Equipment breakdowns can be a major headache for any business, leading to unexpected costs, downtime, and reduced productivity. There are various reasons why equipment breaks down, and it’s essential to understand and address these factors to prevent failures. Here are the top 10 reasons why equipment breaks down:
- Lack of Proper Maintenance
Neglecting regular maintenance tasks such as cleaning, lubrication, calibration, and inspection can significantly reduce the lifespan of equipment.
- Overloading or Misuse
Operating equipment beyond its designed capacity or using it for unintended purposes can lead to premature failure.
- Age
As equipment gets older, its components can wear out, leading to an increased risk of failure.
- Poor Training
Inadequate training of operators and maintenance personnel can result in improper use and maintenance of equipment, leading to breakdowns.
- Environmental Factors
Exposure to extreme temperatures, humidity, dust, and other environmental factors can accelerate wear and tear on equipment.
- Vibration and Shock
Excessive vibration and shock can damage equipment components over time, leading to failure.
- Contamination
Contamination of lubricants, fuels, and other fluids can lead to increased friction, wear, and corrosion, resulting in equipment failure.
- Material Fatigue
Over time, materials used in equipment can experience fatigue and fail, especially under high-stress conditions.
- Design Flaws
Inadequate design or engineering of equipment can lead to inherent weaknesses that result in premature failure.
- Human Error
Mistakes made during installation, operation, or maintenance of equipment can lead to failures.
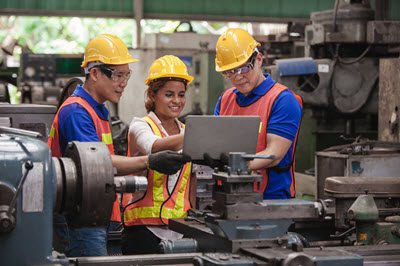
How CMMS Can Help Manage Equipment Breakdowns
Computerized Maintenance Management System (CMMS) software can be a valuable tool for managing and preventing equipment breakdowns. Here’s how CMMS can help:
Optimize Maintenance: CMMS software helps optimize maintenance schedules and activities based on historical performance data, ensuring that maintenance efforts are effective and efficient.
Predictive Insights: Data from equipment history allows for predictive maintenance. By recognizing issues before they lead to failure, organizations can address problems in their early stages, minimizing the risk of costly breakdowns.
Predictive Analytics: The software employs predictive analytics models that analyze data to forecast when equipment is likely to fail, allowing for proactive intervention.
Documentation and Record-Keeping: Maintaining accurate documentation and records is crucial for equipment management. CMMS software can help ensure that all maintenance activities, inspections, and repairs are well-documented, providing a clear history of the equipment’s maintenance and performance.
Final Thoughts
Equipment breakdowns can have significant financial and operational impacts on a business. By understanding the reasons for equipment failures and implementing a proactive maintenance strategy with the help of CMMS software, organizations can minimize downtime, reduce costs, and ensure the reliable performance of their equipment. eWorkOrders CMMS offers a comprehensive solution to streamline maintenance processes, improve asset reliability, and mitigate the risks associated with equipment failures. To experience firsthand how eWorkOrders CMMS can benefit your organization, we invite you to contact us for a personalized demo. Discover how our CMMS software can empower your maintenance teams, enhance equipment uptime, and contribute to the overall success of your maintenance operations.