We depend on automated technology to carry out many of our most important industrial activities in today’s world. Thanks to automation technology we have now reached new heights of production and innovation.
However, the programmable logic controller (PLC) is a crucial invention that made our level of automation possible.
PLC maintenance is essential for ensuring the smooth and reliable operation of many industries. PLCs, or Programmable Logic Controllers, are used to control and automate processes in a wide range of applications, from machinery and production lines to entire factories. Proper maintenance of PLCs is critical to prevent failures, downtime, and other costly problems. In this article, we will discuss the importance of PLC maintenance and some common maintenance tasks that should be performed.
.
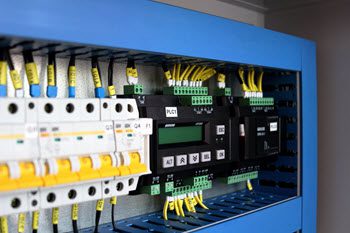
What is a Programmable Logic Controller (PLC)
A programmable logic controller (PLC) or programmable is an industrial computer that works to control a computer system in an industrial organization. These systems have been adapted for the control of manufacturing processes, such as assembly lines, machines, robotic devices, or any activity that requires high reliability, ease of programming, and process fault diagnosis is known as a programmable logic controller (PLC) or programmable controller. Even in our agriculture industry, large farmers have adopted PLC systems for their feed distribution systems, which were sophisticated enough to even measure the amount of grain to each individual animal, on poultry, swine, and cattle feedlots.
PLCs monitor the inputs to the system and then make decisions about related outputs. PLCs, which are typically used to monitor motors or machines, are frequently the core of a predictive maintenance system, which can alert organizations to possible issues before they result in significant breakdowns.
Types of PCLs
There are 4 different types of PLCs:
Fixed integrated PLC
Fixed integrated PLCs have a single unit that houses both the controller and the Input/Output (IO). The main advantage of fixed-type PLCs is their lower cost. Some of the shortcomings are that fixed-type PLCs lack flexibility has less memory, difficult to repair, and are not liable to do complex tasks. Additionally, if any component malfunctions, certain versions require the replacement of the entire system.
Distributed PLC
A network connects the controller and input/output devices. The main advantage of distributed PLCs are reduced space higher life and reliability, easy to maintain, and with its high processing speed, it has greater flexibility. The distributed PLC costs more when used infrequently.
Soft PLC
Is considered a fully complete embedded computer, and can be created using a software technology called a soft PLC. The advantages of Soft PLCs are that they are easier to configure, any amount of sensors and actuators can be networked in, support a variety of programming languages, lowers production costs, and offers sophisticated security solutions. One disadvantage is that soft PLC does not come with any additional software.
Modular PLC
A modular PLC contains separate modules for the controller and IO that are inserted into a chassis. The advantages of the individual modules make them easier to use, provide greater storage capacity, can handle more complicated processes, and can function in harsh environmental conditions. A few disadvantages include complex configuration and the price of a modular PLC being higher than a compact.
How a Programmable Logic Controller Works
Each component of a PLC accepts inputs and regulates outputs, making it an input-output system. The third component of the system, logic programming, governs the interaction between inputs and outputs and takes place in the CPU.
Here’s how each element works:
Input Monitoring
The PLC keeps track of pertinent data inputs and provides that information to the CPU. PLCs with analog capability can accept analog inputs for continuous variables, but some PLCs only accept data inputs with discrete (on/off) inputs. IoT devices, robots, safety sensors, human-machine interfaces, and virtually any other form of data entry point are just a few examples of the sources of input.
Logic Programming
Every PLC has a microprocessor CPU, which can be 16-bit or 32-bit in size. The PLC CPU is configured by engineers and technicians to recognize specific values and conditions and to alter outputs in accordance with its preprogrammed rules. The CPU continually monitors the status of variables and takes actions in response to preset criteria. This simple premise allows a wide variety of designs and functions.
Output Control
The PLC manages a number of switches, motor starters, relays, and other devices attached to its outputs based on the programmed logic. This enables the PLCs to take over mechanical activities like machine operation. By instructing PLCs to transfer their output signal to a subsequent PLC in a chain, engineers can also connect other system components.
Compact PLC Unites
The CPU, inputs, and outputs are typically all contained within one device. The inputs and outputs of the PLC are found combined in the I/O module of the rack-mount modular PLC systems that many industrial facilities utilize, while the logic processes take place in a separate CPU module. I/O modules can be situated far from the CPU, sometimes even in different buildings, or they might be adjacent to it.
Why PLC Maintenance Is Important
The successful operation of your production depends on your programmable logic controllers (PLC). It is critical that they are always operational and operating at their highest level of effectiveness because of this. You might need to repair or at the very least replace a portion or two of your PLC if it develops a problem in order to keep the PLC operating. Regular preventive maintenance of a PLC system is one of the most crucial strategies to keep it running well.
PLC preventative maintenance activities can be time-consuming, but they can spare you from a lot of problems, expensive repairs, and downtime. Here are some suggestions for maintaining programmable logic controllers to include on your preventative checklist.
PLC Maintenance Checklist
Backup Data
Every so often, up-to-date and routine backup of the PLC’s programming is essential.
Program Functionality
When carrying out PLC preventive maintenance, check the functionality of the operating program to ensure the equipment or process being controlled is functioning as required.
Inspect Connections
Make sure that all connections are safe by routinely inspecting things like plugs, sockets, and terminals. Make sure to check connections more often in high-vibration areas, especially paying attention to fasteners like screws and bolts.
Check LED Lights
If your system has LED indicators, be sure to check them regularly.
Inspect Sensors
If sensors are part of your PLC system, be sure they are maintained per manufacturers’ recommendations.Source EMI
To see if you are experiencing any problems with electromagnetic interference, examine your local wiring. To prevent static electricity issues, make sure your lower-level components are far away from high-current lines.
Inspect Battery Status: The status of this indicator shows whether the available battery voltage is sufficient to provide backup power for the EPROM stored in the PLC, in the event of a power failure or when the machine is switched off for maintenance.
Inspect the Overall Condition of the PLC Components
Examine the CPU and the other PLC modules visually for signs of wear, warping, distortion, or overheated parts, such as burnt scents or discoloration.
Spare Inventory
Be sure that you have enough spares to handle your maintenance needs, ultimately minimizing downtime.
Clean Dust
Be sure to remove all dirt or dust that has accumulated on the PLC components including its I/O modules, such as the CPU unit and the I/O system.
Clean and Change Filters
Regularly clean or replace any ventilation filters installed in the PLC enclosures.
Maintain Ventilation
Regularly change the ventilation filters, and be sure to keep items such as installation manuals, tools, drawings, papers, or other materials away from the PLC syste.
Keep Your PCL Insolated Against Airborne Debris
Try and keep out floating debris during regular machine operation at a minimum.
Audit the PLC Systems in Use: Keep an up-to-date inventory of your PLCs.
Software Updates
Check for any product notices, patches, recalls, or required upgrades for any of the PLC components and update accordingly.
Calibrate Devices
If any of your input or output devices require calibration, be sure to include those tasks, along with the circuit cards, in your preventive maintenance program.
Check Environmental Conditions
Be sure to monitor things like humidity levels and temperature as they can hurt your PLC components. Sensors can help you monitor these conditions around the clock.
Inspect the Presence of Potential EMI or RFI Sources
Radio-frequency interference (RFI) or electromagnetic interference (EMI) are major causes of erratic PLC processor issues, without a clear indication of the specific issue. Ideally, during preventive maintenance, you should perform an audit of the local wiring to identify potential sources of EMI that could disrupt the operation of your PLC system.
Replace Modules
You might occasionally need to replace input or output modules due to wear and tear. When replacing modules, make sure you adhere to the instructions and cut off power as directed.
Error History
Take a look at regular reports to see if your PLC system has noted any scanning or error flags. Be sure to find the cause of these problems early.
Equipment Location
PLC should be near the machine it’s controlling, be sure you keep other equipment, particularly those that generate noise or heat, away from your PLC.
Increase Awareness
Pay attention to unusual activity. As an example, if you find that input and output devices are frequently burning out, you may want to check for power spikes or shorts.
Keep Current
If your system has recalled, patches, product notices, or upgrades, be sure to incorporate them into your preventive maintenance program to stay current.
Maintenance Scheduling
The PLC’s application and operational environment determine how frequently it needs preventive maintenance. Some maintenance operations will need to be carried out more often if the PLC system is used in harsh environments or high-vibration applications. To keep the PLC system in good working order, it is best to do everyday duties like dusting or cleaning ventilation filters. Nevertheless, some operations, such as backing up the PLC’s programming, are less dependent on the working environment and are frequently completed twice a year.
Lastly, before you schedule any PLC preventive maintenance, you should carry out some routine inspections of other preventive maintenance procedures, however, will need to be planned according to either time or usage. Utilizing historical data to create the best preventative maintenance schedule is simple if you have a computerized maintenance management system (CMMS). For instance, you would want to plan to replace a certain component twice a year if you notice that it tends to break every 8 to 9 months in order to avoid that breakdown.
Industry PLC Applications
PLC systems are adaptable and suitable throughout many different industries. Below are just a few examples of the applications using PLC technology today.
Manufacturing Production
Plant managers and others can use analysis tools to better leverage resources, batch scheduling of jobs, logistics, supplier timing, and other essential operations in order to develop more efficient manufacturing processes. PLC provides reliable data, such as sensor performance and other information, which can be combined with cloud computing to create a more holistic picture, or “big data.”
Agriculture
The agricultural process involves seeding, plowing, irrigation, planting, fertilizing, weeding, and harvesting. Modern agriculture relies directly and indirectly on automated equipment for growing, processing, and transporting these products. Today companies are using PLCs to revamp existing agricultural equipment automation systems and improving efficiency.
Oil & GAS
Companies operating in the oil and gas industry often add well pad sites as part of their expansion plans. Each of these well pads, which may have one to six wells, must have an individual PLC. These systems use pumps, valves, and sensors to work effectively and efficiently. By developing a single, scalable PLC system that incorporates Human Machine Interface (HMI), oil and gas companies can get a handle on all its well pads quickly and easily.
Glass Manufacturers
PLCs and bus technologies are used by producers of glass products to control material ratios and manufacturing workflows. Glass businesses must use complex, sophisticated procedures that necessitate data collecting and exact quality control. Technology using PLCs can assist with both.
HVAC
A PLC allows an HVAC technician to access a system through the internet. A PLC enables a HVAC technician to connect to a system online. They are able to wirelessly connect with other technicians and simultaneously automate several tasks. Previously, each operation required its own unique controllers. The PLC is a standardized approach to modern HVAC/R technology that improves diagnostic evaluations and system management.
Food Processing System
A PLC is the food processing system that serves for contaminant levels in the water, flow rates in major parts of the water treatment plant, and alternatively, valves that control in-process water flow can be controlled remotely.
Cement Manufacturing
PLC plays a critical role in cement manufacturing. The process involves mixing various raw materials and compounds in a kiln. A PLC program ensures the use of the right quality and quantities of raw materials during the mixing process within the kiln, in which determines which output can result in the best possible quality.
Healthcare
The healthcare systems deploy PLC systems in central utility plants for integration, remote monitoring, and automated control of mechanical-electrical systems.
Chemical, Pharmaceutical, and Nuclear Plants
Depend on PLCs for precise, reliable, and automated control of complex research, development, and production processes.
PCL Risks
Many of the PLC concerns are interconnected and could become more serious as your system gets bigger. These are the key things to look out for:
I/O Device Modules and Field Devices
The entire PLC system is at risk if either an input device or an output device fails. This can be brought on by a power failure and could result in the system stopping abruptly. The PLC typically waits for a signal before starting its subsequent set of actions. An engineer often needs to identify the root cause of the stop and track it back to the individual device in order to fix this issue. There could be a power fluctuation, internal fault, or power loss when numerous devices are frequently having issues.
Ground Integrity
Correct grounding is necessary to keep a PLC and the maintenance team safe. In addition to shielding against electrical white noise, ground integrity also acts as a sound barrier.
Power Problems
Outages due to local or regional blackouts are, the most common sources of power failure outages, and fluctuations can lead to PLC risks. The majority of industrial buildings in use today include backup power sources to eliminate the chance of a power outage. The facility’s most essential operations continue to run continuously during a mainframe blackout, or at least long enough to be appropriately shut down, thanks to the backup power source. Some facilities employ what is referred to as an uninterrupted power supply, which serves as a backup power source.
Electrical Noise Interference
Electrical noise interference from foreign signals can have a significant negative effect on a PLC’s performance. Electromagnetic interference is the most frequent reason for electrical noise, and it often happens when a big motor starts up or when lightning strikes close by. Radio frequency interference, which can be brought on by adjacent antennae and mobile transmitters, is another reason for electrical noise. On an industrial premise, handheld devices that could cause interference should be prohibited on the floor. Furthermore, any machinery on the premises that could be problematic in this regard should be segregated from the PLC.
Temperature Problems
Excessive heat is one of the biggest threats to electronic components. If not properly protected, a PLC system that is surrounded by heat-emitting equipment could fail. In general, all equipment should be kept at temperatures that are significantly lower than the highest limit recommended by the manufacturer. If not, the PLC and/or peripheral component can overheat and stop functioning altogether, if at all.
Corrupted Memory
External influences like frequency interference and power outages might corrupt a PLC’s memory. For instance, the shock could make the code unintelligible to the central processing unit during a brownout or blackout. Similarly to this, a PLC that was unable to shut down properly owing to an unexpected power outage would not read correctly once it was restarted.
Managing The Risks
In order to reduce the possibility of PLC problems, you need to have a good preventive maintenance plan in place and the tools like a computerized maintenance management system (CMMS) to help you keep on top of the risks and avoid downtime. Facility engineers need to set up inspections and follow proper procedures to ensure all parts are properly connected at all ends. The operating environment of a PLC system should be well maintained to ensure no electric noise, moisture or excess heat are present. Most of all, it is crucial to ensure a spare power supply backs a PLC system at all times. This way, if the main power source goes down for any length of time, factories can operate at full or at least necessary capacity. Although some failures we have no control over having preventive maintenance procedures in place will help minimize the saturation.
Benefits of PLC
Although PLC systems have some risks, they also have many benefits. PLC systems, among other things, are simple to integrate, take up minimal room, and improve productivity.
When you make an investment in a good preventative maintenance program, you can anticipate cost savings, increased productivity, and other advantages. Here are some typical PLC maintenance system benefits.
Save Money
One can think of it as a one-time investment because the likelihood of a defect is quite low. PLCs are unquestionably the most cost-effective solutions in this sense. The cost of PLC recovers within a short period.
Prolonged Life and Reliability
The ruggedness of these devices is outstanding. Due to the small number of moving parts, the likelihood of a defect or damage is quite low.
Increased Productivity
>When properly programmed, PLCs are essential for enabling automation, minimizing power consumption, increasing system control, keeping records, and redistributing the available workforce to increase productivity.
Small Space Footprint
PLCs are completely solid-state devices, making them far more compact than hard-wired controllers, which employ electro-mechanical devices.
Tremendous Flexibility
You have more flexibility for every project because data is stored in a group of devices rather than throughout a disjointed system. Additionally, it makes it simpler to expand the overall system by adding devices and PLC hardware as necessary.
Easy to Maintain
Problems are simple to recognize and fix since PLCs are made up of a variety of input and output devices. Each component has a limited number of things to be examined, making it easy to identify problem areas.
Security
The majority of PLC systems have extensive safety and security measures in place to safeguard the data they contain. Additionally, businesses can access private data more securely than they can on older, larger systems.
Machines That Use PLCs
PLC systems can be found everywhere in our highly technological world, from factories to office buildings to even directing traffic on our streets. PLCs are at the very heart of the control of many critical technologies that most of us don`t give even a second thought to, they are so seamlessly and invisibly integrated into our daily lives.
Following are a few instances of common mechanical systems that are managed by PLCs:
Conveyor belt | Textile weaving machine | Level sensor | Beverage filling machine |
Elevator | Waterjet cutting machine | Machining center | Blending machine |
Automatic guided vehicle (AGV) | Welding machine | Measuring instrument | Blow molding equipment |
Automatic packaging machine | Wrapping machine | Metal cutting machine | Boiler |
Automatic palletizing robot | 3D printer | Metalworking machine | Briquetting machine |
Automatic welding robot | ABB robot | Motor control center | Canning machine |
Batch mixer | Asphalt plant | Packaging machine | Carpet cutting machine |
Blow molding machine | Automatic door | Paint booth | CNC boring mill |
CNC lathe | Automatic gate | Pellet mill | CNC drill press |
CNC milling machine | Automatic screw machine | Plastic extrusion machine | CNC flame cutter |
CNC plasma cutter | Bagging machine | Plastic recycling machine | CNC lathe |
CNC punch press | Bandsaw | Pneumatic cylinder | CNC plasma cutter |
CNC router | Beverage bottling plant | Pressure sensor | CNC punch press |
CNC waterjet cutter | Blast furnace | Printing machine | CNC router |
Cold rolling mill | Blow molding equipment | Punch press | CNC waterjet cutter |
Crane | Boiler | Pump | Cold rolling mill |
Die casting machine | Bottling line | Quality control equipment | Concrete mixer |
Electric motor | Bridge crane | Refrigeration system | Control panel |
Extrusion line | Bulk material handling equipment | Robot arm | Conveyor belt |
Fanuc robot | CNC flame cutter | Sawmill | Crane |
Injection molding machine | CNC plasma cutter | Screw machine | Cryogenic tank |
Label applicator | CNC press brake | Sewing machine | Cutting machine |
Laser cutter | CNC router | Shearing machine | Demag crane |
Lathe | CNC turret punch press | Sheet metal machine | Die cutting machine |
LED assembly machine | Compressor | Slitter | Die casting machine |
Milling machine | Concrete mixer | Sorting machine | Dispensing machine |
Motor control center (MCC) | Control panel | Spinning machine | Electric furnace |
Packing machine | Conveyor system | Stamping machine | Extrusion line |
Paper cutting machine | Cooling tower | Steel mill | Fan |
Pick and place robot | Cranes | Temperature controller | Feeding machine |
Plastic blow molding machine | Drying oven | Textile machine | Filling machine |
Plastic injection molding machine | Electric furnace | Thermal oxidizer | Flow |
Plastic thermoforming machine | Fan | Thermoforming machine | Forging press |
Press brake | Feeding machine | Tool and die machine | Furnace |
Punch press | Filling machine | Transfer press | Gearbox |
Robotics assembly line | Flow meter | Turret punch press | Glass cutting machine |
Robots welding | Furnace | Ultrasonic welding machine | Grinding machine |
Sewing machine | Gearbox | Vacuum pump | Heat exchanger |
Shear | Generator | Valve | Heating furnace |
Siemens robot | Glass cutting machine | Waste treatment plant | Hoist |
Sorting machine | Grinding machine | Water pump | Industrial oven |
Spinning machine | Heating furnace | Welding equipment | Injection molding equipment |
Spray booth | Heat exchanger | Wind turbine | Kuka robot |
Stamping press | Hoist | Yarn spinning machine | Lathe |
Steel rolling mill | Industrial oven | Air compressor | Laminating machine |
Textile weaving machine | Injection molding equipment | Air handling unit | Leak tester |
Waterjet cutting machine | Kuka robot | Air conditioning system | Level sensor |
Welding machine | Lathe | Automatic labeling machine | Machining center |
Stamping press | Laminating machine | Automatic screw machine | Measuring instrument |
Steel rolling mill | Leak tester | Batch mixer | Metal cutting machine |
Bottom Line
PLCs (Programmable Logic Controllers) are essential for many industries because they provide a reliable, efficient, and cost-effective way to control and automate processes. Proper maintenance of PLCs is crucial to ensure that they continue to function properly and do not fail, which can result in downtime, lost production, and other costly problems. PLCs are also the foundation for predictive maintenance, which uses data and algorithms to predict when equipment is likely to fail and schedule maintenance before it happens. This can help to prevent unplanned downtime and improve overall efficiency. Regular maintenance of PLCs includes tasks such as checking for signs of wear and tear, replacing faulty components, and performing regular software updates. Proper maintenance can also help to extend the life of PLCs and prevent costly repairs or replacements. Overall, PLCs and maintenance are critical for maintaining the smooth operation of many industries.