Reactive maintenance, while often a necessary response to unexpected equipment failures, can significantly impact a company’s bottom line. The costs associated with downtime, emergency repairs, and the potential for collateral damage are substantial. However, recognizing the challenges posed by reactive maintenance is the first step toward implementing a solution that can mitigate its impact. In this article, we will delve into the drawbacks of reactive maintenance and propose a comprehensive solution to optimize maintenance strategies and safeguard your bottom line.
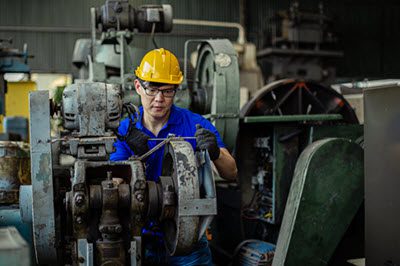
The Solution: Proactive Maintenance Strategies
Incorporate Predictive Maintenance Strategies
By leveraging data and analytics, predictive maintenance foresees potential equipment failures. Actively monitoring critical indicators such as vibration, temperature, or lubrication levels empowers companies to strategically plan maintenance activities, effectively reducing downtime and prolonging the operational life of their equipment.
Integrating a CMMS establishes a centralized platform for managing maintenance activities, work orders, and assets. The streamlined maintenance workflows and proactive scheduling enabled by a CMMS facilitate a smooth shift from reactive to proactive maintenance practices, enhancing overall operational efficiency.
Invest in Continuous Employee Training
A well-informed maintenance team is essential for identifying and addressing potential issues before they escalate. Regular training programs ensure that your team possesses the requisite knowledge and skills to execute preventative maintenance measures, minimizing reliance on reactive approaches.
Implement Regular Equipment Inspections
Establishing a consistent inspection schedule empowers maintenance teams to proactively identify and resolve potential issues before they result in breakdowns. This proactive approach contributes to maintaining equipment health and preventing unplanned downtime, ultimately optimizing overall operational effectiveness.
Conclusion
While dealing with equipment failures, we can’t always escape reactive maintenance, but it’s crucial to understand its impact on a company’s financial well-being. The increased downtime, emergency repair costs, and potential collateral damage can really take a toll. Recognizing the challenges posed by reactive maintenance is the first step toward a smarter and more cost-effective maintenance strategy. We can make a positive shift by incorporating predictive maintenance strategies, embracing a Computerized Maintenance Management System (CMMS), investing in ongoing employee training, and regularly inspecting equipment. This transition from reactive to proactive maintenance not only fine-tunes our strategies but also plays a vital role in keeping the company financially sound. The end goal is to strike a balance that minimizes downtime, cuts costs, extends equipment lifespan, improves overall operational effectiveness, and ensures the long-term sustainability of the business.