To know CMMS meaning is the foundation for modern, data-driven maintenance. A computerized maintenance management system (CMMS) centralizes every asset record, work order, spare-parts count, and KPI in one cloud dashboard so teams can act fast, slash downtime, and extend equipment life.
No wonder the global CMMS software market is already worth about US $1.3 billion and growing at 11% annually, according to Grand View Research – as organizations shift from reactive fixes to proactive reliability programs [1].
For maintenance managers, facility leaders, and small-business owners still juggling spreadsheets or paper logs, understanding what a CMMS does – and why it matters – can unlock dramatic savings, safer workplaces, and a clearer path to Maintenance 4.0.
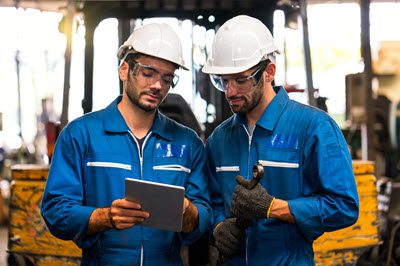
What Is A CMMS? Definition
The term CMMS stands for a computerized maintenance management system, and it refers to software that assists maintenance teams in managing assets, planning maintenance, and monitoring work orders. The system also includes features for condition monitoring, inspection management, checklists, KPI tracking, and accurate documentation of all maintenance activities – which is essential in heavily regulated industries.
What Does a Computerized Maintenance Management System (CMMS) Do?
Below are the core feature modules that give a computerized maintenance management system (CMMS) its real-world power.
Asset and Inventory Management
- Central Asset Register: Store make/model, BOMs, and lifetime cost history for every piece of equipment in one searchable hub.
- Bar-Code / QR Tagging: Scan from a phone to surface manuals, warranty dates, and open work orders in seconds.
- Dynamic Spare-Parts Tracking:On-hand counts auto-adjust as technicians issue or return parts; reorder points trigger POs.
- Cost Roll-ups: See total maintenance spend by asset, line, or site to guide repair-vs-replace decisions.
Why it matters: Eliminates spreadsheet drift and keeps audits painless.
Work Order Automation
- Smart Prioritization Engine: The CMMS scores requests by criticality, safety risk, and SLA, then schedules the right tech.
- Drag-and-Drop Calendar Managers can reshuffle tasks visually, with automatic crew notifications.
- Template Library and Checklists: Standardize PMs and inspections; technicians tick boxes on mobile for instant compliance proof.
- Real-Time Status Updates: Stakeholders see job progress (Assigned – In-Progress – Complete) without chasing emails.
Why it matters: Streamlined workflows trim admin time and boost wrench time.
Mobile and IoT Connectivity
- Offline-First Mobile App: Capture data in remote areas; syncs automatically once back online.
- Push Notifications & Geo-Locate: Route urgent jobs to the nearest qualified technician.
- Sensor and BMS Integrations: Pull vibration, temperature, or BAS alarms to create condition-based work orders – no manual entry.
- Voice-to-Text and Photo Annotations: Techs log findings hands-free and attach images for richer asset history.
Why it matters: Prepares your organization for predictive analytics and”Maintenance 4.0″.
How CMMS Software Works (Step-by-Step)
A CMMS acts as the “nerve center” that captures asset data, routes jobs to the right people, and feeds real-time insights back to managers.
Here’s the typical data flow you’ll experience with eWorkOrders:
Step | Description |
---|---|
Asset & Resource Data Capture | Import equipment records, bills of materials (BOMs), IoT sensor feeds, and spare parts counts into the CMMS to create a centralized asset database. |
Maintenance Request In-take | Work requests are submitted via desktop, mobile devices, or QR codes by staff, operators, or triggered by automated alerts. |
Smart Prioritization & Scheduling | The CMMS assigns a priority score based on asset criticality, checks technician availability, and schedules tasks automatically. |
Mobile Work Execution | Technicians receive digital work orders on mobile devices with checklists, diagrams, and parts lists to complete tasks efficiently. |
Inventory Auto-Reconciliation | As parts are used, inventory levels adjust in real-time, and reorder points can trigger automated purchase requests. |
Completion & History Logging | After completing the job, technicians log time-stamped notes, photos, and updates that become part of the asset’s historical maintenance record. |
Analytics ; Continuous Improvement | CMMS dashboards track KPIs like Mean Time to Repair (MTTR) and downtime. AI insights support ongoing maintenance strategy refinement. |
Companies that automate this loop cut emergency response time by 20% in the first year and extend asset life by up to 50%. The data in a CMMS system supports the many functions, which make it possible to do the following things:
Labor Resource Management
Employee personnel records can be tracked via the labor resource management module in CMMS software, including status, skill level, billing rate, contact information, and more. You can easily match employees or vendors to the assets they maintain, and assign tasks accordingly. You may monitor employee attendance, productivity, and overtime hours in addition to basic information.
Asset Register
Asset registers are management tools that are used to keep track of the assets that a company has. The capitalization policy of each business determines which assets should be listed in the asset register.
Maintain, share, and access detailed lists of compiled asset information including:
- Date of Purchase The moment the asset became the property of the business. The asset’s creation date could be another value
- Purchase Price: The amount paid by the business to acquire the asset. This valuation may include all relevant receipts from the item’s purchase for auditing purposes.
- Owner Of The Asset: As long as the asset is registered in that person’s or entity’s name, the asset owner could be an individual, a group of individuals, or even another entity.
- The Asset User: A person or group of people with the authorization to use the asset in the performance of their respective duties.
- The Manufacturer’s Warranty Information: This includes information on the asset’s original manufacturer, who guarantees the asset’s state at the time of purchase. Information might include how long an asset is acceptable for exchange or return.
- The Asset’s Barcode Or Serial Number: These parallel, machine-readable characters and numbers allow for speedy asset identification. Businesses provide their assets with distinctive barcode codes, which may be scanned to quickly find out further details on the asset.
- Asset Location: A description of the asset’s position on the business grounds. For instance, an LCD projector would most likely be located in the audiovisual room in a school setting.
- Asset Description: A basic description of the asset that simply explains what it is. Brief descriptions facilitate identification because some businesses give their products codenames.
- Insurance Coverage: Any type of asset insurance policy. To safeguard these assets from potential losses, businesses may get property insurance for their structures, such as fire insurance, flood insurance, or earthquake insurance.
- The Asset’s Current Value: The amount the owner could receive if they sold the asset as of the current date.
- The Depreciation Technique Applied: The method of depreciation used to determine the company’s losses after purchasing the asset.
- Maintenance Data: This could include information on how to fix the asset or a history of repairs or replacements. The names of people who fixed the assets as well as the invoices for their work may also be included.
- Asset Lifespan: How long an asset is expected to continue earning income for the organization. Of course, this value evolves with time.
- The Salvage Value Or Estimated Resale Value: The book value of an asset after depreciation has been fully incurred.
Asset Management Glossary of Terms and Definitions
Work Order Management
A Computerized Maintenance Management System (CMMS) Work Order may be a request for repair, restoration, or replacement of equipment or assets.
Work Orders typically include information such as:
- Work Order Number
- Description And Priority
- Order type (repair, replace, scheduled)
- Cause And Remedy Codes
- Who Is Requesting The Work Order
- Who Is Authorizing The Work Order
- Personnel Assigned
- How To Complete The Task, Including Necessary Parts And Other Notes
- When The Work Order Needs To Be Completed
- Where The Work Order Needs To Be Performed
- How To Complete The Task, Including Necessary Parts And Other Notes
Other features of Work Order Management include:
- Automate The Creation Of Work Orders
- Attach Any Relevant Documents, Repair, And Safety Materials
- Schedule And Assign Workers, Crews, And Shifts
- Review, Track And Manage Downtime
- Reserve Materials And Equipment
- Record Budget And Actual Expenses
- Manage Inventory
Preventive Maintenance Automates the start of work orders depending on usage, time, or triggered events. Preventive maintenance is used to organize and associate assets across multiple orders.
Inventory ManagementInventory, distribute and reclaim maintenance and repair operation (MRO) equipment and materials across storage areas, distribution centers, and facilities. Manage suppliers, monitor inventory expenditures, and automate restocking.
Reporting: Create reports for several maintenance categories, including supplier evaluations, material usage, labor and material expenses, and asset availability. Gather and arrange information for audits and analyze data to understand asset availability, performance trends, MRO inventory optimization, and other data to support business choices.
The Evolution Of CMMS Software
Before CMMS, obtaining centralized, dynamic visibility and automated management was impractical because maintenance information was buried in paper files, and later, scattered across spreadsheets.
Large businesses were often the primary users of the original CMMS systems, which first appeared in the 1960s. To update digital records and keep track of maintenance chores, technicians used punch cards and IBM mainframes. Punch cards were replaced by checklists that technicians entered into CMMS systems at the end of their shifts in the 1970s.
In the 1980s and 1990s, as computers became smaller, more accessible, more widely distributed, and more connected, CMMS became more common among small and medium-sized organizations. In the 1990s, CMMS started transferring data across LANs, or local area networks. Many of the new CMMS systems ran on one server but could be accessed from any terminal in the facility.
Intranets and web-based connectivity became more common in the 2000s, extending CMMS capabilities to a variety of mobile devices, field applications, and operational sites. This generation’s CMMS software ran on local servers, therefore upgrades had to be handled locally by the client, who typically watched over the process while vendors handled upgrades remotely using conference calls.
A cloud-based, highly mobile version of CMMS is currently available. Higher data security, quicker installation, and greater functionality are all features it offers. With cloud-based CMMS software, there is no need for complex server set-up and configuration; you simply sign up, log in and start using it immediately. This is because Cloud CMMS is built on multi-tenant architecture where everyone is sharing the same CMMS app with the same security, patches, upgrades, and feature set.
As it turns out, cloud-based software is more cost-effective, dependable, and secure. The application is stored on multiple devices on a virtual server, which means if one piece of hardware fails, another kicks in seamlessly with no loss of service. Automatic upgrades take place at predetermined intervals and are a hands-off approach.
CMMS vs EAM: What’s the Difference?
A CMMS is purpose-built for day-to-day maintenance – work orders, preventive schedules, spare-parts control, and technician mobility.
An EAM (Enterprise Asset Management) platform wraps those same maintenance functions inside a broader asset-lifecycle umbrella that starts with capital planning and stretches through decommissioning. It optimizes an asset’s life cycle in order to decrease the Total Cost of Ownership (TCO) and at the same time maximize overall asset productivity and Return on Asset (ROA).
Think of CMMS as the tactical “maintenance cockpit” while EAM is the strategic, enterprise-wide “asset command center”. Small and mid-sized operations usually choose CMMS because it deploys faster and costs less. Multisite enterprises or heavily regulated industries often opt for EAM to gain deeper financial, risk, and compliance controls.
Feature / Focus | CMMS | EAM |
---|---|---|
Primary Goal | Optimize maintenance execution | Optimize full asset lifecycle |
Core Modules | Work orders, PMs, inventory | CMMS + capital planning, risk, finance |
Typical Users | Maintenance and facility teams | Ops, finance, risk, executive leadership |
Deployment Time | Weeks | Months |
Up-Front Cost | Low to moderate (SaaS) | Higher (license + integration) |
Best Fit | SMBs, single plants, rapid ROI | Large enterprises, regulated sectors |
Example KPI | MTTR, downtime % | Asset ROI, total cost of ownership (TCO) |
Bottom line: Choose a CMMS when maintenance efficiency is your immediate priority; move to EAM when you need enterprise-grade financial and risk visibility.
Key Benefits
No matter how large or small your business is, CMMS software has a big impact on how companies manage their maintenance operations.
- Increased Productivity. The CMMS centralized system gives maintenance teams direct access to work orders, asset locations, inventory, documents, manuals, and more from a computer, Smartphone, or mobile device.
- Improved Workflow And Reduced Backlog. Less backlog due to better planning, organization, scheduling, and management of resources.
- Prolong Assets And Equipment Lifespan. Proper maintenance extends the lifespan of assets, reduces downtime, optimizes performance, reduces repair expenses, and improves reliability, which leads to an increase in ROI.
- Less Disruption In Business Operations. Planned and preventive maintenance schedules can be done at a time that is more convenient for business operations.
- Reduced Labor Costs. Having better control over resource scheduling reduces unnecessary overtime, and provides the ability to schedule skilled technicians.
- Spare Parts And Inventory Control. Set minimum and maximum inventory spare parts and stock levels, so that when the minimum quantity is reached a Purchase Order will automatically be generated and sent to vendors for replenishment. Reduces unnecessary costs and downtime.
- Document Management Control. Store and share documents, manuals, pictures, videos, and other information into the CMMS centralized system.
- Access From Anywhere. 24/7 access from a computer, Smartphone, or mobile device.
- Risks And Accidents Are Reduced. Properly maintained assets\equipment reduces the risk of accidents, and injuries, and minimizes the loss of work time and disruption in business operations.
- Better Control Of Budgets And Expenses. With a CMMS you have more control over maintenance budgeting for expenses such as labor, parts, and miscellaneous costs for the completion of work orders, and replacement of equipment at the end of its lifespan.
- Increase In Customer Satisfaction. A CMMS gives you a better view and control of your maintenance operations. Keeping assets/equipment running at peak performance provides a better customer experience.
- Compliance And Audit Preparation Streamlined. The data-tracking capabilities in a CMMS streamlines the data to generate accurate reports for inspections and compliance regulations.
- Quick Reporting And Analysis. Data can be pulled quickly and effortlessly from the CMMS for analysis. Accurate and reliable reporting helps organizations spot critical weaknesses, so solutions such as regular inspections, preventive maintenance, or spare parts can be put in place to proactively reduce downtime going forward.
- Measurement Of Success. CMMS solutions allow companies to collect maintenance information, turning historical data into insights for an in-depth understanding of how well their organizations are doing
Benefit | How It Helps |
---|---|
Cuts Unplanned Downtime by 30-50% | Automatic preventive scheduling and real-time alerts stop failures before they snowball. |
Boosts Technician Productivity up to 25% | Mobile checklists, bar-code lookups, and instant asset history mean less admin, more wrench time. |
Extends Asset Life 20-40% | Data-driven PM tasks and condition-based triggers slow wear, defer cap-ex, and improve OEE. |
Shrinks Spare-Parts Carrying Costs | Live inventory levels, reorder points, and audit trails keep parts budgets lean—no more over-stocking. |
Speeds Audit and Compliance Reporting | One-click exports for OSHA, ISO 55000, and FDA 21 CFR Part 11 slash prep time from days to minutes. |
Maintenance 4.0 Readiness | Native IoT connectors, AI failure predictions, and KPI dashboards position your team for predictive, connected operations. |
Improves Safety & ESG Scores | Safer assets mean fewer incidents, lower insurance premiums, and stronger sustainability metrics. |
Delivers Fast ROI (6–12 Months) | Most eWorkOrders clients recoup the subscription cost in the first year through downtime savings alone. |
Selecting CMMS Software: Factors to Take Into Account
It’s crucial to take support into account while choosing new CMMS software, in addition to functionality and technological aspects. Naturally, a maintenance management software solution should quickly address all of your functional requirements.
Some of the functions that you should consider:
- Flexibility
- License Pricing Model If Applicable
- Data Importation
- Training
- Technical support
- Software updates
- Security
- Customer ratings and reviews
CMMS Costs and Deployment Options
Before committing to a computerized maintenance management system, weigh how the deployment model – cloud SaaS vs on-premise license – affects both first-year and lifetime cost of ownership.
Cost Component | Cloud CMMS (SaaS) | On-Premise CMMS |
---|---|---|
Up-front license | $0 | From $10,000 one-time fee |
Monthly / annual subscription | $30–$150 per user / month | None (but see maintenance) |
Hosting and security | Included in subscription | Your IT budget (servers, backups, DR) |
Implementation and training | $2,000–$8,000 (scope-dependent) | $10,000+ (longer rollout) |
Software maintenance and updates | Included; auto-deployed weekly | 18–22% of license per year |
Typical payback period | 6–12 months | 12–24 months |
Best fit | SMBs, multi-site, rapid scaling | Heavily regulated or air-gapped plants |
Key Takeaways
- Cloud SaaS minimizes capital expense and delivers continuous upgrades – ideal for teams that need to deploy fast and stay current without extra IT overhead.
- On-premises suits organizations with strict data-sovereignty rules or limited internet access, but the higher up-front and ongoing maintenance costs extend payback time.
- Ask vendors for a total cost of ownership (TCO) worksheet that includes licenses, implementation, integrations, and internal labor so you can compare apples to apples.
Tip: eWorkOrders primarily deploys as a secure cloud CMMS, while on-premise installations are available for organizations that require local data residency or stricter compliance controls.
Maintenance KPIs to Track in Your CMMS
A CMMS turns raw work-order data into actionable metrics. Start with these five”north-star” KPIs – built-in to eWorkOrders dashboards – so you can prove ROI and drive continuous improvement:
KPI | What It Measures | Why It Matters |
---|---|---|
Downtime % | Total hours an asset is unavailable ÷ total scheduled hours. | Quantifies lost production; high downtime signals urgent reliability gaps. |
MTTR (Mean Time to Repair) | Average clock time to restore an asset after failure. | Gauges technician efficiency and spare-parts readiness. |
MTBF (Mean Time Between Failures) | Average operating time between two breakdowns. | Higher MTBF indicates more reliable equipment and effective PMs. |
Planned Maintenance % (PMP) | (Planned maintenance hours ÷ total maintenance hours) × 100. | Shows how proactive vs. reactive your team is; target > 80%. |
Schedule Compliance | Completed planned work orders ÷ planned work orders. | Reveals whether the team executes the maintenance plan on time. |
Tip: Set automatic CMMS alerts when any KPI drifts outside its target band – then drill down to the offending assets or work orders in one click.
CMMS Evaluation Checklist
Choosing the right CMMS can feel overwhelming. Use this 10-point checklist – pulled from hundreds of successful rollouts – to score each vendor side-by-side.
Evaluation Criterion | Ask the Vendor |
---|---|
Deployment Model Flexibility | “Can you offer cloud, on-premise, and hybrid deployment options, and may we switch later?” |
Ease of Use and Mobile Experience | “Will you walk us through a live demo on a phone or tablet so we can gauge usability?” |
Core Maintenance Modules | “Do you include work orders, preventive maintenance, inventory, and purchasing out of the box?” |
Integrations | “Which ERPs, building-management systems, IoT sensors, and SSO providers do you integrate with natively?” |
Reporting and Dashboards | “Can we create custom KPI widgets and export reports to PDF, Excel, and BI tools?” |
Implementation and Training | “What is the typical go-live timeline, and which training resources are included in the quote?” |
Data Migration and Security | “How will you migrate our legacy data, encrypt it at rest and in transit, and back it up?” |
Scalability and Multisite Support | “Can the platform handle unlimited assets, users, and multiple languages across sites?” |
Pricing Transparency | “Will you itemize license or subscription costs and disclose any potential hidden fees?” |
Vendor Support and Product Roadmap | “Do you provide 24/7 support, and can you share your roadmap for future feature releases?” |
Need expert guidance? Visit our services page or schedule a personalized CMMS demo and receive a quick, facility-specific ROI snapshot – no obligations.
Real-World CMMS Projects and Success Stories
Seeing a CMMS in action is often more persuasive than any feature list. Below are three documented wins from organizations that chose eWorkOrders.
Agriculture – Kings River Packing
- Challenge: Seasonal citrus grower relied on paper work orders and had no real-time inventory visibility.
- Impact: Unplanned downtime dropped sharply and productivity rose by about 75%; streamlined labor and parts control saved more than US $500,000 in the first year.
Manufacturing – Specialty Glass Producer
- Challenge: Reactive maintenance and scattered requests hindered ISO-9001 compliance and accurate cost tracking.
- Impact: Centralized work orders met audit requirements and enabled precise labor-cost allocation, cutting overall maintenance spend and supporting data-driven pricing.
Education – Multi-Campus School District
- Challenge: An outdated CMMS caused long response times, frequent emergencies, and limited reporting.
- Impact: Mobile eWorkOrders workflows shortened response times, shifted the team to proactive scheduling, and substantially lowered emergency repairs and total maintenance costs – delivering a safer learning environment.
Whether you manage harvest equipment, precision manufacturing lines, or an entire school district, eWorkOrders delivers rapid, verifiable ROI and scales easily across industries. You can browse many more success stories on our case studies page.
Next Steps: Get More from Your Maintenance Budget
If you’re ready to move from firefighting to proactive, data-driven maintenance, eWorkOrders can help. Our cloud-based CMMS gives you centralized asset histories, automated work-order scheduling, and KPI dashboards – without the long, expensive rollouts typical of legacy systems.
A quick walkthrough will show exactly how the platform fits your goals, budget, and IT environment, and it comes with a no-obligation ROI snapshot tailored to your facility. Book a CMMS Demo – it’s free, takes about 30 minutes, and could uncover thousands in hidden savings.
Frequently Asked Questions
What is an example of a CMMS?
eWorkOrders is a cloud-based CMMS that lets maintenance teams create work orders, schedule preventive tasks, track spare parts, and monitor KPIs from a single dashboard. Its flexible deployment options and intuitive mobile app make it suitable for organizations of all sizes, from single-site facilities to multisite enterprises.
Is CMMS the same as SAP?
No. A CMMS is purpose-built maintenance software, while SAP is a broad enterprise resource-planning (ERP) suite whose modules cover finance, HR, supply chain, and more. SAP can integrate with – or host – maintenance functions, but its scope and complexity go far beyond a typical CMMS.
What is CMMS skill?
“CMMS skill” refers to a technician – or manager’s ability to navigate the software: entering work requests, building preventive schedules, analyzing KPIs, and exporting reports. Strong CMMS skills translate into faster repairs, better asset data, and higher overall equipment effectiveness.
What are two types of CMMS?
The two most common deployment types are cloud/SaaS CMMS, delivered over the internet via subscription, and on-premise CMMS, installed on local servers with a perpetual license. Some vendors also offer hybrid setups that mix both models.