The purpose of this Standard Operating Procedure (SOP) document is to define the process of registering into the service department’s database a piece of equipment identified in the field.
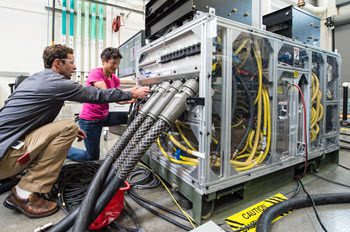
IMPORTANT NOTES
The goal of this SOP is not just to label equipment but to ensure that all pertinent and available information about the asset is entered into the service department’s database. Simply putting a bunch of tags on equipment without first updating the service department’s database will render your labeling system next to useless in short order.
Also, as an internal control, the manager of the pre-stamped metal tags should keep them locked up in a safe place.
REQUIREMENTS
Pre-stamped, metal tags are great for labeling equipment. They are durable and you cannot make duplicates of the same tag. Designate one or two employees to safeguard your tags so that there is some control over their distribution.
This SOP assumes that a software package will be utilized and that the service department’s database is accessible via a Smartphone or mobile device out in the field. The software should be capable of automatically assigning new asset numbers and should be able to upload photographs of the equipment from out in the field.
PROCEDURE
When a piece of equipment to be maintained by the service department is found without a label, a technician will access the database from a Smart Phone or mobile device and add in the necessary information about the asset (e.g., Building/Area, Asset Description, Location, Make, Model Number, Serial Number, etc.).
Pictures of the asset, including pictures of any information plates, should be uploaded into the database. Uploading pictures will make it easier for technicians to identify this equipment in the future.
Uploaded pictures of the information plates can be viewed from anywhere. This easily saves lots of time and expense versus having to go physically out into the field to visit a piece of equipment to collect its information.
When ordering equipment parts, pictures of the information plates, which are retrievable from the database, can be attached easily to an email. This eliminates any errors from entering by hand long cryptic model and serial numbers.
Moreover, Information plates often degrade over time to the point of being unreadable. By taking a picture of the plate and uploading it onto the asset record in the database, this important information will be saved indefinitely.
A work order should be issued requesting that this equipment be tagged.
The worker assigned to label the equipment requests the applicable tag from the employee who safeguards them.
The employee who manages the tags ensures that the data related to the identified equipment is entered into the system. Any service manuals or other supporting documents should be uploaded to the database at this time.
An assessment for preventative maintenance also should be performed at this point and scheduled in the database.
The assigned worker receives the tag, applies it to the applicable piece of equipment, and closes out the work order.
Conclusion
Implementing the Standard Operating Procedure (SOP) for Labeling Equipment is essential for ensuring thorough asset management and operational efficiency. By meticulously registering equipment in the service department’s database and adhering to the outlined guidelines, organizations can streamline maintenance processes and improve overall effectiveness. Integration of eWorkOrders CMMS (Computerized Maintenance Management System) further enhances this SOP, providing advanced features like mobile access, photo uploading, and automated asset numbering. With eWorkOrders, organizations gain a powerful tool to optimize asset tracking, maintenance scheduling, and communication between field technicians and management. This strategic combination of SOP and eWorkOrders CMMS empowers organizations to achieve greater visibility into their assets, enhance preventive maintenance efforts, and ultimately drive long-term operational success.
>