Effective maintenance management is an important component in the operations of manufacturing and warehouse industries, encompassing the meticulous planning, scheduling, and execution of maintenance activities to uphold the optimal functionality of equipment and facilities. Companies can adopt various maintenance strategies to manage these activities.
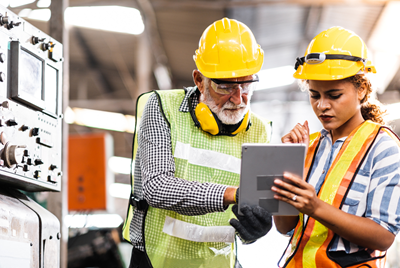
What is Maintenance Management?
Maintenance management involves the meticulous planning, scheduling, and execution of maintenance activities to ensure equipment and facilities remain in optimal working condition. This practice is crucial for production and warehouse industries, aiming to guarantee the availability, efficiency, and safety of equipment and facilities. Tools and techniques are employed to optimize maintenance processes, minimize downtime, and enhance equipment reliability.
CMMS (Computerized Maintenance Management System)
CMMS, an acronym for Computerized Maintenance Management System, is a software application designed to assist companies in managing their maintenance activities. It provides a centralized platform for overseeing maintenance tasks, including work orders, preventive maintenance, inventory management, and asset tracking. The use of CMMS aims to streamline maintenance activities, diminish downtime, and amplify equipment reliability.
Advantages of Different Maintenance Strategies
Reactive Maintenance
Lower Maintenance Costs: Resources are conserved as maintenance activities are performed only when necessary.
Flexibility: Quick responses to equipment failures due to an as-needed maintenance approach.
Preventive Maintenance
Increased Equipment Reliability: Early identification and resolution of potential issues enhance equipment reliability.
Lower Maintenance Costs: Proactive measures prevent major problems, reducing overall maintenance costs.
Predictive Maintenance
Increased Equipment Reliability: Early detection of issues enhances equipment reliability.
Lower Maintenance Costs: Proactive issue resolution minimizes maintenance costs.
Proactive Maintenance
Increased Equipment Performance: Identification and resolution of potential issues improve equipment and facility performance.
Lower Maintenance Costs: Early issue resolution reduces overall maintenance costs.
Disadvantages of Different Maintenance Strategies
Reactive Maintenance
Increased Downtime: Reliance on failures can result in prolonged downtime.
Higher Maintenance Costs: Costs may escalate due to reactive responses.
Preventive Maintenance
Increased Maintenance Costs: Regular maintenance can lead to higher costs.
Reduced Flexibility: Fixed schedules may reduce flexibility in addressing urgent needs.
Predictive Maintenance
Increased Complexity: Specialized tools and techniques may be required, adding complexity.
Higher Upfront Costs: Initial investment in specialized tools can be substantial.
Proactive Maintenance
Increased Upfront Costs: Investment in specialized tools and equipment may be higher.
Reduced Flexibility: Activities may be performed regardless of immediate necessity.
Conclusion
Maintenance management is a pivotal element in the operational efficiency of production and warehouse industries. Various maintenance strategies exist, each with its advantages and disadvantages. When utilizing CMMS solutions, such as eWorkOrders or similar tools, companies aim to streamline maintenance activities, reduce downtime, and enhance equipment reliability. Integrating these systems is part of the broader strategy to optimize maintenance processes in line with industry needs.
Frequently Asked Questions About Maintenance Strategies
What are the 4 maintenance strategies?
- Risk-based maintenance.
What are the 4 benefits of a maintenance strategy?
What is the best maintenance strategy?
While there are numerous factors to consider when selecting a maintenance strategy, preventive maintenance stands out as one of the most widely adopted approaches. The decision on the best strategy involves a tailored consideration of factors such as equipment type, budget constraints, maintenance goals, adherence to industry standards, and risk tolerance. It’s an individualized choice that reflects the unique needs and operational context of each organization.
How can I implement a maintenance management system in my company?
Implementing a maintenance management system involves evaluating current practices, selecting a suitable system, and developing an inclusive implementation plan involving all stakeholders.
How can I measure the effectiveness of my maintenance management system?
Key performance indicators (KPIs) such as equipment uptime, maintenance costs, and backlog can be tracked, while feedback from stakeholders provides insights for improvement.
What is Total Productive Maintenance (TPM)?
Total Productive Maintenance (TPM) is a comprehensive maintenance strategy aimed at achieving optimal production efficiency. It focuses on minimizing breakdowns, defects, unplanned stops, and safety incidents within the production process. By promoting proactive and preventive measures, TPM seeks to enhance equipment effectiveness and overall operational efficiency, ultimately working towards the goal of near-perfect production outcomes.
How do different maintenance strategies—Corrective Maintenance, Preventive Maintenance, Risk-Based Maintenance, and Condition-Based Maintenance—differ from Total Productive Maintenance (TPM)?
Corrective Maintenance vs. TPM: Corrective maintenance is a reactive strategy that addresses equipment issues after they occur, focusing on repairs to restore functionality. In contrast, Total Productive Maintenance (TPM) is proactive, aiming to prevent breakdowns and defects through systematic and holistic maintenance, promoting near-perfect production outcomes rather than responding to failures.
Preventive Maintenance vs. TPM: Preventive maintenance involves scheduled tasks to prevent failures, whereas TPM takes a broader approach. TPM optimizes overall production efficiency by addressing breakdowns, defects, unplanned stops, and safety incidents, going beyond Preventive Maintenance’s focus on routine scheduled tasks.
Risk-Based Maintenance vs. TPM: While Risk-Based Maintenance prioritizes maintenance tasks based on risk assessments and potential consequences, TPM seeks near-perfect production outcomes by minimizing various issues. TPM is holistic in addressing efficiency concerns, whereas Risk-Based Maintenance prioritizes tasks based on perceived risks.
Condition-Based Maintenance vs. TPM: Condition-based maintenance relies on real-time monitoring and maintenance triggered by the specific condition or performance of equipment. In contrast, TPM aims for optimal efficiency by addressing a broad range of potential problems within the production process, going beyond real-time condition monitoring to achieve overall operational excellence.