Benchmarking in maintenance is an essential approach for organizations aiming to streamline their maintenance processes and improve operational efficiency. By evaluating their performance against industry standards and best practices, companies can uncover gaps and areas needing improvement. This helps them implement tailored strategies to enhance their maintenance activities. This discussion outlines key actions and recommended approaches to effectively set benchmarks for improving maintenance in industrial settings.
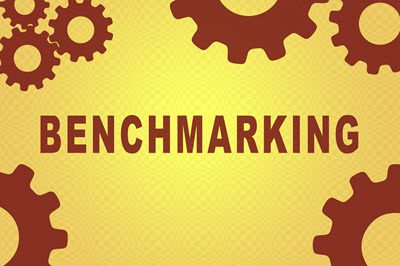
Understanding Benchmarking
Understanding maintenance benchmarking involves looking at how your maintenance practices compare to the best in the industry. It’s more than just a comparison; it’s about identifying where you can improve to make your processes smoother and more effective. Think of a benchmark as a baseline — a point of reference that helps you measure how your organization stacks up to others in your field. The goal is to pinpoint performance gaps, find ways to optimize, and ultimately boost how well your maintenance operations run.
Choosing a Suitable Maintenance Benchmark
Determining an effective maintenance benchmark involves considering certain crucial factors. In the realm of maintenance, a reliable benchmark should possess the following qualities:
Industry Relevance
The benchmark should focus on measuring aspects that directly contribute to enhancing your business. For instance, gauging the time it takes for an individual in your company to perform maintenance on an asset is pertinent if your goal is to reduce downtime. Conversely, if your objective is to boost sales by increasing product output, measuring the time your assets spend in creating the product becomes a crucial metric.
Accuracy
The measurements derived from the benchmark must precisely reflect the intended parameters. For instance, if the benchmark aims to measure downtime on an asset, it is imperative to ensure that all relevant assets are being tracked within the specified timeframe. Accuracy is paramount for meaningful insights and effective decision-making in the maintenance processes.
Peer Comparison
When selecting organizations to benchmark against, it’s essential to focus on those with similar operational characteristics, such as company size, asset types, and asset volume. This ensures that comparisons are relevant and realistic, providing clearer insights into performance gaps. With this approach, you can set practical goals that are more aligned with industry standards and challenges, helping refine your maintenance management practices for better results. By drawing from the experience of similar companies, you can adopt proven strategies that directly address the needs and demands of your own operations.
Real-Time Measurements
Utilize real-time data for benchmarking rather than relying on speculative measurements. This approach provides a more accurate representation of your current performance in industrial maintenance.
Percentage-Based Metrics
Measure events in percentages to account for differences in fleet density. This allows for more meaningful comparisons across organizations of varying sizes.
Repair-Focused Metrics
Prioritize metrics that are repair-related rather than preventive maintenance (PM) related. This focus helps identify areas where immediate improvements can be made in your maintenance operations.
Key Maintenance Metrics to Consider
When setting maintenance benchmarks, consider incorporating the following metrics:
Mean Time Between Failure (MTBF
This metric helps determine the optimal timeframe for equipment downtime for maintenance activities. It provides insights into the reliability of your assets and is crucial for effective maintenance management.
Mean Time to Repair (MTTR)
MTTR serves as a benchmark for future comparison. It measures the average time required to repair and restore equipment to full functionality, which is essential for minimizing downtime.
Overall Equipment Effectiveness (OEE)
OEE measures the overall effectiveness of the company’s equipment. It takes into account availability, performance, and quality to provide a comprehensive view of asset utilization in industrial maintenance.
Maintenance Backlog
This metric reflects the time value of incomplete maintenance jobs. It helps prioritize maintenance tasks and identify potential bottlenecks in the maintenance process.
Maintenance Cost per Unit or Ton
This common benchmark quantifies maintenance within the context of quantity produced. It provides insights into the efficiency of maintenance operations relative to production output.
Key Steps for Implementing a Benchmarking Process
Define Key Performance Indicators (KPIs)
Identify the critical areas of maintenance performance that you want to benchmark, such as equipment uptime, maintenance costs, or mean time between failures (MTBF).
Utilize Diverse Data Sources
Combine internal performance data with external benchmarking information to gain a comprehensive view of your maintenance operations.
Compare Performance
Compare your maintenance KPIs with those of industry leaders or similar organizations to identify performance gaps.
Set Realistic Targets
Based on the benchmarking results, set realistic targets for improvement in each KPI, taking into account industry best practices and your organization’s specific circumstances.
Develop Action Plan
Identify the concrete steps and best practices needed to achieve the target KPIs, and develop action plans for implementation.
Track and Review
Continuously track and benchmark your performance against the targets, and review and adjust your action plans as needed to drive continuous improvement.
Best Practices for Benchmarking Maintenance Performance
Focus on Relevance: Prioritize KPIs that directly align with your organization’s maintenance objectives and overall business goals.
Use Both Internal and External Data: Combine internal performance data with external benchmarking data to gain a comprehensive view of performance.
Involve Cross-Functional Teams: Engage cross-functional teams in the benchmarking process to gain diverse perspectives and buy-in for improvement initiatives.
Document and Share Results: Document the benchmarking process, action plans, and results to create a knowledge base for continuous improvement and share best practices across the organization.
Leveraging CMMS for Benchmarking Success
A Computerized Maintenance Management System (CMMS) stands as a technological ally, transforming the way organizations handle, streamline, and optimize their maintenance operations. This powerful software empowers users to efficiently schedule and monitor maintenance tasks, oversee work orders, manage equipment and inventory, and generate insightful reports for strategic decision-making. By acting as a centralized hub for maintenance data and processes, CMMS becomes the cornerstone for enhancing asset reliability, minimizing downtime, and exercising control over maintenance expenses. When integrated with maintenance benchmarking, CMMS evolves into a unique tool, providing organizations with distinct insights to measure their performance against industry benchmarks and best practices, ultimately identifying tailor-made avenues for improvement.
Final Thoughts
Maintenance benchmarking is a powerful tool for organizations seeking to optimize their maintenance practices and drive operational efficiency. By carefully selecting relevant metrics, implementing a structured benchmarking process, and leveraging advanced technologies like CMMS, companies can identify areas for improvement and implement strategies to achieve maintenance excellence. Regular benchmarking, coupled with a commitment to continuous improvement, enables organizations to stay competitive and adapt to evolving industry standards in the dynamic field of industrial maintenance and maintenance management.
FAQs About Setting Maintenance Benchmarks
What is maintenance benchmarking, and why is it important?
Maintenance benchmarking involves comparing your organization’s maintenance practices with industry standards or best practices. It’s crucial for identifying areas of improvement, optimizing processes, and enhancing overall maintenance efficiency.
How do I determine which maintenance benchmarks are relevant for my industry?
Consider your industry type, the nature of your equipment, and your specific maintenance goals. Relevant benchmarks should align with your objectives and provide meaningful insights into your organization’s performance.
Can I use maintenance benchmarks for different types of equipment?
Yes, benchmarks can be adapted for various equipment types. However, it’s essential to consider the specific characteristics and requirements of each asset when selecting and interpreting benchmarks.
What is the recommended frequency for revisiting and revising maintenance benchmarks?
It’s crucial to conduct regular reviews to keep benchmarks in sync with industry dynamics and emerging best practices. Updating benchmarks at least on an annual basis or whenever substantial changes occur within your organization or industry.
How do I involve my maintenance team in the benchmarking process?
Encourage open communication with your maintenance team to gather insights into current practices, challenges, and suggestions for improvement. Involving the team ensures a more comprehensive understanding of your organization’s maintenance landscape.
What are the common challenges in implementing maintenance benchmarks?
Challenges may include resistance to change, data collection issues, and a lack of standardized metrics. Addressing these challenges requires clear communication, training, and a commitment to continuous improvement.
Can maintenance benchmarks be used for small businesses as well?
Yes, maintenance benchmarks are scalable and can be adapted for businesses of all sizes. The key is to select benchmarks that align with the scale and objectives of your organization.
How can maintenance benchmarking contribute to cost savings?
By identifying areas for improvement and adopting best practices, maintenance benchmarking can lead to more efficient processes, reduced downtime, and optimized resource allocation, ultimately contributing to cost savings in the long run.
How does integrating a CMMS (Computerized Maintenance Management System) enhance maintenance benchmarking?
A CMMS streamlines data collection, providing real-time insights into maintenance activities. By leveraging CMMS data, benchmarking becomes more accurate and actionable, allowing organizations to measure performance against industry standards and continuously improve maintenance strategies.
See What Our Customers Are Saying
Customer Testimonials
Case Studies
Additional Resources
The Ultimate Library of Maintenance Checklists
CMMS Articles & Directories
Maintenance Terms & Definitions Glossary