Create, generate, and customize reports tailored to your specific needs. With eWorkOrders, you have the flexibility to choose from a wide range of pre-built report templates. Some of the report types you can create include:
In today’s complex industrial environment, where reliability and efficiency are critical, organizations are continually seeking effective ways to manage and prevent failures. One such method is FRACAS—Failure Reporting, Analysis, and Corrective Action System. This in-depth guide explores the fundamentals of FRACAS, covering its history, process, implementation, advantages, and how it’s applied across different industries. Whether you’re familiar with the system or just starting out, this article offers valuable insights into how FRACAS can transform your failure management strategies and promote continuous improvement.
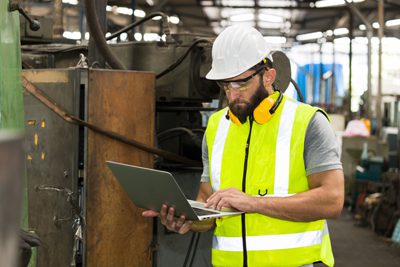
What is FRACAS?
Fracas, which stands for the Failure Reporting, Analysis, and Corrective Action System, is a systematic approach used to identify, analyze, and resolve failures in products, systems, or processes. It involves documenting failures, conducting detailed analysis to determine root causes, and implementing corrective actions to prevent future occurrences.
The Origins and Purpose of FRACAS
Originally developed by the U.S. Department of Defense, FRACAS is widely used in industries like aerospace, manufacturing, and healthcare to enhance reliability, improve performance, and reduce maintenance costs. Its core functions include:
- Documenting and logging details about equipment malfunctions and other reliability concerns.
- Reviewing, assessing, and prioritizing reported failures and issues.
- Determining corrective measures and applying them to prevent similar problems in the future.
- Monitoring reliability and maintainability trends over time for deeper analysis.
- Using failure data and implemented solutions to support ongoing reliability assessments.
When Should FRACAS Be Performed?
FRACAS is typically initiated after a system has been deployed. Once failures start to surface, and you can gather sufficient failure data, meaningful FRACAS analysis can be conducted. Implementing FRACAS offers several advantages for system performance:
- Drives improvements in system reliability.
- Enhances the understanding of how failures affect interconnected systems.
- May uncover hidden or fundamental reliability issues.
- Validates or challenges the original engineering assumptions established through Failure Modes, Effects, and Criticality Analysis (FMECA).
The FRACAS Cycle: A Practical Approach to Managing Failures
The FRACAS cycle is a hands-on process designed to systematically address failures and keep operations running smoothly. Here’s how it works:
Failure Reporting
Start by documenting what went wrong. Capture the basic info—when it happened, which equipment was involved, and the symptoms of the failure. Keeping it straightforward ensures consistency.
Data Gathering
Next, collect all relevant details about the failure. This might include how the equipment was running at the time, any recent maintenance performed, and other key observations. The more context you have, the better.
Analysis
This is where you roll up your sleeves and dive into the real issue. Use methods like Root Cause Analysis (RCA), Pareto charts, or Weibull analysis to thoroughly investigate why the failure happened. The aim is to uncover the true cause, not settle for a surface-level explanation.
Planning Corrective Actions
Once you know the cause, it’s time to create a plan. Develop specific steps to fix the issue, targeting the root cause. This isn’t just about patching things up—it’s about preventing the problem from happening again.
Putting the Plan into Action
With your plan in hand, make the necessary changes—whether it’s adjusting equipment, tweaking processes, or revising procedures. It’s all about making sure the corrective actions are put in place effectively.
Verification
After implementing the fix, test it out. Monitor the situation closely to ensure the solution is doing its job and preventing the same failure from recurring.
Closing the Loop
Once you’re confident the issue is resolved, document everything—the actions you took, the results, and any lessons learned. This step brings closure to the specific incident.
Continuous Learning
Even after resolving the issue, don’t stop there. Regularly review past FRACAS reports to spot trends and uncover ways to improve reliability across the board. This is where real, ongoing improvement happens.
This process isn’t just about solving one-off problems. It’s about using failures as opportunities to build stronger, more reliable systems over time. Good preventive maintenance starts with an accurate asset criticality assessment.
Examples of a FRACAS in maintenance
Here are a few FRACAS examples from the world of maintenance that highlight how to use failure data to improve reliability at your facility:
Root Cause Analysis of Recurring Failures
By analyzing work orders for fault codes and conducting root cause analysis, you discover that equipment frequently fails when old parts are used for repairs. You also notice these faults result in significant production losses. Based on this FRACAS data, you can justify increasing your inventory budget to stock new parts and avoid these costly failures.
Identifying the Impact of Process Changes
An asset that rarely failed before starts experiencing more frequent breakdowns. Through FRACAS analysis, you determine the problems began three months ago when the plant changed product specifications, affecting the machine’s configuration. This insight allows you to develop new procedures for communicating plant changes to reduce downtime across multiple locations.
Prioritizing Maintenance Issues
A failure report for all your work orders identifies three common types of error codes. With limited resources to address only one this quarter, you review your Failure Mode and Effects Analysis (FMEA), cost reports, and Root Cause Analysis (RCA) to determine which error has the biggest impact. This data-driven approach helps you secure a budget to hire more technicians and correct the highest priority issues first.
Improving Maintenance Procedures
FRACAS analysis of a machine’s work history reveals instances of improper assembly leading to misalignment and loose connections. Root cause analysis determines that current bearing defects stem from shaft misalignment caused by inadequate maintenance team training. This leads to assigning properly trained staff for machine alignment and implementing mandatory training on alignment procedures for all team members.
Enhancing Preventive Maintenance
By tracking failure modes over time, you notice certain components are failing before their scheduled replacement in your preventive maintenance program. This FRACAS data allows you to adjust PM schedules and potentially switch to a condition-based maintenance approach for these components.
These examples demonstrate how FRACAS can be used to systematically collect failure data, analyze root causes, implement corrective actions, and continuously improve maintenance practices and equipment reliability.
Implementing FRACAS comes with significant benefits
What are the benefits of implementing FRACAS? It is like asking what the benefits of a smoothly functioning reliability system are. They include:
A decrease in the total cost of ownership/lifecycle costs.
When a production system suffers fewer breakdowns, you can save an extraordinary amount of money. You will spend fewer spares, save on labor costs, and extend the useful life of your equipment.
An increase in asset availability.
Greater operational availability supports increased revenue by creating more capacity for new clients. It also increases product margin by amortizing equipment costs over greater product quantities. In translation, it decreases production cost per unit.
An increase in customer satisfaction.
Improved equipment reliability ensures that planned quantities, quality, and delivery dates are respected, ensuring client satisfaction and retention.
Better regulatory compliance.
Equipment failure threatens employee safety and can lead to environmental non-compliance. Operating in a controlled environment allows for planned shutdowns and stoppages rather than rushed emergency responses to failure.
A reduction in scrap rates and warranty claims. Equipment failures or degradation can produce products that are out of specification or exhibit high failure rates. Improved reliability reduces the impact and occurrence of such events, lowering rework costs and improving client satisfaction.
With that out of the way, it’s time to check how failure reporting, analysis, and corrective action systems look in action. Start improving your system with these tips for effective asset management.
FRACAS: Best Practices for High-Quality Data Collection
Here are some key tips for collecting good data for your FRACAS (Failure Reporting, Analysis, and Corrective Action System) implementation:
Standardize failure reporting forms and processes:
- Create standardized templates for reporting failures.
- Define clear procedures for when and how to report issues.
- Ensure all relevant teams understand and follow the reporting process.
Capture comprehensive failure details:
- Document specifics like date, time, equipment involved, symptoms, and operating conditions.
- Include photos or diagrams where applicable.
- Record environmental factors that may have contributed.
Implement proper data validation:
- Have a process to verify reported failures.
- Cross-check data entries for accuracy and completeness.
- Train staff on proper data entry techniques.
Use appropriate technology:
- Implement CMMS or dedicated FRACAS software.
- Enable real-time data capture when possible.
- Ensure systems can integrate and share data across teams.
Involve cross-functional teams:
- Get input from engineering, maintenance, operations, quality control, etc.
- Encourage collaboration to get multiple perspectives on failures.
Prioritize root cause analysis:
- Don’t just record symptoms, dig into underlying causes.
- Document a thorough analysis of each failure.
Track corrective actions:
- Record what actions were taken to address each failure.
- Follow up to verify the effectiveness of corrective measures.
- Update procedures/processes based on lessons learned.
Analyze trends over time:
- Look at failure patterns across equipment, time periods, conditions, etc.
- Calculate key metrics like MTBF, and MTTR.
- Use statistical tools to identify significant trends.
Maintain data quality:
- Regularly audit and clean data.
- Remove duplicate or erroneous entries.
- Keep historical records for long-term analysis.
Foster a culture of reporting:
- Encourage staff to report all issues, not just major failures.
- Emphasize learning, not blame.
- Provide feedback on how reported data is being used.
Steps for implementing FRACAS in your business
The following steps provide a roadmap for implementing a FRACAS methodology.
Remember, you must customize the final system to your industry, equipment, and way of working. Copying the system of another business will be sub-optimal and possibly doomed to fail.
1. Select a team and define your goals
A FRACAS system is at the core of your reliability program. However, this doesn’t mean that having technical personnel is enough.
Ideally, you will be able to pull people from the following departments:
- Maintenance and reliability engineers for obvious reasons.
- Someone from the quality department to help structure the methodology and align it to the company standards.
- Someone from the warehouse, as FRACAS, will inevitably impact them, and you’ll need their buy-in and support.
<li”>The equipment operators will be key to making your new system work, so possibly include someone from production.
- Senior management should also be involved to help clear the inevitable roadblocks and make judgment calls on strategy.
As a team, spend time aligning and agreeing on the goals for the new system. It’s easy to become sidetracked by data collection. Keep in mind that your role, and that of the system you devise, is to improve reliability. Agree on and document what you hope to achieve.
2. Choose your software management system
While you can run a FRACAS system manually, it makes no sense in this day of technology. You will want to use a CMMS or EAM. Both allow real-time data collection, analysis, and reporting and provide a readily accessible archive of in-service history.
Designing and building your FRACAS workflow with the management system in mind is an efficient way to integrate your data capture, storage, and analysis requirements.
3. Decide what data you will collect
Avoid becoming bogged down in too much data. Use the information that enables making decisions and taking action. Your data may include failure modes and mechanisms, historical data, reliability information, MTBF, or mean time to failure (MTTF). You’ll certainly need product specifications. If you already use CMMS, much of what you need will be at your fingertips.
To ensure a rigorous and auditable process, create a table showing what data you need to collect and why. Identify how it will be collected and the tools you’ll use to analyze it.
When you first implement a FRACAS, start small. Your data may be as simple as the number of failures by component, system, or area.
4. Create standardized failure codes
A core principle of FRACAS is using a standardized taxonomy for failures for easier analysis. How would you sort and sift to aggregate the data if everyone wrote long-hand faults?
The aviation world does this well with its ATA codes which describe every system and subsystem on an aircraft and then extend to zones. For example, when using this system to search for failures in the landing gear steering, you’ll use 32-50 as the search criteria. The landing gear is ATA chapter 32, while the steering subsystem is 50.
Devise similar codes to suit your organizational context. All employees can use them to report failures and rectification efforts. You can even apply standard codes to failure modes for greater specificity.
Your CMMS is an excellent tool for enforcing this discipline by preventing the entry of any codes that do not adhere to the approved structure.
5. Define organizational roles and a RACI chart
Defining clear role responsibilities in new initiatives is crucial. Create a RACI chart with FRACAS tasks listed down the Y-axis and relevant roles along the X-axis.
A RACI chart is a project management tool used to clarify roles and responsibilities for tasks, milestones, and deliverables within a project. The acronym RACI stands for:
Responsible: The individual who executes the work required to complete a task.
Accountable: The person who has the final say and ultimate responsibility for ensuring the task is completed.
Consulted: Those whose expertise is sought during the task’s execution; they provide valuable input and advice.
Informed: Individuals who need to be kept in the loop about the task’s progress and outcomes, typically receiving updates once the task is finished.
At each intersection of a task and a role, decide whether that role is responsible for executing the task (R), accountable for its execution (A), consulted with (C), or simply informed (I). If the role has no involvement, place a horizontal line (-).
By using this chart, everyone can see who collects data, who does the analysis, and who is responsible for implementing corrective actions.
6. Develop the FRACAS policy, procedures, and process map
For those who dislike administration, this will be the least enjoyable part of the process. Unfortunately, this step is vital to ensure everyone is clear on what FRACAS is, why it is used, and how the system works.
Your FRACAS policy should include:
- The organizational roles
- A RACI chart that features key data required, the report formats, and the training each role should receive
- A process map that outlines the required steps and procedures.
7. Deploy the FRACAS
Distribute the policies and procedures manual and begin training the involved personnel while holding information sessions to update all employees on the new system. Data collection and analysis can commence.
8. Analyze received data
In the analysis phase, you will use your preferred tools. However, the intent is to reach the root cause of the failure to inform corrective actions. The data can be sorted into predominant failures using basic Pareto analysis, with common failure causes identified using Weibull analysis.
Standard root cause analysis techniques like Five Whys, Fish-bone Analysis, or an Ishikawa diagram can help drill down to actionable causes.
9. Generate corrective actions
Actions used to address failures can take many forms. You may work with a supplier or an OEM to modify equipment, change operating processes, or use alternative components to prevent future failures. There might be inspection tasks, condition monitoring, or life limits on components that reduce the impact of future problems.
Regardless, during the generation of corrective actions, it is important to remain focused on preventing the analyzed failure, achieving business goals, and not creating consequential impacts that shift the problem elsewhere.
10. Use KPIs to track FRACAS effectiveness
FRACAS is a closed-loop system that works on the principles of continuous improvement. The only way to close the loop after implementing corrective actions is to monitor the effectiveness of the outcomes.
Action monitoring aside, it is also wise to implement KPIs to monitor if the FRACAS system is being used and if corrective actions are properly implemented. Try to develop a few indicators that you can roll into a dashboard, providing a summary of the health and effectiveness of your FRACAS system.
Benefits of Implementing FRACAS
Implementing FRACAS (Failure Reporting, Analysis, and Corrective Action System) can provide significant benefits to an organization. Based on the search results, here are some of the key benefits of implementing FRACAS:
Decreased Total Cost of Ownership/Lifecycle Costs:
- Fewer breakdowns in production systems lead to cost savings.
- Reduced expenditure on spare parts.
- Decreased labor costs for repairs and maintenance.
- The extended useful life of equipment.
Increased Asset Availability:
- Improved operational availability creates more capacity for new clients.
- Allows for amortization of equipment costs over larger product quantities.
- Decreases production cost per unit.
Increased Customer Satisfaction:
- Improved equipment reliability ensures planned quantities, quality, and delivery dates are met.
- Enhances customer confidence and loyalty.
- Contributes to increased client retention.
Better Regulatory Compliance:
- Allows for planned shutdowns and stoppages rather than emergency responses.
- Mitigates safety hazards and reduces the potential for environmental violations.
Reduction in Scrap Rates and Warranty Claims:
- Improved reliability reduces the occurrence of out-of-specification products.
- Lowers rework costs and improves product quality.
Improved Reliability:
- Systematic addressing of failures enhances overall system reliability.
- Promotes a culture of continuous improvement.
Data-Driven Decision Making:
- Provides valuable insights into asset performance.
- Enables more informed decision-making for resource allocation and risk management.
Risk Reduction:
- Helps identify and address potential failures proactively.
These benefits demonstrate that FRACAS can have a significant positive impact on an organization’s operations, costs, customer relations, and overall performance. By providing a structured approach to failure management and continuous improvement, FRACAS enables companies to learn from past issues, prevent future failures, and ultimately deliver higher-quality products and services.
How a CMMS Helps with FRACAS
Implementing new processes can be challenging, especially when you have established ways to do things in your facility. Learn how our work order software streamlines maintenance requests and tracks task progress in real time. The good thing is that, in this case, software can make things much easier for you. Let’s look at some ways how.
Facilitates Reporting
A CMMS simplifies failure reporting by setting up a consistent reporting framework. You can customize the app to prompt users with specific questions and required details, ensuring that all failure data is collected uniformly. This standardized approach helps factory workers follow a clear process, making it easier to integrate reporting into your FRACAS system from the start.
Streamlined Reporting
A CMMS (Computerized Maintenance Management System) can simplify failure reporting by establishing a consistent format. You can set up the system to prompt factory workers with specific questions and required details for each failure report. This ensures that everyone follows a uniform approach when documenting issues, which is crucial for a successful FRACAS (Failure Reporting, Analysis, and Corrective Action System) implementation.
Efficient Work Order Management
Once a failure is reported, the next step is assigning tasks to maintenance personnel. A robust CMMS allows you to create and distribute digital work orders easily. Workers get instant notifications on their mobile devices, complete with all relevant failure details, ensuring they have the information they need to address the issue promptly.
Enhanced Data Analysis
Analyzing failure data is a critical component of FRACAS. A good CMMS not only tracks your failure reports and corrective actions but also enhances root cause analysis. This helps pinpoint the underlying issues causing equipment problems. By regularly analyzing this data, you can refine your corrective measures and monitor their effectiveness over time. Tools like eWorkOrders offer advanced reporting modules that provide actionable insights from your data, supporting continuous improvement.
In essence, leveraging a CMMS can make the process of adopting new practices smoother and more efficient, turning potential challenges into opportunities for better management and optimization.
Conclusion
Implementing a robust FRACAS system is crucial for organizations seeking to enhance reliability, reduce costs, and improve overall performance. By systematically addressing failures and promoting continuous improvement, companies can significantly benefit from decreased lifecycle costs, increased asset availability, and improved customer satisfaction.
To maximize the effectiveness of FRACAS, integrating it with a powerful Computerized Maintenance Management System (CMMS) like eWorkOrders is essential. eWorkOrders CMMS provides the necessary tools to streamline failure reporting, manage work orders efficiently, and conduct in-depth data analysis. With its user-friendly interface and advanced features, eWorkOrders can help organizations standardize their reporting processes, facilitate quick responses to failures, and generate valuable insights for informed decision-making. By leveraging eWorkOrders CMMS in conjunction with FRACAS, businesses can create a comprehensive reliability management system that drives continuous improvement and operational excellence.