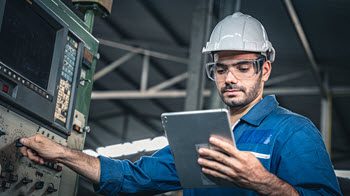
Industrial electrical equipment is the backbone of many manufacturing and production processes. Ensuring its optimal performance is crucial for maintaining productivity and preventing costly downtime. However, like any machinery, electrical equipment can exhibit signs of wear and potential failure. Recognizing these signs early can help in implementing timely maintenance strategies, often facilitated by a computerized maintenance management system (CMMS), to ensure continuous operation and safety.
Key Indicators Your Industrial Electrical Equipment Requires Attention
Overheating
Overheating often signals that electrical equipment is failing. This issue can arise from various factors such as circuit overloads, inadequate ventilation, or faulty cooling systems. Key indicators of overheating include:
- Surfaces of equipment that feel unusually hot
- The presence of melted insulation or a burning odor
- Discoloration of components caused by excessive heat
It’s crucial to address overheating issues promptly to extend the equipment’s lifespan and minimize fire risks.
Unusual Noises
When electrical equipment produces unusual or loud sounds, it may signal underlying issues like loose connections, degraded components, or mechanical failures. Common noises to be aware of include:
- Grinding or rattling
- Humming or buzzing
Promptly investigating and resolving these noises is crucial to prevent additional damage and ensure the equipment’s safe operation.
Frequent Tripping of Circuit Breakers
If circuit breakers frequently trip or fuses blow, it may signal issues like short circuits, overloading, or faulty components. This can lead to significant downtime and potential damage to other connected devices. Regular inspections and maintenance can help identify and rectify these issues before they escalate.
Vibration and Mechanical Imbalances
Excessive vibrations in electrical equipment can be caused by mechanical imbalances, loose connections, or worn-out components. These vibrations can accelerate wear and tear, leading to premature equipment failure. Regular inspections should include checks for unusual vibrations and their sources.
Fluctuations in Voltage or Frequency
Voltage or frequency fluctuations can disrupt normal power supply, causing equipment malfunctions and performance issues. These fluctuations might indicate failures within the electrical system and should be monitored closely to facilitate timely corrective actions.
Insulation Breakdown
Insulation breakdown is a serious issue that can lead to electrical failures and pose safety risks. Signs include:
- Arcing or sparking
- Visual damage to insulators
Timely inspection and maintenance of insulation systems can prevent these issues from escalating, ensuring the integrity of the equipment.
Visible Damage and Corrosion
Visible damage such as cracks, rust, or corrosion on equipment components can weaken their structural integrity and lead to failures. Regular cleaning and inspection can help identify early signs of corrosion, allowing for appropriate remedial actions.
Flickering or Dim Lights
Lights that flicker or dim may indicate underlying electrical issues such as loose connections, circuit overloads, or failing components. It’s crucial to address these symptoms promptly to avoid more significant electrical complications.
Burning Smell
A burning odor coming from electrical equipment usually suggests overheating or an electrical fault. This could be due to melting insulation or a short circuit. Immediate action is necessary to investigate and mitigate potential fire hazards.
Performance Decline
When electrical equipment shows signs of reduced efficiency, it often points to internal problems like worn-out bearings, misalignment issues, or deteriorated insulation. Regular upkeep, including lubrication and alignment adjustments, is crucial for maintaining optimal performance.
CMMS for Effective Maintenance
Using a CMMS (Computerized Maintenance Management System) can greatly streamline maintenance for industrial electrical equipment. It centralizes maintenance records, plans routine inspections, tracks service requests, and automates preventive maintenance tasks, leading to less equipment downtime, improved efficiency, and longer asset life.
Conclusion
Recognizing the signs that your industrial electrical equipment requires attention is crucial for maintaining operational efficiency and safety. By implementing regular maintenance checks and utilizing a CMMS,, such as eWorkOrders, you can ensure that potential issues are addressed promptly, minimizing the risk of unexpected failures and costly repairs. Prioritizing these maintenance strategies not only safeguards your equipment but also enhances the overall reliability and productivity of your industrial operations.