
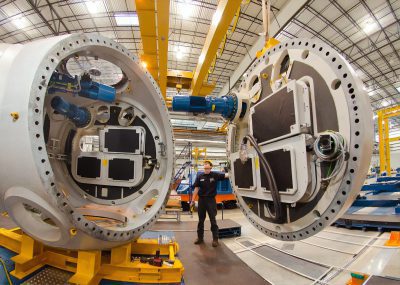
As we are slowly approaching the reopening of our economy and the reopening of buildings that have been dormant for a while, we are now starting the painful tasks of getting facilities operational and safe for employees and preparing for more aggressive inspections. Not only do you have to catch up on routine maintenance tasks, but there are also new specific precautions and safety guidelines you need to think about in preparing for the reopening of your facility. With the additional tasks and concerns related to sanitation, electrical, fire protection, inspections, and other facility-specific operations you need to be able to effectively manage all of these tasks and still be productive. Plus making sure that you are even better prepared to meet any other disaster that may arise.
Below are some recommended procedures to help you in preparing your facility for reopening.
Having the Right Tools
As you are weeding through all of the overwhelming normal tasks and the new recommendations, policies, procedures, and guidelines, how are you going to manage through these tasks?
Maintenance shouldn’t be complicated. Having the right tools in place like a computerized maintenance management system (CMMS) can help you quickly and easily streamline and manage these tasks from anywhere. With a CMMS, everything is stored in one centralized system with the ability to view and run reports using real-time data, which makes your chore of preparing for inspections a whole lot easier. CMMS can help you through your current situation and also prepare you in case there is another disaster. Now is the time to take control of your maintenance operations and manage your operations faster, easier, and more efficiently.
New Guidelines*
One of the first things is to get an understanding of what are the cleaning and disinfecting requirements for your state and local health guidance. If your building has been unoccupied for a long time or due to COVID-19, you need to review the guidelines from the Centers for Disease Control and Prevention (CDC) and their recommendations for completing normal routine cleaning and disinfecting procedures. If you continue operating on a limited basis, you need to consider additional cleaning and disinfecting procedures as specified in your state or local guidelines.
Checklists*
Every business has its own special checklist of items that pertains to helping them in their standards and regulations to ensure operator safety, optimal efficiency, and good practices. Checklists improve work order accuracy, ensure maintenance process consistency, enhance collaboration, validate that tasks have been completed, and help provide regulatory compliance. Using a CMMS, it is easy to incorporate checklists on your work orders and monitor the status in real-time.
Facilities Structure*
- Debris: Inspect sidewalks, stairs, hallways, etc., and remove any debris, both on the exterior and interior of the building.
- Roof: Inspect and repair roofs for any water leaks, damage, debris, blockages, etc.
- Gutters: Inspect and clean any debris and make sure that water is being discharged away from the building.
- Water Damage: Check walls and ceilings for signs of water damage or cracks.
- Mold: Inspect your facilities to ensure that your building does not have mold.
- Stagnant or Standing Water: Inspect interior and outside areas to remove any stagnant or standing water.
- Test Water Supply: Dormant pipes and plumbing are potential bacterial growth hazards.
- Flammable Liquids: Review and inspect all flammable liquids rooms for ventilation, drainage, electrical, dispensing, spray painting interlocks, and fire protection. Ensure that all flammable liquid containers are checked for leaks, damage, labeled and stored properly in a ventilated area.
- Employee Environment: Clean and disinfect all areas to meet CDC guidelines.
- Social Distancing: Ensure that all workstations and work areas meet CDC guidelines.
- Sanitization Procedures: With all the necessary sanitization procedures put in place, you need to create a communications plan to keep employees informed.
Fire Safety Checks*
- Fire Extinguishers: Inspect if you have enough, make sure that they are easily accessible and recharge as necessary. Display and have clear communications on fire safety within your facility. Make sure that all workers know all of the exit plans. Make sure that special purpose extinguishers and are clearly marked.
- Fire Alarms: Confirm and test all fire protection alarms (smoke, flow, and tamper) for damage and operation via testing and confirmation with any central station. Inspect all manual pull devices to ensure they are accessible and not damaged.
- Sprinkler Systems: Physically inspect that all sprinklers are not damaged, and all valves are in the open position, gauges are not damaged and operable.
- Facilities Fire Protection Plan: Review, update and continue to implement your facilities’ fire protection program.
- Escape Plans: All escape paths are free of any clutter, doors are in operation and not blocked, fire doors are working properly, emergency lighting is working properly, and exit signs are easily visible and illuminated.
- Codes & Standards: Confirm that all relevant NFPA Codes and Standards have been met.
- Emergency Entrance Procedures: Confirm that all “special” emergency entrance procedures are put in place and communicated.
- Inspections: Confirm that all maintenance and inspections are current.
- Dangerous Liquids Storage: Hand Sanitizers or alcohol-based hand rubs, disinfectants, cleaning supplies are stored and managed safely to NFPA 101 guidelines.
Electrical*
- Machines: Make sure that machines are all properly grounded.
- Junction Boxes: Check and inspect junction boxes to make sure that they are fitted and close properly.
- Extension Cords: Ensure they are located out of main aisles and heavy traffic and that that they are in good condition, not near water, properly being used outdoor or indoor, can handle the voltage of the devices, and are the proper length.
- Power Distribution: Confirm that there have been no changes in power distribution and requirements for your facility.
- Test: Test and repair all relays, breakers, fused disconnects, etc.
- Generators: Inspect, test and repair backup generators and backup power distribution systems.
- Outlets: Inspect power sockets, cables, equipment, plant, and electrical systems for any damage and make repairs.
- Electrical Code: Inspect your electrical devices to make sure that they are all up to date and meet regulations and are up to code.
- Wiring: Inspect wiring and repair any damaged wiring.
- Electrical Loads: Electrical loads should be restored slowly to prevent damage to electrical systems. As power is restored, maintenance personnel should monitor equipment operation.
HVAC and Plumbing Systems*
After months of now operating, bringing these systems back to full operation can be a big challenge. The checklist for bringing these systems back up to normal operations varies across building types and sizes and the types of HVAC systems that your facility has implemented. It is recommended that the best way to address HVAC systems is following the first day of operation, following ASHRAE/ ACCA Standard 180-2018, Standard Practice for Inspection and Maintenance of Commercial Building HVAC Systems.
- Operational: Test and confirm the system is operational and make any necessary repairs.
- Manufacturers Requirements: Clean and replace filters and do any maintenance that is recommended by the manufacturer and any CDC requirements. Lubricate pumps and motors, etc.
- Maintenance: Clean coils/heat wheels/louvers/dampers, ensure that louver and dampers are operating.
- Floor Drains: Inspect and clean out floor drains and ensure that there are no obstacles blocking the drains.
- Water System: If you have been dormant for a period of time, it might be a good idea to flush the building’s water system to help remove the possibility of mold or bacteria buildup.
Returning Idle Tools, Machinery and Equipment*
- Initial Restart: Review and follow manufacturer’s recommendations and procedures for starting up and break-in periods for equipment and machinery.
- Cleaning and Disinfecting: Inspect, clean, and disinfect equipment, tools and machinery before resuming operations.
- Damage: Inspect and repair all equipment, tools, pumps, boilers, etc., before operations.
- Training: Re-train employees on the use and safety of machinery.
- Maintenance Schedules: Review, update and create preventive maintenance schedules for equipment and machinery.
- Machinery & Equipment Maintenance: Replace lubricants and cooling fluids, belts, oil pressure, etc., for critical equipment, ensure that all safeguards are properly in place and working.
- Machine Tolerance: Check calibrations and alignment to help ensure sensors and measuring devices are functioning properly.
- Inspections: Increase inspections until equipment and machinery are working at normal capacity.
Miscellaneous*
- Sanitization: Follow CDC-recommended sanitation procedures for the reopening of your facilities.
- Social Distancing: Follow CDC “social distancing” restrictions during the reopening of your facilities.
- Protective Gear: Communicate all recommended usage of Personal Protective Equipment, masks, etc., to employees upon reopening.
- Sanitization Supplies: Make sure that everyone knows your facility guidelines, processes, and availability of sanitation supplies.
- Contingency Plan: Develop a contingency plan for emergency sanitization to address the possibility of an infected person entering your facility.
The above is not an all-inclusive procedure for reopening your facility after a shutdown but are just some recommendations that you might want to add to your checklist.
Maintenance Planning
These are just some of the tasks that facility managers are adding to their daily task lists. With the added responsibilities due to COVID, the challenges are even tougher. There is an even greater need to protect employees, keep environments safe, keep equipment running at peak performance, ensure that everything is documented for inspections, make sure inventory is well stocked and the bottom line is that companies need to work smarter and be prepared. Having Computerized Maintenance Management System (CMMS) software in place is the key to keeping your maintenance operations working through any disaster. Organizations that focus on long-term maintenance planning outperform reactive ones.
Implementing a CMMS helps businesses take control of their maintenance operations and unleash the power of the system to enable you to manage your business operations from anywhere through any disaster.
Jeff Roscher is Co-Founder and President of eWorkOrders (Information Professionals, Inc.). eWorkOrders is an industry leader in computerized maintenance management system (CMMS) software.
*DISCLAIMER: The information contained in this article is for informational purposes only. The information is just some recommendations to add to your checklist. This is not a fully comprehensive list of all of the things that are needed to be checked but does contain many of the items that should be checked during their initial work to reopen a building. This is not intended to be a substitute for professional medical or health advice.