Preventive maintenance is critical to the longevity and dependability of any piece of equipment. Not only does well-maintained equipment save time and money, but it also ensures safety and productivity. Yet, keeping track of all the maintenance requirements for various types of equipment can be challenging. That is why having a comprehensive equipment preventive maintenance checklist can be quite beneficial. This checklist is intended to provide thorough guidelines to ensure that all equipment is routinely and adequately maintained, decreasing the chance of breakdowns, downtime, and costly repairs.
In this article, we will introduce you to the ultimate equipment preventive maintenance checklists that will ensure the seamless and efficient operation of your equipment. Additionally, as you read further, you will learn how utilizing preventive maintenance checklists can result in a significant reduction in equipment downtime, elimination of operational expenses, establishment of standardized workflows, increased ROI, and enhanced overall productivity
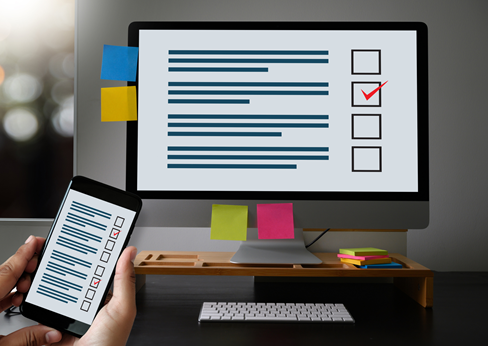
Preventive Maintenance Definition
Preventive maintenance is a proactive approach to equipment maintenance that involves regular inspections, cleaning, and servicing to prevent potential issues before they arise. The primary goal of preventive maintenance is to maintain equipment in optimal condition and functionality, reduce the likelihood of unexpected breakdowns, and extend its lifespan. This is achieved by performing routine maintenance tasks such as lubrication, part replacements, and repairs at scheduled intervals to prevent equipment failure and ensure its reliability and safety. Preventive maintenance is a crucial process that ensures equipment longevity and efficiency, reduces downtime, and improves productivity.
What Is A Preventive Maintenance Checklist?
A preventive maintenance checklist is a detailed record that lists a series of maintenance tasks for a specific asset. Its purpose is to guide technicians and maintenance teams in creating consistent and reliable maintenance procedures within a facility or enterprise. Typically, equipment manufacturers, consultants, or other relevant parties create the checklist, which serves as the foundation for any maintenance program. Maintenance teams are crucial in implementing the checklist and ensuring that all essential tasks are performed at the appropriate intervals. By adhering to the checklist, maintenance teams can help reduce the risk of equipment failure, prolong equipment lifespan, and enhance operational efficiency.
There are four key action items for any preventive maintenance program. Each of these items plays an important role in ensuring the success of a preventive maintenance program.
Inspection
Regular inspections of equipment and facilities are critical to ensure safety and proper functioning as intended by the manufacturer. Inspections help prevent workplace injuries and protect property, providing liability protection for businesses.
Detection
Preventive maintenance enables the detection of potential problems early before they become costly and difficult to fix. By adopting a proactive approach to maintenance, facility managers can save money and prevent downtime.
Correction
Facility managers must take prompt corrective action to address problems when they are detected, preventing further deterioration or disruption to operations. Preventive maintenance encourages a proactive approach to equipment care.
Prevention
Facility managers can identify and rectify repeated issues with equipment by keeping detailed inspection records and maintenance notes, preventing future failures. This approach reduces stress and increases productivity for facility teams, allowing them to focus on proactive maintenance tasks.
The Preventive Maintenace Pre-Checklist
Prior to initiating preventive maintenance, it’s essential to complete a pre-checklist containing fundamental information for any preventive maintenance plan. Here are some key actions to take:
Evaluate And Inventory The Current Condition Of Your Facility
Establish benchmarks for efficiency, quality, uptime, maintenance, and other essential metrics based on current performance. Gain a thorough understanding of every aspect of your facility that will undergo preventive maintenance.
Locate Documentation
For machinery, preventive maintenance can be done according to the manufacturer’s recommendations and specifications. Locate and review all relevant documentation.
Create Your Own Documentation
A preventive maintenance checklist for your facility is a good starting point and quick reference, but make sure to comprehensively document your preventive maintenance plan and processes in a location that all employees can access and review. Maintenance management software is a useful tool to comprehensively document your preventive maintenance plan and processes in one centralized location.
Refine The Key Performance Indicators (KPIs)
Base the preventive maintenance checklist on a cost/benefit analysis of previous preventive maintenance programs. Maintenance managers may opt for adjusting PMs and key performance indicators depending on company activities, conditions, and other factors.
Types Of Preventive Maintenance Checklists
There are several types of preventive maintenance checklists that can be used, depending on the specific needs of an organization. Some of the most common checklists include:
A Pass-Or-Fail Preventive Maintenance Checklist
Pass/fail checklists are commonly used for equipment inspections to detect early signs of trouble. Checklists are extremely beneficial for overseeing the state of important equipment, such as temperature, water pressure, or oil level, on a consistent basis. A pass/fail checklist, for example, could direct technicians to inspect the oil level and confirm that it falls within the acceptable range. The equipment passes the examination if the oil level is appropriate. If not, it fails, and a notification is sent to add more oil to the machine. On the other hand, a “fail” condition, such as a rise in temperature, could suggest an imminent malfunction, prompting maintenance staff to investigate further.
A Step-By-Step Preventive Maintenance Checklist
Step-by-step checklists are ideal for tasks that require more than just monitoring equipment conditions. They are especially helpful for preventive maintenance procedures that involve the replacement of belts, motors, or other equipment components. The step-by-step checklist offers detailed instructions on how to carry out each step of the task, guaranteeing that every technician follows the same process and completes all required steps. By following a step-by-step checklist, maintenance personnel can ensure that crucial maintenance procedures are consistently executed and carried out thoroughly.
Types Of Preventive Maintenance Checklists And Tasks
Below are some checklists for preventive maintenance of machines which may vary depending on the specific equipment, manufacturer’s recommendations, and other factors.
Preventive Maintenance For Machines
- Inspect and clean filters.
- Inspect and tighten bolts and nuts.
- Inspect safety guards and other safety devices.
- Inspect and clean mechanical brakes or clutches.
- Inspect cooling systems, such as radiators or fans, for debris or damage.
- Check for leaks in hydraulic systems.
- Check lubrication levels and refill if needed.
- Check for proper alignment and adjust as necessary.
- Check for proper pressure and flow rates for hydraulic and pneumatic systems.
- Check for unusual vibration, noise, or other signs of wear.
- Check and replace worn or damaged hydraulic fluid lines.
- Replace worn or damaged parts as necessary.
- Clean and lubricate chains, gears, and sprockets.
- Verify proper operation of safety interlocks and limit switches.
- Test the machine’s operation to ensure it’s functioning properly.
- Examine electrical connections and wiring for wear and damage.
- Ensure that machinery is clear of debris, before and after every shift.
- Wipe machine surfaces of lubricant, dirt, and other loose debris each day.
- Test backup systems, such as emergency stop buttons or backup power supplies.
- Verify the machine’s calibration if applicable.
- Verify proper operation of the machine’s control systems, including software updates and backups.
Preventive Maintenance For Material Handling Equipment
Below are just a few examples of preventive maintenance checklists for material handling equipment. The specific items on a checklist may vary depending on the equipment, manufacturer recommendations, and other factors.
Forklift Preventive Maintenance Checklist
- Inspect and clean air filters.
- Inspect and tighten bolts and nuts.
- Inspect brakes and replace worn or damaged parts.
- Check and adjust tire pressure.
- Check the battery and charging system.
- Check and replace worn or damaged forks.
- Check oil, hydraulic fluid, and coolant levels.
- Verify the proper operation of the lift mechanism.
- Test the horn, lights, and other electrical components.
- Test backup systems, such as the emergency brake or backup alarm.
Article: Common Forklift Problems & How To Avoid Them
Conveyor Preventive Maintenance Checklist
- Check belt tension and alignment.
- Clean and lubricate chains or sprockets.
- Check and replace worn or damaged belts.
- Verify proper operation of motors and drives.
- Replace worn or damaged parts as necessary.
- Inspect safety guards and other safety devices.
- Inspect and clean rollers, pulleys, and bearings.
- Inspect electrical connections and wiring for wear and damage.
- Test the conveyor’s operation to ensure it’s functioning properly.
Article: Conveyor Belt Maintenance CHecklist – Things You Shouldn’t Forget
Pallet Jack Preventive Maintenance Checklist
- Inspect and clean air filters.
- Inspect brakes and replace worn or damaged parts.
- Inspect and tighten bolts and nuts.
- Check and adjust tire pressure.
- Check oil and hydraulic fluid levels.
- Check the battery and charging system.
- Verify the proper operation of the lift mechanism.
- Test the horn, lights, and other electrical components.
- Test backup systems, such as the emergency brake or backup alarm.
Article:Maintenance Tips To Help Prolong The Lifespan Of Pallet Jacks
Preventive Maintenance For Facility Infrastructure
Below are a few examples of some items that can be added to a preventive maintenance checklist for facility infrastructure: It is important to consult with qualified professionals and follow manufacturer recommendations when developing a preventive maintenance program for facility infrastructure.
HVAC System Maintenance Checklist:
- Clean or replace air filters.
- Inspect and clean ductwork.
- Inspect and clean condenser coils.
- Inspect ductwork for leaks or damage.
- Inspect and clean drain pans and lines.
- Inspect and tighten electrical connections.
- Inspect and replace worn or damaged parts.
- Inspect and clean condenser and evaporator coils.
- Test and inspect thermostats.
- Test and calibrate thermostats
- Lubricate motors and bearings.
- Test safety switches and controls.
- Test and inspect refrigerant levels.
- Clean or replace air filters.
- Clean air filters and replace them as necessary.
- Check and adjust refrigerant levels.
Article: Commercial HVAC Maintenace Tips & Checklist
Plumbing System Maintenance Checklist
- Inspect and tighten electrical connections.
- Inspect and replace worn or damaged parts.
- Inspect and repair leaks in pipes and fixtures.
- Inspect and replace worn or damaged fixtures.
- Inspect and clean drains and traps.
- Inspect and test backflow preventers.
- Inspect and test water heaters.
- Test emergency shutoff valves.
- Test backflow prevention devices.
- Test and adjust the water pressure.
- Check for leaks and repair as necessary.
- Lubricate pumps and valves.
- Flush water heaters and tanks/
Electrical System Maintenance Checklist
- Inspect and replace worn or damaged wiring and cables.
- Inspect and replace worn or damaged breakers and fuses.
- Inspect and tighten electrical connections.
- Inspect and replace worn or damaged parts
- Inspect and test fire alarms and smoke detectors.
- Check and test emergency lighting systems.
- Test and calibrate electrical meters and instruments.
- Test and inspect uninterruptible power supplies (UPS).
- Test and inspect ground fault circuit interrupters (GFCIs).
Fire Protection System Maintenance Checklist
- Inspect and test fire pumps.
- Inspect and test fire alarms and smoke detectors.
- Inspect and replace worn or damaged parts.
- Test and inspect fire extinguishers.
- Test and inspect fire sprinkler systems.
- Test and inspect emergency lighting systems.
Security System Maintenance Checklist
- Inspect and test access control systems.
- Inspect and replace worn or damaged parts.
- Test and inspect surveillance cameras.
- Test and inspect alarms and intrusion detection systems.
Building Envelope Maintenance Checklist
- Inspect the roof for leaks or damage.
- Inspect and replace worn or damaged parts.
- Inspect windows and doors for leaks or damage.
- Seal gaps or cracks in walls, windows, and doors.
- Clean gutters and downspouts.
Elevator and Escalator Maintenance Checklist
- Inspect and test elevator and escalator controls.
- Inspect and replace worn or damaged parts.
- Inspect and test electrical panels.
- Inspect and test circuit breakers.
- Inspect and test grounding systems.
- Inspect and test emergency generators.
- Lubricate moving parts and adjust tension as necessary.
- Test and inspect emergency stop buttons.
Building Interior
- Inspect electrical receptacle cover plates for tightness and damage.
- Inspect cart casters for signs of wear.
- Examine the floors, ceilings, and walls for evidence of deterioration.
- Check for evidence of leaks.
- Check the condition and operation of toilets and showers.
- Check fire extinguishers and any firefighting equipment.
- Check doors for proper operation and make sure that exits are not obstructed.
- Check for garbage in storage areas.
- Check for evidence of insect or other pest infestation.
- Make sure that shelving is secure, organized, and labeled.
- Ensure work areas and walkways are clearly and visibly marked.
- Confirm that controls such as timers and photocells are functioning.
- Test smoke and carbon monoxide detectors.
- Test the fire alarm system.
Building Exterior
- Inspect the roof, cleaning it if necessary. Use the appropriate fall protection or prevention measures when working in high places.
- Inspect the stack and all roof penetrations.
- Check the condition of the paint and walls.
- Check for plants on the building and its foundation.
- Check the storm drains.
- Check trees to make sure that no branches are about to fall.
- Check that the area around the trash bins is clean.
- Look for broken windows, doors, and railings.
- Clean drains and gutters on the roof, testing downspouts and drains by flushing them with water.
- Make sure gutters are appropriately anchored.
- Remove any plant life growing on the roof.
- Clean up any broken glass or other debris.
- Examine the condition of the sidewalk, driveway, and parking lot.
- Examine the condition of any fencing.
Preventive Maintenance For Network And Data Systems
Below are some examples of items that you should consider adding to your preventive maintenance checklist for network and data systems. It’s important to consult with qualified IT professionals and follow manufacturer recommendations when developing a preventive maintenance program for network and data systems.
Server Room
- Inspect and clean server room floors, walls, and ceilings.
- Inspect and test UPS (Uninterruptible Power Supply) system.
- Inspect and test the HVAC (Heating, Ventilation, and Air Conditioning) system.
- Test the backup generator and verify fuel levels.
- Check for unauthorized equipment or devices.
- Check the server room temperature and humidity.
Network Equipment
- Inspect and clean switches, routers, and other network equipment.
- Inspect and replace worn or damaged cables.
- Test and inspect wireless access points.
- Test and inspect firewalls and security systems.
- Test and inspect backup power supplies.
- Review and update network documentation.
Data Storage And Backup
- Inspect and clean backup tape drives or other backup devices.
- Inspect and test data storage arrays.
- Inspect and replace worn or damaged storage media.
- Review and update backup and disaster recovery plans.
- Verify offsite storage of backup media.
- Test and verify backup schedules and logs.
Software
- Install the operating system and software updates.
- Inspect and maintain antivirus and malware protection.
- Review and update access control lists and user accounts.
- Test and verify remote access and VPN (Virtual Private Network) connections.
- Review and update software licensing and maintenance contracts.
Email And Communication Systems
- Inspect and clean email servers and other communication servers.
- Test and verify email backups and archives.
- Review and update email and communication policies.
Security And Access Control
- Test and verify access control systems.
- Inspect and test surveillance systems.
- Review and update security policies and procedures.
- Inspect and test intrusion detection and prevention systems.
Internet Connectivity
- Test and verify internet connectivity and speed.
- Review and update internet usage policies.
- Inspect and clean firewall filters and rules.
Cloud Services
- Inspect and test cloud-based services.
- Verify cloud service backups and archives.
- Review and update cloud service policies and contracts.
User Training and Education
- Conduct regular user training and education.
- Review and update user security policies and procedures.
Determine Frequency For Each Checklist
It is important to determine the appropriate frequency for each checklist to ensure proper maintenance and inspection of equipment.
Daily Checklists
These are typically used for quick inspections and safety checks, such as monitoring temperature or checking for potential hazards between shifts.
Weekly Checklists
These can include tasks related to daily checklists but don’t require as frequent completion.
Monthly Checklists
These often involve more thorough tasks such as replacing fluids or inspecting internal components.
Quarterly Checklists
These may involve third-party inspections to verify safety and industry compliance, while seasonal checklists may require changes in equipment for different weather conditions.
Annual Checklists
These may include more complex tasks like disassembling machinery to check for proper functioning.
By utilizing maintenance management software, such as CMMS, these checklists can be easily managed and scheduled for completion, ensuring equipment is properly maintained and downtime is minimized.
Steps To Build An Effective Maintenance Checklist
Equipment and Asset Identification
Generate a comprehensive list of all equipment and assets requiring maintenance. This will establish the scope of the checklist and guarantee coverage of all equipment.
Maintenance Task Determination
Identify the specific maintenance tasks for each piece of equipment based on manufacturer recommendations, industry standards, and organizational requirements.
Frequency Setting
Determine how often each maintenance task should be performed based on factors such as equipment type, age, usage patterns, and environmental conditions.
Responsibility Assignment
Assign the responsibilities of performing each task to specific individuals or teams to ensure that maintenance activities are completed consistently and on time.
Checklist Creation
Develop a clear, concise, and easy-to-follow checklist for each piece of equipment that includes maintenance tasks, their frequency, and the responsible parties.
Checklist Testing
Test the checklist to ensure that it includes all necessary tasks and is easy to use. Obtain feedback from maintenance personnel and adjust as necessary.
Checklist Implementation
Once the checklist is final, integrate it into your maintenance program. Train employees on how to use the checklist and make it easily accessible.
Review and Update
Regularly review the checklist to ensure its effectiveness and accuracy. Make changes as needed to reflect equipment modifications, usage patterns, or other factors that may affect maintenance requirements.
Benefits Of Preventive Maintenance Checklists
Overall, the use of preventive maintenance checklists is an important aspect of a comprehensive maintenance program, helping businesses minimize downtime, reduce costs, and improve safety and efficiency.
Enhanced Equipment Performance
By conducting regular inspections and maintenance, preventive maintenance checklists can help keep equipment in good working order, minimizing the likelihood of breakdowns and malfunctions.
Extended Equipment Lifespan
Preventive maintenance checklists can help identify issues early on, allowing for prompt repairs or replacements, which can ultimately prolong the lifespan of the equipment.
Improved Safety
Regular maintenance and inspections can help ensure that equipment is operating safely, minimizing the risk of accidents or injuries in the workplace.
Cost Savings
Preventive maintenance checklists can help businesses save money by reducing the need for expensive repairs, minimizing equipment downtime, and avoiding costly emergency repairs.
Compliance with Regulations
Many industries have specific regulations and standards that must be met, and preventive maintenance checklists can help ensure that equipment and facilities meet these requirements.
Increased Efficiency
Regular maintenance can help ensure that equipment is operating at optimal efficiency, which can lead to cost savings, improved productivity, and better performance.
Better Planning and Scheduling
With regular maintenance and inspections, businesses can plan and schedule maintenance activities more effectively, minimizing disruptions to operations and allowing for better resource allocation.
Improved Documentation
Preventive maintenance checklists help businesses keep detailed records of maintenance activities, providing a clear audit trail that can be useful for regulatory compliance, troubleshooting, and other purposes.
Increased Accountability
By assigning specific maintenance tasks to employees and tracking their completion through checklists, businesses can increase accountability and ensure that maintenance is performed consistently and on schedule.
Better Communication
Preventive maintenance checklists can help improve communication between maintenance personnel, managers, and other stakeholders by providing a standardized approach to maintenance activities and ensuring that everyone is on the same page.
Reduced Environmental Impact
By identifying and addressing issues early on, preventive maintenance checklists can help minimize the environmental impact of equipment and facilities, reducing energy consumption, emissions, and waste.
How eWorkOrders Can Help Streamline Your Preventive Maintenance Checklists
eWorkOrders is a comprehensive solution designed to streamline and optimize preventive maintenance checklists. It offers centralized checklist management, automation, and scheduling to ensure that maintenance tasks are consistently and punctually executed, mitigating the risk of equipment breakdowns and costly downtime. The software assigns responsibilities, maintains detailed documentation, and sends proactive notifications and alerts. With powerful analytics and reporting tools, eWorkOrders facilitates data-driven decision-making. Moreover, it offers customization options tailored to diverse checklist requirements, enhancing flexibility. Alongside its mobile accessibility and commitment to efficiency, eWorkOrders delivers a range of benefits, including reduced downtime, decreased operational costs, standardized workflows, improved ROI, and heightened productivity. Ultimately, eWorkOrders simplifies preventive maintenance, contributing to the safety, reliability, and optimal condition of equipment.
Final Thoughts
An efficient preventive maintenance checklist is crucial in maintaining equipment and facilities in their best condition. By setting the appropriate frequency for each checklist and customizing it to fit the unique requirements of your organization, you can significantly lower the risk of expensive breakdowns and operational interruptions. Employing a computerized maintenance management system (CMMS) like eWorkOrders is an effective means of managing checklists and ensuring that maintenance is performed consistently and on schedule. In addition, a CMMS can also facilitate work orders and asset management, allowing you to track maintenance tasks and repairs, schedule inspections, and monitor equipment performance over time. This level of insight can help you identify patterns and trends, enabling you to make informed decisions about when to replace equipment or upgrade assets, ultimately saving your organization time and money in the long run.
Additional Resources
CMMS Articles & Directories
Maintenance Terms & Definitions Glossary
Asset Management Glossary of Terms & Definitions
Customer Testimonials
Customer Case Studies
Disclaimer: The information provided in this article and the associated preventive maintenance checklists are intended for informational purposes only. These checklists serve as general recommendations for maintenance tasks and are not exhaustive. Actual maintenance requirements may vary based on specific equipment, manufacturer recommendations, industry regulations, and other factors. It is essential to consult with qualified professionals, including equipment manufacturers and industry experts, to develop and implement a comprehensive preventive maintenance program tailored to your organization’s needs.
While these checklists are designed to promote safety, improve equipment performance, and reduce downtime, they are not a substitute for professional maintenance and inspections. Users should exercise caution and follow all safety protocols when performing maintenance tasks and should seek professional assistance when necessary.
Any reliance on the information provided in this article and the associated checklists is at the reader’s discretion. The authors and publishers of this article do not assume any liability for any actions taken or decisions made based on the information presented herein. Readers are encouraged to verify the accuracy and applicability of the information to their specific circumstances and equipment and to seek professional advice as needed.