Planned Maintenance May Cause A Temporary Loss In Productivity
But the Costs of a Breakdown Could be Substantial!
Industrial robots have revolutionized modern manufacturing and production facilities, offering increased efficiency, precision, and flexibility. They provide a workforce that operates without breaks, sleep, or errors, bringing numerous benefits to the industry and its workforce. However, like any machinery, robots require regular maintenance to operate at optimal levels and avoid costly breakdowns or replacements. Preventative maintenance for industrial robots is essential for maximizing productivity and avoiding dips in quality or complete system shutdowns. Whether your business is currently utilizing robots or plans to do so in the future, understanding and implementing effective maintenance strategies is crucial for maximizing your investment.
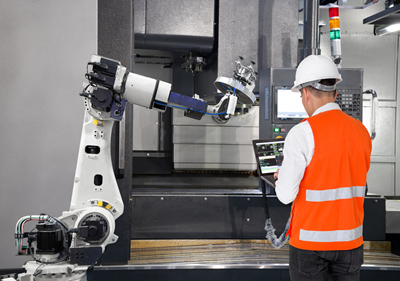
Why Preventive Maintenance is Important for Robots
Preventive maintenance is essential for robots to function at their best and last a long time while minimizing malfunctions and expensive replacements. Robots, like any mechanical piece of equipment, may develop a number of problems, including contamination, component wear, and misalignment, without proper maintenance. these can have a negative effect on their performance and result in breakdowns and unscheduled downtime.
Having a maintenance plan in place with routine maintenance procedures like cleaning, lubrication, and inspections can help to avoid unnecessary problems from happening, increasing the robot’s lifespan and lowering the frequency of failures and downtime. Scheduled preventative maintenance helps in locating and addressing minor issues before they become bigger, more expensive issues.
By ensuring that all safety measures and components are functioning as intended, performing preventative maintenance can contribute to enhancing the safety of the robotic system. This, in turn, can reduce the likelihood of accidents, employee injuries, and equipment damage to both the robotic system and its environment.
Preventative maintenance is fundamental to keeping robots operating as intended for as long as feasible while reducing downtime and repair expenses.
Robot Preventive Maintenance Checklist
Although each type of robot may have a different maintenance plan, numerous maintenance activities should be included in routine examinations. Consider the following common maintenance recommendations:
- Monitor the robot’s motion and inspect its harness, cables, and structure
- Listen for excessive noise or vibrations
- Examine the backup controller’s memory
- Verify proper brake functioning
- Inspect the teach pendant
- Evaluate the robot’s repeatability
- Tighten any external bolts
- Check for defective seals and signs of grease or oil leakage
- Remove any chips or debris from the robot
- Lubricate joints, bushings, and balancer housing
- Test the batteries in both the controller and robot arm, and replace them if necessary
- Clean the vents and cooling fans using compressed air, and replace any filters if necessary
- Clean the light curtains and sensors.
- Verify the integrity of any grippers, end-effectors, or tooling attached to the robot arm
- Inspect any fixtures or mounting hardware that the robot interacts with
- Check the condition of the robot’s drive belts or other motion components
- Verify the accuracy of any sensors or vision systems used by the robot
- Clean and recalibrate any force-torque sensors
- Check the condition of any pneumatic or hydraulic hoses and connections
- Inspect the condition of any machine vision lenses or cameras
- Verify the calibration and accuracy of any laser trackers or other measurement devices used for robot positioning
- Check the condition of any custom software or scripts used to program the robot
- Verify the functionality of any interlocks or safety devices, such as emergency stop buttons or light curtains
- Conduct any required software updates or firmware upgrades for the robot controller or peripheral equipment
- Verify that the robot is properly grounded and that all electrical connections are tight and secure.
Preventative Maintenance Frequency
Different robot manufacturers all have their own maintenance manuals that you’ll want to refer to for scheduling preventative maintenance.
Follow the timetables recommended by these manufacturers for performing preventative maintenance, and ensure that the maintenance is carried out as per their designated schedule. Regular inspection of industrial robots is essential to avoid minor issues from turning into significant problems, as well as to enable your maintenance team to work efficiently during peak production schedules.
Neglecting regular robot preventive maintenance can result in problems such as position deviation, repeatability issues, cable damage, program loss, and potential safety hazards. The maintenance of your robot may include activities that are specific to the manufacturer’s guidelines, as well as those that occur within daily, monthly, and annual timeframes. If the manufacturer’s specifications are stricter than the general guidelines provided, it is important to always adhere to them.
1. Daily Checks
To ensure that industrial robots are performing at optimal levels, some crucial functions must be performed daily. These checks are relatively quick and easy to conduct but can detect significant issues with industrial robots before they start their daily operations. The daily checks include:
- Visual inspection: Check for any visible damage, loose connections, or missing parts. Look for signs of wear and tear, such as frayed wires, cracked hoses, or damaged components.
- Cleanliness: Clean the robot and its components to remove any dust, dirt, or debris that may have accumulated during use. This will help prevent contamination of sensitive components and ensure proper functioning.
- Lubrication: Check and lubricate any moving parts such as joints, gears, and bearings. This will help ensure smooth movement and prevent excessive wear on these components.
- Battery level: Check the battery level and charge it as needed. Make sure that the battery is properly installed and securely connected.
- Sensors: Check the sensors on the robot to ensure they are clean and unobstructed. This will help the robot to detect objects and navigate properly.
- Software updates: Check for any software updates and install them as needed. This will ensure that the robot is running the latest version of its software and is optimized for performance.
- Test Run: Run a test program to ensure the robot is functioning properly. Check for any error messages or anomalies during the run.
2. Monthly Checks
Monthly checks should be more detailed than daily checks but are still largely superficial. These will catch any operational issues and prevent the majority of problems that occur:
- Power system: Check the power system, including batteries, chargers, and power cables. Inspect for any signs of damage or wear and tear, and replace any faulty components.
- Drivetrain: Check the drivetrain, including belts, pulleys, and chains, and ensure they are properly tensioned and lubricated. Replace any components that are worn or damaged.
- Control system: Inspect the control system, including the controller, interface, and wiring. Check for any loose connections, damage, or wear and tear, and repair or replace as needed.
- End effectors: Inspect the end effectors, such as grippers or sensors, and ensure they are properly aligned and calibrated. Clean or replace any parts that are worn or damaged.
- Safety systems: Check the safety systems, including emergency stop buttons, safety switches, and guards. Make sure they are functioning properly and are properly installed.
- Cleaning: Perform a more thorough cleaning of the robot, including its interior components, to remove any accumulated debris or dirt.
- Programming: Review and update the robot’s programming as needed to ensure it is optimized for performance and productivity.
- Ventilation: Clean and ventilate the robot controller’s cooling fans to maximize airflow.
- Back-up memory: Back up the robot controller’s memory to prevent the loss of important data or programs.
- Visual inspection in motion: Complete a visual inspection of the robot in motion, checking the robot, harness, and cables to identify any signs of wear, misalignment, or other issues that may affect performance.
3. Quarterly Checks
Quarterly checks are even more detailed than monthly checks and focus on safety features and fixtures. These checks include the following:
- Check the batteries: Check the batteries and their charging status. Make sure they are properly charged and functioning correctly. Replace them if necessary.
- Check the joints: Inspect the joints and bearings for wear and tear. Replace any damaged components.
- Check the sensors: Ensure that all sensors are working correctly. Test each one to make sure it is accurately detecting and measuring its target.
- Check the wiring: Check the wiring and connectors for any signs of damage or wear. Replace any damaged components.
- Lubricate moving parts: Lubricate any moving parts to reduce friction and extend the life of the robot.
- Check the software: Check the software to ensure that it is up-to-date and functioning correctly. Update any outdated software and troubleshoot any issues.
- Check all connections: Check all connections between the robot and any power supplies, fans, or safety equipment.
- Check all unit cables: Check all unit cables for any kinks, pinch points, cuts, tears, or loose connections.
- Tighten all bolts: Tighten all bolts, especially external mounting bolts.
- Detail clean the mechanical unit: Detail clean the mechanical unit to remove any chips or debris.
4. Annual Checks
Annual checks should be extremely detailed to cover all aspects of machine functionality. This is the time to review any performance metrics from the last year to see if the machine has shown any signs of slowing down or consuming more power than usual. Some of the checks include the following:
- Replace batteries: It is recommended to replace batteries every year in the mechanical unit, RAM, APC, and CPU. It is essential to ensure these batteries do not die, since this may cause serious issues in functionality.
- Replace grease and oil: Replace grease and oil and be sure to select options that are recommended by the manufacturer.
- Inspect brake operation: Inspect the operation of the brake to ensure there are no delays.
- Check all connections: Check all connections between the robot and any power supplies, fans, or safety equipment.
- Check all unit cables: Check all unit cables for any kinks, pinch points, cuts, tears, or loose connections.
- Check the wiring: Check the wiring and connectors for any signs of damage or wear. Replace any damaged components.
- Tighten all bolts: Tighten all bolts, especially external mounting bolts.
- Detail clean the mechanical unit: Detail clean the mechanical unit to remove any chips or debris.
- Inspect joints and bearings: Inspect the joints and bearings for wear and tear. Replace any damaged components.
- Inspect sensors: Ensure that all sensors are working correctly. Test each one to make sure it is accurately detecting and measuring its target.
- Check the software: Check the software to ensure that it is up-to-date and functioning correctly. Update any outdated software and troubleshoot any issues.
- Complete functional tests: Complete thorough functional tests to make sure the robot meets specifications.
Industrial Robot Safety Tips
To minimize the risk of accidents involving robots, it’s important to follow industrial robot safety tips during programming, maintenance, repair, setup, and testing that require human interaction. Below are some safety tips to consider:
- Install boundary warning devices, barriers, and interlocks around robot systems.
- Safety curtains, fences, or work cell equipment should be used as barriers around the cell to protect employees.
- Provide annual robot safety training for employees who work with robots.
- Offer work cell operators specialized training tailored to their specific robot.
- Establish and enforce a preventive maintenance program for robots and work cells.
- Ensure operators read and comprehend robot system documentation, especially that pertaining to robot safety.
- Allow only qualified employees familiar with the safety requirements of working with a robot to operate robot systems.
- In addition to implementing industrial robot safety practices for a facility and its staff, the robotic work cell must meet the following requirements:
- The maximum reach of a robot should be marked on the floor with safety tape or paint.
- A flashing warning device must be visible from any point around the work cell.
- Emergency stop buttons should be located around the cell.
Robot Decommissioning
Determining when to decommission an industrial robot can be a difficult decision, particularly when maintenance costs start to add up. It’s essential to consider the machine’s usable life, which varies and is based on its function and how well it’s been maintained.
Robot decommissioning is a vital component of the manufacturing process and plays a significant role in freeing up plant floor space. Robotic assembly lines or cells can be disassembled quickly while preserving their value. When deciding to decommission a unit, it’s crucial to consider the following factors:
- Retiring an industrial robot solely because of its age is usually insufficient. Start by calculating how much you spend on replacement parts and whether you’re having trouble finding those components because they’re no longer readily available. In such instances, you may need to pay more or wait longer for them to arrive.
- Is the robot breaking down more frequently than before? Shorter intervals between repairs may indicate that it’s time to consider decommissioning the machine. Additionally, more costly and frequent issues may indicate that it’s no longer economically feasible to
- Investigate whether the robot’s performance has decreased, which could be caused by improper upkeep. If maintenance is being done correctly and the quality is still not up to par, it may be time to decommission the robot and install a newer one, which may require a transition period but is necessary to keep the facility productive.
- Consider the urgency of the decommissioning, especially if it must take place during a plant shutdown or downtime. Delays can be costly to the production process if deadlines are not met.
- Avoid disconnecting any of the robot cables during decommissioning unless the robot is too old to hold any value. Robot cables are often specific to the robot model and can be expensive to replace, reducing the resale value of the unit. Disconnecting cables correctly may require labor, but this cost is usually outweighed by the value of the cables on the used market.
- Consider the ease of decommissioning, which may vary depending on the project. Some projects may involve simple takedowns, while others may require the removal of costly structures like mezzanines. The cost of removing these structures may be absorbed into the removal cost to lower or negate out-of-pocket expenses to the seller.
- The location of manufacturing plants can be an important factor. Those located far from prime industrial areas may face difficulties when it comes to removing heavy machinery. Local contractors may not have the necessary expertise to carry out the precise removal function required for dismantling robotic lines.
Tips for Developing an Effective Robot Preventive Maintenance Program
We have outlined some of the maintenance tasks and their timelines, It’s now time to create and implement a schedule for the preventative maintenance of your industrial robots. Following the steps below can help to develop and implement a preventative maintenance plan for your industrial robots.
1. Establish a Maintenance Schedule
Begin by creating a strict maintenance schedule based on the manufacturer’s specifications for your equipment. Use the recommended timeline as a guide but adjust it to fit your specific needs. Include daily, monthly, and annual maintenance items in your plan. If necessary, increase the frequency of maintenance items based on your industry or application.
2. Implement the Schedule
Ensure that the maintenance schedule is communicated to all stakeholders and personnel and posted in a visible location such as a company bulletin or calendar system. Train employees during their annual training sessions to emphasize the importance of preventive maintenance. Review the schedule regularly to avoid conflicts with manufacturing flow, customer orders, or other company matters.
3. Regularly Reassess the Plan
Assess your preventive maintenance plan periodically to ensure it aligns with changes in your company, such as the introduction of new equipment, automation expansion, changes in staff or floor organization, or increases in energy consumption. Review the plan with decision-makers and essential staff and determine a new maintenance schedule if necessary.
4. Find Experts to Make Repairs
Consider partnering with specialists in industrial robot maintenance to help you create a tailored maintenance plan and perform regular maintenance tasks. Although having repair personnel on staff may be convenient, it can be expensive, especially for smaller companies. Working with experienced professionals who understand your equipment and processes, can help you maintain your industrial robots effectively and affordably.
5. Data Analytics
Consider using data analytics and predictive maintenance technologies to further enhance your maintenance program. By collecting and analyzing data from your equipment, you can identify patterns of equipment failures and predict when maintenance is necessary. This can help you proactively schedule maintenance before equipment failure occurs, avoiding unplanned downtime and increasing production efficiency.
Benefits Of Regular Robot Maintenance
- Routine Maintenance: Regular maintenance can help identify and address bottlenecks, inefficient processes, and unnecessary downtime. This can lead to improved production efficiency, reduced lead times, and increased output.
- Reducing Manufacturing Time: If regular maintenance isn’t followed, robots may slow down over time due to poor lubrication or worn parts. While the change may not be noticeable, it can add up to substantial amounts of lost time.
- Optimal Performance: Regular maintenance ensures that robots are functioning at their highest capacity and efficiency, allowing them to perform at their best.
- Improved Productivity: Robots improve productivity by automating repetitive tasks.
- Enhanced Safety: Regular maintenance helps ensure that robots are functioning safely and reliably, minimizing the risk of accidents or injuries to workers.
- Minimizing Downtime: Maintenance can help prevent unexpected breakdowns and malfunctions, minimizing the risk of costly downtime and lost productivity.
- Minimized Repair Costs: Identifying and fixing small problems early through regular maintenance can help prevent more significant issues from occurring, which can result in expensive repairs.
- Improving Product Consistency: Regular maintenance can help ensure that products are manufactured to the same quality standards each time, reducing the risk of defects and customer complaints.
- Reducing Energy Consumption: Poorly-maintained robots with worn-down parts or inadequate lubrication may consume more power than necessary to operate. Even minor changes can result in significant increases in energy costs when multiple robots are involved. By maintaining industrial robots properly, manufacturing companies can ensure they are functioning efficiently, thereby minimizing overhead costs and the overall cost of ownership.
- Maximizing Equipment Lifespans: Industrial robots are costly investments, and their lifespan can be significantly extended through regular preventative maintenance by manufacturing companies.
- Lowering The Total Cost of Ownership: Proper maintenance can help extend the lifespan of machinery and equipment, reducing the need for costly repairs and replacements. It can also help improve efficiency and reduce energy costs, resulting in overall cost savings for the manufacturing company.
Robots Maintenance Management Software
Robot maintenance management software is a valuable tool for manufacturing companies to manage and optimize their robotic systems. This software can help streamline maintenance processes by scheduling regular inspections and preventive maintenance tasks, monitoring equipment health, and automatically generating work orders. With the use of real-time monitoring, the software can detect any malfunctions and alert the maintenance team for immediate intervention, reducing equipment downtime. Additionally, it can provide analytics and generate reports to help managers make informed decisions about their maintenance practices, ensuring maximum efficiency and reducing costs. A computerized Maintenance Management System (CMMS) is a type of maintenance management software that is commonly used for this purpose. It provides a centralized database for storing all maintenance-related information, such as work orders, equipment history, and maintenance schedules, allowing for easier tracking and reporting.
Final Thoughts
Robot maintenance is essential for the continued efficiency and longevity of industrial robots. By implementing a proper maintenance program, companies can improve product quality, reduce energy consumption, and maximize equipment lifespan. This ultimate guide and checklist provide a comprehensive overview of the best practices for robot maintenance, including regular inspections, lubrication, and cleaning, among others. By following these steps and regularly maintaining their robots, manufacturers can optimize their production processes, enhance safety, and reduce costs. It is important to remember that maintenance needs may differ depending on the type of robot and the industry in which it operates. Therefore, companies should tailor their maintenance programs to their specific needs and seek professional advice when necessary. Ultimately, by prioritizing robot maintenance, manufacturers can ensure their robots are operating at peak performance, leading to increased productivity, profitability, and competitiveness.