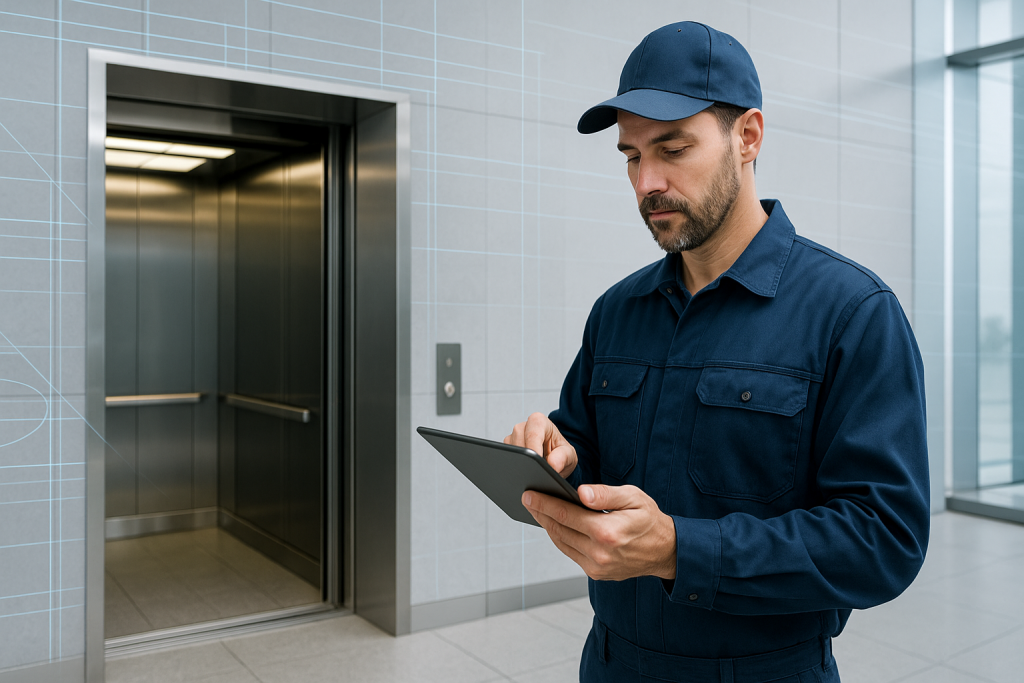
Lift maintenance is the safeguard that keeps people moving, shields your organization from liability claims, and prevents budget-draining downtime. When elevators stall unexpectedly, tenant satisfaction plummets, safety risks rise, and unplanned repair invoices hit hard.
This guide gives you an actionable checklist, clear cost benchmarks, and step-by-step compliance tips drawn from ASME A17.1 and regional regulations—everything building and facility professionals need to keep lifts reliable, safe, and audit-ready.
Need a quick refresher first? Our detailed Elevator Maintenance Tips article covers the fundamentals; the pages below build on that foundation with tactics you can implement today.
Why Regular Lift Maintenance Matters
Lift maintenance failures can ripple through an entire operation. In fact, elevators worldwide break down an average of four times a year, leading to 272 million hours of lost service annually [1]. Building owners and facility managers should carefully consider the following crucial factors when it comes to elevator maintenance:
- Elevators are responsible for transporting passengers and goods between different floors, making their safety paramount. Regular maintenance is essential to identify and address potential issues before they escalate, ensuring the elevator remains reliable and safe for all users. A sudden breakdown of the elevator can lead to severe accidents, causing injuries or worse.
- Elevators play an important role in daily building operations, and their downtime can cause significant inconveniences for occupants and visitors. In the worst-case scenario, prolonged elevator outages can disrupt business operations, leading to productivity losses and potential reputational damage for the building management.
- Repairing or replacing broken elevators can be an expensive endeavor, often running into tens or hundreds of thousands of dollars, depending on the severity of the issue and the elevator’s complexity. Regular maintenance helps identify minor problems early on, preventing costly breakdowns and prolonging the useful life of the elevator, thereby reducing long-term expenses.
- Many regions have strict laws and regulations governing elevator maintenance and safety inspections. OSHA requires at least one comprehensive inspection every 12 months, plus monthly operational checks, while ASME A17.1-2022 obliges owners to maintain a documented Maintenance Control Program (MCP) for each lift. In some jurisdictions, buildings are required to display the date of their last maintenance inspection inside the elevator.
How Often Should You Service a Lift?
A one-size-fits-all timetable doesn’t work for lift maintenance—service frequency hinges on how hard the unit works and what the law demands where you operate.
Usage tiers
- Residential / low-rise (≤ 6 stops): Full preventive visit every 3 months and a visual check monthly.
- Mid-rise commercial (7–20 stops, moderate traffic): Technician visit every 4–6 weeks plus remote monitoring.
- High-rise, heavy-use, or hospital lifts: Weekly hands-on checks, with sensors feeding condition data around the clock.
Regulatory inspection benchmarks
Rule of thumb: Scheduled maintenance visits should outnumber statutory inspections by a factor of three or more; waiting for the legal deadline almost guarantees extra elevator repair costs later.
Warning signs you’re sliding toward elevator repair territory
- Doors hesitate, bounce, or close slower than usual
- Car levels stop noticeably above or below the floor
- New grinding, rattling, or humming noises
- Frequent “nuisance” shutdowns or controller fault codes
- Rising call-back count for the same component
If you see two or more of these red flags between planned services, escalate to a diagnostic visit immediately—catching faults early is far cheaper than an after-hours repair call-out and days of downtime.
Preventive vs Predictive vs Corrective: Choosing the Right Strategy
Strategy | Core Goal | Typical Tasks | Trigger | Pros | Cons |
Preventive Maintenance | Stop faults before they start | Scheduled lubrication, safety-device testing, door operator cleaning | Calendar or run-time intervals (e.g., every 500 car cycles) | Predictable costs, proven to extend equipment life | Can waste labour if intervals are too conservative |
Predictive Maintenance | Fix when data predicts failure | Vibration trend analysis, oil-particle counts, motor temperature trending | Sensor thresholds, algorithmic alerts | Cuts downtime and parts spend; enables just-in-time ordering | Requires sensors, analytics, and skilled interpretation |
Corrective Maintenance | Restore service after a failure | Seal replacement, PCB swap, door operator rebuild | Component breaks or fails inspection | No upfront cost until something breaks | Unplanned outages, higher liability, premium call-out fees |
IoT & condition-monitoring in action
- Load-cell sensors flag door drag that precedes operator motor burnout, allowing a quick preventive adjustment instead of a full elevator repair.
- Remote controller diagnostics push live fault codes to a CMMS, automatically launching a work order and notifying on-call technicians.
- Vibration beacons on traction machines predict rope slip, enabling an in-shaft inspection during the next scheduled lift maintenance window rather than an emergency shutdown.
Blending preventive and predictive tactics usually delivers the best ROI—predictive data fine-tunes preventive intervals, while corrective capability remains the safety net for unforeseeable events.
How to Perform Lift Maintenance
Proper maintenance helps identify and address potential issues before they become significant problems. Performing lift maintenance typically involves the following steps:
Inspection
Regular inspections are crucial for identifying any signs of wear and tear, damage, or malfunction in the lift components. Trained technicians inspect the lift’s mechanical, electrical, and safety systems.
Cleaning
Keeping the lift clean is essential to prevent dirt and debris from interfering with the smooth operation of the lift doors, buttons, and other components.
Lubrication
Proper lubrication of moving parts reduces friction and wear. This includes the lift’s gears, pulleys, and other mechanical elements.
Testing Safety Features
Technicians will test various safety features, such as emergency brakes, door sensors, and overload protection, to ensure they are working correctly.
Replacing Worn Parts
Any damaged or worn-out components identified during inspections should be promptly replaced with genuine parts to maintain the lift’s performance and safety.
Software and Control System Checks
For modern lifts with computerized control systems, technicians will check the software and make any necessary updates to ensure the lift operates smoothly and efficiently.
Load Testing
Periodic load testing is done to ensure that the lift can handle its rated capacity safely.
Emergency Preparedness
Technicians should be well-trained in handling lift emergencies and be able to respond quickly to any unexpected situations.
It is crucial to have lift maintenance performed by trained and certified professionals. Attempting to maintain lifts without the necessary expertise can lead to safety risks and potential legal issues.
If you own or manage a building with a lift, you should consider entering into a maintenance contract with a reputable lift maintenance company. They will typically offer regular maintenance visits, emergency call-out services, and the expertise needed to keep your lift in optimal working condition. The frequency of maintenance visits may vary depending on factors such as the type of lift, its usage, and local regulations, but typically they occur every 1 to 6 months.
Remember, lift maintenance is not just about meeting regulatory requirements; it’s about ensuring the safety and comfort of everyone who uses the lift.
Elevator Maintenance: Schedules and Checklists for Efficiency
Developing elevator maintenance schedules and checklists involves considering several crucial factors to ensure efficient maintenance and compliance with regulations. Here are the key steps involved:
Factors To Consider
When creating elevator maintenance schedules, various factors need to be taken into account, including:
- Usage statistics of each elevator
- Data from condition monitoring sensors (if applicable)
- Input from elevator operators (if applicable)
- Relevant local regulations
Adaptation to Location
The final maintenance schedule must also account for any location-specific extraneous circumstances that may affect elevator performance and maintenance.
In-House Maintenance
For those performing elevator and lift maintenance in-house, it is essential to ensure that the work is carried out up to the required standards and in compliance with regulations.
Standard Operating Procedures (SOPs)
Establishing standard operating procedures and preventive maintenance checklists is an effective way to ensure consistent and reliable maintenance practices.
CMMS System Integration
If using a Computerized Maintenance Management System (CMMS) like eWorkOrders, you can streamline the maintenance process. This involves creating SOPs and checklists within the CMMS software and attaching them to the corresponding elevator equipment entries in the database. Additionally, these documents can be linked to specific work orders.
Easy Access for Technicians: By integrating SOPs and checklists into the CMMS, technicians gain quick and convenient access to these resources. They can access the necessary documents with just a couple of clicks or taps on their screens, regardless of their location.
By following these steps and utilizing a comprehensive CMMS system, elevator maintenance can be efficiently scheduled, executed, and monitored, leading to improved elevator performance and compliance with regulatory requirements.
Lift Maintenance Checklist
Each bullet below captures the essentials your team should tick off during every scheduled visit. Use it as a live template in your CMMS:
Machine Room
- Test the smoke- and fire-alarm circuit and verify signal to the main panel.
- Check and top up oil; lubricate bearings, gears, and governor as per OEM spec.
- Inspect wiring for frays, discoloration, or overheating, and tighten any loose terminals.
- Clear obstructions so there’s full head- and side-room for technicians; store no non-elevator items.
Top-of-Car
- Examine hoist cables for kinks, broken strands, or corrosion.
- Test brake mechanism and confirm the car holds under rated load.
- Verify inspection station & stop switch operation; confirm emergency hatch can be opened easily.
- Scan hoistway for debris, vandalism, or water intrusion.
Lift Car Interior
- Cycle doors several times to ensure smooth, unobstructed travel.
- Check finishes—ceiling, panels, handrails—for damage or looseness.
- Replace burned-out lamps/indicators inside the cab and COP.
- Dial the emergency phone/alarm to verify instant connection to the monitoring centre or 911.
Lift Pit
- Inspect cables, guide rails, rollers & switches for wear or mis-alignment.
- Clean and test sump pump; remove standing water, oil, and debris.
- Check spring or oil buffers for corrosion, secure anchors, and correct centring.
- Examine pit lighting & GFCI outlets for proper function and 10 fc illumination.
Doors, Safety Devices & Emergency Systems
- Verify light curtains / door sensors and interlock contacts on every landing.
- Test emergency stop, alarm bell, and car top stop switch; record reset times.
- Confirm fire-fighter recall (Phase I & II) and automatic recall by FAIDs function as designed.
- Inspect overspeed governor, safety gear & rope tension device for seal integrity and proper clearance.
Creating a Maintenance Schedule that Sticks
Every OEM publishes baseline service intervals, but the most reliable lift maintenance plans refine those numbers with real-world usage data.
1. Start with the OEM playbook
Major manufacturers such as KONE and Otis lay out minimum preventive tasks and intervals in their service manuals—weekly lubrication for door operators, quarterly safety-gear tests, annual hoist-rope inspection, and so on.kone.us These benchmarks ensure warranty protection and align with the ASME A17.1 Maintenance Control Program (MCP) requirements that every lift must meet.theelevatorconsultant.comelevatorinfo.org
2. Layer on actual usage data
- Trip counters & car-cycle logs Adjust oil-change or bearing-inspection frequency when traffic exceeds OEM “normal use” assumptions.
- Operating hours & starts High-rise shuttle cars that run 20 hours a day may need weekly checks that a low-rise residential lift can stretch to monthly.
- Environmental factors Heat, humidity, or industrial dust can shorten lubricant life and trigger mid-cycle tasks.
3. Combine calendar and runtime triggers
Trigger type | Example rule | Why it matters |
Calendar-based | “Lubricate door rollers every 30 days.” | Catches age-related degradation. |
Runtime-based | “Inspect a traction machine every 10 000 car moves.” | Matches wear directly to usage, preventing over- or under-servicing. |
Using both trigger types ensures regulatory boxes are ticked while heavy-use components get attention exactly when they need it.
Who Should Perform Maintenance?
ASME A17.1 and OSHA 1917.116 both state that lift maintenance must be carried out only by “qualified” or “competent” personnel—people who can demonstrate the skills, training, and credentials to keep riders safe and regulators satisfied.
Licensed Elevator Contractors
Contracting an OEM or independent elevator firm remains the default choice for most buildings. These companies hold state elevator licences, carry specialised liability insurance, and employ technicians who meet industry-standard certifications (see checklist below). Contracts typically bundle routine elevator maintenance, 24/7 call-outs, and code-mandated tests.
In-House Technicians
Large portfolios sometimes justify their own teams—especially when lifts share common models and spare-parts bins. An internal tech programme only works when every mechanic:
- Holds a current Certified Elevator Technician (CET) card;
- Completes OEM refresher courses; and
- Logs each task in a CMMS for traceability.
Without those safeguards, any cost savings evaporate the first time a regulator asks for proof of competence.
Third-Party Audits & Inspections
Even with a maintenance contract, most authorities require an annual (or semi-annual) inspection by a Qualified Elevator Inspector (QEI) who is independent of the service provider. naesai.org Auditors verify that the Maintenance Control Program (MCP) is up to date, witness safety-gear and governor tests, and spot-check documentation.
Certification Checklist
Use this quick list when evaluating a contractor, hiring an in-house tech, or scheduling an audit:
Must-Have Credential | What It Proves | Issuing Body |
CET – Certified Elevator Technician | Hands-on competence in installation, service, and elevator repair | National Assoc. of Elevator Contractors (NAEC) naec.org |
QEI – Qualified Elevator Inspector | Authority to perform code inspections and witness tests | NAESA International / ASME QEI-1 naesai.org |
State Elevator Mechanic Licence | Legal permission to work on lifts within the jurisdiction | State elevator board |
OEM Factory Training Certificates | Model-specific knowledge (e.g., Otis Gen2 belts, KONE EcoDisc motors) | Equipment manufacturer |
OSHA 10- or 30-Hour Card | General workplace-safety competency | U.S. Dept. of Labor |
Securing the right mix of certified professionals—contracted or in-house—gives you defensible compliance and the expertise to drive down downtime and unplanned costs.
Calculating Lift Maintenance Costs
Elevator maintenance costs can vary depending on several factors, including the type of elevator, its age, complexity, and the service provider. Let’s delve into the key cost considerations when it comes to elevator maintenance:
Elevator Type
Different types of elevators, such as hydraulic, traction, or machine-room-less (MRL) elevators, have distinct maintenance requirements. Each type may involve specific components and mechanisms, which can impact the overall maintenance cost.
Age and Condition
Older elevators may require more frequent and extensive maintenance to keep them running efficiently and safely.Regular Maintenance for older elevators is essential to prevent breakdowns and extend their useful life.
Service Level
Elevator maintenance plans come in various service levels, ranging from basic preventive maintenance to comprehensive packages that cover repairs and emergency call-outs. The more comprehensive the service level, the higher the cost.
Frequency of Maintenance
The frequency of maintenance visits also affects the cost. Elevators subject to heavier usage or located in high-traffic buildings may require more frequent inspections and maintenance.
Certified Technicians
Elevator maintenance should be performed by certified technicians who possess the necessary expertise and training. Hiring certified professionals ensures the elevators receive proper care, but their hourly rates can impact maintenance costs.
Replacement Parts
As elevators age, certain components may require replacement. Sourcing original equipment manufacturer (OEM) parts can be more expensive, but it ensures compatibility and reliability. However, there are alternatives, such as refurbished or aftermarket parts, that can be more cost-effective.
Outsourcing vs. In-House Maintenance
Building owners have the option to outsource elevator maintenance to specialized servicing companies or handle it in-house with dedicated maintenance staff. The decision may depend on budget considerations and the scale of the elevator maintenance needs.
Emergency Repairs
In the event of an unexpected breakdown, emergency repairs may be necessary to restore elevator functionality quickly. Emergency service calls often come with additional costs, so proactive maintenance is essential to minimize the likelihood of emergencies.
A clear picture of all cost drivers lets you defend budgets and spot savings before they disappear into reactive elevator repair bills. Below is a benchmark snapshot for a single mid-rise traction lift.
Cost Category | Typical Range* | What It Covers | |
Preventive maintenance contract (annual) | US $3,500 – $5,000 | Scheduled service visits, lubrication, safety-device tests, basic call-out allowance | |
Emergency call-outs / minor repairs | US $209 – $580 per event (avg. $393) | Labour, travel, fault reset, minor parts | |
Parts replacement during breakdowns | ≈ US $700 in materials + US $1,200 labour | Door rollers, seals, relays, small PCB boards | |
Major modernisation | US $150,000 – $1 million per car | Controller, machine, doors, cab, code upgrades |
* Actual figures vary by region, vendor, and traffic profile, but these benchmarks capture the 80 % most common scenarios.
Quick ROI Calculator
Formula:
Avoided Downtime Cost − Annual Maintenance Spend
Annual Maintenance Spend
×100=ROI %
Example:
- Downtime cost per hour (lost rent, staff idle time): US $450
- Hours of downtime prevented by proactive plan: 40 h/year
- Annual preventive contract: US $4,500
4,500(450×40)−4,500
4,500
×100=300% ROI
Even a modest 10-hour reduction produces a positive return—proof you can take to finance when negotiating next year’s service budget.
Want to calculate your own numbers? Use our free CMMS ROI Calculator to estimate your potential savings.
Leveraging CMMS to Automate Compliance & Uptime
Alt text: eWorkOrders logo.
Modern lift maintenance programs live or die on the strength of their data. A Computerized Maintenance Management System (CMMS) such as eWorkOrders ties every compliance check, repair, and spare-part transaction to a single digital thread, so nothing falls through the cracks.
- Work-order automation routes incoming requests to the right technician, opens each job with the relevant SOP, and lets you schedule required ASME A17.1 test routines at the exact intervals you specify.
- Mobile inspections let field techs attach photos, meter readings, and signatures from the top-of-car or pit—even offline—closing the loop in seconds.
- Real-time dashboards & KPIs surface open violations, mean time between failures (MTBF), and cost variance the moment data is saved, giving managers instant visibility.
Case in point: According to eWorkOrders’ customer averages, manufacturers that adopt its Tool & Die Management Software report up to a 20–40 % cut in tool-related downtime and as much as a 30 % reduction in maintenance costs after implementation.
Looking beyond vertical transport? Explore our Fleet Maintenance Management Software for mixed-asset operations and keep every piece of equipment—lifts included—running at peak reliability. Keep your compressed air systems operating efficiently with these air compressor maintenance tips.
FAQ
What is the maintenance of a lift?
Lift maintenance is a planned program of inspections, cleaning, lubrication, adjustments, and safety tests that keeps an elevator or platform lift operating smoothly, safely, and in full compliance with codes such as ASME A17.1 or EN 81. Regular maintenance reduces breakdowns, extends equipment life, and provides documented proof of due diligence for insurers and regulators.
How often should a lift be serviced?
Most passenger lifts in commercial buildings need a technician visit every four to six weeks, plus a statutory full inspection every six or twelve months, depending on local regulations (e.g., LOLER in the UK or OSHA/ASME in the US). High-traffic or hospital installations may warrant weekly checks, while low-rise residential lifts can often stretch to quarterly service if usage is light.
What maintenance does a lifted truck need?
A vehicle with an aftermarket suspension lift requires periodic torque checks on all lift-kit hardware, inspection of driveshaft and steering angles, verification that brake-line extensions aren’t rubbing, and frequent greasing of suspension joints. Because the altered geometry adds stress, tyres, wheel bearings, and alignment should also be monitored more often than on a stock truck.
What is the cost of lift maintenance?
Annual preventive maintenance contracts for a single mid-rise traction lift typically range from US $3,500 to $5,000, covering routine visits and basic call-outs; emergency repairs or major parts replacements are extra. Over a 20-year life cycle, proactive maintenance generally costs 30–40 % less than a reactive, repair-only approach by avoiding downtime and premature component failures.