In recent years, the way organizations approach maintenance has transformed dramatically, driven by rapid technological innovation and the increasing need for efficiency in dispersed operations.
Traditional maintenance practices that relied heavily on on-site inspections and manual monitoring are giving way to smarter, more connected systems. Advances in IoT, AI, and predictive analytics now allow companies to oversee equipment health, track performance, and prevent failures without being physically present.
As industries adapt to hybrid work models and globalized supply chains, the ability to manage maintenance remotely has become not just a convenience but a necessity. This article explores the top trends shaping remote maintenance management in 2025 and how they are redefining operational excellence.TEXT
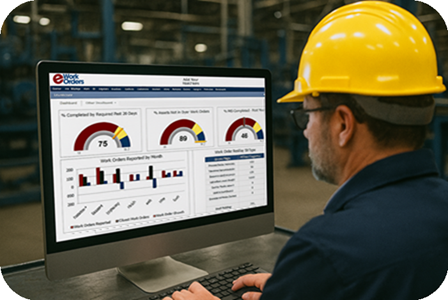
What Is Remote Maintenance?
Remote maintenance is the practice of servicing machines or systems from a distance using digital tools like sensors, cameras, cloud platforms, and artificial intelligence. It allows industries to monitor performance, detect issues, and carry out repairs without being on-site.
How does remote maintenance work?
Remote maintenance functions through a structured process that enables technicians to diagnose, monitor, and resolve equipment issues without being physically present. This approach combines advanced technology, secure communication, and real-time data analysis to ensure equipment remains operational with minimal downtime.
Real-Time Data Collection
The foundation of remote maintenance lies in continuous data gathering from equipment and systems. Modern industrial machines are fitted with sensors that capture vital information such as performance levels, operating conditions, temperature, vibration, and energy usage.
This real-time monitoring provides a constant flow of insights that helps detect subtle variations that might indicate wear, inefficiency, or upcoming failures. Without such live data, technicians would struggle to identify hidden issues, making predictive maintenance and timely interventions much more difficult to achieve.
Secure Transmission
Once the equipment generates performance data, it must be sent safely to a central monitoring system or cloud platform. Secure data transmission ensures that sensitive information remains protected from unauthorized access or tampering.
This process typically uses encrypted communication channels and strict authentication protocols, which safeguard operational details while allowing seamless access for authorized personnel. Organizations can then trust the information being analyzed and reduce risks associated with cyberattacks or technical disruptions in connected environments.
Analysis and Interpretation
After the data is transmitted, technicians and engineers rely on advanced analysis tools to study the information thoroughly. These tools include diagnostic software, predictive algorithms, and machine learning models that highlight irregular patterns or inefficiencies.
By comparing current performance data with historical benchmarks, they can spot early signs of malfunction before they escalate. This interpretation stage transforms raw data into actionable insights, enabling informed decision-making and precise maintenance strategies that minimize downtime, extend equipment life, and enhance overall operational reliability.
Remote Connection and Control
In cases where issues are detected, technicians can remotely connect to the equipment using secure access technologies. This connection allows them to observe real-time operations, run diagnostic tests, and make necessary adjustments without being physically on-site. They may fine-tune system settings, update software, or even restart specific components to restore performance.
Practical Applications of Remote Maintenance
Remote maintenance isn’t just a trend; it’s changing how industries operate. From manufacturing floors to hospital wards, businesses are leveraging digital tools to keep systems running smoothly with minimal downtime. Here’s how it plays out in key sectors.
Automotive
In the automotive industry, remote maintenance helps reduce downtime and ensures vehicles remain in peak condition. Through real-time monitoring and predictive maintenance, system components are continuously analyzed to detect performance issues or signs of wear before they lead to failures. Maintenance activities can be performed remotely or guided via mobile devices, providing technicians with real-time information to stay informed.
Aerospace
Remote maintenance plays a vital role in aerospace, where performance issues can directly affect safety and flight operations. Airlines rely on remote monitoring systems to collect real-time information from sensors embedded in aircraft. These systems transmit digital information securely, allowing technicians to detect anomalies, assess risks, and perform maintenance tasks remotely when possible.
High-Tech Manufacturing
In high-tech manufacturing, remote maintenance enables factories to remain efficient and productive while minimizing risks of defects or malfunctions. Augmented reality tools can guide on-site staff through routine maintenance activities using mobile devices or AR headsets, providing step-by-step instructions from a remote expert. Meanwhile, monitoring tools help identify issues arising in system components and enable swift troubleshooting without the need for an expert’s physical presence.
Healthcare
Medical equipment failure isn’t an option. Remote maintenance ensures that critical devices—like MRI machines and ventilators are continuously monitored. Automated alerts notify technicians of anomalies, allowing for immediate action. This not only keeps essential equipment operational but also improves patient safety by reducing unexpected breakdowns.
Facilities Management
From climate control to security, modern buildings depend on interconnected systems. Remote maintenance streamlines oversight of HVAC, lighting, and surveillance equipment, allowing facility managers to adjust settings, diagnose issues, and schedule servicing without being on-site. Data-driven insights also enable cost-effective maintenance planning, helping to prevent minor problems from turning into expensive repairs.
Key Trends in Remote Maintenance Management
Below are some of the key trends in remote maintenance management.
1. Predictive Maintenance with IoT
Waiting for equipment to fail is old-school. Predictive maintenance leverages IoT sensors to catch early warning signs, allowing teams to schedule fixes before disaster strikes. AI-powered analytics make this even sharper, analyzing vast data streams to highlight potential weak points. The result? Less downtime, fewer costly surprises, and a more efficient operation.
2. Cloud-Based CMMS Integration
Maintenance management without a cloud-based CMMS is like fighting with one hand tied behind your back. Today’s teams need instant access to asset data, work orders, and reports, no matter where they are. A centralized system allows seamless tracking and collaboration, ensuring nothing slips through the cracks.
3. Remote Troubleshooting and Diagnostics
Traveling to diagnose an issue is a waste of time. With remote access tools, technicians can assess problems in real time, cutting response times dramatically. Augmented reality (AR) solutions even allow field staff to get step-by-step guidance from experts without flying them in. Live data feeds, video calls, and remote control capabilities turn guesswork into precision troubleshooting.
4. Cybersecurity in Maintenance Operations
More remote access means more security risks. A single breach can cripple operations, making cybersecurity a non-negotiable priority. Multi-factor authentication, encryption, and routine software updates must be standard practice. Businesses that ignore these safeguards are playing a dangerous game.
5. Workforce Adaptation and Training
Digital tools are only effective if teams know how to use them. Training on IoT, cloud-based CMMS, and cybersecurity best practices ensures smooth remote operations. Mobile-friendly interfaces help workers stay connected, while clear communication protocols keep everyone on the same page. A tech-equipped workforce is the backbone of any successful remote maintenance strategy.
6. AI-Powered Maintenance
Artificial intelligence is transforming the way remote maintenance is carried out, shifting the focus from reactive repairs to proactive care. By applying machine learning models, organizations can detect early warning signs of equipment failure and address issues before they disrupt operations.
AI-driven predictive analytics not only reduces costly downtime but also ensures that maintenance schedules are optimized for efficiency. This leads to smarter resource allocation, improved diagnostic accuracy, and a significant boost in overall system reliability.
7. Remote Assistance through Augmented Reality (AR)
Augmented reality is rapidly becoming a valuable tool in remote maintenance. Using AR, a remote expert can guide on-site staff in real time, overlaying digital information onto physical system components. This ensures that technicians perform maintenance tasks accurately while reducing errors and downtime.
AR-based remote assistance also decreases the need for travel expenses and improves safety by limiting exposure to hazardous environments. The technology supports seamless collaboration, making it possible to resolve issues arising in remote locations quickly and effectively.
8. Remote Training
Virtual reality is transforming how technicians are trained by offering realistic and fully immersive environments. Instead of working directly on expensive or sensitive equipment, trainees can practice complex maintenance procedures in a virtual space without risk of damage or injury.
This approach not only lowers costs but also provides repeated practice opportunities, helping workers gain confidence before applying their skills in real-world situations. Remote training ensures consistency, accessibility, and efficiency, making it a powerful tool for technical workforce development.
9. Cost Savings Initiatives
Organizations are embracing remote maintenance practices to achieve significant cost savings. Travel expenses for on-site visits, along with the downtime associated with waiting for technicians, create unnecessary financial strain. By allowing equipment to be maintained remotely, businesses minimize idle time for their staff while improving productivity.
The ability to perform maintenance efficiently from a distance also enhances equipment reliability, ensuring fewer disruptions. As a result, companies reduce operational costs and achieve better long-term value from their systems and infrastructure.
10. Workforce Development
As remote maintenance technologies advance, the demand for highly skilled technicians and engineers will continue to rise. These professionals will need to not only understand traditional maintenance practices but also master the use of advanced digital tools and remote systems. To remain effective in their roles, continuous learning and professional development will become critical.
Ongoing training programs, certifications, and hands-on experience with emerging technologies will enable maintenance professionals to stay adaptable and thrive in an evolving, technology-driven landscape.
Remote Maintenance Best Practices
Follow the practices in this section to ensure that your IT infrastructure remains resilient, minimizes downtime, and adapts effectively to increasingly complex digital environments.
1. Secure Remote Access and Connectivity
IT teams need secure connections to monitor systems, resolve performance issues, and perform maintenance tasks without depending on on-site visits. To strengthen security, organizations should adopt Virtual Private Networks (VPNs) and two-factor authentication (2FA). Maintaining strong connectivity ensures that IT professionals can confidently manage remote locations, perform critical maintenance activities, and support system components consistently in real time.
2. Ensure Compliance with Regulations
Protecting sensitive data during data transmission is essential to avoid data breaches and maintain system integrity. IT teams should rely on encryption, secure access protocols, and layered authentication methods. Beyond security controls, compliance with standards such as HIPAA, PCI DSS, GDPR, SOX, NIST, and ISO 27001 ensures organizations follow proper guidelines when systems are maintained remotely.
3. Implement Proactive Monitoring and Alerts
Proactive monitoring plays a vital role in preventing issues before they disrupt operations. IT teams should implement continuous monitoring systems that provide real-time information on performance, resource use, and security concerns. Setting up alerts and notifications allows staff to stay informed about issues arising in remote systems and prioritize responses based on severity.
4. Ensure Patch Management and Updates
Failing to update software leaves systems exposed to cyberattacks and reduces reliability. That is why regular software updates and patch management are central to secure and stable IT operations. Scheduling and deploying updates remotely helps address vulnerabilities, enhance performance, and resolve bugs before they cause performance issues. Automated deployment tools and centralized management systems allow IT professionals to efficiently perform maintenance tasks across multiple endpoints.
5. Collaborate and Share Knowledge
Effective collaboration is a critical best practice for remote maintenance. Shared platforms and remote access tools allow multiple IT professionals to work on the same system simultaneously, improving efficiency and reducing response time.
Teams should also document and share best practices, solutions, and lessons learned through communication channels such as messaging groups or knowledge bases. This culture of collaboration ensures expertise is distributed across the team, empowering members to perform maintenance tasks more effectively and deliver stronger support to remote locations.
6. Select Tools that are Scalability and Easy to Integrate
Organizations should select tools that handle increasing endpoints, mobile devices, and system components without compromising performance. Equally important is integrating these tools with existing infrastructure to ensure seamless operations.
Compatibility with applications, operating systems, and hardware is essential for long-term effectiveness. By prioritizing scalability and integration, IT teams can support increasingly complex environments, maintain reliable remote monitoring, and future-proof their ability to perform maintenance efficiently across diverse environments.
Unique Insights from eWorkOrders
At eWorkOrders, we’ve seen industries transform with remote maintenance. Companies that adopted cloud-based CMMS early now handle maintenance with agility. The shift to real-time monitoring means fewer emergency repairs and more planned maintenance, reducing costs and stress.
One key lesson? Predictability beats reactivity. Businesses relying on spreadsheets and phone calls struggled with downtime, while those using automated alerts and sensor-driven maintenance stayed ahead of problems. The difference isn’t just convenience, it’s operational survival.
Another insight: remote maintenance isn’t just about technology; it’s about mindset. Teams that embrace remote tools and standardized workflows adapt faster. Those clinging to outdated manual processes waste time and resources. Our experience shows that structured, digital-first maintenance strategies lead to better asset reliability and lower long-term expenses.
The future of maintenance is remote, data-driven, and proactive. eWorkOrders CMMS makes this possible with advanced remote maintenance capabilities, giving teams the tools they need to monitor, track, and manage assets from anywhere.
Our CMMS software comes equipped with robust enterprise features, including spare parts inventory management, meter readings, GIS mapping, advanced filtering, system integration, and secure access through single sign-on.
It also supports predictive maintenance by leveraging condition monitoring techniques and sensor data to anticipate equipment failures before they occur. This proactive approach not only reduces unplanned downtime but also extends asset lifespan by ensuring maintenance is performed only when necessary.
The benefits to your company are measurable. Companies see significant improvements in overall maintenance efficiency, lower MTTR, and longer MTBF, all of which contribute to decreased monthly maintenance costs.
For businesses evaluating the right maintenance management software, eWorkOrders stands out as one of the top CMMS software solutions on the market. Managing maintenance tasks remotely? Learn more about how eWorkOrder remote worker CMMS solutions can help you.
Common Questions About Remote Maintenance Management
What is remote maintenance management?
Remote maintenance management is the practice of monitoring, troubleshooting, and servicing equipment from a distance using digital tools. It allows teams to handle maintenance tasks without being physically present, reducing travel time and increasing efficiency.
How does predictive maintenance help businesses?
Predictive maintenance uses IoT sensors and AI to detect early signs of wear or failure, allowing teams to address issues before they become costly breakdowns. This approach minimizes downtime, extends equipment lifespan, and optimizes maintenance schedules.
Why is cybersecurity important in remote maintenance?
More connected systems mean more potential vulnerabilities. Strong cybersecurity measures, such as multi-factor authentication, data encryption, and regular software updates, keep systems safe from cyber threats, preventing unauthorized access and data breaches.
What industries benefit most from remote maintenance?
Industries that rely on uptime and operational efficiency—such as manufacturing, healthcare, and facilities management- see the most significant benefits. Remote monitoring enables faster response times, better asset management, and reduced operational costs.
How can teams transition to remote maintenance?
Start by adopting a cloud-based CMMS for centralized task management. Integrate IoT monitoring for real-time equipment insights. You should train staff to use remote tools effectively. Small, incremental changes can make the transition smoother and more manageable.