Commercial Airport’s
Maintenance & Operations System Upgrades
This major US commercial airport uses eWorkOrders to manage their maintenance and operations functions. The airport covers 2,600 acres, with multiple runways. Runways are 150’ wide which can handle planes of any size. More than 1.1 million travelers pass through each year. Over 1,400 people are employed at the airport. The airport is subject to federal regulation CFR 14 Part 139, which requires inspections and certification by the Federal Aviation Administration (FAA).
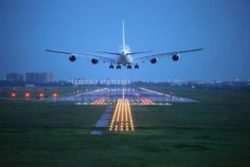
Prior to Implementing eWorkOrders
In 2010 the airport was using a client-server application called MP2. It was only accessible from their internal network. It allowed airport employees to enter work orders, but when techs needed to update the status of a work order or needed to obtain additional information, it required them to find a computer with the client software installed to log into the system. Also, it was extremely limited since it prevented interaction with the tenants that reported problems and who had additional service requests for the maintenance department.
In late 2010 the facilities maintenance department switched to eWorkOrders. One of the key benefits was that the new system was internet-based and very user-friendly. This made it possible for tenants to enter their own work orders without requiring training. Tenants were not required to have user ids and passwords. There was no time spent on user administration for service requesters. The request portion was very easily rolled out. Incoming requests could get approved by the facilities department and routed to the appropriate worker. In addition, maintenance techs carry wireless tablets enabling them to access the system in real-time making them much more efficient. They can check part availability, gather additional information, and close work orders faster. The system also allows tracking the amount of time each tech spends on any one work order. This allows for better staff allocation.
Phase 2 – The Airfield Inspections Module
In 2014 the airport was looking to automate the twice-daily inspection required by the FAA. They were hoping for something that would be able to integrate with eWorkOrders since the facilities maintenance department was very happy with their solutions and not likely to change to another program. It was perfect timing as eWorkOrders was in the process of implementing their Geographic Information System (GIS) module and would complement the airport’s needs rather well. The airport chose to contract eWorkOrders to develop an Airfield Inspections Module that would meet their FAA Part 139 compliance needs.
Using the preventive maintenance module, daily airfield inspections work orders were set up to automatically generate for both the daytime and nighttime inspections. The airfield inspection form was designed for easy use on mobile devices to be used on airport grounds. It allows them to select which inspectors would be participating in each inspection, provide any feedback notes and NOTAM numbers that had been issued. They could also report discrepancies for items needing inspection. Each item category is marked with a “satisfactory” or “problem” result. When a category is flagged as a problem, an interactive satellite view of the airport appears. This map can automatically determine the inspector’s location and display nearby assets as intuitive icons. Clicking on the icons enables inspectors to find out all of the asset details, as well as, automatically generate a work order specific to the issue noted. It will forever remain linked with that particular airfield inspection, a feature required for FAA Part 139 compliance. Inspectors can also generate work orders for a specific geographic location, instead of an asset. This is ideal for reporting ground issues such as potholes and loose soil. Easy-to-run reports were developed to print inspections in full detail either in mass quantities or, on an individual basis, with the specifics of any resulting work orders attached.
Summary
Overall the airport’s operations and inspections have been dramatically improved. All management, inspectors and maintenance techs have everything they need at their fingertips either textually, through a calendar interface or via the interactive map. Tenants enter their own requests and are kept in the loop as updates are made and work is completed. Tremendous amounts of time have been saved by taking service requests, automating inspections and ensuring regulatory compliance.
See What Our Customers Are Saying
Additional Resources
CMMS Articles & Directories
Maintenance Terms & Definitions Glossary
Checklists
Note: As a courtesy to our customers, we do not publish their company names, but the actual case studies are available upon request.