Every minute a production line stalls, money bleeds. Siemens reports unscheduled downtime now drains 11% of annual revenue—roughly $1.4 trillion—from the world’s 500 largest manufacturers, and in automotive plants, it can burn $2.3 million for each idle hour [1].
The proven cure is a preventive maintenance software. This is a computer program specially designed to make the planning and execution of preventive maintenance tasks easier and more efficient. It is usually a CMMS (Computerized Maintenance Management System), including a “maintenance plans” functionality.
It replaces costly reactive firefighting with data‑driven foresight, keeping your critical assets running when profits depend on every second, and building the resilient maintenance culture modern facilities demand. This article shows you how.
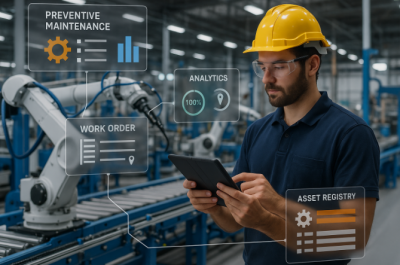
Why Every Facility Needs a Proactive Mindset
Firefighting after equipment breaks is painfully expensive. Reactive work orders cost three to four times more than proactive maintenance across an asset’s life cycle. At the same time, 82% of organisations still suffer unplanned downtime that derails production and slices margins, according to Empowering Pumps [2].
Adopting a preventive mindset flips the equation, otherwise known as the maintenance maturity curve. Climbing each rung leads to increased reliability while shrinking maintenance spend as a share of asset value.
- Run‑to‑failure – chaos and premium call‑out fees.
- Time‑based preventive–scheduled servicing curbs surprises.
- Condition‑based – sensors trigger work exactly when needed.
- Predictive optimisation – analytics forecast issues before they bite.
McKinsey reports that companies that progress to levels 3–4 shave up to 40% off maintenance spend, boost reliability key performance indicators (KPIs) by double digits, and reclaim valuable production hours [3].
How Preventive Maintenance Software Works
Imagine a digital control tower for maintenance. The following four stages are the core loop a modern CMMS follows:
Asset Registry
Every piece of equipment—machines, HVAC units, vehicles—goes into an asset registry with make, model, criticality, and service history.
Triggers
These are time‑based, meter‑based, or condition‑based rules—calendar dates, meter readings, or sensor thresholds—that tell the system exactly when service is due.
Work Order Execution
When a trigger fires, the platform auto‑creates a work order, routes it to the right technician, and reserves the parts.
Analytics and Reporting
Built‑in analytics crunch every completed job to spot failure patterns, calculate mean time between failure (MTBF), and forecast budgets.
Together, these four stages form the “plan → do → learn → improve” cycle that turns raw maintenance data into proactive action.
Automating Work‑Order Scheduling
A good preventive maintenance management software engine acts like a personal assistant for your calendar. Time‑based rules handle weekly inspections; meter‑based rules fire after 5000 run‑hours, and condition‑based rules listen to vibration or temperature sensors so you only service when it matters.
That precision pays off: IoT‑enabled maintenance cuts downtime up to 50% and trims costs 20‑30% in 2025 benchmark studies [4]. Freed from manual scheduling, planners can focus on continuous improvement instead of chasing missed tasks.
Asset and Parts Tracking in One System
An integrated CMMS pairs each asset with its Bill of Materials (BOM) and matches work orders to live inventory levels. Barcode or RFID scans update stock in real time, helping teams hit parts parity—just enough inventory, never too much. Faster parts also push mean time to repair (MTTR) down and production back up.
Real‑Time Mobile Access for Technicians
Out on the floor—or 20m up a cooling tower—techs need data, not desk PCs. Mobile CMMS apps deliver offline checklists, instant photo uploads, and push alerts that keep everyone synced.
QR‑code scans pull up manuals in seconds, while safety prompts ensure lock‑out/tag‑out steps are logged before a single bolt is turned. The result: safer jobs, quicker fixes, and richer data flowing straight into the analytics loop.
Five Business Results You Can Measure
The best part about implementing preventive maintenance software is the clear, trackable return on investment (ROI). It doesn’t just “feel” more efficient—it delivers hard numbers you can take to the boardroom. Here are five high-impact outcomes you can expect, based on industry benchmarks and real-world case studies.
Extend Asset Life Cycles | Proactive care can extend equipment life by 20–40%, particularly when lubricants, filters, and calibration are handled on time [3]. This slows depreciation, reduces capex frequency, and keeps your critical machines operating at peak for longer. |
Slash Unplanned Downtime | Each minute of unplanned downtime can cost manufacturers an average of $22,000. Automated triggers and alerts see unplanned downtime fall, keeping production lines humming. |
Automate Compliance and Safety | Keeping up with OSHA, ISO 55000, and internal EHS standards is easier when inspection logs, safety checklists, and audit trails are automated. No more chasing paperwork or scrambling during audits—everything is documented and time-stamped. |
Boost Technician Productivity | A modern preventive maintenance management software chops emergency call‑outs. Technicians follow scheduled workflows instead of chasing breakdowns, freeing time for training, root‑cause analysis, and ongoing improvement. |
Improve Operational Efficiency and ROI | Companies running equipment preventive maintenance software hit the sweet spot, improving both margins and equipment availability across the board. |
Choosing the Right Preventive Maintenance Software
Selecting the best equipment preventive maintenance software means matching features to your organization’s size, processes, and growth plans. Use this quick checklist to evaluate vendors:
Scalability
Can it handle 50 assets today and 5,000 next year?
Deployment Model
SaaS vs. on‑premises—consider IT resources, security, and uptime requirements.
Integrations
Look for prebuilt connectors to ERP, IoT platforms, and financial systems to avoid data silos.
Usability
A modern UI, drag‑and‑drop scheduling, and quick mobile access reduce training time and boost adoption.
Support and Training
24/7 helpdesk, online knowledge base, and professional services ensure you hit the ground running.
Must‑Have Features | Nice‑to‑Have Innovations |
---|---|
An automated scheduling engine that handles time, meter, and condition triggers. | IoT sensor integration for live condition monitoring. |
Mobile application with offline mode and push notifications. | AI‑driven failure prediction to flag risks before they occur. |
Analytics dashboard with real‑time KPIs (MTTR, MTBF, downtime). | Digital twin support to simulate scenarios and optimize maintenance plans. |
A vendor portal for streamlined spare‑parts ordering and warranty tracking. | Augmented reality (AR) guides for hands‑free repairs and training materials. |
Special Considerations for Small and Mid‑Sized Businesses
For smaller operations, tight budgets and limited IT resources make rapid results essential. Preventive maintenance software for small companies should offer:
- Low up‑front costs – look for subscription pricing that scales with your asset count.
- Quick deployment – cloud‑hosted solutions eliminate lengthy installations and hardware investments.
- Minimal IT overhead – automatic updates and built‑in security let you focus on maintenance, not system upkeep.
- User‑friendly setup – preconfigured templates and intuitive workflows mean technicians are productive from day one.
- Flexible licensing – add or remove users and modules without costly renegotiations.
These SaaS advantages democratize industrial‑grade CMMS tools, so even a 20‑person shop can benefit from enterprise‑level capabilities. If you need help implementing quickly, explore our services for expert onboarding, configuration, and training tailored to your scale and goals.
Implementation Roadmap: 30‑60‑90 Days to Proactive Maintenance
To turn your preventive maintenance vision into reality, follow a structured 30‑60‑90 day plan that balances quick wins with sustainable change.
Days 1–30: Foundation and Alignment
Asset audit and data cleanup
Conduct a thorough inventory of all assets, tag them with unique identifiers, and import existing service histories into the CMMS. Cleaning up legacy spreadsheets and removing duplicate records ensures your new system starts with reliable, actionable data.
Stakeholder kickoff
Bring maintenance, operations, procurement, and IT together in a workshop to agree on top‑priority KPIs (e.g., MTTR, uptime targets) and define roles. Early engagement builds shared ownership and smooths cross‑departmental collaboration.
Change‑management launch
Roll out a communication plan that highlights quick‑win goals, establishes “maintenance champions” in each team, and provides a central FAQ hub. Regular updates and leadership testimonials keep the momentum high.
Onboarding support team activation
Schedule weekly check‑ins with eWorkOrders’ implementation specialists to configure user permissions, set up basic workflows, and build initial dashboards. Their expertise accelerates your timeline and mitigates common setup pitfalls.
Days 31–60: Pilot and Process Refinement
Pilot scheduling
Choose a representative asset group—such as HVAC units or critical pumps—and implement calendar‑ and meter‑based work orders. This limited rollout lets you validate trigger thresholds and fine‑tune notification settings without overwhelming your entire operation.
Feedback loops
Collect input from the field through surveys and frontline huddles, then adjust task descriptions, attachment workflows, and approval chains. Continuous refinement ensures technicians trust and adopt the new system.
Dashboard setup
With real work‑order data flowing in, collaborate with your support team to build role‑based dashboards showing MTTR trends, upcoming service windows, and compliance status. Visual KPIs drive informed decision‑making and highlight areas for improvement.
Days 61–90: Scale and Continuous Improvement
Full deployment
Expand automated scheduling and dashboard access to all critical assets, incorporating learned best practices and updated standard operating procedures (SOPs). Establish a monthly review cadence to monitor adoption rates and system health.
Advanced integration
Link your CMMS to upstream systems—ERP for parts procurement, IoT platforms for live sensor data, and HR tools for workforce planning—to create an end‑to‑end maintenance ecosystem.
Ongoing coaching
Keep the eWorkOrders support team engaged for quarterly check‑ups, advanced feature training, and strategic roadmap sessions. Dedicated coaches help embed a culture of continuous improvement.
eWorkOrders: Your Partner in Proactive Maintenance
When it comes to keeping assets online and costs under control, eWorkOrders stands apart. As a family-owned, web-based CMMS, we combine enterprise-grade power with the agility and personal service that small and mid-sized businesses crave. Here’s what makes us unique:
Fully configurable workflows
Tailor asset hierarchies, work-order templates, and approval chains to your exact processes—no coding required.
Mobile-first design
Technicians get real-time task lists, offline checklists, and QR/barcode scanning, so work happens anywhere without missing a beat.
Advanced analytics and reporting
Turn every completed job into insights—track MTTR, MTBF, compliance rates, and spend versus RAV in intuitive dashboards.
Seamless integrations
Connect to ERP, IoT platforms, and vendor portals out of the box, breaking data silos and accelerating work-order cycle times.
Dedicated support and training
Our implementation team becomes an extension of yours, guiding setup, change management, and ongoing optimization.
Explore success stories on our case studies page or book a personalized demo today.
FAQs
What is preventive maintenance software?
Preventive maintenance software is a computerized maintenance management system (CMMS) that schedules, tracks, and documents routine service tasks, such as inspections, lubrication, and part replacements, before equipment fails. By automating triggers (time, meter, or sensor-based) and logging every work order, it transforms a reactive repair culture into a proactive, data-driven strategy.
What is an example of preventive software maintenance?
Updating the firmware on a fleet of CNC machines every quarter is a form of preventive software maintenance. It ensures compatibility with new tooling libraries and patches security vulnerabilities before problems arise. The CMMS issues the update work order on a predefined interval, assigns a technician, and records completion for audit purposes.
What is the best maintenance software?
“Best” depends on your asset mix, budget, and scalability needs, but leading analysts look for cloud deployment, mobile access, robust analytics, and proven ROI. eWorkOrders consistently ranks at the top for its configurable workflows, rapid implementation, and dedicated support, making it a top choice for organizations seeking quick wins with long-term growth potential.
What is an example of a preventive maintenance program?
A comprehensive preventive maintenance program in a food-processing plant might include monthly lubrication of conveyors, quarterly calibration of temperature sensors, and annual overhauls of critical chillers. Each task is scheduled in the CMMS, linked to standard operating procedures (SOPs), and tracked via KPIs like mean time between failure (MTBF) and overall equipment effectiveness (OEE).
References
- https://assets.new.siemens.com/siemens/assets/api/uuid:1b43afb5-2d07-47f7-9eb7-893fe7d0bc59/TCOD-2024_original.pdf
- https://empoweringpumps.com/how-to-avoid-the-unnecessary-costs-associated-with-reactive-maintenance/
- https://www.mckinsey.com/capabilities/operations/our-insights/manufacturing-analytics-unleashes-productivity-and-profitability
- https://www.mckinsey.com/~/media/mckinsey/industries/technology%20media%20and%20telecommunications/high%20tech/our%20insights/the%20internet%20of%20things%20the%20value%20of%20digitizing%20the%20physical%20world/the-internet-of-things-mapping-the-value-beyond-the-hype.pdf
]