In today’s fast-paced business world, staying competitive requires a solid maintenance strategy. Two popular approaches — preventive maintenance and predictive maintenance — are often at the forefront of discussions. Each offers distinct ways to keep equipment running smoothly and minimize downtime. This guide will walk you through the ins and outs of both strategies, highlighting their strengths, challenges, and practical applications. By the end, you’ll have the insights needed to choose the right approach for your business in the Preventive vs Predictive Maintenance debate, potentially saving time, money, and resources in the process.
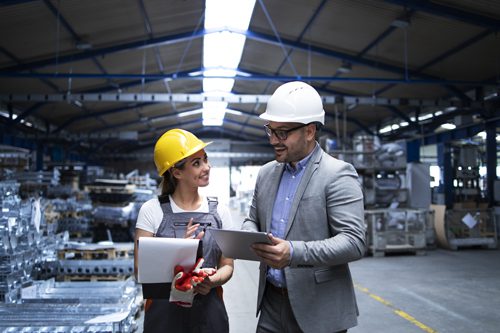
Understanding Preventive Maintenance: The Proactive Approach
Preventive maintenance, sometimes called preventative maintenance, is all about taking proactive steps to keep your equipment in top shape. This approach involves conducting regular, scheduled maintenance tasks designed to avoid unexpected breakdowns and prolong the lifespan of your assets.
For many years, preventive maintenance has been a trusted practice across various industries, providing a consistent and organized method for caring for machinery and equipment. By focusing on maintenance before problems arise, businesses can run more smoothly, minimize downtime, and create a more reliable work environment. In essence, it’s a smart way to invest in the health of your operations.
Key Characteristics of Preventive MaintenanceRegular Schedule
Maintenance tasks are performed at fixed intervals, regardless of the current condition of the equipment.
Proactive Measures
Actions are taken to prevent failures before they occur, reducing the likelihood of unexpected breakdowns.
Simplicity
Generally simpler to implement than predictive maintenance, making it accessible to a wide range of organizations.
Benefits of Preventive Maintenance
Reduced Unexpected Breakdowns
By addressing potential issues early, preventive maintenance significantly decreases the chances of sudden equipment failures.
Extended Equipment Lifespan
Consistent care and attention prolong the useful life of assets, maximizing your return on investment.
Improved Safety
Well-maintained equipment is less likely to malfunction, enhancing workplace safety and reducing the risk of accidents.
Increased Reliability
Regular upkeep ensures equipment performs consistently, leading to improved production quality and efficiency.
Better Resource Planning
With a set maintenance schedule, organizations can better plan for downtime and allocate resources effectively.
Limitations of Preventive Maintenance
Increased Downtime
Equipment must be stopped for scheduled maintenance, which can lead to production interruptions.
Potential Overservicing
Maintenance may be performed when not strictly necessary, leading to wasted resources and potential wear on components.
Higher Initial Costs
Regular maintenance can be costly due to frequent inspections and repairs, especially in the early stages of implementation.
Exploring Predictive Maintenance: The Data-Driven Revolution
Predictive maintenance is changing the landscape of how we handle machinery upkeep. This approach moves away from traditional maintenance strategies by employing data analytics and real-time monitoring to anticipate equipment failures before they occur. Rather than relying solely on scheduled inspections, predictive maintenance enables teams to act at just the right moment, addressing potential issues before they escalate.
With this proactive approach, businesses can significantly reduce unexpected downtime and improve operational efficiency. By analyzing data trends and equipment performance, organizations can pinpoint when maintenance is necessary, leading to smarter resource allocation and less disruption to workflow.
As we continue to embrace technological advancements, predictive maintenance stands out as a forward-thinking strategy that not only enhances asset reliability but also supports long-term cost savings. It’s about ensuring that your equipment is not just running but thriving when you need it the most.
Key Characteristics of Predictive Maintenance
Condition-Based Maintenance
This approach focuses on performing maintenance tasks according to the actual state of the equipment, rather than relying on a fixed schedule.
Continuous Monitoring
Equipment is consistently observed through the use of sensors and Internet of Things (IoT) devices to anticipate possible failures before they occur.
Analytics-Driven
This strategy employs sophisticated analytics, machine learning, and artificial intelligence to analyze equipment data and generate precise forecasts about maintenance needs.
Benefits of Predictive Maintenance
Minimized Downtime
By forecasting potential failures ahead of time, maintenance activities can often be carried out without halting equipment operations, significantly reducing disruptions to production.
Cost Efficiency
This approach eliminates the need for unnecessary maintenance tasks, leading to lower overall costs and better utilization of resources.
Targeted Resource Allocation
Maintenance efforts are directed to areas where they are most required, ensuring that both labor and materials are used effectively.
Boosted Asset Performance
Tackling issues before they escalate contributes to improved equipment efficiency and higher productivity levels.
Informed Decision-Making
The insights gained from monitoring equipment performance empower teams to make data-driven decisions regarding maintenance strategies and asset management.
Limitations of Predictive Maintenance
Higher Initial Investment
Requires advanced monitoring tools, sensors, and data analysis capabilities, which can be costly to implement
Complexity
More complex to implement and requires specialized skills in data analysis and interpretation.
Data Dependency
This relies heavily on accurate data collection and interpretation, which can be challenging in some environments.
Between Preventive vs Predictive Maintenance – Key Differences
Although preventive and predictive maintenance both strive to minimize downtime and extend equipment lifespan, they utilize distinctly different methods. Let’s explore the main differences between them:
Aspect | Preventive Maintenance | Predictive Maintenance |
---|---|---|
Timing | Scheduled at regular intervals | Based on real-time data and equipment conditions |
Technology Requirements | Minimal technology (manual checks and basic monitoring) | Requires advanced sensors, IoT, and data analytics |
Downtown Prevention | Reduces the risk of unplanned downtime through regular checks | Minimizes downtime by anticipating problems before they occur |
Approach | Proactive maintenance | Data-driven approach |
Conclusion
Choosing between preventive and predictive maintenance depends on your organization’s unique needs, resources, and goals. Preventive maintenance offers a reliable, structured approach for maintaining equipment, while predictive maintenance utilizes data-driven insights to optimize maintenance strategies. Ultimately, the most effective strategy may involve a combination of both approaches, allowingbusinesses to capitalize on the strengths of each to achieve operational excellence.
A Computerized Maintenance Management System (CMMS) like eWorkOrders can help streamline both preventive and predictive maintenance strategies, providing the tools necessary to monitor, track, and manage your maintenance tasks efficiently.