Maintenance troubleshooting stands as the silent hero behind the seamless operation of any industrial machinery. When equipment falters or behaves unexpectedly, it’s the troubleshooter’s keen eye and systematic approach that come to the rescue. Beyond the routine checks and preventive measures lies a dynamic process—a fusion of art and science. In this article, we unravel the essence of maintenance troubleshooting, exploring not only its significance but also unveiling 12 powerful techniques to elevate your mastery. From identifying elusive problems to crafting effective solutions, this is your key to conquering the intricate dance of equipment maintenance. Welcome to the realm where challenges transform into victories through the artful precision of troubleshooting.
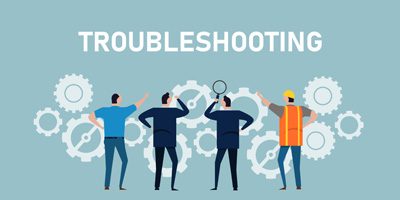
What is Maintenance Troubleshooting?
Maintenance troubleshooting is a structured and essential approach designed to pinpoint and address issues within malfunctioning components and systems. Born out of the necessity to counter unexpected equipment failures, this process extends its reach from individual device malfunctions to the comprehensive breakdown of entire operating systems. The troubleshooting journey encompasses tracking down the origin of the problem, effecting repairs, and instating corrective measures to thwart a recurrence. Effective troubleshooting methodologies hinge on the adept gathering of information, astute diagnosis of potential causes, and the strategic application of solutions tailored to rectify the issue at hand. Following a systematic four-step trajectory—identify the problem, plan a response, test the solution, and resolve the problem—this process is iterative, often requiring multiple cycles before achieving a resolution. Leveraging these methodologies, maintenance teams stand to optimize resource allocation, bolster efficiency, and elevate overall maintenance performance. Techniques encompass regular inspections, prioritizing critical assets, formulating preventive maintenance plans, embracing predictive maintenance, implementing reliability-centered maintenance (RCM), meticulous maintenance record-keeping, staff training, root cause analysis, parts consolidation before troubleshooting, and fostering unwavering management commitment to preventive maintenance practices.
The Importance of Maintenance Troubleshooting
Maintenance troubleshooting stands as the linchpin of operational continuity in the industrial landscape. It serves as the vigilant guardian against the unpredictability of equipment failure, ensuring the seamless functionality of diverse machinery. The significance of maintenance troubleshooting becomes glaringly evident in the face of unexpected breakdowns, where the absence of clear warning signs necessitates a methodical approach to identifying and rectifying underlying issues. While preventive maintenance and condition-based strategies mitigate the risk of unplanned downtime, the reality remains that machinery failures defy a consistent pattern. In this dynamic environment, robust maintenance troubleshooting techniques emerge as the key to minimizing failure, swiftly implementing remedies, and fostering operational resilience. The importance lies not just in resolving issues as they arise, but in proactively fortifying systems against potential disruptions, ultimately defining the success and longevity of industrial operations.
Why Strong Maintenance Troubleshooting Techniques Matter
Maintenance troubleshooting represents a methodical approach to identifying and resolving issues within malfunctioning components and systems. It’s essential due to unexpected equipment failures, ranging from mobile device malfunctions to full system breakdowns. The irregular nature of machinery failures, not following predictable patterns, underscores the criticality of troubleshooting. While preventive and condition-based maintenance reduces unplanned downtime, complete elimination is challenging. Robust troubleshooting techniques minimize failures and expedite timely repairs. In the absence of refined troubleshooting, there’s a risk of wasted time, production losses, compromised safety, and increased failure instances. Proficiency in troubleshooting techniques distinguishes between an overwhelming backlog and a stable maintenance program. Effective methodologies involve comprehensive information gathering, precise diagnosis, and targeted solutions. Adopting these techniques enables organizations to allocate resources strategically, enhance operational efficiency, and elevate overall maintenance performance.
Maintenance Troubleshooting Tips
It all begins by equipping yourself with the right tools.
Using CMMS Software for Maintenance Troubleshooting
Maintenance software, particularly a Computerized Maintenance Management System (CMMS), streamlines troubleshooting. It assists in organizing data, providing real-time access, and facilitating efficient documentation. From building detailed asset histories to utilizing failure codes, CMMS software enhances overall troubleshooting capabilities.
Holistic Documentation Practices
Comprehensive documentation is a cornerstone of effective maintenance troubleshooting. Implementing thorough record-keeping practices ensures that critical information, such as equipment history, past issues, and successful resolutions, is readily available. This wealth of knowledge becomes instrumental in streamlining the troubleshooting process and contributes to more informed decision-making.
Build Detailed Task Lists (Checklists)
Solid planning is vital for exceptional troubleshooting. Detailed task lists provide technicians with a blueprint, preventing crucial steps from being overlooked.
Quantify Asset Performance
In-depth knowledge of asset performance is critical for effective troubleshooting. Advanced reporting plays a crucial role in analyzing asset performance at a deeper level.
Make Additional Information Accessible
Create a digital knowledge hub, ensuring that valuable resources such as reports, asset histories, failure codes, and task lists are easily accessible.
Create In-Depth Asset Histories
Beyond manuals, detailed asset histories are essential. They provide a method for cross-referencing current issues with past problems and prioritizing solutions effectively.
Root Cause Analysis and Failure Codes
Utilize root cause analysis by repeatedly asking “why” to identify the immediate and core causes of failure. Integrate failure codes for consistent categorization.
Predictive Maintenance Integration
Take your troubleshooting to the next level by integrating predictive maintenance techniques. Leverage data analytics and sensor readings to foresee potential issues before they escalate. Adopting a proactive approach minimizes unplanned downtime and enhances equipment reliability.
Condition Monitoring Techniques
Implement advanced condition monitoring techniques to assess the health of critical assets. Regularly monitor factors like vibration, temperature, and lubrication conditions. A proactive understanding of asset conditions allows for early detection of abnormalities, facilitating quicker and more accurate troubleshooting.
FMEA Analysis (Failure Modes and Effects Analysis)
Embrace Failure Modes and Effects Analysis (FMEA) to systematically evaluate potential failure modes of critical components. This structured approach helps in identifying failure causes, their effects, and the likelihood of their occurrence. By conducting FMEA, you can develop robust preventive measures to address potential issues.
Real-Time Collaboration Platforms
Facilitate real-time collaboration among maintenance teams. Utilize digital platforms that allow technicians to share insights, troubleshooting techniques, and solutions instantly. Collaborative tools enhance the collective knowledge of the team, enabling faster problem resolution.
Continuous Training Programs
Invest in continuous training programs for maintenance staff. Equip them with the latest industry knowledge, technological advancements, and troubleshooting methodologies. A well-trained team is more adept at handling diverse challenges and implementing efficient solutions.
Mastering the Art and Science of Maintenance Troubleshooting
Navigating the intricate landscape of maintenance, mastering the art and science of troubleshooting emerges as a fundamental skill. Elevate your proficiency by seamlessly incorporating predictive maintenance, advanced monitoring, systematic analysis, and continuous training into your troubleshooting toolkit. These strategies contribute to the resilience and agility of your maintenance operation, allowing it to adeptly address the complexities of modern industrial challenges. The integration of collaborative platforms ensures real-time insights, fostering swift problem resolution and enriching the collective knowledge of your team. Acknowledging the inherent uncertainty in diagnosing the cause of failure, these approaches not only empower effective troubleshooting in the present but also foster a forward-looking, adaptive approach. Embrace these techniques to steer your maintenance practices towards sustained success in the ever-evolving landscape of technology and operational demands.
Remember, effective troubleshooting isn’t just about solving today’s problems; it’s about fortifying your maintenance strategy for the challenges of tomorrow. As technology evolves, so should your approach to troubleshooting, ensuring a sustainable and high-performing maintenance ecosystem.
FAQs About Maintenance ToubleShooting
Is troubleshooting the same as maintenance?
No, troubleshooting and maintenance are distinct yet interconnected processes. Maintenance involves routine activities aimed at preventing equipment failure, while troubleshooting is the systematic approach to identifying and resolving issues when unexpected failures occur.
Why is maintenance troubleshooting important?
Maintenance troubleshooting is crucial as it allows for the swift identification and resolution of issues with faulty components and systems. It helps minimize downtime, enhance efficiency, and maintain a stable maintenance program.
What is the difference between preventive maintenance and troubleshooting?
Preventive maintenance focuses on scheduled activities to prevent equipment failure, while troubleshooting deals with unplanned issues, diagnosing the root cause, and implementing solutions to bring equipment back to operational status.
How does technology contribute to maintenance troubleshooting?
Technology, such as Computerized Maintenance Management Systems (CMMS) and predictive analytics, streamlines troubleshooting by organizing data, providing real-time access to information, and facilitating efficient documentation.
Can maintenance troubleshooting be proactive?
Yes, by integrating predictive maintenance techniques, condition monitoring, and Failure Modes and Effects Analysis (FMEA), maintenance troubleshooting can become proactive. This allows for the early detection and prevention of potential issues before they escalate.
How can organizations optimize maintenance troubleshooting?
Organizations can optimize maintenance troubleshooting by creating detailed task lists, quantifying asset performance, making information easily accessible through digital knowledge hubs, and investing in continuous training programs for maintenance staff.
Is troubleshooting always successful in resolving issues?
While troubleshooting is a systematic approach, it doesn’t guarantee 100% success due to the complexity of some issues. However, effective troubleshooting significantly improves the chances of identifying and resolving problems efficiently.