Efficiency and reliability in manufacturing hinge on one fundamental principle: proper maintenance. Imagine the impact of a CNC machine breakdown on productivity and deadlines. That’s where the significance of meticulous machine maintenance comes into play. Preventing machine downtime isn’t just about avoiding inconvenience; it’s about safeguarding profitability, customer trust, and operational reputation. With intricate technology and precise operations, CNC machines demand regular attention to ensure optimal performance.
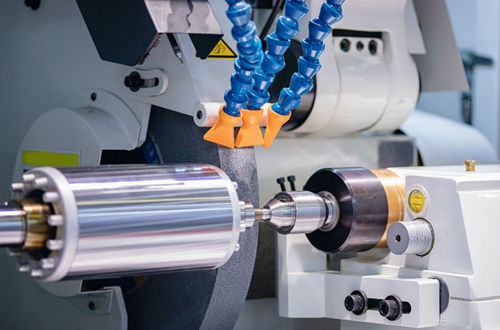
Mastering CNC Machine Maintenance: What You Should Know
Precision is the heartbeat of CNC machines, capable of achieving hair-thin accuracy (within 0.0001 inches). The key to unlocking this precision lies in a practice that is both essential and deceptively simple: maintenance. In the realm of CNC machining, where precision is paramount and errors come with a high price tag, understanding the core maintenance tasks is not just practical but imperative
Coolant Management
CNC machines rely on proper coolant levels and concentration to dissipate the heat generated by swift tool movements, ensuring the integrity of workpieces and tools.
Efficient Cooling
Spindles racing at speeds over 10,000 RPM demand efficient cooling to fend off thermal challenges. Temperature sensors stand guard, providing alerts for temperature variations.
Lubrication
Like a well-choreographed ballet, CNC machines necessitate precise lubrication to maintain the seamless motion of intricate parts, preventing premature wear.
Fluid Oversight
Beyond lubrication, careful monitoring of hydraulic and other fluid levels is essential. Unusual fluid consumption might hint at underlying issues.
Surface Hygiene
In a universe where precision rules, even surfaces matter. Regularly wiping down surfaces—windows, doors, lights, handles—ensures clarity, grip, and a spotless work environment.
A seasoned maintenance expert brings more than just tools and oils. They bring an acute ear attuned to the machine’s rhythm, sensing the melody of optimal performance. A sudden shift in operational sounds becomes their cue, indicating a call for attention. In this delicate choreography, maintenance isn’t confined to the visible; it extends to what you hear, feels, and forestall.
What Should Be the Maintenance Schedule for CNC Machines?
The cost of an unexpected CNC machine breakdown can be a hard-hitting blow – roughly five times more costly than a proactive annual maintenance plan. The cornerstone of such planning is the Preventive Maintenance Plan, designed to safeguard CNC machines’ reliability. But how frequent should maintenance tasks be undertaken? Striking the right balance between routine maintenance and production efficiency requires tailoring the schedule to individual shop needs and experiences, while still heeding the manufacturer’s recommendations. Manufacturers of CNC machines prescribe general maintenance intervals, yet these often undergo adjustments based on a shop’s unique production demands. Customizing the plan to align with optimal performance and minimal downtime is key, ensuring a fine-tuned workflow. A strategic plan is only part of the equation. Modern CNC machines come equipped with sophisticated sensors and detectors that keenly detect potential issues. These systems raise alerts, notifying maintenance teams to address specific areas in need of attention. For instance, when a hydraulic hose ruptures, the machine senses pressure loss and halts the cycle to prevent further harm, simultaneously notifying the operator and even the supervisor via email in case of more severe problems. Robust construction lends most CNC machines a degree of resilience, requiring substantial force to inflict serious damage.
While this outline isn’t exhaustive, it covers the majority of essential tasks, categorized by intervals for your convenience. It’s important to note that CNC machine maintenance practices can vary among manufacturers or companies based on their specific processes and production needs.
Daily Maintenance
Ensure the optimal performance of your CNC machine with this comprehensive daily maintenance checklist:
Mechanical
- Ensure cleanliness around the chuck or spindle and the machine bed.
- Verify the security of all covers or guards.
- Clean slide rails, such as doors or covers, to maintain smooth movement.
Electrical
- Check the indicator lights for all machine components.
- Test the functionality of all emergency push buttons.
- Perform a motor test by starting and stopping while pressing the emergency push button.
- Verify the overall operation of the machine
Hydraulic
- Inspect for any signs of leakage in the hydraulic system.
- Check the oil level in the hydraulic system.
- Ensure the chiller unit is functioning effectively to regulate temperature.
Tool Setter
- Thoroughly inspect all tooling for any signs of damage or wear.
- Check lubrication levels and replenish if necessary.
- Grease parts that appear dry to ensure smooth movement.
- Verify the concentration and fill levels of coolant.
- Empty the chip hopper to maintain efficient chip evacuation.
- Check the levels of the hydraulic system.
- Wipe down all surfaces to prevent the buildup of small metal shavings.
Weekly Maintenance
Mechanical
- Check the Oil level of Head stock/Gear Box and Automatic Lubrication Unit.
- Check for any mechanical part is damaged. Any loose of mounting bolts.
- Check any abnormal sound from Gear box.
Electrical
- Check the Cable shaping of cable loop.
- Check all cable for any damage of insulation.
- Check any chattering sound from any component.
- Check the current consumption of all motor.
Hydraulic
- Pipe should not Damage.
- Check if any abnormal sound from pump.
Monthly Maintenance
Mechanical
- Examine all drive belts for correct tension and any signs of damage. Adjust tension as needed.
- Check the filter of the gearbox lubrication system. Clean or replace it if required.
- Evaluate the coolant condition and replace it if necessary.
- Inspect the jaws for jamming and lubricate them if needed.
Electrical
- Inspect all motors to ensure they are functioning correctly.
- Re-torque the bolting of motors and clean their surroundings.
- Verify the proper functioning of all electromagnetic components.
- Check and replace brushes on rotating components as needed. For instance, replace the telescopic brush of the clutch, carbon brushes of DC motors and generators.
Hydraulic
- Inspect for any signs of leakage in the hydraulic system
- Check the oil level in the hydraulic system.
- Ensure the chiller unit is functioning effectively.
- Examine pipes for any damage.
- Listen for any abnormal sounds coming from the hydraulic pump.
- Clean the hydraulic filter.
- Check the pressure settings in the hydraulic system.
Additional Monthly Maintenance Tasks
- Clean or replace air filters.
- Check and clean coolant filters.
- Clean radiators and cooling fans.
- Review oil fill checklists for any signs of unusual oil consumption.
- Remove and clean the chuck and jaws.
- Grease and adjust chains or conveyors.
Semi-Annual Maintenance
Mechanical
- Evaluate the clearance in the guide ways and examine the taper wedge for wear and tear.
- Verify the accuracy of the output products.
- Check for any taper cutting issues.
- Inspect the alignment of the head or spindle.
- Examine the backlash of axis drives.
Electrical
- Inspect all limit switches to ensure they are functioning correctly.
- Verify the proper functioning of all proximity switches.
- Re-torque all breaker connections to ensure secure electrical connections.
Hydraulic
- Re-torque all valves and cylinder mounting to maintain proper alignment.
- Inspect all safety valves for proper functioning.
- Replace all filters in the hydraulic system.
- Replace the O-rings of valves if required.
- Check for any oil leakage from the cylinders.
Additional Semi-Yearly Maintenance Tasks
- Lubricate all moving parts.
- Check and calibrate the machine’s accuracy and precision.
- Inspect and clean the coolant system thoroughly.
- Examine and tighten all bolts and fasteners.
- Clean and inspect the machine’s electrical components.
- Test and verify emergency stop and safety systems.
Yearly Maintenance
Mechanical
- Check the radial and axial play of the spindle to ensure proper alignment.
- Replace all the wipers of the guide ways to prevent contamination and maintain smooth movement.
- Inspect the mounting of the guideways for stability and alignment.
- Evaluate the condition of bearings for wear and proper functioning.
- Check the leveling of the machine’s base and align if required to maintain precision.
- Check the headstock for tapering to ensure accurate machining.
- Inspect and adjust drawbar tension for secure tool retention.
- Run a backlash program and replace X and Y axis gibs if needed to maintain accuracy.
Electrical
- Inspect and tighten all electrical connections and terminals.
- Check and test the machine’s electrical grounding system.
- Verify the proper functioning of all control panel components.
- Clean and inspect the machine’s electrical cabinet for dust and debris.
Hydraulic
- Drain and replace hydraulic oil and filters.
- Test hydraulic oil for contaminants and replace filters as needed.
- Inspect and test hydraulic pumps and valves.
- Check the condition of hydraulic hoses and replace if necessary.
Additional Yearly Maintenance Tasks
- Remove the coolant tank completely; clean out metal chips not caught by the conveyor; inspect and clean the coolant system for bacterial growth.
- Drain and clean the lubrication unit; replace the lubrication oil
- Perform a comprehensive cleaning of the entire machine, including hard-to-reach areas.
- Calibrate the machine’s accuracy and precision.
- Test and verify the machine’s emergency stop and safety systems
- Inspect and replace any worn or damaged belts.
- Lubricate all moving parts and ball screws as per manufacturer recommendations.
- Inspect the chuck cylinder for proper operation.
- Review and update the machine’s maintenance schedule based on its performance throughout the year.
Regular and meticulous maintenance ensures that your CNC machine operates at its best, delivering consistent and precise results while extending its operational life.
Note: Please remember that this checklist is meant to offer general guidance. Your specific machine requirements, usage patterns, and manufacturing processes may necessitate adjustments to this checklist for optimal results. Regular, tailored maintenance ensures your CNC machine continues to deliver reliable performance and prolonged operational life.
Efficient CNC Maintenance: Boosting Performance and Satisfaction
While the tasks performed by various CNC machines may differ, their maintenance requirements share common elements: lubrication, coolant management, filter upkeep, and more. The realm of robotics presents a distinct narrative; these robust machines demand minimal ongoing maintenance efforts.
While preventive measures aim to avert breakdowns, the inevitability of repairs remains. A workshop equipped with in-house resources to swiftly address machine issues transforms the equation. External assistance incurs both time and expenses, yet an internal maintenance team can swiftly respond to a CNC machine breakdown, curbing downtime significantly. With readily available in-house spare parts, repair durations are generally minimized. This efficacy not only reflects in the financial outcome but also resonates in timely deliveries and contented customers.
Trusted Performance For Years
How long do CNC machines usually last with proper maintenance? Trusted performance can be expected for as long as 20 years. Again, these are rugged machines built to withstand harsh environments and continuous use.
Most often, machine replacement is dictated by newer technology or faster capabilities rather than a catastrophic breakdown. Accuracy issues are usually the first telltale sign that a machine is reaching its end, often far enough that no maintenance intervention can bring it back.
The right CNC machine maintenance not only results in high-end performance, it also means peace of mind. Operators and supervisors know that these valuable pieces of equipment are well cared for, and instant alerts will be sent if a problem occurs. Incorporating advanced Computerized Maintenance Management System (CMMS) software like eWorkOrders can amplify these benefits, providing an efficient platform for organizing and overseeing maintenance checklists and tasks.
However, peace of mind truly rests on the reliability of the information in a shop’s preventive maintenance system. Documentation of everything — machine inspection, service, issues, replacement — is critical in evaluating maintenance’s effectiveness and how much you can rely on it to make future business decisions.
Pallet jacks, forklifts, floor scrubbers. A valued maintenance professional’s knowledge goes beyond CNC machines, of course.
Frequently Asked Questions (FAQs) Related To CNC Machine Maintenance
How often should I schedule maintenance for my CNC machine?
The frequency of maintenance depends on factors like machine usage, environment, and manufacturer recommendations. Typically, regular inspections and basic tasks like cleaning should be performed daily, while more comprehensive maintenance can be scheduled weekly, monthly, semi-annually or yearly.
Can I handle CNC machine maintenance tasks on my own, or do I need professional assistance?
Basic tasks such as cleaning, lubrication, and visual inspections can often be performed by operators. However, more complex maintenance, adjustments, and troubleshooting are best left to trained professionals to avoid causing further damage.
How does implementing a Computerized Maintenance Management System (CMMS) benefit CNC machine maintenance?
A CMMS like eWorkOrders streamlines maintenance processes by helping you schedule, track, and manage maintenance tasks. It provides automated alerts for upcoming tasks, stores historical maintenance records, and facilitates data-driven decisions for optimal machine performance.
How do I know when it’s time to replace a cutting tool or spindle component?
Regular tool inspections are essential. If you notice signs of wear, chipping, or reduced machining quality, it’s time to replace the tool. For spindles, monitor for unusual vibrations or noises, and inspect the spindle taper for debris buildup.
How do I ensure the accuracy and precision of my CNC machine’s output over time?
Regular calibration and alignment of machine axes are essential to maintain accuracy. Scheduled maintenance, adherence to manufacturer guidelines, and professional inspections contribute to consistent precision.
Can preventive maintenance extend the lifespan of my CNC machine?
Absolutely. Implementing a well-structured preventive maintenance plan can significantly extend the lifespan of your CNC machine by identifying and addressing potential issues before they escalate
What benefits does eWorkOrders offer for CNC machine maintenance?
eWorkOrders CMMS simplifies maintenance management by providing a centralized platform for scheduling, tracking, and managing maintenance tasks. It helps streamline operations, reduce downtime, and improve overall machine efficiency through organized maintenance processes.