled and routine servicing, aiming to curb equipment failure and prevent the unwelcome scourge of unplanned machine downtime. It’s a strategy that resonates deeply with maintenance teams and facility managers who understand that proactive action is the key to operational efficiency.
Harnessing the Power of Real-Time Data Insights and CMMS
The modern landscape of maintenance has been revolutionized by real-time data insights and the advent of Computerized Maintenance Management Systems (CMMS). CMMS software serves as a technological marvel, allowing maintenance teams to plan and schedule tasks based on actual data, rather than relying on guesswork. This marriage of data and technology empowers preventive maintenance by identifying potential breakdowns before they occur, ensuring that maintenance activities are carried out while equipment is still operational.
Designing a Comprehensive Preventive Maintenance Strategy
A well-crafted preventive maintenance strategy involves a proactive approach that falls between reactive maintenance and highly evolved predictive maintenance. It encompasses the careful scheduling of maintenance tasks based on time, usage, and condition-based triggers. Manufacturer guidelines play a crucial role in determining the optimal preventive maintenance schedule, allowing critical assets to be maintained efficiently.
Advantages and Disadvantages of Preventive Maintenance
The benefits of preventive maintenance are manifold. It extends equipment lifespan through meticulous cleaning, lubrication, and parts replacement, saving substantial costs in the long run. Operational disruptions are minimized, safety levels are elevated, and the need for large and costly repairs is drastically reduced.
However, there are also considerations to be aware of. Maintenance planning requires resources and investment in time, while the risk of conducting maintenance too frequently could impact equipment efficiency. This is where CMMS shines, providing the framework to optimize maintenance frequency through data-driven decision-making.
Navigating the Terrain of Maintenance Applications
Preventive maintenance finds its application across various assets, from manufacturing facilities to intricate production lines. It encompasses systems like HVAC and electrical systems, ensuring they operate within safety and compliance levels. Cleaning, lubrication, and parts replacement – these are the As we conclude our exploration into the realm of preventive maintenance, it’s evident that a new era of operational excellence is within our grasp. Preventive maintenance isn’t just a concept; it’s a dedication to ensuring smooth operations. And with the dynamic capabilities of eWorkOrders CMMS by our side, this dedication becomes even more powerful. Here’s to a future where disruptions are minimized, costs are managed, and productivity thrives. With eWorkOrders CMMS and the principles of preventive maintenance at the forefront, we’re not simply aiming for operational excellence – we’re actively pioneering it, forging a path toward a prosperous and successful tomorrow.
Partnering for Excellence with eWorkOrders CMMS
As we conclude our exploration into the realm of preventive maintenance, it’s evident that a new era of operational excellence is within your grasp. Preventive maintenance isn’t just a concept; it’s a dedication to ensuring smooth operations. And with the dynamic capabilities of eWorkOrders CMMS by your side, this dedication becomes even more powerful. Here’s to a future where disruptions are minimized, costs are managed, and productivity thrives.
See What Our Customers Are Saying
Customer Case Studies
Customer Testimonials- Read More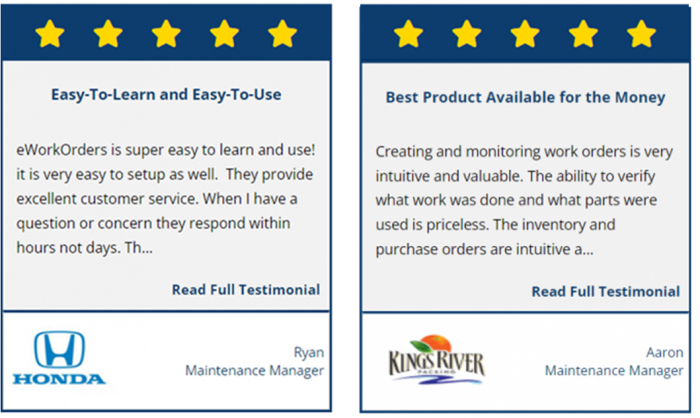
Frequently Asked Questions (FAQs)
What is preventive maintenance?
Preventive maintenance is a proactive approach to maintenance where regular servicing and inspections are performed on equipment to prevent breakdowns and unplanned downtime.
How does preventive maintenance differ from reactive maintenance?
Preventive maintenance involves scheduled maintenance tasks to prevent issues, while reactive maintenance addresses problems after they’ve occurred, leading to more downtime and costs.
What are the benefits of preventive maintenance?
Preventive maintenance extends equipment lifespan, reduces downtime, optimizes efficiency, lowers costs, and improves safety and compliance.