Maintenance managers are the backbone of any organization’s operational efficiency, ensuring that equipment, machinery, and facilities are always in top working order. Their role goes beyond routine repairs, encompassing strategic planning, team leadership, and the implementation of preventive maintenance programs. This article outlines the key responsibilities of maintenance managers and underscores their importance in minimizing downtime, optimizing resources, and driving organizational success.
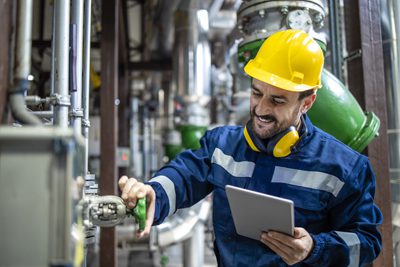
Understanding the Role of a Maintenance Manager
A maintenance manager is responsible for planning, coordinating, and executing maintenance activities to ensure equipment reliability and minimize downtime. Their role requires technical expertise, leadership, and strategic thinking to support the organization’s goals and maintain operational excellence.
Core Responsibilities
Preventive and Predictive Maintenance
Maintenance managers prioritize asset longevity and reliability by:
- Developing and implementing preventive maintenance schedules.
- Utilizing predictive maintenance techniques to identify potential failures.
- Monitoring equipment performance to reduce unplanned downtime.
Team Leadership and Coordination
Effective maintenance requires collaboration across teams, and the manager is responsible for:
- Supervising and training maintenance staff to ensure proficiency.
- Delegating tasks and managing workflow to meet deadlines.
- Promoting a culture of safety and efficiency within the team.
Asset Management
Maintenance managers oversee the lifecycle of equipment and assets, which includes:
- Tracking asset conditions and maintenance history.
- Planning for upgrades, replacements, or decommissioning.
- Ensuring compliance with industry standards and regulations.
Budgeting and Cost Management
Financial oversight is a critical component of the maintenance manager’s role. This includes:
- Preparing and managing budgets for maintenance operations.
- Evaluating the cost-effectiveness of repairs versus replacements.
- Identifying opportunities to optimize resources and reduce expenses.
Vendor and Contractor Management
Maintenance managers often collaborate with external vendors, handling tasks such as:
- Sourcing and negotiating contracts for equipment and services.
- Monitoring vendor performance and adherence to agreements.
- Managing relationships to ensure quality and timely support.
Technology Integration
Modern maintenance practices leverage technology for efficiency, including:
- Implementing CMMS for streamlined work order management and tracking.
- Utilizing IoT devices and sensors for real-time equipment monitoring.
- Keeping up with emerging technologies to improve maintenance practices.
Essential Skills for Maintenance Managers
To excel in their role, maintenance managers need a diverse skill set:
- Technical Knowledge: Expertise in mechanical, electrical, and automation systems.
- Leadership: Ability to motivate and manage teams effectively.
- Problem-Solving: Quick thinking to address unexpected equipment failures.
- Analytical Skills: Data-driven decision-making to improve maintenance outcomes.
What Are the Different Types of Maintenance Managers?
Maintenance managers may specialize in specific industries or focus on particular types of maintenance. These roles include:
Industry-Specific Maintenance Managers
- Manufacturing Maintenance Manager: Oversees complex machinery, preventive maintenance, and large maintenance teams in industrial settings.
- Fleet Maintenance Manager: Focuses on maintaining vehicles and equipment for transportation or logistics industries.
<li”>Facility Maintenance Manager: Handles building systems like HVAC, plumbing, and electrical, ensuring comfort and compliance.
Functional Maintenance Managers
- Reliability Manager: Concentrates on improving equipment reliability and minimizing failures.
- Shutdown Manager: Specializes in planning and executing maintenance during plant shutdowns or turnarounds.
What Certifications Are Available for Maintenance Managers?
Certifications help maintenance managers stay updated on best practices and advance their careers:
Maintenance-Specific Certifications
- Certified Maintenance & Reliability Professional (CMRP): Focuses on reliability and asset management strategies.
<li”>Certified Plant Maintenance Manager (CPMM): Emphasizes maintenance management best practices and team leadership.
General Certifications Beneficial for Maintenance Managers
- Project Management Professional (PMP): Develops project management skills essential for overseeing maintenance projects.
- Lean Six Sigma: Enhances efficiency and process improvement in maintenance operations.
CMMS: A Maintenance Manager’s Essential Tool
A maintenance manager is critical to maintaining the efficiency and longevity of an organization’s assets. From crafting effective maintenance strategies to leading teams, the role requires a strategic focus on minimizing downtime and maximizing asset performance. One indispensable tool in their arsenal is a Computerized Maintenance Management System (CMMS) software.
Conclusion
The maintenance manager’s role is integral to ensuring operational efficiency, asset longevity, and cost-effective maintenance strategies. By utilizing tools like CMMS, promoting team collaboration, and leveraging modern technologies, maintenance managers drive productivity and reliability across organizations. As industries advance, the demand for skilled maintenance managers will continue to grow, making this role a cornerstone of operational success.
See What Our Customers Are Saying
Additional Resources
Disclaimer: Job Titles and Responsibilities The job titles and responsibilities listed in this document are subject to change and may vary depending on the organization’s specific needs, structure, and operational requirements. These descriptions are intended to provide a general overview and may not reflect the exact title or comprehensive list of duties for every position within the company. Actual job titles, roles, and responsibilities may be adjusted to align with organizational goals, industry trends, or business demands. Employees should refer to their most current job description or consult with their supervisor or Human Resources department for the most up-to-date and accurate information regarding their specific position.
<