A nationally recognized warehouse and distribution center, operating multiple facilities across the U.S., came to us seeking a warehouse maintenance management software solution to improve how they manage operations and inventory across their entire distribution network. With decades of experience in logistics and fulfillment, they distribute a wide range of products—from consumer goods to specialized equipment. Their operations rely on heavy machinery, time-sensitive workflows, and strict safety and regulatory compliance.
Running 24/7, equipment failures or inventory shortages directly impact service levels and customer satisfaction. As the company grew, their manual processes for tracking maintenance tasks and managing spare parts became inefficient and prone to error. They needed a comprehensive maintenance operations software to centralize and streamline their maintenance strategy across all locations.
We collaborated closely with David, the Director of Facilities & Maintenance, who oversees the reliability and efficiency of operations nationwide. Below, David shares his experience using eWorkOrders CMMS for warehouses and partnering with our team.
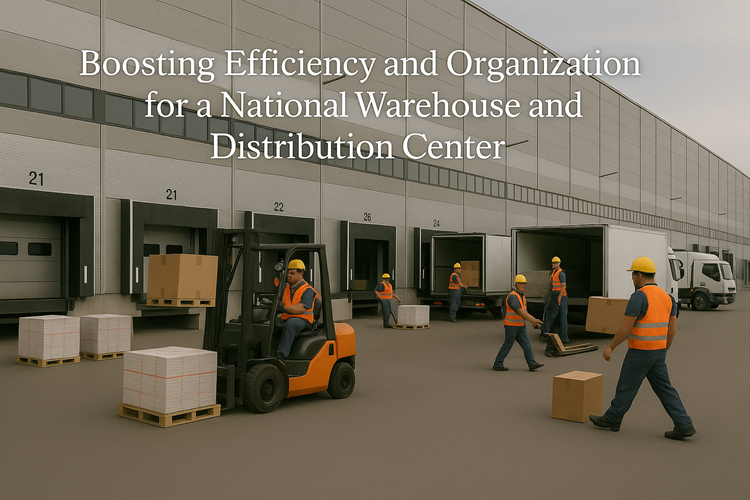
Business Challenge
For years, we managed maintenance and inventory with spreadsheets, whiteboards, and paper files. What was manageable in a couple of locations quickly became chaotic as we expanded to over a dozen facilities. It became difficult to ensure consistency, accuracy, and efficiency across our warehouse maintenance operations.
We frequently missed preventive maintenance schedules, technicians struggled to access accurate asset histories, and inventory management was decentralized and reactive. Finding the right spare parts or knowing when equipment like forklifts was last serviced took excessive time.
We lacked a centralized system to track vendor pricing, service contracts, and technician labor hours, leading to overspending and underperformance. Our executive team demanded better visibility into KPIs, asset performance, and cost control.
We needed a scalable, easy-to-use warehouse maintenance software that integrated asset tracking, work order management, mobile access, inventory control, and compliance reporting—all in one platform.
</div
Warehouse Maintenance Management Software Solution
After evaluating several CMMS platforms for warehouses, we chose eWorkOrders for its flexibility, comprehensive features, and outstanding customer support. Implementation was straightforward, and the eWorkOrders team guided us through every step.
Four key factors influenced our decision: affordability, ease of use, customization, and mobile access. Even technicians with limited technical experience adapted quickly.
With eWorkOrders, we gained:
- A centralized dashboard to manage all maintenance work orders across multiple warehouse locations.
- Real-time assignment and monitoring of technician workloads.
- Fully integrated inventory and spare parts management </a with automated reordering.
- Preventive maintenance scheduling that greatly reduced emergency equipment downtime.
- Customizable dashboards and reports providing leadership with full operational visibility.
The inventory management system revolutionized how we track parts across facilities. No more scrambling for stock—everything is tracked in real time, costs are transparent, and replenishment occurs automatically based on usage.
Proactive preventive maintenance software scheduling now keeps us ahead of equipment failures, reducing costly emergency repairs and unplanned downtime.
With mobile maintenance solutions, technicians receive, update, and close work orders directly from phones and tablets, attaching photos and notes for real-time accuracy.
Our compliance management software capabilities simplify audits. From OSHA inspections to customer inquiries, detailed maintenance records are available instantly.
Executive meetings feature custom dashboards to highlight operational trends and cost savings.
Implementation
Implementation was smooth. Our Account Manager provided guidance from system setup to user training. Choosing the hosted version eliminated IT overhead, and we went live in just weeks.
Data migration for assets and inventory was efficient with the help of the technical team. Despite varying user experience levels, everyone adapted quickly. Training was rolled out by location, supported throughout by eWorkOrders.
Customization impressed us—from permission settings to workflow automation, we tailored the platform to match our internal warehouse maintenance processes perfectly.
Ensuring Warehouse Compliance Through Maintenance Software
Warehouse safety is paramount. eWorkOrders helps us stay compliant by tracking equipment inspections, maintenance logs, and employee certifications all within the system. Audit preparation—internal or regulatory—is quick with instant access to required documentation.
The system supports compliance with ISO standards, OSHA regulations, making it a critical part of our risk management.
Results From Using Our Warehouse Maintenance Management Software
Since adopting eWorkOrders CMMS, we have full visibility over:
• 5,000+ maintenance work orders annually
• Over 2,200 unique parts tracked across facilities
• Complete asset histories and technician labor hours per task
By reducing downtime, eliminating manual tracking, automating parts procurement, and optimizing labor management, we estimate annual savings exceeding $450,000.
Beyond cost savings, we’ve enhanced service levels, reduced emergency repairs, and significantly boosted technician productivity and accountability.
Summary
eWorkOrders CMMS has transformed our warehouse maintenance operations—from reactive to proactive, fragmented to centralized, paper to digital. Our team is more efficient, equipment reliability is up, and leadership has the actionable data needed for smart decision-making.
For any multi-site warehouse, distribution center, or logistics operation, I highly recommend eWorkOrders. It’s more than software—it’s a comprehensive maintenance management strategy enabling scalable growth with confidence.” Hear directly from users who improved efficiency with eWorkOrders in these authentic reviews.
The bottom line: “eWorkOrders CMMS is essential to our operational success—we wouldn’t run our warehouses without it.”
This guide to air compressor care helps avoid equipment failure and production delays.
.
The following case study is a composite scenario based on typical customer experiences with eWorkOrders CMMS.