Creating a preventive maintenance program is essential for ensuring the longevity and efficiency of your equipment and facilities. Here are some effective tips to help you establish an effective preventive maintenance program:
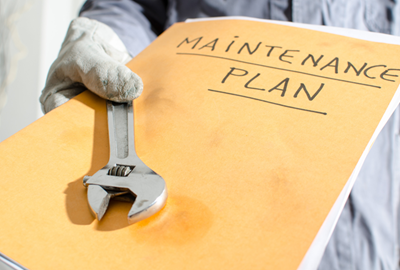
1. Inventory Assets
- Compile a comprehensive list of all assets that require maintenance.
- Record details such as make, model, serial number, specifications, and location.
2. Determine Priorities
- Conduct a criticality analysis to rank assets based on their importance to operations, cost of repair, and likelihood of failure.
- Focus on assets that are critical to production, have high repair costs, or require regular maintenance.
3. Set Maintenance Goals
- Align your preventive maintenance goals with the overall objectives of your organization.
- Define clear, measurable goals such as reducing downtime, extending asset life, and improving safety.
4. Develop Maintenance Schedules
- Design a maintenance timeline that incorporates manufacturer guidelines, past maintenance records, and the criticality of each asset.
- Implement a mix of calendar-based and usage-based indicators to establish optimal maintenance intervals.
5. Create Maintenance Procedures
- Develop detailed maintenance procedures for each asset, including step-by-step instructions, required tools, and safety precautions.
- Ensure procedures are standardized and easily accessible to maintenance staff.
6. Implement a CMMS
- Utilize a Computerized Maintenance Management System (CMMS) to automate scheduling, track work orders, and maintain records.<
- Ensure the CMMS is user-friendly and provides real-time data on maintenance activities.
7. Train Maintenance Staff
- Deliver thorough training sessions for maintenance personnel on utilizing the CMMS and executing specific maintenance tasks.
- Provide continuous education to ensure staff stay current with emerging technologies and industry best practices.
8. Monitor and Adjust
- Regularly review maintenance activities and performance metrics to identify areas for improvement.
- Adjust maintenance schedules and procedures based on feedback and data analysis.
9. Document and Record
- >Maintain meticulous documentation of all maintenance activities, including work orders, inspections, repairs, and parts utilized.
- Leverage these records to monitor asset performance, spot trends, and identify recurring issues.
10.Evaluate and Improve
- Periodically evaluate the effectiveness of your preventive maintenance program.
- Use key performance indicators (KPIs) such as Mean Time Between Failures (MTBF) and Mean Time to Repair (MTTR) to measure success.
- Continuously seek ways to improve the program based on data and feedback.
Maximizing Maintenance Effectiveness with eWorkOrders
Implementing a preventive maintenance program is a strategic investment that pays dividends in equipment reliability, operational efficiency, and cost savings. While the tips outlined provide a solid foundation, the key to success lies in consistent execution and continuous improvement. By leveraging advanced CMMS solutions like eWorkOrders, organizations can transform maintenance from a reactive necessity to a proactive driver of business performance. eWorkOrders’ robust features enable real-time monitoring, data-driven decision-making, and streamlined workflows, empowering maintenance teams to anticipate issues before they arise. As industries evolve and equipment complexity increases, those who embrace comprehensive preventive maintenance strategies supported by cutting-edge technology will be best positioned to thrive in an increasingly competitive landscape.