What Is a Manufacturing Maintenance System?
A manufacturing maintenance system is a digital platform used to manage, track, and streamline maintenance activities across production equipment, assets, and facilities. It replaces traditional paper logs or spreadsheets with a structured approach that helps ensure machines are available, safe, and working at optimal efficiency. At its core, the system centralizes all maintenance tasks—whether reactive (fixing problems), preventive (scheduled upkeep), or predictive (condition-based interventions). It allows teams to schedule work orders, manage spare parts inventory, document inspections, and generate reports, all from one platform. Modern systems often come in the form of Computerized Maintenance Management Systems (CMMS) or Enterprise Asset Management (EAM) platforms. These tools are designed not just to support technicians in the field, but also to give operations managers and executives a clear, data-driven view of asset health, technician performance, and maintenance costs. A manufacturing maintenance system becomes especially critical in environments where production downtime translates to major losses. Instead of scrambling to fix issues after they occur, manufacturers can shift to a more strategic, proactive model that keeps operations running smoothly.Why Maintenance Systems Matter in Modern Manufacturing
In today’s manufacturing landscape, reliability is everything. Machines need to run consistently, operators need visibility into issues before they escalate, and decision-makers require real-time data to guide investments and operational choices. This is where a maintenance system becomes indispensable. Here’s why it matters:- Downtime is expensive: Every hour of unplanned downtime can cost thousands in lost productivity, missed deadlines, or even damaged reputation. Maintenance systems reduce this risk by scheduling preventive tasks and identifying patterns in failures.
- Workforce efficiency: Instead of relying on paper logs or tribal knowledge, technicians can access asset histories, maintenance checklists, and repair guides from a mobile device. This cuts guesswork and speeds up repairs.
- Asset longevity: Consistent upkeep prevents premature equipment failure, reducing the need for costly replacements and extending the life of critical assets.
- Compliance and safety: Regulatory bodies often require maintenance logs and audit trails. A digital system keeps all records in one place, ensuring compliance is seamless and verifiable.
- Scalability: As operations grow—across more shifts, more lines, or more sites—the system scales with it. You don’t need to reinvent the wheel each time you expand.
Types of Maintenance Approaches in Manufacturing
Maintenance Type | Description | Best For | Key Benefits |
---|---|---|---|
Reactive Maintenance | Run-to-failure; maintenance is only performed after equipment breaks. | Non-critical assets | Low upfront cost, simple to manage but high long-term risk. |
Preventive Maintenance | Time- or usage-based tasks scheduled at regular intervals, regardless of asset condition. | Predictable wear-and-tear equipment | Increases asset lifespan, reduces emergency repairs. |
Predictive Maintenance | Uses sensors and performance data to assess asset condition and trigger maintenance only when necessary. | High-value or high-risk equipment | Reduces unnecessary work, prevents surprise breakdowns. |
Prescriptive Maintenance | AI-driven; not only predicts issues but recommends actions based on historical and real-time data. | Advanced manufacturing environments | Optimized decision-making, efficient resource allocation. |
Key Features to Look For in a Manufacturing Maintenance System
Not all maintenance systems are built with manufacturing in mind. Some are too generic; others lack the depth to handle complex operations. When choosing a system, manufacturers should prioritize features that directly support day-to-day maintenance activities, data visibility, and plant-wide coordination.1. Work Order Management
Easily create, assign, prioritize, and track work orders. Technicians should be able to access instructions, attach photos, log time, and close out tasks from a desktop or mobile device.2. Preventive Maintenance Scheduling
Automate recurring tasks based on time intervals, meter readings, or usage thresholds. This ensures nothing slips through the cracks and reduces dependency on memory or manual reminders.3. Asset Management
Store detailed records of each asset—location, manufacturer data, service history, part requirements, warranty info. This data drives smarter decisions on repairs, replacements, and lifecycle planning.4. Parts and Inventory Tracking
Link parts to specific assets and work orders, track inventory levels, and generate automated reorder alerts. This reduces delays from missing parts and helps control procurement costs.5. Mobile Access
Maintenance doesn’t happen at a desk. Mobile-friendly systems allow techs to receive assignments, scan barcodes, and update records on the floor, in the warehouse, or out in the field.6. Dashboards and Reporting
Real-time dashboards show active work orders, asset health status, team workload, and KPIs. Custom reports help identify bottlenecks, justify budgets, and support audits.7. Integration with IoT and ERP Systems
Connecting with sensors, SCADA systems, or enterprise platforms (like SAP or Oracle) enhances automation and centralizes operational data. Choosing a system with these features sets up manufacturers to not only manage maintenance but continuously improve it.Common Maintenance Challenges in Manufacturing and How Systems Solve Them
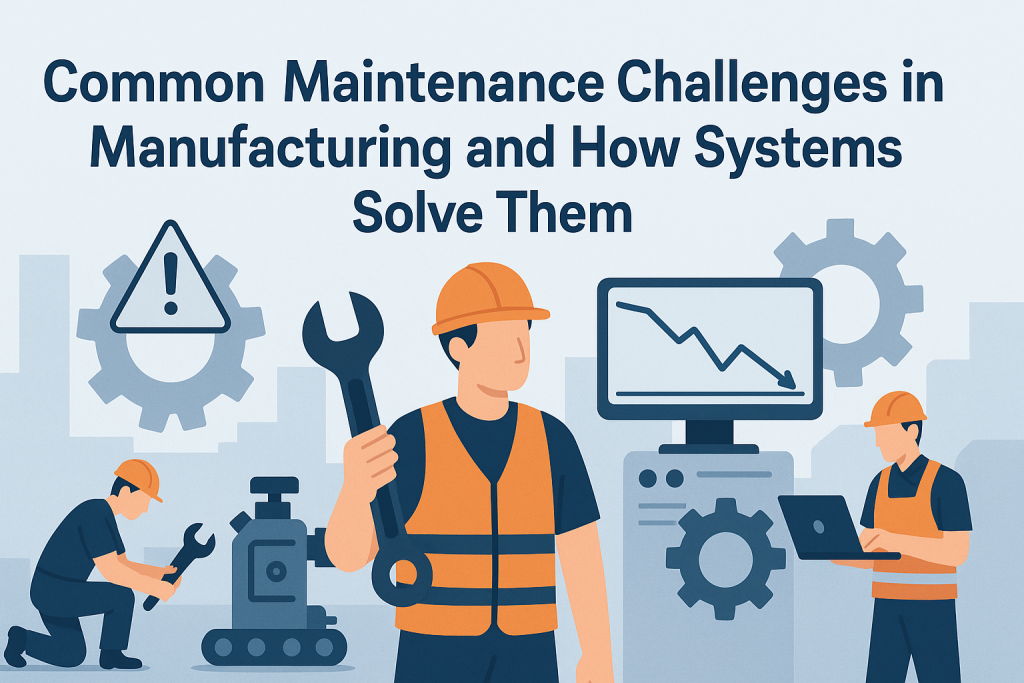
Challenge 1: Unplanned Downtime
Unpredictable breakdowns halt production and hurt delivery timelines. Maintenance systems address this by enabling preventive and predictive maintenance plans, so issues are addressed before they cause failure.Challenge 2: Poor Record-Keeping
Scattered data or missing logs make it hard to identify recurring problems. Centralized digital records give teams full visibility into each asset’s performance and repair history.Challenge 3: Delayed Repairs
Technicians waste time chasing approvals, locating manuals, or waiting for spare parts. A maintenance system streamlines these steps, automating approvals and making documents and parts lists readily accessible.Challenge 4: Inconsistent Maintenance Routines
Without standardized procedures, outcomes vary. Systems enforce checklists, ensure accountability, and help audit performance across shifts and teams.Challenge 5: Compliance Risks
Regulatory audits require complete maintenance logs and proof of inspections. A digital trail of all work orders, asset changes, and technician actions helps ensure smooth inspections and peace of mind. The right software doesn’t just store information—it actively resolves points of friction that stall operations.The Role of Automation and IoT in Maintenance Efficiency
Today’s manufacturers are leaning into Industry 4.0, and maintenance systems are evolving in step. Automation and IoT (Internet of Things) play a big role in how fast and accurately maintenance can be performed.Smart Sensors and Condition Monitoring
IoT sensors can monitor vibration, temperature, pressure, and other indicators in real time. These metrics feed into the maintenance system, which flags early signs of failure—often before a human would notice.Automated Alerts and Triggers
When thresholds are crossed (e.g. a motor overheating), the system can automatically generate a work order, notify the maintenance lead, or even shut down the machine to prevent damage.Predictive Maintenance with Machine Learning
Over time, data from assets, parts, and repairs train predictive models that identify which equipment is likely to fail, when, and why. The system becomes smarter, delivering better forecasts and helping teams focus on high-risk areas.Autonomous Scheduling
Some systems can dynamically assign technicians based on availability, skillset, and proximity—especially in large facilities. This minimizes idle time and balances workloads. By combining IoT capabilities with workflow automation, a modern manufacturing maintenance system shifts maintenance from reactive firefighting to intelligent, strategic operations.How eWorkOrders Stands Out as a Manufacturing Maintenance System
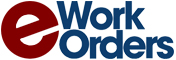
Intuitive Interface, Powerful Back-End
While many systems are clunky or require extensive training, eWorkOrders prioritizes a clean interface that new users can adopt quickly. At the same time, it offers powerful features like asset hierarchies, multi-site management, and deep analytics.Mobile and Cloud-First
Designed for field use, the system runs smoothly on tablets and smartphones. All data is stored securely in the cloud, giving maintenance teams access to real-time insights whether they’re on the shop floor or offsite.Tailored Preventive Maintenance Tools
With eWorkOrders, teams can automate recurring PM schedules, assign checklists, and set task triggers based on asset usage. These tools help reduce guesswork and ensure timely upkeep of critical equipment.Integrated Parts Management
The system keeps an up-to-date catalog of parts linked to each asset. This streamlines repairs, prevents delays, and supports better procurement planning.Flexible Reporting for Operations and Compliance
Managers can generate custom dashboards or export data to meet internal KPIs, maintenance audits, and industry-specific regulations. The reporting is flexible enough for both day-to-day ops and executive review.Fast, Low-Risk Implementation
Unlike many enterprise systems that take months to deploy, eWorkOrders offers rapid onboarding with minimal disruption. Its team works directly with manufacturing clients to ensure alignment with existing processes and goals. eWorkOrders isn’t just a tool—it’s a strategic partner for manufacturers ready to scale their maintenance programs intelligently.Implementation: What It Takes to Set Up and Succeed
Even the best manufacturing maintenance system can fall short without proper implementation. Success comes from more than software—it requires alignment across people, processes, and priorities.1. Start With Clear Goals
Define what success looks like: Is it reducing downtime by 20%? Improving PM compliance? Tracking repair costs by line or location? Clear metrics help shape system setup and post-launch evaluation.2. Audit Current Processes
Before migrating data, review how maintenance tasks are currently managed. Identify gaps, redundant steps, or pain points. This helps tailor the system’s configuration to reflect real workflows, not idealized ones.3. Train Technicians and Supervisors
Change management is key. Even with a user-friendly interface, teams need time to adopt new habits. Start with champions—experienced users who can help others—and schedule refresher sessions as needed.4. Import Assets and Schedules
Populate the system with detailed asset records, preventive maintenance routines, checklists, and any available historical data. This creates a strong foundation for accurate tracking from day one.5. Monitor and Adjust
After launch, track performance and user feedback. Tweak workflows, permissions, or report formats based on real use. Many teams discover they can optimize even further once they see how powerful the system is in action.6. Leverage Support and Upgrades
Use vendor support to troubleshoot quickly, stay updated on new features, and explore advanced tools like IoT integrations or API connections to other platforms. The transition doesn’t have to be disruptive. With the right guidance and goals, a manufacturing maintenance system can begin delivering ROI within weeks.Future Trends in Manufacturing Maintenance Technology
As manufacturing continues to evolve, so does the way maintenance is managed. The rise of smart factories, AI, and edge computing is reshaping expectations for what a maintenance system can do. Below are the key trends set to define the future of manufacturing maintenance.AI-Powered Predictive Maintenance
AI is already enhancing condition monitoring, but in the near future, it will do much more than flag anomalies. AI models will continuously learn from asset usage patterns, repair history, and environmental conditions to predict not just when a failure might occur—but how to prevent it entirely.Digital Twins
A digital twin is a virtual replica of a physical asset, updated in real time using sensor data. These models let maintenance teams simulate changes, test interventions, and anticipate breakdowns without ever touching the actual machine. As costs drop, digital twins are becoming more accessible—even to mid-size manufacturers.Edge Computing for Instant Response
Rather than sending all data to the cloud, edge devices process information locally at the machine level. This enables faster response times, reduced latency, and less reliance on stable internet connections—especially useful for time-sensitive equipment monitoring.Voice and AR-Assisted Workflows
Wearable devices and augmented reality (AR) glasses can overlay instructions directly onto the technician’s field of view. Paired with voice commands, this allows hands-free execution of complex maintenance tasks—ideal for high-risk or high-volume environments.Sustainability-Linked Maintenance
As manufacturers aim to meet ESG goals, maintenance systems will track metrics like energy usage, emissions, and waste. By maintaining assets efficiently, organizations reduce environmental impact—making sustainability a built-in outcome, not just an external target. These trends aren’t far off. Many are already being adopted by manufacturers who want to stay ahead of the curve. A flexible, modern manufacturing maintenance system is the foundation needed to adapt and thrive as these technologies become the standard.Conclusion
In manufacturing, margins are tight and expectations are high. Every hour counts, every machine matters, and every delay has consequences. A strong manufacturing maintenance system isn’t just about managing repairs—it’s about unlocking better performance across your entire operation. With the right system in place, teams respond faster, equipment lasts longer, and production stays on track. Downtime drops. Visibility improves. Budgets become more predictable. And when challenges do arise, you have the data and processes to respond with speed and precision. Whether you’re struggling with inconsistent maintenance, managing multiple sites, or simply ready to modernize your operations, now is the time to act. Explore how eWorkOrders can help you build a smarter, more efficient maintenance program tailored to your manufacturing needs. Book a demo today.FAQs
Maintenance plays a vital role in manufacturing by ensuring that equipment remains reliable, efficient, and safe to operate. Without proper maintenance, unplanned downtime can disrupt production schedules, increase operational costs, and reduce product quality. A proactive maintenance system helps extend asset life, improve safety standards, and keep manufacturing lines running smoothly—supporting both short-term performance and long-term profitability.
The most effective type of maintenance often depends on the specific context, but predictive maintenance is widely regarded as the most efficient and cost-effective approach. By using real-time data from sensors and performance metrics, predictive maintenance allows teams to intervene only when equipment shows signs of wear or failure. This minimizes unnecessary tasks while preventing major breakdowns, helping manufacturers strike the right balance between uptime and resource use.
Manufacturing maintenance includes all activities related to keeping production equipment and systems in optimal working condition. This covers everything from routine inspections and scheduled servicing to emergency repairs and part replacements. It also involves documenting maintenance history, monitoring asset performance, and ensuring compliance with safety and industry regulations. The goal is to maximize equipment availability and efficiency while reducing long-term costs.
Three of the most common maintenance problems in manufacturing are unexpected equipment failures, lack of consistent preventive routines, and poor tracking or documentation. Unplanned failures can lead to costly downtime, while missing regular upkeep shortens asset life and increases risk. Meanwhile, weak documentation makes it difficult to identify recurring issues, manage inventory, or demonstrate compliance during audits—all of which can hinder operational performance.