Maintenance can make or break an operation. When equipment fails, everything from productivity to safety and revenue is at risk. Yet many businesses still rely on outdated systems—spreadsheets, email chains, or paper logs—to manage increasingly complex maintenance demands. In today’s high-stakes environment, those methods don’t just fall short—they create costly blind spots.
This is where a CMMS system (Computerized Maintenance Management System) steps in. It’s not just a tool; it’s a shift in how maintenance is planned, executed, and improved. With a CMMS, organizations can automate tasks, track assets in real time, standardize workflows, and generate reports that support better decision-making.
Whether you’re overseeing a facility with thousands of assets or managing field teams across multiple sites, a CMMS system helps you move from firefighting mode to proactive control. It ensures your equipment gets the right attention at the right time—and that your team stays aligned, informed, and efficient.
What is a CMMS System?
A Computerized Maintenance Management System (CMMS) is software that centralizes all maintenance-related information to help organizations manage maintenance operations more effectively. It acts as a digital command center, giving maintenance teams the tools they need to plan, track, and analyze work related to assets, inspections, repairs, and more.
At its core, a CMMS stores detailed records of assets and their associated maintenance activities. It helps maintenance managers schedule tasks, track spare parts, automate routine inspections, and log technician work—all from a single platform.
Today’s CMMS systems are cloud-based, mobile-accessible, and often integrated with IoT sensors, ERP software, and other operational systems. This allows for real-time monitoring and automation, improving both responsiveness and long-term planning.
Organizations across manufacturing, facilities, energy, healthcare, and logistics rely on CMMS tools to increase asset reliability, reduce downtime, and gain operational visibility.
Core Components of a CMMS System
An effective CMMS system goes beyond simple task tracking. It offers a full suite of capabilities tailored to maintenance and asset-intensive environments:
Asset Registry
Every piece of equipment is logged with key data—make, model, serial number, location, usage hours, warranty, vendor details, and service history. This becomes a living record of each asset’s lifecycle.
Preventive Maintenance
Schedules can be set based on time, usage, condition, or custom triggers. Teams receive automated reminders, and checklists help standardize service tasks.
Work Order Management
Create, assign, and monitor work orders in real time. Attach manuals, safety documents, and photos. Technicians can mark completion and record observations through a mobile app or desktop dashboard.
Inventory and Spare Parts
Track spare parts stock levels, link parts to specific assets, and automate reordering when inventory runs low. This avoids unnecessary delays during repairs.
Vendor Management
Track third-party service providers, contractor work, contracts, and SLAs. This ensures outside maintenance is held to the same standards as internal teams.
Mobile Access
Technicians can access tasks, update records, and submit service details from the field. Mobile CMMS features like barcode scanning and photo uploads save time and improve data accuracy.
Analytics and Dashboards
Understand trends in downtime, maintenance costs, MTBF (mean time between failures), and MTTR (mean time to repair). Use this data for smarter planning and budget allocation.
Read more about Reporting, Analytics, and Dashboard Features.
CMMS Work Order System Explained
A CMMS work order system is often the most heavily used feature—and for good reason. It brings structure and clarity to every maintenance request and task.
When someone spots a problem, they can create a work request from any device. Once approved, it becomes a work order, with details about the task, assigned technician, priority level, required parts, and deadline.
Technicians receive the assignment in real time. They can view past work, check documentation, and mark the job as complete once done—all while in the field. This eliminates back-and-forth emails or paperwork and keeps the process moving.
Work orders are logged permanently, creating an auditable trail for compliance and review. Over time, patterns emerge: repeat issues, asset problem areas, underperforming teams, or seasonal spikes. That insight is what turns a basic work order system into a tool for continuous improvement.
Benefits of Using a CMMS System
Implementing a CMMS system creates value across the organization—not just for the maintenance department.
Reduced Downtime
By automating preventive maintenance and improving technician response times, CMMS systems significantly reduce equipment failures and production halts.
Increased Asset Longevity
Regular servicing, driven by CMMS reminders, reduces wear and tear. Assets last longer and perform better over time, reducing capital expenditure needs.
Streamlined Communication
Workflows are centralized. Technicians, supervisors, and stakeholders all view and interact with the same system, improving coordination and reducing miscommunication.
Cost Savings
CMMS systems help identify underperforming assets, overused parts, and labor inefficiencies. This data drives smarter budgeting and helps eliminate waste.
Improved Compliance and Audit Readiness
Digital records of inspections, repairs, certifications, and maintenance activities are stored automatically. This is critical for industries with OSHA, FDA, or ISO regulations.
Scalable Processes
Whether you manage a single plant or a network of properties, CMMS platforms scale with your operations, adapting to team size, asset complexity, and organizational growth.
Industries That Rely on CMMS Systems
CMMS systems are used widely, but here’s how they play out across key sectors:
- Manufacturing: Tracks machines, schedules line maintenance, and minimizes unplanned production stops.
- Facilities Management: Manages HVAC, elevators, lighting, and infrastructure across campuses or buildings.
- Healthcare: Ensures critical equipment (e.g., imaging machines) is always operational and compliant.
- Education: Coordinates facilities, IT, and safety maintenance across classrooms and campuses.
- Transportation & Logistics: Oversees fleet maintenance, warehouse systems, and spare parts inventory.
Each industry benefits in its own way—but the unifying theme is operational clarity, reduced downtime, and optimized resource use.
CMMS vs Other Maintenance Solutions (ERP, EAM, BMS)
While CMMS platforms are purpose-built for maintenance, they often get confused with other enterprise tools.
CMMS vs ERP
ERP systems like SAP or Oracle may have a maintenance module, but they’re typically finance-first and hard to customize for frontline teams. CMMS tools are technician-friendly, asset-centric, and focused on real-time execution.
CMMS vs EAM
Enterprise Asset Management (EAM) systems are broader, focusing on strategic planning, asset lifecycle costing, and risk forecasting. A CMMS, by contrast, is operational—it helps technicians do their jobs efficiently each day.
CMMS vs BMS
A Building Management System (BMS) automates HVAC, lighting, and utilities. While it can trigger alerts, it doesn’t manage tasks, inventory, or technician work. CMMS systems take those alerts and drive action.
In many organizations, a CMMS integrates with ERP, EAM, or BMS platforms to bridge operational and strategic functions.
Implementation Challenges and How to Overcome Them
Rolling out a CMMS system isn’t plug-and-play. Here are the most common obstacles—and how to address them:
- Resistance to Change: Train staff early, explain the benefits, and involve technicians in platform selection.
- Bad or Missing Asset Data: Conduct a physical audit before go-live. Input clean, accurate records into the new system.
- Over Customization: Avoid the temptation to tweak every field. Start with core workflows, then evolve.
- Underutilization: Assign internal champions, run weekly usage reports, and make the system part of daily habits.
A successful implementation is gradual, supported by leadership, and driven by a clear business case.
What Makes a CMMS System Effective?
Not all CMMS platforms are equal. The best systems consistently deliver long-term value because they’re built for real-world maintenance teams—not just IT buyers. Here are the traits that make a CMMS truly effective:
Intuitive Design
A clean, user-friendly interface ensures that technicians and managers can navigate the system quickly without long training. The best platforms offer simple navigation, drag-and-drop scheduling, and fast data entry.
Mobile-First Access
Modern maintenance teams are mobile. A strong CMMS should allow technicians to access work orders, scan assets, upload photos, and log tasks directly from their phone or tablet—even offline when needed.
Real-Time Updates
Work order changes, task completions, and asset status updates should sync instantly. This real-time visibility helps teams avoid duplication, respond faster, and reduce downtime.
Scalability
Whether managing 100 or 10,000 assets, the platform should stay organized and responsive. Multi-location support, user roles, and asset grouping help larger teams scale without chaos.
Advanced Reporting
The best CMMS platforms provide dashboards and automated reports that track KPIs like MTTR, labor hours, and asset downtime. This data helps teams make better decisions and demonstrate ROI.
Easy Integrations
A CMMS should connect seamlessly with ERP, SCADA, procurement tools, and BMS systems. Integration ensures maintenance stays aligned with finance, operations, and compliance teams.
Configurable Without Being Complicated
You should be able to adjust workflows, templates, and fields without a developer. Effective systems offer flexibility without adding unnecessary complexity.
Strong Support
Responsive customer service, clear documentation, and ongoing updates make a big difference—especially during rollout or scale-up.
About eWorkOrders CMMS System
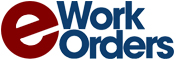
eWorkOrders is a cloud-based CMMS platform trusted across industries like manufacturing, property management, healthcare, and education. It offers a full suite of tools that simplify maintenance and asset tracking—while remaining accessible and easy to use.
Key features include asset lifecycle tracking, real-time work order creation, preventive maintenance scheduling, inventory management, and mobile access. Technicians can upload photos, scan barcodes, complete inspections, and close work orders on the go.
What sets eWorkOrders apart is its fast deployment, flexibility, and top-tier customer support. The platform integrates smoothly with other systems and includes customizable dashboards for data reporting and trend analysis.
Organizations using eWorkOrders report reduced downtime, better audit readiness, and improved team accountability. It’s particularly effective for businesses with complex, distributed maintenance needs and teams that need a reliable system in the field.
Request a free demo of eWorkOrders to see how it can streamline your maintenance operations.
Conclusion
A CMMS system doesn’t just organize maintenance—it transforms how teams operate. It eliminates guesswork, reduces breakdowns, and makes every maintenance dollar go further. In fast-paced, asset-intensive environments, that’s a serious advantage.
If your organization is still relying on spreadsheets or outdated processes, it’s time to move forward with a smarter, scalable system.
Request a free demo of eWorkOrders and explore how it can help you take full control of your maintenance operations—today and into the future.
FAQs
One widely adopted CMMS platform is eWorkOrders, which enables organizations to manage preventive maintenance schedules, track work orders, store asset histories, and ensure compliance from a centralized dashboard. It’s used across industries including manufacturing, healthcare, education, and property management. The platform is known for its ease of use, mobile accessibility, and strong customer support. By digitizing maintenance operations, eWorkOrders helps reduce downtime and improve asset performance.
No, SAP is primarily an ERP (Enterprise Resource Planning) system. While it offers a Plant Maintenance (PM) module that covers some maintenance functionality, it’s not a purpose-built CMMS. SAP PM is more complex to configure and lacks the hands-on, technician-friendly interface that dedicated CMMS platforms provide. For day-to-day maintenance operations, most teams prefer using standalone CMMS tools that are more intuitive and easier to deploy.
The “best” CMMS depends on the size of your operation, asset complexity, team structure, and industry needs. Top-rated systems include eWorkOrders, Fiix, UpKeep, and Limble, each offering unique features like mobile-first design, customizable workflows, and real-time analytics. For smaller businesses, ease of setup may matter more, while larger enterprises often need advanced integrations and reporting tools. It’s important to demo multiple platforms and choose the one that fits both your current and future needs.
The two primary types are on-premise and cloud-based CMMS systems. On-premise systems are installed locally on your organization’s servers and may offer more control but require more IT maintenance. Cloud-based systems, on the other hand, are accessed via browser or app and are generally easier to implement, update, and scale. Most modern organizations are moving toward cloud-based CMMS due to lower setup costs, remote access, and automatic updates.