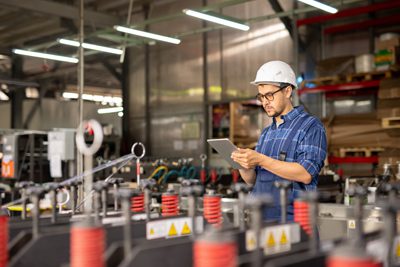
The Impact of Maintenance on Manufacturing Efficiency
Well-maintained equipment produces higher quality outputs. When machines operate at peak performance, they’re less likely to create defects or inconsistencies in products. This not only reduces waste but also enhances customer satisfaction and brand reputation.
Enhanced Safety
Proper maintenance is crucial for workplace safety. Faulty equipment can pose serious risks to operators and other personnel. By keeping machinery in top condition, manufacturers can significantly reduce the likelihood of accidents and injuries.
Cost Savings
While maintenance requires an upfront investment, it leads to substantial cost savings in the long run. Preventing major breakdowns avoids expensive repairs and replacements. Additionally, well-maintained equipment operates more efficiently, consuming less energy and resources.
Increased Operational Efficiency
Regularly serviced machines operate at optimal speeds and capacities. This translates to higher production rates and improved overall equipment effectiveness (OEE), a key metric in manufacturing efficiency.
Best Practices for Maintaining Manufacturing Equipment
Implement a Preventive Maintenance Schedule
Develop a comprehensive preventive maintenance plan based on manufacturer recommendations and historical data. This should include regular inspections, cleaning, lubrication, and parts replacement. Our preventive vs predictive guide explains cost and scheduling differences.
Utilize Predictive Maintenance Technologies
Leverage sensors and data analytics to predict when equipment is likely to fail. This allows for more targeted and timely maintenance interventions.
Train Operators in Basic Maintenance
Give your machine operators the know-how to take care of simple maintenance tasks. This helps them catch problems early and keeps your maintenance team from getting overloaded with smaller issues.
Keep Detailed Maintenance Records
Keep comprehensive maintenance records by documenting every repair, part replacement, and performance detail. This valuable data helps spot trends and fine-tune your maintenance strategies for better efficiency and equipment longevity.
Invest in Quality Parts and Tools
Using high-quality replacement parts and maintenance tools may cost more initially but pays off in terms of equipment longevity and reliability. Discover evolving trends in work order systems and industry standards.
High-Maintenance Equipment in Manufacturing
Some types of manufacturing equipment require more frequent and intensive maintenance:
- CNC Machines: Require regular calibration and lubrication to maintain precision.
- Industrial Robots: Need frequent software updates and mechanical checks.
- Conveyor Systems: Demand consistent cleaning and belt tension adjustments.
- Hydraulic Presses: Require regular fluid checks and seal replacements.
- Injection Molding Machines: Need frequent nozzle cleaning and barrel maintenance.
Implementing a Computerized Maintenance Management System (CMMS)
The Role of Reliability-Centered Maintenance (RCM)
The Importance of Reliability-Centered Maintenance (RCM)
Conclusion: Investing in Maintenance for Long-Term Success
In conclusion, staying competitive in manufacturing requires more than just reacting to equipment issues—it demands a proactive maintenance strategy. By investing in robust programs, cutting-edge technologies like eWorkOrders CMMS, and continuous operator training, manufacturers can significantly boost efficiency, reduce costs, and ensure high-quality production. A well-maintained facility is a strong foundation for success, leading to reduced downtime, improved safety, and sustained long-term growth. Now is the time to assess your maintenance approach and implement these strategies for a stronger, more productive operation. Your future success depends on it.