What is 5 Whys Root Cause Analysis?
5 Whys root cause analysis is a straightforward problem-solving technique that uncovers the underlying cause of a problem by asking “why?” iteratively—typically five times—using verifiable evidence. Teams map cause-and-effect to a single, actionable root cause, then assign, implement, and monitor corrective actions to prevent recurrence and improve reliability.
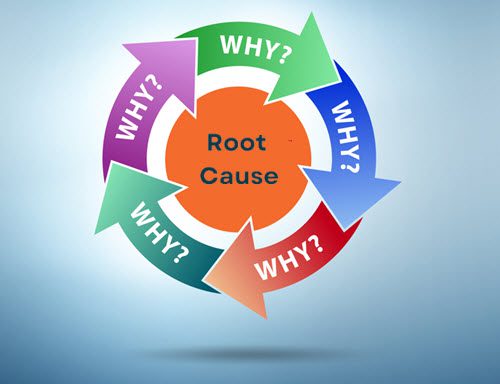
What Is the Goal of Root Cause Analysis?
The goal of root cause analysis is a permanent fix and prevention—not quick symptom-patching. By using fact-based methods like 5 Why RCA, teams in maintenance, operations, and quality align on the true cause, implement corrective and preventive actions, and verify outcomes to stop issues from recurring.
In practice, RCA aims to:
- Pinpoint the underlying cause with evidence (not opinions).
- Translate findings into corrective actions with clear owners and due dates.
- Update standard work/PM tasks to prevent recurrence.
- Monitor results (e.g., recurrence rate, MTTR) and adjust if needed.
- Document the trail for traceability, training, and audits.
A root cause analysis is a proactive approach to quality—it strengthens audit readiness, reduces compliance risk, protects customer satisfaction (fewer defects, fewer delays), and lowers total cost of ownership. That’s why root cause analysis is important across maintenance and QA.
Why Root Cause Analysis Is Important (Business & Quality Impact)
Understanding why root cause analysis is important comes down to prevention, performance, and proof. Put simply, a root cause analysis is a proactive approach to quality—it finds and fixes the underlying cause so problems stop repeating, operations stabilize, and customers see consistent results.
- Reduced downtime & cost: Eliminates repeat failures, cutting unplanned stops, rework, scrap, and rush parts/labor. Expect improvements in MTTR/MTBF, asset availability, and total cost of ownership.
- Higher first-time fix & reliability: Clear causes translate into precise corrective and preventive actions, boosting technician effectiveness and line stability.
- Compliance & audit readiness: Fact-based investigations create a traceable record (problem → causes → actions → results) that satisfies regulators, customers, and internal audits.
- Proactive quality: Shifts teams from firefighting to prevention—updating SOPs, training, and PM tasks so the fix is baked into standard work.
- Customer impact & safety: Fewer defects and delays mean better on-time delivery, fewer complaints/returns, and lower risk events—protecting both brand trust and workplace safety.
- Cross-functional alignment: Maintenance, operations, and QA rally around shared evidence and KPIs (recurrence rate, defect rate, downtime minutes), ensuring improvements sustain over time.
The 5 Whys Method in Action
Exploring the 5 Whys method entails persistently questioning “why” in various ways to reveal the underlying cause of a problem. As an example, a manufacturing company faces delays in product delivery. The investigation progresses:
- Why did the production delay occur?
- Due to a machine breakdown.
- Is there visible or measurable evidence supporting this root cause determination?
- Could another “why” lead to a more plausible root cause?
- Could anything else have contributed to this problem?
- Why did the machine break down?
- The motor malfunctioned.
- Is there visible or measurable evidence supporting this root cause determination?
- Could another “why” lead to a more plausible root cause?
- Could anything else have produced this problem?
- Why did the motor malfunction?
- Lack of lubrication.
- Is there visible or measurable evidence supporting this root cause determination?
- Could another “why” lead to a more plausible root cause?
- Could anything else have contributed to this problem?
- Why was lubrication neglected?
- Absence of a routine maintenance schedule.
- Is there visible or measurable evidence supporting this root cause determination?
- Could another “why” lead to a more plausible root cause?
- Could anything else have produced this problem?
- Why is there no maintenance schedule?
- Reliance on outdated manual processes.
- Is there visible or measurable evidence supporting this root cause determination?
- Could another “why” lead to a more plausible root cause?
- Could anything else have contributed to this problem?
Recognizing the iterative nature of the 5 Whys, it’s essential to pose crucial questions after each iteration to ensure a comprehensive and grounded analysis.
When to Use 5 Whys (and When Not To)
Use 5 Whys when you need a fast, fact-based read on a problem that likely has a single dominant cause. It shines in day-to-day operations where speed, clarity, and prevention matter more than exhaustive analysis.
Use 5 Whys when…
- The issue is simple to moderately complex with a likely single causal chain.
- It involves human/process factors (handoffs, SOP gaps, unclear checks, training).
- You see recurring minor failures (e.g., mislabeled parts, missed lube intervals, wrong setpoints).
- Data is available to verify each “why” (logs, timestamps, sensor readings, work orders).
- You can translate the root cause into actions (standard work, PM task, checklist).
Examples: repeated late starts on a line due to missing changeover tools; recurring barcode misreads traced to worn labels; repeated bearing heat due to skipped lubrication.
Use with other tools for broader cause discovery
- Pair with Fishbone/Ishikawa to brainstorm categories (Methods, Manpower, Machines, Materials, Measurement, Environment).
- Use Pareto charts to prioritize which problems to run 5 Whys on.
- Add 5 Hows to convert the confirmed root cause into concrete corrective actions.
Escalate beyond 5 Whys when…
- Problems are multi-factor/complex (controls + mechanical + supplier variability).
- Stakes are high (safety, regulatory, customer impact) and require formal investigation.
- You need probabilistic or systems analysis (e.g., FMEA, Fault Tree, A3, DOE).
Rule of thumb: if you can’t validate each why with evidence—or you end up with multiple competing root causes—zoom out with Fishbone first, or switch to a deeper RCA method.
How to Run a 5 Whys RCA (Step-by-Step)
Use this practical flow to turn 5 whys root cause analysis into repeatable results on the shop floor and in the field. It blends eWorkOrders’ existing guidance with a clear, role-based process you can run in any stand-up or huddle.
Assemble the team & define the problem (with data)
Facilitator (keeps pace/no-blame), Process Owner (area/line lead), Maintenance Tech/Engineer, and QA/Quality Rep (add Operator/Safety as needed).
- Write a tight problem statement: asset/line, location, time window, observed symptom, impact.
- Pull evidence: CMMS history, logs/timestamps, sensor trends, photos, checklists, scrap/rework counts.
- Set scope & success criteria: what “fixed” looks like, when you’ll review results.
Ask “Why?” up to five times (fact-based, no blame)
- Start from the observed effect and ask “Why?”
- Write each answer underneath the previous one—one cause per line.
- Validate every link with evidence (data, observations, standards).
- Keep it process/system-focused, not people-focused; avoid jumping to solutions.
- Stop when reaching a cause that, if addressed, prevents recurrence.
Identify the root cause & verify
- Test the hypothesis: quick checks, trials, or historical comparisons.
- Look for sufficiency: does addressing this cause plausibly stop the issue without creating new ones?
- Cross-check with QA/operations; confirm standards/specs were clear and available.
- If multiple plausible causes emerge, branch and verify each or zoom out with Fishbone.
Translate to corrective actions (5 Hows)
Use 5 Hows to move from cause → concrete actions:
- How will we fix it now? (containment)
- How will we prevent it? (standard work, PM task, poka-yoke)
- How will we train/communicate?
- How will we measure? (MTTR, MTBF, recurrence rate)
- How will we sustain? (audits, leader standard work)
Assign owners, due dates, and evidence required. Create and assign tasks directly from findings with our work order software.
Document, implement, and monitor results
- Record the full chain (problem → Why1–Why5 → actions), attach photos/logs, and link to affected assets in your CMMS.
- Implement & verify: check completion quality, not just status.
- Monitor KPIs: recurrence rate, MTTR/MTBF, defect/scrap trends, downtime minutes.
- Schedule a check-back (e.g., 30–45 days) to confirm the fix held; if not, iterate.
Best Practices for 5 Why RCA
Use these habits to make 5 whys root cause analysis fast, fair, and effective—every time.
- Distinguish causes vs. symptoms; verify with data. Challenge each “why” with logs, timestamps, photos, and specs; don’t accept opinion-only answers.
- Keep scope tight. Define the asset, time window, and impact; avoid premature convergence, and allow more than five whys if the chain warrants it.
- Focus on processes/systems, not people. Maintain a no-blame tone and encourage cross-functional input (operations, maintenance, QA, safety).
- Visualize and document thoroughly. Use a whiteboard or digital board to map the chain; record evidence, decisions, owners, and due dates for traceability.
- Validate every link. If a “why” can’t be backed by evidence, pause and investigate before moving on.
- Stop at an actionable root cause. Choose the point where a concrete corrective action will prevent recurrence, not just reduce symptoms.
Common Pitfalls (and How to Avoid Them)
Even well-run sessions can drift. Use this checklist to keep your 5 whys root cause analysis sharp—and know when to switch tools.
- Oversimplifying complex issues
Do instead: Scope first. If you see multiple causal branches, expand with a Fishbone/Ishikawa diagram, then run 5 Whys on the top candidates. - Stopping at the first plausible cause
Do instead: Require evidence for every link (logs, photos, specs). Ask, “What data would disprove this why?” - Confirmation bias (pet theories win)
Do instead: Involve cross-functional reviewers (Ops, Maintenance, QA). Assign a facilitator to challenge assumptions and seek counter-examples. - Blaming people, not processes
Do instead: Reframe to system/standard work (SOPs, checklists, visual controls). Address training and clarity of specs. - Vague problem statements
Do instead: Define asset/line, time window, observed effect, and impact—plus a measurable success criterion. - No owner / no due date
Do instead: Assign a single owner per action with a clear due date; track handoffs and escalation paths. - No monitoring or follow-up (issues reoccur)
Do instead: Set a check-back date and watch recurrence rate, MTTR/MTBF, defect/scrap. Compare pre/post results. - Incomplete documentation
Do instead: Record the full chain (Problem → Why1–Why5 → Actions) with attachments/evidence for audit and training.
When to escalate beyond 5 Whys
Move to Fishbone, FMEA, or A3 if:
- Multiple root-cause branches remain after validation.
- The problem spans mechanical + controls + supplier interactions.
- Safety/regulatory/customer risk is high and requires formal rigor.
- Data conflicts or you can’t verify each “why” with objective evidence.
From Insight to Action: Closing the Loop in CMMS
Turn your 5 whys root cause analysis into lasting results by operationalizing the fix inside your systems—not just on a whiteboard.
- Standardize the fix. Update SOPs/standard work, add visual controls or poka-yokes, and include any training steps required.
- Create preventive tasks. Add PM jobs with clear frequencies, skills, and meter/usage triggers; link tasks to specific assets so they appear on the right schedules.
- Issue corrective work orders. Assign owners, priorities, and due dates; capture materials/tools needed for execution using our work order software (assignment + traceability).
- Attach evidence. Include photos, specs, drawings, torque values, and acceptance criteria so technicians know exactly what “good” looks like.
- Track completion and verify. Require closure notes and a check-back date (e.g., 30–45 days) to confirm the issue does not recur.
- Monitor KPIs in your system of record. Use your CMMS to store the RCA record, link actions to assets, and track MTBF, MTTR, recurrence rate, labor hours (and downtime minutes) over time.
- Audit and sustain. Keep an auditable trail of decisions and outcomes; if metrics drift, revisit the chain and adjust the standard work/PM plan.
FAQ
What is 5 Why root cause analysis?
5 whys root cause analysis is a simple, evidence-driven method that uncovers the underlying cause of a problem by asking “why?” iteratively—typically five times. Teams document each cause-and-effect link, then implement and verify corrective actions that prevent the issue from recurring.
What are the 5 steps of root cause analysis?
A practical flow is: (1) define a clear problem statement and scope, (2) gather data/evidence, (3) ask “Why?” up to five times to trace cause-and-effect, (4) identify and verify the root cause, and (5) translate findings into corrective/preventive actions with owners, due dates, and follow-up checks.
What is the 5 why standard?
There isn’t a formal global “standard”; 5 Whys is a widely used Toyota-origin technique. The accepted practice is to ask successive “whys,” keep answers fact-based and no-blame, record one cause per level, and stop when reaching an actionable cause that—once fixed—prevents recurrence.
What is the 5 Whys checklist?
A useful checklist includes: concise problem statement, Why 1–Why 5, evidence/data for each link, the corrective action, owner, due date, and a check-back date to confirm the fix holds. Many teams also note impacted assets/SOPs and the KPI to monitor (e.g., recurrence rate, MTTR/MTBF).
What is the primary objective of the 5 Whys method in root cause analysis?
The 5 Whys method aims to uncover the underlying causes of problems or incidents by repeatedly asking “why.” It delves beyond surface-level symptoms to identify the fundamental issues at the core of a problem.
How does the 5 Whys method contribute to transformative maintenance practices?
The 5 Whys method acts as a catalyst for organizational change by revealing hidden layers of root causes. It propels organizations towards a preventive maintenance mindset, minimizing future breakdowns and fostering sustained operational excellence.
Can the 5 Whys method address complex problems with multiple root causes?
While the 5 Whys method is effective, it may oversimplify complex problems by implying a single root cause. To mitigate this, it is essential to approach it with flexibility and be open to other problem-solving techniques when complexities arise.
How does the 5 Whys method contribute to continuous improvement in maintenance operations?
The 5 Whys method, when used in conjunction with routine performance testing, ensures that potential bottlenecks and areas for optimization are identified. This proactive approach contributes to continuous improvement, handling increasing maintenance data efficiently.
What is the significance of blending the 5 Whys method with other problem-solving techniques?
Blending the 5 Whys method with other techniques creates a comprehensive approach to tackling problems. This synergy enhances the depth and effectiveness of root cause analysis, providing a strategic tool for addressing maintenance challenges.