In the dynamic world of manufacturing, where precision intertwines with productivity, packaging machines emerge as unsung heroes, ensuring products reach consumers in impeccable condition. Amidst the seamless packaging process, the often overlooked linchpin is maintenance. A meticulously maintained packaging machine is instrumental in preserving efficiency and also extends its lifespan significantly, resulting in improved operational performance and cost savings.
Within the diverse realm of packaging checklists tailored to distinct needs, this guide provides a curated set of tasks to enhance your existing checklist. These tasks serve to fortify your maintenance strategy, establishing a robust foundation for consistent, peak performance from your packaging machines.
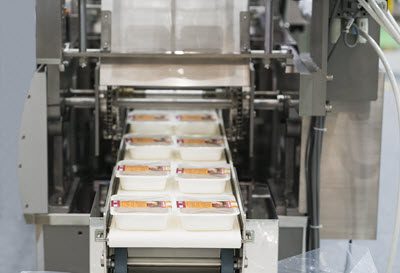
Types of Checklists
Manufacturing checklists are critical tools for ensuring quality, efficiency, and safety in the production process. Here are some types of manufacturing checklists commonly used in the industry:
- Quality Control Checklists
- Process Validation Checklists
- Equipment Maintenance Checklists
- Safety Inspection Checklists
- Standard Operating Procedure (SOP) Checklists
- And the list goes on.
The Importance of Maintenance
Preventing Downtime
Downtime can be a costly affair in the manufacturing industry. Regular maintenance helps identify and address potential issues before they escalate, reducing unexpected breakdowns and production halts.
Optimizing Performance
Packaging machines, with their intricate components, require precise calibration. Routine maintenance ensures that all moving parts, belts, and motors operate as intended, maintaining the machine’s optimal performance.
Ensuring Product Quality
A well-maintained packaging machine contributes to consistent product quality. Any malfunction in the machine can lead to packaging defects, compromising the integrity of the product.
Safety First
Safety is paramount in any manufacturing environment. Regular checks on safety features such as emergency stops, sensors, and guards help create a secure working environment for operators.
Cost Savings
While it might seem counterintuitive, investing in regular maintenance is a cost-effective strategy. It’s more economical to prevent issues through scheduled upkeep than to deal with the aftermath of a major breakdown.
Maintenance Checklist for Packaging Machines
Inspect Moving Parts
Regularly check belts, chains, and gears for signs of wear. Replace any components that show excessive wear or are nearing the end of their lifespan.
Lubrication
Proper lubrication is essential for reducing friction and preventing premature wear. Follow the manufacturer’s guidelines for lubrication intervals and use the recommended lubricants.
Check Sensors and Controls
Ensure all sensors and control systems are functioning correctly. Calibrate sensors to maintain accuracy in measuring and dispensing materials.
Inspect Seals and Gaskets
Leaks can lead to product contamination and damage to the machine. Regularly inspect seals and gaskets for any signs of wear, and replace them as needed.
Cleanliness is Key
Keep the machine clean from dust, debris, and product residue. Regularly clean conveyors, hoppers, and product contact surfaces to prevent contamination.
Electrical Components
Check electrical connections, wiring, and components. Tighten loose connections, replace damaged wiring, and ensure that electrical systems are up to code.
Perform Alignment Checks
Misalignment can lead to uneven wear and reduced efficiency. Check for proper alignment of belts, gears, and other moving parts.
Test Safety Features
Regularly test emergency stops, interlocks, and other safety features. Ensure that operators are trained to use these features effectively.
Review Software and Programming
For automated packaging machines, review and update software regularly. Ensure that the programming aligns with current production needs.
Schedule Professional Inspections
While regular in-house checks are crucial, consider scheduling professional inspections at regular intervals. Experienced technicians can identify issues that might go unnoticed during routine checks.
Tips for Prolonging the Performance of Packaging Equipment
Regular Maintenance Schedule
Establish a routine maintenance schedule for your packaging machines. Regular inspections and preventive maintenance can identify potential issues before they escalate.
Follow Manufacturer Guidelines
Adhere to the manufacturer’s recommended maintenance procedures and guidelines. This ensures that you’re maintaining the machines according to the specifications outlined by the people who designed them.
Train Operators
Train machine operators on proper usage and handling of the equipment. Mishandling can lead to premature wear and tear.
Monitor and Record Performance
Implement a system to monitor the performance of your packaging machines. Keep records of key performance indicators and any deviations from normal operation.
Replace Worn Parts Promptly
Regularly inspect machine components, and replace any worn or damaged parts promptly. Delaying replacements can lead to more significant issues.
Calibration Checks
Calibrate sensors and measuring devices regularly to ensure accuracy in the packaging process. Inaccuracies can lead to packaging defects and waste.
Invest in Quality Tools and Materials
Use high-quality packaging materials and tools. Investing in reliable materials can reduce strain on the machines and contribute to longer lifespans.
Temperature and Humidity Control
Maintain suitable temperature and humidity levels in the packaging area. Extreme conditions can affect the performance of machinery.
Implement Predictive Maintenance
Utilize predictive maintenance technologies to foresee potential issues. This can involve monitoring equipment using sensors and data analytics to predict when maintenance is needed.
Create a Contingency Plan
Develop a contingency plan for unexpected breakdowns. Having spare parts on hand and a plan for rapid repairs can minimize downtime.
Regularly Update Software and Controls
If your packaging machines use software or control systems, ensure that they are regularly updated. Outdated software can lead to inefficiencies and compatibility issues.
Employee Engagement
Encourage employees to report any irregularities or unusual sounds in the machines promptly. Early detection can prevent major breakdowns.
Consider Professional Audits
Periodically bring in professionals for audits and inspections. External perspectives can uncover issues that might be overlooked internally.
Embrace Maintenance Management Software
Implementing a robust Computerized Maintenance Management System (CMMS) can revolutionize your packaging machine maintenance. CMMS provides a centralized platform for scheduling, tracking, and managing maintenance tasks. It helps automate work orders, track equipment history, and provide real-time insights into the health of your machines. By leveraging CMMS, you can enhance preventive maintenance, promptly address issues, and optimize the overall lifespan of your packaging machines. Consider solutions like eWorkOrders CMMS for efficient maintenance tracking and streamlined operations.
Conclusion
The proactive approach of regular maintenance is a small investment that pays significant dividends in the longevity and performance of packaging machines. By following a comprehensive checklist and adopting a culture of preventive maintenance, manufacturers can ensure their packaging processes remain efficient, reliable, and cost-effective.
See What Our Customers Are Saying
Additional Resources
Disclaimer: The guidelines here offer a foundational framework for packaging machine management. Keep in mind that specific requirements may vary based on your machine’s type and model. Consult with your machine’s manufacturer or a professional for tailored advice aligned with your equipment’s specifications. Adhering to manufacturer-recommended procedures enhances reliability. This checklist isn’t exhaustive; users are encouraged to customize it. Consider tools like eWorkOrders CMMS for efficient management. Note that reliance on this checklist is at your own risk, and we disclaim liability for errors. Prioritize safety and compliance by seeking professional advice.
Note: The recommendations provided in this checklist offer general recommendations for tools management. It is important to note that the list below contains suggested considerations that you should consider when creating your own checklist.