Maintenance is rarely glamorous—but it’s often the backbone of reliable operations. And yet, for many teams, maintenance remains disjointed—scattered across sticky notes, spreadsheets, walkie-talkie updates, and unread emails. That’s where a dedicated work order system changes the game.
When done right, a digital work order system helps maintenance teams respond faster, plan smarter, and reduce friction between departments. It enables technicians to stay focused on what they need to do, while supervisors gain the clarity to improve overall performance. And for the wider business, it offers peace of mind that nothing’s being left to chance.
This article explores how work order systems help organizations streamline maintenance, what features actually make a difference, and how teams can use these tools to improve day-to-day reliability. We’ll also highlight how eWorkOrders—one of the most versatile and well-regarded systems in the space—helps maintenance teams simplify the complex and deliver results without added overhead.
Why eWorkOrders Stands Out
eWorkOrders was developed with the understanding that maintenance needs aren’t universal. The demands of a small university facility are different from those of a multi-site manufacturer or a public utility.
What ties them together is the need for:
- Quick response times
- Clear task visibility
- Accountability across teams
The platform supports all of these needs without becoming overly complex, offering flexibility that suits both small operations and large, multi-site organizations.
A Clean Interface That Makes Work Easier
At the heart of eWorkOrders is a user-friendly interface that simplifies the entire maintenance process. Users can quickly create, assign, track, and close work orders from one central system. Technicians in the field and supervisors in the office can stay aligned, with everything logged, timestamped, and searchable—eliminating the need for email updates or manual follow-ups.
Mobile Access for Field Technicians
With mobile access, technicians can receive tasks, check asset histories, upload photos, and close out jobs without heading back to a desk. This is particularly useful in industries where response time and documentation are critical—such as healthcare, manufacturing, and municipal services. Real-time updates help teams move faster and keep records accurate.
Interested? Learn more about our mobile maintenance.
Real-Time Dashboards and Custom Reporting
eWorkOrders makes it easy for supervisors and decision-makers to see what’s going on. The platform offers clear, customizable dashboards that show task progress, overdue work, asset performance, and more. Instead of managing multiple spreadsheets or chasing paper records, everything needed is available in one up-to-date system.
For a deeper understanding, check out our employee management.
More Than Just Work Orders
The platform connects with the wider scope of maintenance management. It integrates with inventory systems, asset tracking, and compliance modules, making it easier to prepare for audits, manage spare parts, and track equipment lifecycles—all within a few clicks.
Reliable Support and Ongoing Improvements
Support is one of eWorkOrders’ strongest qualities. Users often highlight:
- Responsive and helpful customer service
- Hands-on onboarding support
- Regular feature updates based on user feedback
This helps teams stay productive without getting stuck when issues arise.
Ready to Improve Maintenance Efficiency?
See how eWorkOrders can help your team streamline operations, stay on top of tasks, and make smarter decisions. Book a demo today to experience the platform in action.
The Challenge of Disorganized Maintenance
For many organizations, maintenance doesn’t break down because of bad intentions—it breaks down because of bad systems.
Category | Issue/Challenge | Explanation | Impact |
---|---|---|---|
Operational Inefficiencies | Disjointed Task Tracking | Tasks are forgotten, repeated, or half-completed due to unclear communication. | Leads to wasted time, missed maintenance, and inefficiencies. |
Visibility Gaps | No Clear Task Status | Teams don’t know what has been done or what’s pending. | Makes coordination and accountability difficult. |
Ripple Effects | Minor Issues Escalate | Small unresolved issues like a broken light signal larger problems. | Erodes trust, delays response, affects team morale. |
Preventive Maintenance Risks | Missed Scheduled Checks | No system to track and enforce recurring tasks. | Increases risk of major failures and unplanned downtime. |
Technician Burden | Lack of Clarity & Tools | Technicians lack context, task history, or knowledge of required parts. | Wastes technician time and creates inefficiencies. |
Reputation of Maintenance | Perception as Unreliable | Teams see maintenance as slow, unresponsive, or reactive. | Hurts morale, limits budget approvals, and reduces cooperation. |
Solution Provided | Centralized Work Order System | All tasks are logged, assigned, prioritized, and tracked in one place. | Improves transparency, efficiency, trust, and team performance. |
What Makes a Good Work Order System?
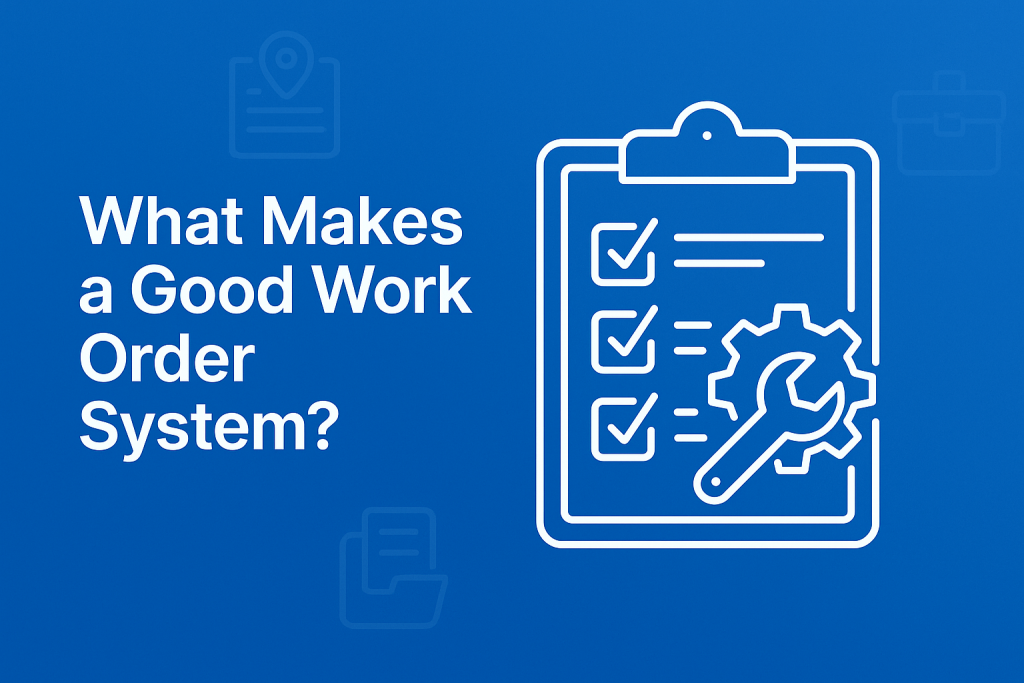
Not all work order systems are created equal. Some are little more than glorified to-do lists. Others are overly complex—built with so many features that everyday tasks become harder, not easier. The best systems find the balance: powerful enough to support complex teams, simple enough to use every day without friction.
So, what separates a good work order system from one that slows you down?
A solid system typically includes:
- Straightforward scheduling and assignment tools: Work orders should be quick to generate and assign. You shouldn’t need five clicks to log a leaking valve or schedule a technician. The interface needs to prioritize speed and clarity, especially during busy hours or emergencies.
- Real-time updates and mobile access: Field technicians shouldn’t have to return to a desk to close a job or check their next assignment. A mobile-friendly system allows them to view work orders, update statuses, upload photos, and flag new issues directly from the field.
- Detailed asset histories: Being able to see past work orders, notes, and recurring issues for an asset gives context. It saves time, avoids repeat mistakes, and helps teams identify long-term trends or root causes.
- Customizable workflows and forms: Maintenance looks different across industries—and sometimes even between two buildings in the same company. Good systems offer flexibility to tailor fields, approval chains, and notification settings.
- Inventory and spare part tracking: Work orders don’t operate in a vacuum. A great system will connect with inventory, so technicians know if the parts they need are available, or if a procurement step is required before a repair can happen.
- Role-based permissions: Not everyone needs the same level of access. Supervisors may need full visibility, while technicians just need task details. Role-based permissions keep the interface clean and secure for every user.
- Support for different maintenance types: Whether it’s reactive work, scheduled PMs, or predictive alerts tied to sensor data, the system should be able to manage them all under one roof.
But functionality alone doesn’t make a system successful.
A good work order platform also understands its users. It should help teams get more done without forcing them to change everything about how they work. That means:
- A fast learning curve.
- Minimal data entry to complete a task.
- Clean navigation that surfaces key information upfront.
- Notifications that prompt the right action—without overwhelming inboxes or dashboards.
At the heart of it all is this: a good system doesn’t just organize work. It improves it. It guides teams toward consistency, makes outcomes measurable, and gives every technician the tools they need to succeed.
Moving Beyond Paper: Benefits of a Digital Work Order System
For decades, maintenance teams managed with clipboards, binders, and whiteboards. And for some, those methods still feel dependable—until they’re not. When an urgent task is misfiled, or a technician can’t access a record because it’s in a locked office, that system shows its limits.
Switching to a digital work order system isn’t about chasing trends—it’s about enabling visibility, structure, and responsiveness in a way paper never could.
With a digital system, teams gain:
Benefit | Description | Impact |
---|---|---|
Centralized Visibility | All work orders are stored in one system, accessible to supervisors and technicians alike. Includes task details, checklists, and asset history. | Reduces confusion, improves coordination, and ensures everyone is on the same page. |
Reduced Communication Lag | Real-time updates and mobile notifications replace in-person updates or delayed calls. | Speeds up task handoffs and decision-making, keeping workflows moving. |
Stronger Accountability | Tasks are assigned with timestamps and tracked to completion, including responsible parties. | Improves transparency, performance management, and trust within teams. |
Cleaner Documentation & Audit Trails | Every job leaves a complete digital record (task details, parts used, timestamps, personnel). | Simplifies audits, warranty claims, compliance checks, and dispute resolution. |
Consistent Procedures | Templates ensure recurring tasks are done the same way each time, with clear steps. | Reduces training time, lowers human error, and standardizes quality of work. |
Automated Reporting | Built-in tools generate reports on technician performance, asset reliability, and recurring issues. | Saves time and provides insights for continuous improvement and budget planning. |
The shift away from paper also changes the culture of maintenance.
Work becomes more proactive. Tasks aren’t just logged—they’re anticipated. Preventive maintenance gets done on time because it’s scheduled and reminded automatically. Reactive work becomes easier to triage, thanks to better data and prioritization tools. Teams stop running from crisis to crisis and start building reliability into every part of their workflow.
It’s not just about being faster. It’s about having a system that reduces friction and builds clarity into everyday decisions.
Paper may have worked in the past, but as operations scale or grow more complex, the margin for error shrinks. A digital work order system keeps everyone aligned—even as buildings expand, teams grow, or new regulations roll in.
Inside a Modern Maintenance Workflow
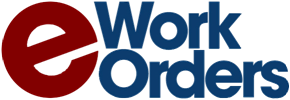
A good maintenance workflow is more than a checklist—it’s a rhythm. One that allows teams to respond quickly when things go wrong, but also ensures routine work is carried out before problems appear. With a digital work order system, this rhythm becomes repeatable, trackable, and easy to improve over time.
Here’s how a modern workflow typically unfolds:
1. Work Request Submission
It often starts with a request—something noticed by a team member, reported through a portal, or flagged automatically by a monitoring system.
- Digital portals allow employees, tenants, or supervisors to submit requests instantly.
- Fields can capture the issue description, location, asset ID, and urgency.
- Optional photos or attachments add context, helping technicians arrive prepared.
The system captures everything in one place, removing the guesswork and follow-up emails that typically clog the process.
2. Work Order Generation
Once reviewed, the request becomes a work order. This step formalizes the task, assigns it a unique ID, and ensures it enters the team’s queue.
- Supervisors can assign priority levels and due dates.
- The system can automatically route requests based on location, asset type, or technician skillset.
- Recurring tasks—like monthly checks or inspections—can be auto-generated on a schedule.
This stage introduces structure. Rather than reactive scrambling, work is distributed thoughtfully across available resources.
3. Assignment and Scheduling
The supervisor or system assigns the work order to a technician—or a team—and schedules it within their calendar.
- Technicians are notified on their mobile device.
- Details include location, asset information, checklists, safety instructions, and any past service history.
- The scheduler can balance workloads across multiple people, teams, or shifts.
Everyone knows what they’re doing, when, and why. No need for last-minute phone calls or paperwork drop-offs.
4. Execution and Documentation
Once the technician begins the task, everything happens in the system.
- Status updates reflect when a job is started, paused, or completed.
- Technicians can upload photos, record actions taken, and leave comments.
- Spare parts used are logged automatically from inventory (or requested if unavailable).
This not only streamlines the task but builds a record—one that’s valuable for future diagnostics or audits.
5. Review and Closure
Supervisors review the completed work order. If all checks are met, the task is closed. If not, it can be returned with comments or flagged for follow-up.
- Metrics like time-to-complete and technician performance are recorded.
- Reports are updated in real time, feeding into dashboards and analytics.
- If needed, recurring work orders can be triggered for future intervals.
What used to be an informal process becomes a clean, data-backed loop. Tasks are no longer buried in paperwork or lost in someone’s inbox.
Conclusion
Maintenance doesn’t have to be a reactive scramble or a frustrating tangle of missed tasks and miscommunication. With the right work order system in place, it becomes something else entirely: a source of stability, clarity, and control.
If your current process feels scattered, slow, or hard to scale, now’s the time to explore what a purpose-built platform can do.
eWorkOrders helps organizations of every size bring structure and speed to their maintenance operations—with tools that are flexible, intuitive, and proven in the field. Whether you’re managing a few assets or coordinating across dozens of facilities, eWorkOrders gives you the visibility and control you need to get ahead of the curve.
Book a demo with eWorkOrders to see how your team can streamline maintenance and work smarter.
FAQs
A work order system is a digital tool used to create, assign, track, and document maintenance tasks. It replaces manual methods like paper logs or spreadsheets with a structured platform that offers real-time visibility and control. This helps teams avoid missed tasks, respond faster to issues, and build a reliable maintenance process that supports long-term operational efficiency.
A good work order system automates recurring preventive tasks by scheduling them in advance and sending timely reminders to technicians. It ensures that nothing falls through the cracks—even when workloads are high. Over time, this reduces the likelihood of breakdowns, extends asset life, and cuts down on emergency repairs.
Even small teams benefit from having a structured system in place. It removes the guesswork from task assignments, ensures issues are logged and tracked properly, and provides a historical record of what’s been done. Most platforms, including eWorkOrders, scale well—from single-facility teams to enterprise-level operations—making them a valuable investment regardless of size.
Look for ease of use, mobile accessibility, asset history tracking, and the ability to automate recurring tasks. It should support real-time updates, offer clear reporting, and integrate with other parts of your operations, like inventory or compliance workflows. A system that fits your team’s habits—not one that forces a complete overhaul—will drive the most adoption and value.