An established oil and gas production company, operating drilling and processing facilities across North America, needed a better oil and gas maintenance software solution. Their goal was to manage maintenance more efficiently in remote, high-risk environments—covering upstream, pipeline, and refining operations with complex compliance needs.
Maintenance tasks were managed manually through spreadsheets, printed logs, and disconnected systems, making it difficult to track work orders, asset performance, or compliance documentation across multiple oilfields. Failures in critical equipment led to costly downtime, safety risks, and compliance gaps.
Their team needed a centralized, mobile-friendly oil and gas maintenance software to improve reliability, reduce downtime, and simplify compliance reporting. We worked closely with their Maintenance and Compliance Director to implement a scalable, cloud-based CMMS solution.
Here’s what they had to say about partnering with eWorkOrders.
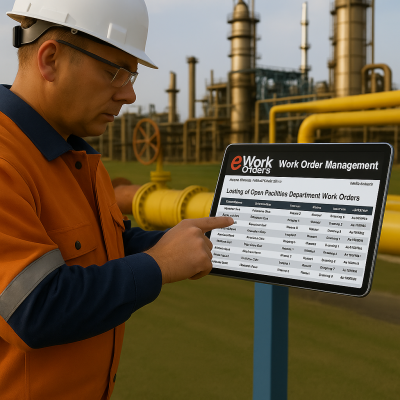
Business Challenge
Maintaining equipment across remote oil and gas sites with manual tools created inefficiencies, risks, and poor visibility into critical operations. Work orders were often delayed or lost, and asset histories were scattered or incomplete. Maintenance scheduling was reactive, increasing the chance of unplanned shutdowns.
The company also struggled with regulatory compliance. Audit preparation was time-consuming, and tracking environmental inspections, pressure vessel checks, and safety certifications required combing through paper records. Leadership lacked real-time insights into performance KPIs or maintenance costs.
They needed a reliable CMMS for oil and gas operations that could track maintenance activities, asset performance, and technician productivity in real time—whether at a corporate office or an isolated well pad.
Oil & Gas Maintenance Management Software Solution
After comparing several oil and gas CMMS platforms, the company selected eWorkOrders for its ease of use, powerful asset management tools, and support for remote field operations. Implementation was fast and fully supported by the eWorkOrders team.
Key benefits included:
- A centralized system for managing all maintenance work orders by asset, location, or technician.
- Mobile access to view and close work orders, upload photos, and log inspection results in the field.
- Inventory management software to control stock across multiple supply yards.
- Automated preventive maintenance schedules to reduce downtime on compressors, pumps, and pipeline infrastructure.
- Custom reports and dashboards showing maintenance KPIs, equipment costs, and compliance status.
Having one platform to handle oil and gas asset management, mobile inspections, and compliance workflows transformed how the company manages field reliability and safety.
Implementation
Implementation was completed in weeks, not months. eWorkOrders provided end-to-end onboarding, from asset data import to technician training. The hosted version eliminated the need for IT infrastructure, and the system was fully operational across field locations quickly.
Users of all technical levels adopted the software with minimal training. The system was configured to reflect internal workflows and approval chains, including contractor management, field-level permissions, and escalation rules.
Ensuring Compliance in the Oil & Gas Industry
eWorkOrders CMMS gave the company peace of mind when it came to environmental and safety compliance. Technicians record all inspections, maintenance logs, and certifications directly into the system—with timestamps, signatures, and photo documentation.
When regulators request reports, everything is accessible within seconds. The system supports readiness for OSHA, API, and local environmental audits, while reducing the paperwork burden on field teams.
Results From Using eWorkOrders in Oil & Gas Operations
After going live with eWorkOrders, the company saw measurable improvements:
• 25% reduction in emergency repairs across key sites
• 15% increase in technician productivity with mobile work order access
• Full traceability on over 10,000 assets and inspection events
• Instant access to historical records for audits and reporting
They now operate with proactive maintenance strategies, real-time field data, and full confidence in their compliance standing.
Summary
With eWorkOrders, this oil and gas company transitioned from reactive, paper-based processes to a fully digital, proactive maintenance program. The software’s flexibility, mobile capabilities, and robust compliance tools now support every level of their operation—from the field to the executive team. Don’t take our word for it—explore real customer testimonials about how eWorkOrders is transforming maintenance management.
“We run a safer, more efficient operation thanks to eWorkOrders,” said their Maintenance Director. “It’s become a critical piece of our equipment strategy and risk management across every site.”
The following case study is a composite scenario based on real-world customer experiences with eWorkOrders CMMS.