A major power and energy plant operator, with facilities supporting both fossil fuel and renewable generation across North America, approached us looking for a power plant maintenance software solution that could scale with their operations. They faced strict regulatory demands, complex asset networks, and 24/7 operations requiring high uptime and complete maintenance visibility.
Previously reliant on spreadsheets, email, and disconnected legacy systems, they struggled to manage preventive maintenance, inspections, technician workloads, and asset reliability across multiple generation sites. They needed a modern CMMS for energy facilities that could centralize operations, automate processes, and improve safety and compliance across all plants.
We worked closely with Sam, the Maintenance & Reliability Director, who manages teams across coal, hydroelectric, and solar power stations. Below, Sam shares how implementing eWorkOrders CMMS transformed their plant maintenance and compliance tracking processes.
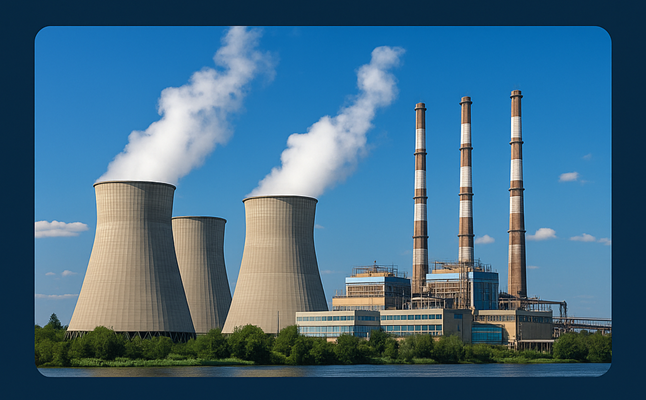
Business Challenge
We operate in a high-stakes environment—where any equipment failure or compliance issue could lead to safety risks or regulatory penalties. With a growing portfolio of power plants, our decentralized maintenance approach became a liability.
We routinely missed preventive maintenance tasks, had no standard process for logging inspections, and found it hard to track critical systems like turbines, boilers, transformers, and switchgear. When an audit came around, preparing documentation was time-consuming and stressful.
Technicians were frustrated with manual work orders and limited visibility into asset history. Spare parts were tracked inconsistently, causing delays and unnecessary purchases. Leadership had no real-time insight into performance KPIs or maintenance costs.
We needed a centralized, cloud-based energy maintenance management software platform to unify work order tracking, preventive maintenance, spare parts inventory, labor hours, and compliance—all while being intuitive enough for plant teams to adopt quickly.
Energy Facility Maintenance Management Software Solution
After evaluating several CMMS options tailored to utilities and energy production, we selected eWorkOrders CMMS for power plants because of its user-friendly interface, mobile functionality, customizable workflows, and outstanding customer support.
Our teams now rely on eWorkOrders to:
- Track and schedule preventive maintenance on critical systems like turbines, pumps, and backup generators.
- Manage technician work orders across multiple generation sites in real time.
- Automate spare parts inventory management with reorder alerts and location-based stock tracking.
- Generate audit-ready maintenance logs and compliance reports in seconds.
- Gain real-time visibility into labor performance, asset reliability, and energy plant KPIs via custom dashboards.
Technicians access and close work orders from their mobile devices, attach equipment photos, and log parts usage instantly. This real-time data improves accountability and reduces administrative overhead. Our compliance audits—previously weeks of preparation—now take hours, with every inspection and maintenance record easily accessible.
Implementation
Implementation was seamless. Our dedicated Account Manager supported us from planning through go-live. Data migration included thousands of assets, equipment categories, historical maintenance records, and technician schedules—all handled smoothly.
Training was tailored to each facility, and even our most experienced plant engineers found the system easy to use. We went live across all our energy facilities in under two months, with minimal disruption to operations.
Customization capabilities let us align the software with our internal processes—from automated escalations to location-based permissions and detailed compliance workflows.
Energy Plant Compliance & Safety With CMMS
Regulatory compliance is a constant in our industry. With eWorkOrders, we track equipment inspections, calibration schedules, and safety certifications in one system. The platform supports compliance with OSHA, EPA, and NERC standards, and simplifies readiness for internal and third-party audits.
Every work order includes a digital trail—who performed the task, when, what was done, and which parts were used. This transparency protects us from fines, reduces legal exposure, and gives our leadership peace of mind.
Results From Using Our Power Plant Maintenance Software
With eWorkOrders, we now efficiently manage work orders across all our generation sites and keep track of parts and consumables with automated replenishment. Our team maintains comprehensive asset histories, including detailed records of labor and downtime events.
Since implementing the software, we have significantly reduced unplanned outages and emergency repairs, while optimizing technician scheduling. This has led to substantial savings in downtime, labor hours, and inventory waste.
The ability to generate real-time compliance and cost reports has also empowered our executive team to make more informed decisions, enabling smarter investments in equipment upgrades and energy initiatives..
Summary
Implementing eWorkOrders CMMS has transformed our energy plant maintenance strategy. We’ve moved from reactive repairs to proactive reliability. Our technicians are more productive, our audits are faster, and our equipment is more dependable.
If you’re managing power plants, utilities, or energy infrastructure, eWorkOrders is a must-have solution. It’s not just a tool—it’s a foundation for safe, efficient, and compliant operations.
The following case study is a composite scenario based on typical customer experiences with eWorkOrders CMMS.