In maintenance-intensive industries, equipment reliability directly impacts profitability and productivity. Facility managers, plant directors, and maintenance professionals continuously grapple with balancing preventive measures against operational demands. CMMS (Computerized Maintenance Management System) software provides a structured solution, centralizing maintenance operations to significantly reduce downtime and optimize asset performance.
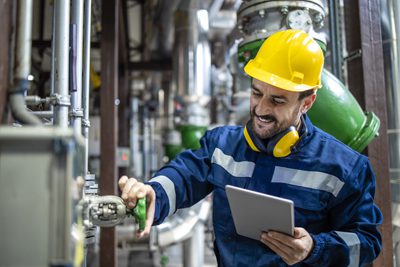
Understanding CMMS: What Does It Mean?
A CMMS, meaning Computerized Maintenance Management System, is a specialized software designed to streamline and automate the management of maintenance activities. It acts as a comprehensive digital hub for scheduling tasks, recording asset data, managing inventory, and analyzing performance. Unlike traditional spreadsheet-based approaches, a CMMS centralizes information, enhancing accessibility and enabling data-driven decision-making.
Historical Context and Evolution of CMMS
Initially introduced in the 1960s as basic maintenance management systems, early CMMS implementations relied on mainframe computers. Over decades, CMMS evolved significantly with advancements in technology. Today’s cloud-based platforms provide real-time access, mobile integration, and advanced analytics capabilities, adapting to the dynamic needs of modern industries.
Challenges in Traditional Maintenance Practices
Challenge | Issue | Consequences |
---|---|---|
Manual Record-Keeping | Inaccurate or incomplete documentation Lost or misplaced records | Poor decision-making due to unreliable data Difficulty tracing asset history or recurring issues |
Reactive Maintenance | Frequent emergency repairs Reduced asset lifespan Compromised safety from sudden equipment failure | Unplanned downtime disrupting operations Frequent replacement and capital expenditures Increased risk of workplace accidents and safety hazards |
Limited Visibility and Reporting | Lack of real-time data Poor tracking of performance metrics | Delayed identification of potential issues Inability to measure maintenance effectiveness accurately |
Inventory Mismanagement | Excessive or inadequate spare parts stocking Difficulty forecasting inventory needs | Increased inventory costs or prolonged downtime Frequent emergency purchases and inefficiencies |
Regulatory Compliance Risks | Poor record-keeping affecting compliance audits Missed mandatory inspections or maintenance | Risk of fines, penalties, or legal liabilities Safety hazards, regulatory breaches, and reputation damage |
Core Features and Functionalities of CMMS Software
Automated Preventive Maintenance Scheduling
Preventive maintenance is crucial to asset longevity and operational continuity. CMMS software automatically schedules recurring maintenance tasks based on predefined criteria such as time intervals or equipment usage. This automation reduces manual planning efforts and ensures critical maintenance tasks are never overlooked.
Robust Asset Management and Tracking
Accurate asset management is foundational for efficient operations. CMMS platforms offer detailed tracking capabilities, recording each asset’s location, maintenance history, performance metrics, and warranty information. Maintenance teams access comprehensive asset profiles instantly, facilitating swift decision-making and timely interventions.
Inventory Control and Spare Parts Management
CMMS software simplifies inventory management by tracking parts usage, maintaining optimal stock levels, and alerting maintenance personnel when inventory needs replenishing. This eliminates costly delays associated with unavailable parts, significantly reducing downtime.
Comprehensive Reporting and Analytics
Advanced analytics and customizable reporting capabilities within CMMS software empower facility managers and reliability engineers to identify patterns, track KPIs, and make strategic decisions based on reliable data. Reports typically include maintenance efficiency, asset uptime, repair histories, and cost analysis, facilitating continuous improvement.
Industries That Can Benefit From a CMMS
CMMS software delivers practical, measurable advantages across various sectors.
Manufacturing and Industrial Plants
Manufacturers adopt CMMS to enhance equipment uptime, optimize maintenance schedules, reduce operational costs, and ensure timely production cycles.
Healthcare Facilities
Hospitals and healthcare providers leverage CMMS to maintain critical medical equipment, comply with regulatory standards, and ensure patient safety.
Property and Real Estate Management
CMMS supports property managers in maintaining extensive property portfolios by centralizing maintenance scheduling, improving response times, and increasing tenant satisfaction.
Educational Institutions
Schools and universities utilize CMMS for efficient facility management, ensuring a safe, well-maintained educational environment through proactive maintenance.
Government and Public Infrastructure
Government agencies employ CMMS to manage public infrastructure, ensuring efficient operation and reliable maintenance of essential public assets and facilities.
Strategic Implementation of CMMS
Successful CMMS adoption goes beyond installation—it requires a clear strategy that brings people, processes, and technology together. A thoughtful implementation ensures the system fits the organization’s real-world needs and delivers lasting value.
Initial Planning and Assessment
Before investing in a CMMS, it’s important to map out the current state of maintenance operations. This involves identifying pain points, such as recurring equipment failures, delays in work orders, or difficulties with inventory tracking.
Organizations should define specific goals—whether that’s reducing downtime, cutting maintenance costs, or improving regulatory compliance—and choose a CMMS platform that can support these outcomes. Involving stakeholders from different departments at this stage creates a more complete picture of needs and prevents gaps that could slow down adoption later.
Effective Training Programs
Even the most powerful CMMS will fall short if users aren’t confident in how to operate it. Building an effective training program means going beyond a single onboarding session. Hands-on workshops, user manuals tailored to different roles, and ongoing support resources all contribute to smoother transitions.
Real-world scenarios, such as generating work orders or logging asset inspections, should be part of training so that users can apply the system to their daily tasks right away. An easy-to-access knowledge base and periodic refresher courses help maintain system fluency over time.
Continuous Evaluation and Improvement
After rollout, organizations need to view their CMMS as a living system, not a one-time setup. Regular check-ins—through maintenance KPIs like average repair time, downtime reductions, or on-time completion rates—highlight whether the CMMS is delivering on its promises.
Gathering feedback from users at all levels reveals insights into hidden inefficiencies or new needs. From there, system settings, workflows, and even training materials can be adjusted to better match the day-to-day realities of the operation. In this way, the CMMS remains a tool that evolves with the business, rather than becoming an outdated layer of administration.
CMMS Implementation Checklist
Step | Action Points |
---|---|
Assess Current Maintenance Processes |
|
Select the Right CMMS Platform |
|
Develop a Structured Training Program |
|
Launch and Monitor Performance |
|
Continuously Update and Improve |
|
Common Mistakes When Choosing or Implementing a CMMS
Future CMMS Trends
As organizations demand more from their maintenance operations, CMMS platforms are adapting with new technologies that promise better precision, efficiency, and accountability.
Here’s a closer look at the trends shaping the future of CMMS:
Artificial Intelligence and Machine Learning
Next-generation CMMS platforms are moving beyond scheduled reminders toward true predictive maintenance. By analyzing patterns in equipment behavior, AI and machine learning algorithms can forecast failures before they happen.
This allows maintenance teams to plan interventions at the most cost-effective moments, avoiding unnecessary downtime and reducing wear on assets. Over time, these systems will learn from every action, continuously refining maintenance schedules to align perfectly with real-world usage patterns.
Increased Mobility
Mobile access is no longer a luxury—it’s becoming a core requirement. Technicians are spending more time on the floor, in the field, or across multiple sites, and future CMMS platforms will continue to expand mobile functionality.
Real-time updates, barcode scanning, remote work order completion, and instant access to asset histories from any device will streamline maintenance workflows. The focus will shift to creating mobile-first designs that allow full functionality without needing to return to a desktop or office.
Enhanced Sustainability Tracking
Sustainability goals are gaining equal importance alongside operational targets. Future CMMS solutions will include built-in features to track energy usage, emissions tied to equipment performance, waste reduction efforts, and compliance with environmental standards.
By consolidating these metrics within the maintenance platform, organizations can easily monitor their environmental impact, make data-driven decisions to reduce resource consumption, and demonstrate compliance during audits or ESG reporting.
Blockchain Technology in CMMS
Blockchain’s promise of secure, immutable records holds real potential for maintenance management. By recording every maintenance activity on a blockchain ledger, organizations can create transparent, tamper-proof histories for each asset.
This can dramatically improve accountability, simplify regulatory audits, and provide trusted data for warranty claims, resale, or liability cases. Blockchain integration could also enhance supplier coordination, allowing organizations to verify parts, maintenance services, and warranties with complete traceability.
eWorkOrders CMMS: Comprehensive Maintenance Management Solution
Conclusion
CMMS software is not merely a technological upgrade; it represents a strategic enhancement of maintenance management practices. Organizations leveraging CMMS solutions like eWorkOrders achieve optimized operational efficiency, reduced maintenance costs, and enhanced asset reliability, positioning them for sustainable success in increasingly competitive environments.
Book a demo today and discover how eWorkOrders can enhance your maintenance strategies through their comprehensive services.
FAQs
Is SAP a CMMS system?
SAP is primarily an ERP (Enterprise Resource Planning) system, but it includes maintenance management modules that can perform some CMMS functions. However, it is not a standalone CMMS platform.
What is CMMS skill?
A CMMS skill refers to the ability to use maintenance management software effectively, including scheduling preventive tasks, managing assets, analyzing maintenance data, and improving workflow efficiency.
Is there a CMMS certification?
Yes, certifications like the Certified Maintenance & Reliability Professional (CMRP) and Certified Plant Maintenance Manager (CPMM) validate a professional’s expertise in using CMMS systems and managing maintenance operations.
What is an example of a CMMS?
eWorkOrders, Fiix, and Limble are examples of dedicated CMMS platforms used across industries to organize maintenance activities, track assets, and optimize preventive maintenance.